Anodizing Services
We use different types of anodizing, such as Type II polar oxidation and Type III anodizing, which can be customized according to the requirements of the product.
Anodizing type II
All tolerances apply after anodizing
Project | Info |
---|---|
Materials | Aluminum |
Colors | Clear, black, you can define your color according to RAL. |
Glossiness | Glossy or matte |
Texture | Smooth, matte finish. |
Thickness | 0.00007” to 0.0010” |
Surface roughness | Ra 0.4μm to 1.2μin |
Hardness | 250-500 HV(The hardness range can be adjusted as needed) |
Heat resistance | 150°C(302°F) |
Application | Improve hardness, increase surface wear resistance, and enhance aesthetics |
Anodizing type III
All tolerances apply after anodizing.
Project | Info |
---|---|
Materials | Aluminum |
Colors | Clear, Black |
Glossiness | Glossy or matte |
Texture | Smooth, matte finish. |
Thickness | 0.0005” to 0.0045” |
Surface roughness | Ra 0.5μm to 3.0μin |
Hardness | 450-600 HV(The hardness range can be adjusted as needed) |
Heat resistance | 200°C(392°F) |
Application | Used to improve the corrosion resistance, wear resistance, and appearance of metal parts |
Example of anodizing parts
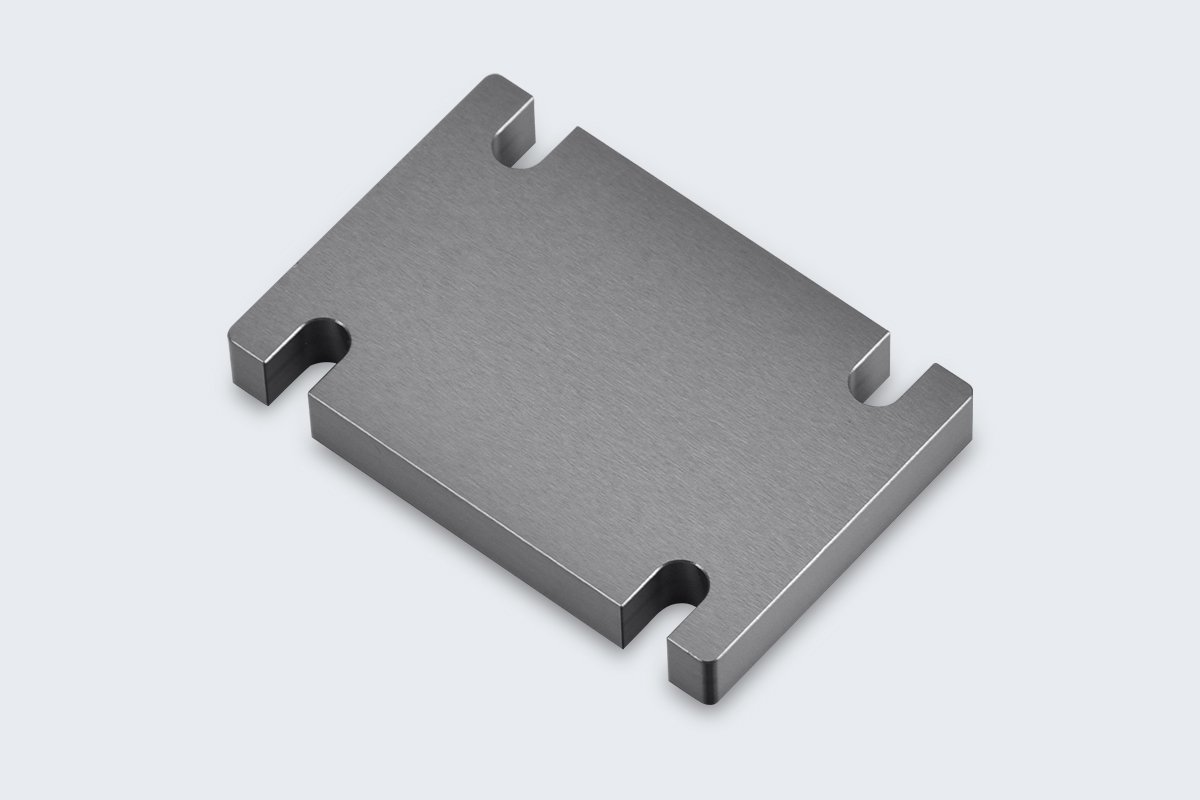
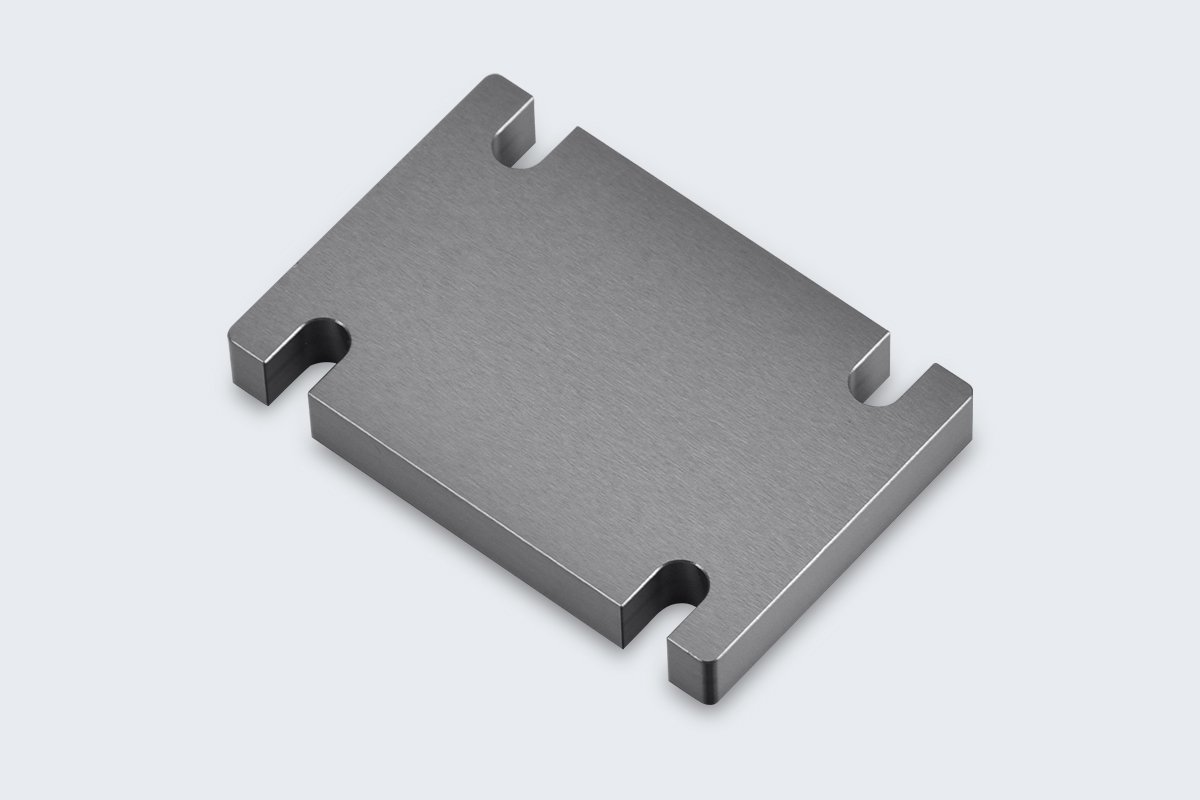


Design considerations for anodized parts
- Increase the thickness of the part surface: Anodizing will form a layer of oxide on the surface of the metal part, which will increase the surface thickness. This may have an impact on the size and functionality of the parts, so it is recommended to block and cover threads, reams, or other critical surfaces before anodizing to ensure that their functionality is not affected.
- Shelf marks: If the parts do not have holes, they may be hung on the conductive frame for anodizing treatment using spring clips, wire wrapping, or other methods. This may result in leaving small areas without oxidation treatment, known as “shelf marks”. If these areas have a significant impact on product performance, they need to be marked in the drawing to remind operators.
