If you are in the manufacturing industry, you know that air bubbles in injection molding can be problematic. Not only do they affect the quality of your products, but they can also lead to waste and affect your bottom line. However, there are ways to avoid air bubbles in injection molding. In this article, we will go over some of the best practices that professionals use to prevent air bubbles in injection molding.
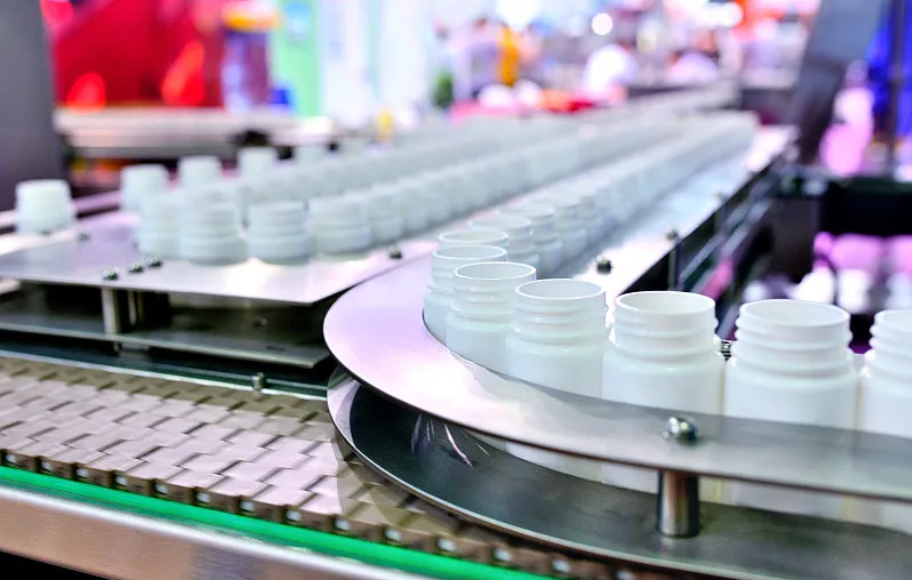
- Ensure Proper Venting
One of the main causes of air bubbles in injection molding is improper venting. To avoid this, it is essential to have enough vents for the plastic to flow through during the injection process. These vents are typically small, thin channels that allow air to escape during the injection process. Without sufficient venting, the air gets trapped between the plastic and the mold, causing air bubbles.
- Check Your Injection Speed
Another key factor that can cause air bubbles in injection molding is the injection speed. If the injection speed is too fast, the plastic material will move too quickly, not allowing enough time for air to escape. This can lead to air bubbles forming in the final product. To avoid this, it’s important to find the optimal injection speed that allows for proper air release.
- Use High-Quality Materials
The quality of the plastic material used in injection molding can also affect the occurrence of air bubbles. Poor-quality materials may contain impurities or debris, which can contribute to air bubbles forming. Therefore, it is crucial to use high-quality plastic materials that have gone through quality control measures. This will help to ensure that the plastic is free of any contaminants that could cause air bubbles.
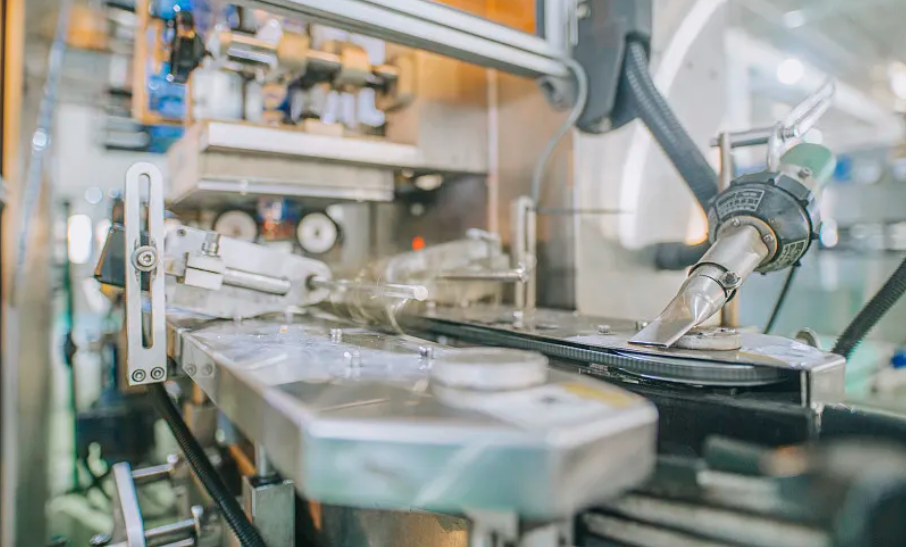
- Minimize the Material’s Heat History
The heat history of the plastic material can also contribute to air bubbles in injection molding. When plastic is heated and cooled repeatedly, it can create air pockets within the material. This, in turn, can lead to air bubbles forming during the injection molding process. To avoid this, it’s best to minimize the plastic’s heat history by using virgin materials and keeping the material’s temperature in check throughout the injection molding process.
Conclusion
To avoid air bubbles in injection molding, it’s important to ensure proper venting, check injection speed, use high-quality materials, and minimize the material’s heat history. By following these best practices, you will be able to reduce the occurrence of air bubbles and improve the quality of your final products. Remember, prevention is always better than cure. So, pay attention to these details, and you’ll be well on your way to success in injection molding.