Beginners’ machining, may encounter some strange shape parts, their geometric shape is not square, round, triangle and other common shapes, but some bevel and chamfer composition, but in cnc machining parts manufacturing common practice is to reduce the acute Angle of parts caused by damage or injury opportunities. To solve this problem, mechanics removed part of the 90-degree Angle and created a chamfer, also known as a bevel. Although the terms “bevel” and “chamfer” tend to be interchangeable in practice, there are clear differences. Let’s take a moment to read this blog about the difference between bevel and chamfer and see how cnc machining uses these features when making parts.
What are bevels and chamfers?
The bevel refers to the rectangular surface with smaller angles on both sides, while the chamfer is to polish the edges and corners of the geometric figure into rounded corners, making it more smooth.
Bevel and chamfer, as common operations in manufacturing, have many advantages. They can reduce the relative motion between parts and help improve the performance of mechanical equipment. In addition, bevel and chamfering are often used in the field of sensor technology, because they can make the light more evenly distributed on the sensor, thus improving the detection accuracy.
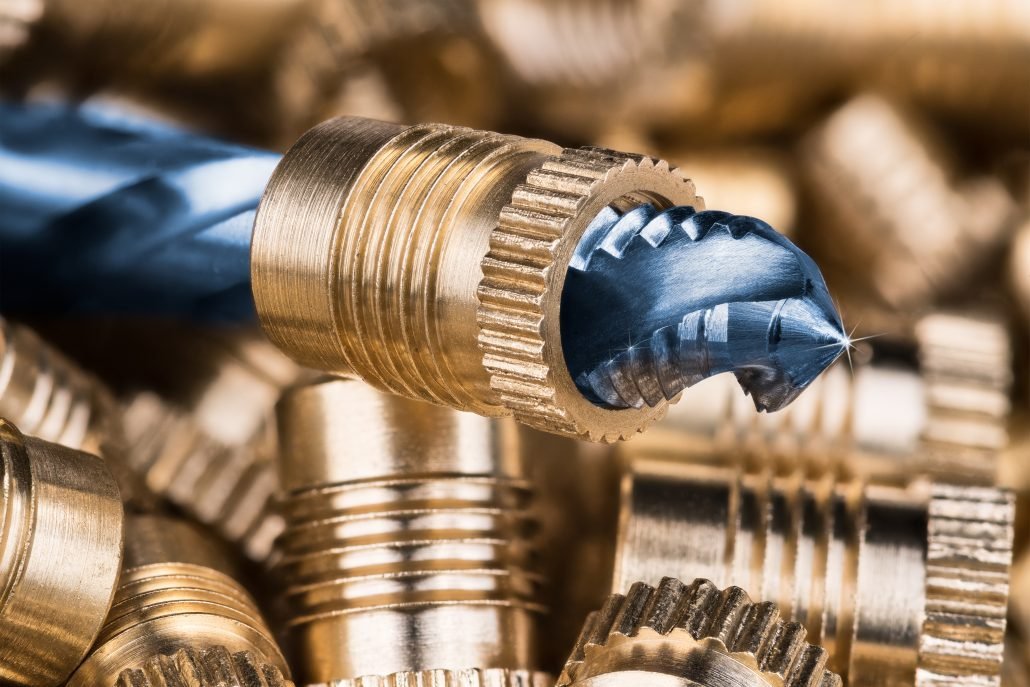
Define the difference between bevel and chamfer
Bevel and chamfer are both used in CNC machining parts, but their purposes and ways of realization are different. Bevels are often used to make the shape of a part more beautiful, or to improve the quality of the surface of the part. Chamfering is to reduce the edge sharpness of parts, so as to avoid risks and dangers caused by too many edges and corners.
The terms “bevel” and “chamfer” describe the same geometric features in a part, but differ. Defining them in detail can help identify the differences:
cNC machining bevel
A bevel is a slanted edge between two main faces of a part for easy connection to the other face. Bevel angles can be measured at any Angle other than 45 degrees, and they help improve wear resistance, safety, and aesthetics. For example, cutting tools, mirrors, and glass furniture have bevels in their blades to prevent the sharp edges of the glass from causing injury.
