Metal injection molding (MIM) is a manufacturing process that allows the production of complex metal components with specific geometries, using a combination of powder metallurgy and plastic injection molding. This technology offers many advantages in terms of cost, speed, and precision, making it a popular choice for high-tech industries such as aerospace, medical, and telecommunications.
In this article, we will give you a detailed explanation of how metal injection molding works, its applications, benefits, and limitations, and some real-world examples of its use.
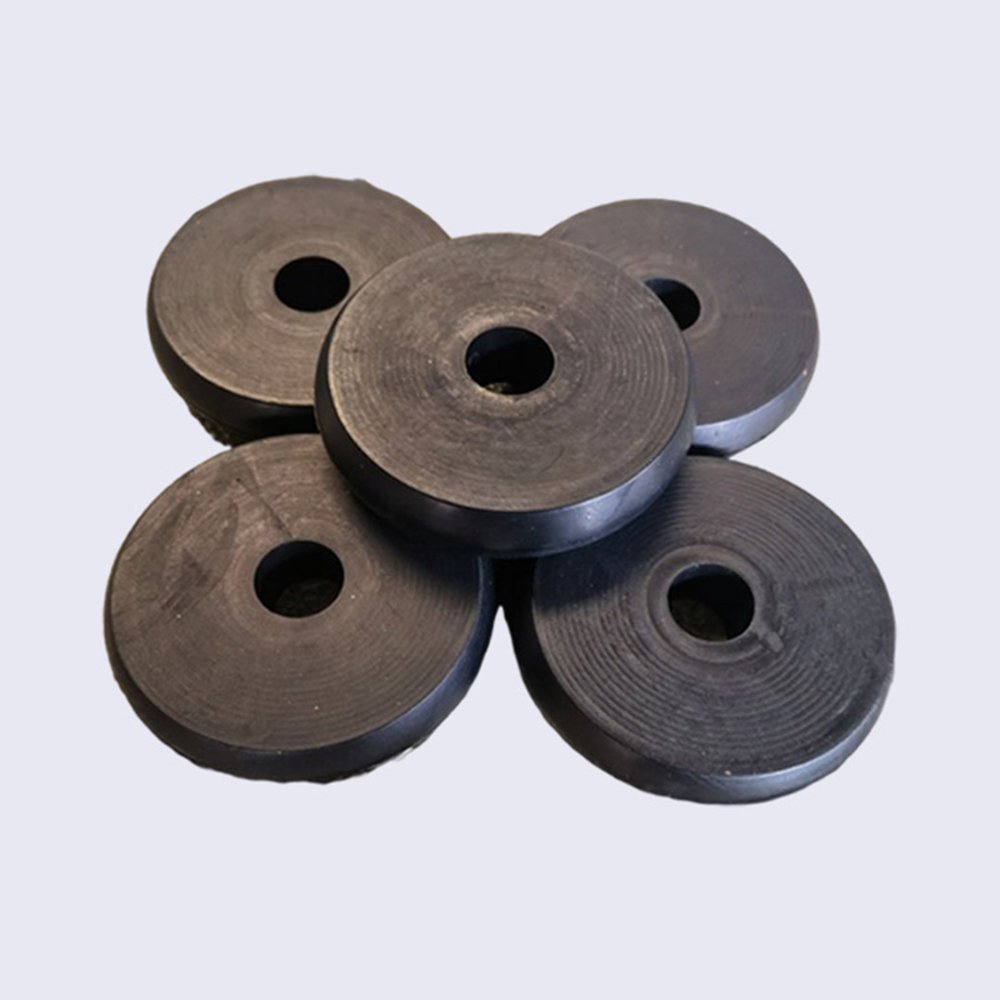
What is Metal Injection Molding?
Before diving into the process of metal injection molding, let’s first understand what is meant by the term. Metal injection molding is a type of powder metallurgy, which involves mixing fine metal powders with a binder material to create a feedstock that can be molded into complex shapes. The molded component, also known as a “green part,” is then subjected to a series of thermal and chemical treatments to remove the binder and consolidate the metal powders, resulting in a dense and strong final product.
The feedstock used in metal injection molding typically consists of a small amount of plastic binder, such as polyethylene or polypropylene, and a large percentage of metal powder, often ranging from 60% to 90% by volume. The choice of metal powder depends on the specific application and desired properties, such as strength, hardness, corrosion resistance, or magnetic properties.