- Conductivity: Anodizing will form an insulation layer, so the conductivity of the treated parts is poor. This needs to be considered in design and engineering to ensure that the electrical connections of the parts are not disturbed.
- Rounding edges and corners: To prevent local overheating and burning caused by current concentration, all sharp corners on the workpiece should be rounded off. This can improve the uniformity and efficiency of the processing process.
- Surface roughness: After hard anodizing treatment, the surface roughness may decrease, making the parts smoother. But if the workpiece already has a very smooth surface, it may lose some smoothness.
- Special fixtures: Due to the high voltage and current required for hard anodizing, special fixtures must be designed to ensure good conductive contact of the workpiece. Otherwise, breakdown or burning of the contact part of the workpiece may occur, thereby affecting the treatment effect.
Latest Blog Posts
Climb Milling vs. Conventional Milling: A Battle for Manufacturing Precision
2024-07-22
In mechanical processing, milling is crucial for metalworking. This guide explores climb milling (down milling) and conventional milling (up milling), focusing on their impact on ...
Read More →
Resin Vs. Plastic: Understanding The Core Differences For Better Material Selection
2024-07-22
In materials science, resins and plastics are pivotal polymer materials widely used in daily life and industrial production. Despite functional similarities, their core differences are ...
Read More →
How Do Mechanical Springs Store Energy?
2024-07-18
In the vast field of mechanical engineering, mechanical springs, as a basic and important component, play a key role in storing and releasing energy. With ...
Read More →
Put your parts into production today
- All information and uploads are secure and confidential.