CNC machining chamfering
Instead of connecting a cnc machined part to the beveled edge of another part, the chamfer transitions between two right-angled surfaces of the same part. Unlike the bevel, the chamfer is always at a 45 degree Angle. Chamfering removes sharp edges of parts at 90 degree angles to prevent injury during handling. Chamfering also improves the overall integrity of the part by protecting the corners of the part from damage.
Application scenario
Bevel and chamfer are used in different scenarios. In the design of parts need to choose the appropriate treatment according to the actual situation.
Application scenarios of bevels:
Inclined plane is applicable to the surface of parts with a certain Angle of inclination, such as the upper surface of a cylinder;
1.2 Bevels are usually used for the aesthetics of parts design and to reduce the resistance of materials when they are cut;
1.3 Bevel is also a good choice when 3D effect is needed on part surface.
Application scenarios of chamfering:
2.1 Chamfering is suitable for occasions where the designed parts need high compression and shear resistance, such as automobile engine parts, mechanical parts, etc.;
2.2 The second application scenario of chamfering is to reduce the sharp edges of parts and protect human safety;
2.3 When the connection strength of parts needs to be more stable, chamfering is also a good choice.
When choosing the machining method, we need to make trade-offs according to the actual situation. If you need to increase the strength of the part and reduce the cost of production, then the bevel is a good choice. If we need to increase assembly and protection capabilities, then we should choose chamfering.
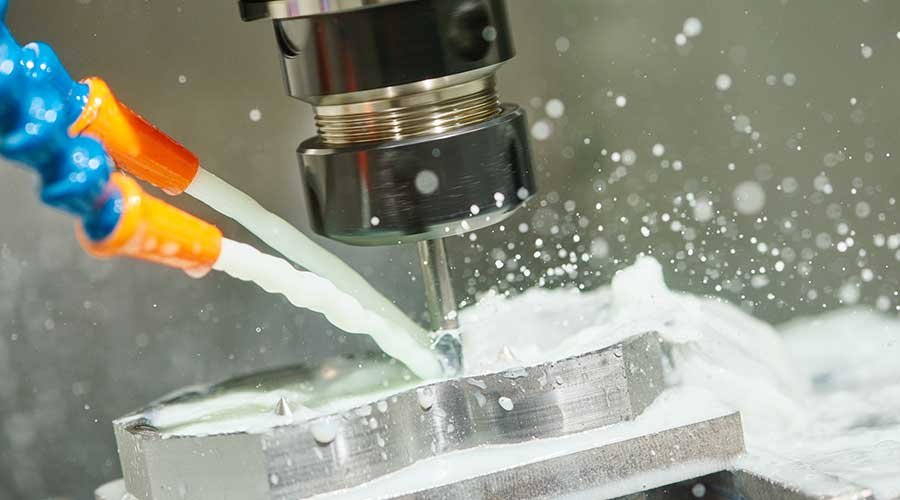
Bevel and chamfer machining material difference
In machining, bevel and chamfer they have different use in machining materials, the following Longsheng technology to introduce in detail the two processes are suitable for machining which materials
Bevel machining material
Bevel machining is mainly for large structural parts, it needs to directly cut materials. This requires the hardness of the material is relatively high, and relatively wear-resistant. Common materials are carbon steel, stainless steel, alloy steel, aluminum alloy, titanium alloy, copper and so on.
Stainless steel is a very strong and corrosion-resistant metal. It is often used in construction, automobiles and manufacturing. As a high-value metal, titanium alloy is widely used in the aerospace industry and biomedical fields due to its lightweight and excellent corrosion properties. Copper and aluminum alloys are commonly used in electrical equipment, building materials and machinery manufacturing.