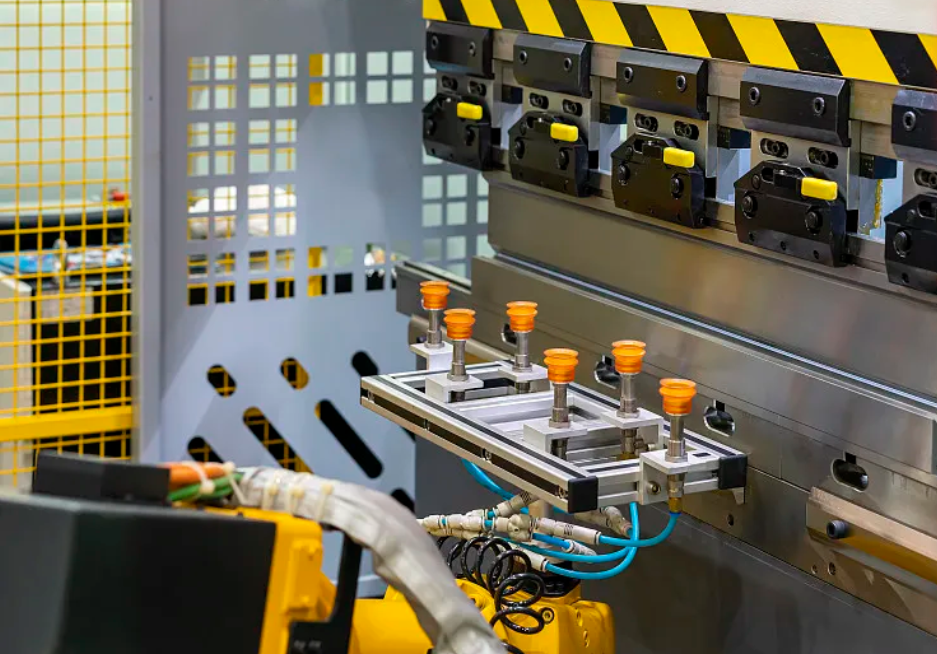
Why Choose Metal Injection Molding?
Metal injection molding has a number of advantages over other metalworking methods:
- Versatility: MIM can produce parts from a range of metals, including stainless steel, titanium, copper, and more.
- Precision: the injection molding process ensures consistent, high-quality parts with tight tolerances.
- Complexity: MIM can produce intricate shapes and features that would be difficult or impossible to create using other methods.
- Cost-effectiveness: MIM is often more cost-effective than traditional methods for producing complex metal parts in smaller quantities.
The Metal Injection Molding Process
The metal injection molding process involves several steps, as shown in the simplified flowchart below:
- Feedstock preparation: The metal powders and binder are mixed together and fed into a screw-type injection molding machine, which heats the feedstock and injects it into a mold cavity.
- Molding: The feedstock is injected into the mold cavity, where it solidifies into the desired shape. The mold is usually made of tool steel or ceramic, and can be designed to produce multiple parts in one cycle.
- Debinding: The green parts are removed from the mold and subjected to a thermal process called debinding, which removes most of the binder material. This step can be done in a heated air or vacuum environment, and can take several hours to several days depending on the size and complexity of the part.
- Sintering: The debound parts are then subjected to a high-temperature sintering process, which fuses the metal powders together and removes any remaining binder material. The sintered parts shrink in size by up to 20%, depending on the material and process conditions, but retain their shape and integrity.
- Finishing: The sintered parts may undergo additional finishing steps, such as machining, polishing, coating, or heat treatment, to achieve the desired surface finish, tolerance, or properties.
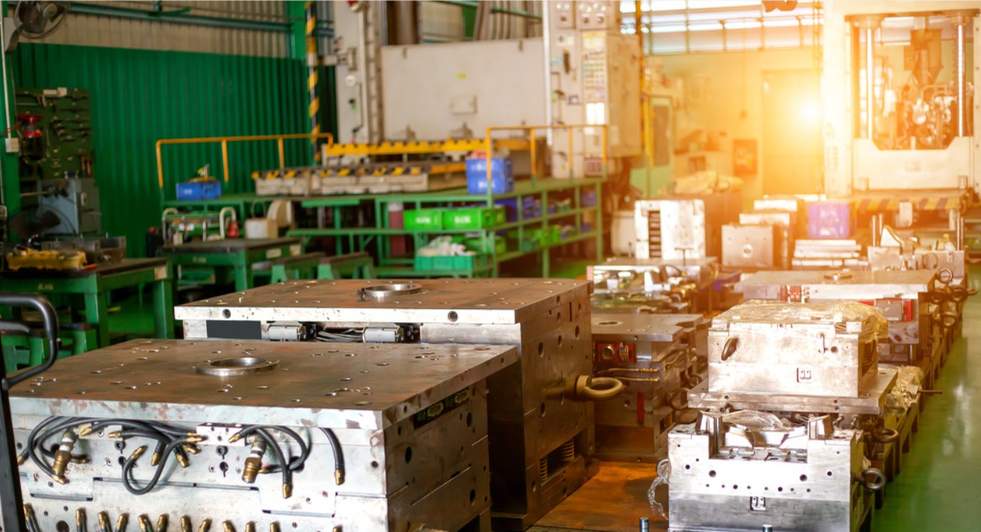
Applications and Benefits of Metal Injection Molding
Metal injection molding is widely used in various industries to produce complex metal parts that are difficult or impossible to make using other methods. Some common examples include:
- Surgical instruments, such as forceps, scissors, and implants
- Aerospace components, such as turbine blades, nozzles, and connectors
- Electronics housings, such as connectors, switches, and sensor housings
- Firearms components, such as triggers, bolts, and mag wells
- Automotive parts, such as fuel injectors, gears, and brake calipers
The benefits of metal injection molding are numerous, including:
- High precision: Metal injection molding can produce parts with tolerances as low as +/- 0.05%, or even better in some cases.