In addition to hardness and wear resistance, bevel machining materials are also characterized by good machinability, as well as good thermal conductivity. This in the process of machining can ensure the service life of the tool, and not easy to burn.
Chamfering materials
In contrast, chamfering is mainly to trim the corners of parts. It seems relatively simple, but in fact, the choice of materials is also crucial. Some of the most commonly used chamfering materials include: tungsten steel, high speed steel, cobalt-molybdenum alloy and tungsten carbide.
Tungsten steel is a kind of high strength, high hardness and high density metal. It is often used in tool making. High speed steel is a steel with a high ratio of carbon to tungsten. It has high strength and hardness, so it is widely used in manufacturing high-speed cutting tools. Cobalt-molybdenum alloy is an excellent wear resistant material and is often used where high durability or high temperature erosion is required. Tungsten carbide is an excellent wear-resistant material, widely used in tools, metal industry and machinery manufacturing.
Chamfering materials need to be relatively easy to machine cut, but also easy to shape. This requires the choice of soft materials. In addition, after chamfering the surface of the material must be smooth, so the material also has a good surface hardness.
Bevel and chamfer parts manufacturing cost
An operator will use a chamfered milling cutter or “cutter” when machining a part with a cnc to create a bevel or chamfer in the machined part. Bevel angles may require more channels to complete and usually have a larger area to cut than chamfering, but this is subjective. In addition, a double chamfered end mill cuts chamferes at the top and bottom of the work piece without turning it over. Machining shops find these tools versatile as they can be used for chamfering, chamfering, deburring, spot removal and countersunk holes. However, beveling and chamfering can increase the manufacturing cost of parts, as discussed below.
The cost of adding additional features to the design
Bevels and chamferes are used to protect parts and their users for obvious reasons. However, these features are usually more about beauty than function, and they increase the cost of producing parts.
Some practical questions to ask before including bevel or chamfer in your design:
parts need cant or chamfering can play a role?
need bevel for security purpose?
how to check the tolerance of bevel or chamfering?
it is added to the design of the function of cost-effective?
Features such as bevels and chamferes require additional time during manufacturing. When multiplied by the number of parts produced, even a 5% increase in time per part adds up to a significant cost increase. If extraneous features do not serve any necessary function or purpose, reconsider them. The specified tolerances of bevels or chamferes should also undergo some review. Machine shops require more time to manufacture and check tighter tolerances, which also increases the cost of parts production.

Save money on countersunk holes and other chamfering features
Although chamfering should be carefully checked for aesthetic use to avoid unnecessary manufacturing costs, there are some reasonably cost chamfering applications. For example, countersunk drilling of threaded holes helps avoid burrs during tapping that may affect how the two mating surfaces are held together.
Countersunk holes also help the bolts align properly at the beginning and avoid costly misthreaded connections during assembly. For some holes, such as aircraft rivets, accurate countersunk holes are so important that they require strict tolerances to ensure that a sufficient amount of mating material is available for a secure connection.
Another cost effective use of chamfering is in the internal features of cnc machined parts. Designing the chamfer into the feature of the part rather than smoothing it out will reduce the manufacturing cost of the part. Chamfering will reduce the time required to cut right angles in the part and allow cheaper tools to be used. Internal chamfering also helps prevent dust and waste from accumulating in the corners of parts.
Considering all of these issues before designing a bevel or chamfer into a part provides advantages. If the design does not require these features, eliminating them will simplify manufacturing, saving time and money. On the other hand, if the design does require them, the impact on production time and expense can still be reduced. One approach is to provide large tolerances and simplify the manufacture of bevels and chamferes if precise dimensions are not critical. Another option is to completely remove the chamfer feature from the CAD model and add a note to the 2D drawing instructing the cnc shop to “remove all sharp edges”.
Bevel and chamfer applications
Bevel and chamfer are widely used in machine manufacturing. Whether on lathes, milling machines or other machining equipment, bevels and chamferes can be used to achieve some special machining requirements.
The application of inclined plane in machining can be used to process slots, slots, threads, etc. Its function is to make the workpiece surface produce an Angle, in order to be more convenient and accurate in the subsequent machining. The geometric shape of the inclined plane can be right triangle, isosceles triangle, etc., according to the actual need to choose the appropriate shape and Angle.
Another common machining technique is chamfering, which is usually used to remove edges and angles from an object to make it more beautiful and secure. Chamfering is also very widely used in machinery manufacturing, for example, the use of chamfering at the connection points of automotive engines to protect bolts from excessive tightening and stress, thus improving the service life and durability of parts
In addition, the bevel and chamfer can also realize some special requirements in the manufacturing process, such as the edge of the steel plate needs to be chamfered to improve the accuracy and beauty of welding; In the manufacture of gear, it is also necessary to use bevel machining to improve the noise and wear resistance of gear.
Chamfer and bevel machining technology
In CNC machining, in addition to the basic drilling and cutting functions, CNC machine can also carry out many other types of processing, such as bevel and bevel machining, bevel machining and bevel machining differences and application fields are not the same, so the machining technology between them will be different, the following Longsheng technology will be detailed:
Bevel machining technology
Bevel machining is a process in which a cycloid, bevel, or radius is produced by removing part of the material on the workpiece’s surface. Bevel machining is a precise and efficient process that can be used to manufacture a wide variety of workpieces, such as metal profile parts, molds, tools and complex mechanical components. In the manufacturing process, bevel machining mainly has the following three categories:
Flat bevels: This type of bevels are manufactured according to different angles and are used for different mechanical components. For example, a flat bevel with an inclination of 45 degrees can be used in the fabrication of contour parts of calipers.
Strip bevel: This machining method is most suitable for the machining of strip, strip and tubular elongated parts. Strip bevel can make a series of bevels on the plane.
Complex bevel: This machining method can be used to produce a variety of scrap copper, scrap iron and other waste products, such as artifacts, sculptures and so on.
Chamfering machining technology
Chamfering is a machining method used to produce a beautiful appearance of the workpiece and to remove burr. Chamfer can improve wear resistance, corrosion resistance, plasticity and life span of workpiece surface. It is an important machining method, can be used to produce a variety of workpiece, such as metal plate, turning workpiece, stamping workpiece, etc. In the process of machining, chamfer is mainly divided into the following three types:
Fitting Angle: This Angle is mainly used for milling and groove machining to extend the service life of the workpiece.
Mirror Angle: This kind of Angle is mainly used for spinning workpiece, CNC parts online, parts made of wire and stamping chips, etc., to bring a better appearance to the workpiece surface.
Conventional Angle: This Angle is suitable for many types of workpiece, such as stamping workpiece, turning workpiece, wire cutting, etc., as mentioned above.
Bevel machining technology and chamfering machining technology are commonly used in machining field, but there are many differences between them. Therefore, in the selection of different machining technology, it is necessary to decide according to the characteristics and requirements of the workpiece.
Hope this article has been helpful! For example, a chamfer is used at the connection points of a car engine to protect bolts from over-tightening and stress, thereby improving the service life and durability of parts
In addition, the bevel and chamfer can also realize some special requirements in the manufacturing process, such as the edge of the steel plate needs to be chamfered to improve the accuracy and beauty of welding; In the manufacture of gear, it is also necessary to use bevel machining to improve the noise and wear resistance of gear.
FAQ
CNC machining can provide a complex, customized shape to the workpiece, especially when machining small, complex, and large numbers of parts. It also provides high precision, repeatability, and efficient production of the workpiece.
In terms of meaning and practical application, bevel is more flexible than chamfer. Chamfering is often used to reduce the likelihood of physical impact on an object’s surface, while bevelings can be shaped to achieve specific functions, such as reducing weight and improving rigidity.
Common CNC machining techniques include milling, cutting and drilling. Using these techniques, different geometry shapes can be created by varying the rotation and cutting depth of the tool.