- Complex geometries: Metal injection molding can create intricate shapes, thin walls, undercuts, and internal features that are otherwise impossible to achieve using traditional machining or casting.
- Material flexibility: Metal injection molding can process a wide range of metal alloys, including ferrous and non-ferrous materials, stainless steel, titanium, and magnetic materials.
- Cost-effective: Metal injection molding can offer significant cost savings compared to other manufacturing methods, especially for high-volume production runs.

Limitations of Metal Injection Molding
Despite its many advantages, metal injection molding has some limitations that should be taken into account. These include:
- Material limitations: Some metal powders are more difficult to process than others, depending on their particle size, shape, chemistry, or flowability. For example, aluminum and copper alloys can be challenging to inject due to their high thermal conductivity and low viscosity.
- Size limitations: Metal injection molding is best suited for small to medium-sized parts, typically weighing less than 100 grams. Larger parts may be possible but require specialized equipment and longer processing times.
- Production variability: Metal injection molding can be sensitive to process variables such as temperature, pressure, and mixing ratio, which can affect the quality and consistency of the final product. Tight process control is therefore necessary to achieve optimal results.
Real-World Examples of Metal Injection Molding
To give you a better idea of the versatility and potential of metal injection molding, let’s look at some real-world examples:
- A medical device manufacturer used metal injection molding to produce a hemostat forceps with a complex shape and a tight tolerance of 0.05 mm. The metal alloy used was a low-carbon stainless steel that offered high strength and corrosion resistance.
- A telecom equipment maker used metal injection molding to create a connector housing with a thin wall and multiple internal features. The metal alloy used was a nickel-iron-copper material with high magnetic permeability and low coercivity.
- A firearm component supplier used metal injection molding to manufacture a bolt carrier group for an AR-15 rifle. The metal alloy used was a high-strength steel that offered good wear and corrosion resistance. The part was finished with a black nitride coating for added durability and aesthetics.
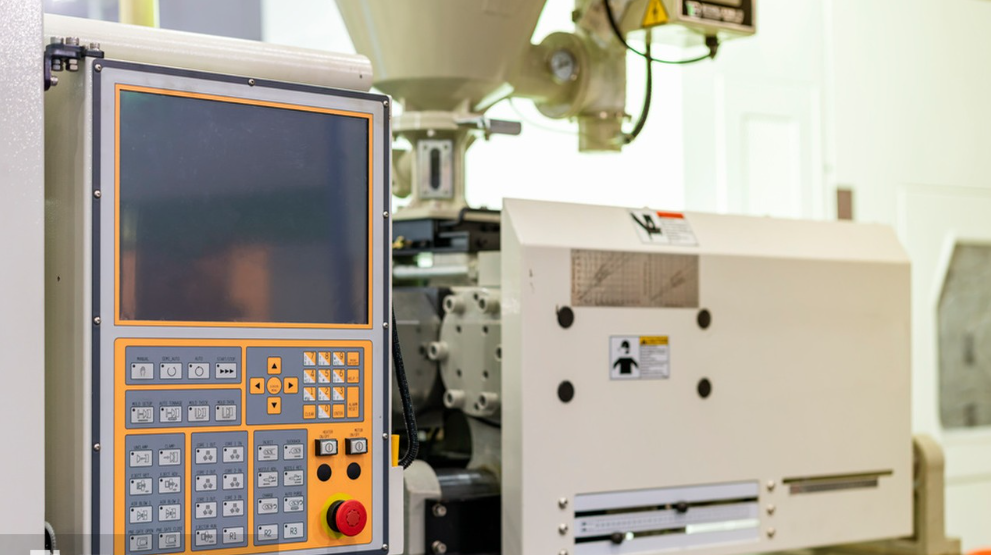
Conclusion
Metal injection molding is a powerful manufacturing technology that combines the benefits of powder metallurgy and plastic injection molding. By using this process, complex metal parts can be produced with high precision, speed, and cost-effectiveness, making it an ideal choice for many industries. However, metal injection molding has its limitations and requires careful process control and design optimization to achieve optimal results. At the end of the day, metal injection molding offers a valuable alternative to traditional machining, casting, or forging, and opens up new possibilities for product design and innovation.
FAQ
Yes, metal injection molding can produce high-strength parts. The strength of the parts produced depends on the materials used and the design of the part. metal injection molding parts can meet or exceed the strength of parts produced using traditional manufacturing methods.
Die casting is another popular metal manufacturing process that is often confused with metal injection molding. The key difference between the two is the materials used. Die casting involves forcing molten metal into a mold cavity, while MIM involves mixing metal powder with a binder and then injecting the mixture into a mold. metal injection molding offers more flexibility in terms of material selection and can produce more complex shapes compared to die casting.