Surface finishing process The use of modern physics, chemistry, metallology and heat treatment and other disciplines of technology to change the status and properties of the surface of the part, so that it and the core material for optimal combination to achieve the predetermined performance requirements of the process method, called surface finishing.
Surface finishing action:
Improve surface corrosion resistance and wear resistance, slow down, eliminate and repair material surface changes and damage.
To give ordinary materials a surface with a special function.
Save energy, reduce costs and improve the environment.
For metal parts, our most commonly used surface finishing methods are: mechanical grinding, chemical treatment, surface heat treatment, spray surface, etc.

Surface finishing technology
1.Surface heat treatment – surface quenching
Surface quenching refers to the heat treatment method of strengthening the surface of parts by using rapid heating to austenitize the surface without changing the chemical composition of the steel and the core structure.
Surface hardening purpose:
① The surface has high hardness, wear resistance and fatigue limit;
The heart has sufficient plasticity and toughness under the condition of maintaining a certain strength and hardness. Hard on the outside but tough on the inside.
Suitable for parts that withstand bending, torsion, friction and impact.
Materials for surface hardening:
(1) 0.4-0.5%C medium carbon steel. If the carbon content is too low, the surface hardness and wear resistance will decrease. Carbon content is too high, the toughness of the heart decreases.
(2) Cast iron improves its surface wear resistance.
Preliminary heat treatment:
(1) Process: tempering or normalizing for structural steel. The former has high performance and is used for important parts with high requirements, while the latter is used for ordinary parts with low requirements.
(2) Objective: To prepare the tissue for surface quenching; Obtain final cardiac tissue.
2.Thermal spraying
Thermal spraying is the melting of metal or non-metallic materials by heating, continuous blowing of compressed gas to the surface of the parts, forming a coating firmly combined with the matrix, and obtaining the required physical and chemical properties from the surface of the parts.
Instructions:
① The spraying heat source can be gas flame, electric arc, plasma arc or laser beam;
② Spraying materials can be metals, alloys, metal oxides and carbides, ceramics and plastics, etc. The material form can be wire, bar or powder.
③ The spray matrix can be solid materials such as metal, ceramic, glass, plastic, gypsum, wood, cloth, paper and so on.
④ The coating thickness of the spray is tens of microns to several millimeters.
Characteristics of thermal spraying:
① Flexible process, wide range of application. Thermal spraying construction objects can be large or small, small to the 10mm inner hole (line explosion spraying), large to Bridges, iron towers (flame wire spraying or arc spraying), can be sprayed indoors, can also be operated in the field; It can be sprayed in whole or in part.
② The matrix and spraying materials are extensive. Various physical and chemical properties of the workpiece surface can be obtained by spraying different materials.
③ The workpiece stress deformation is small. The matrix can maintain a low temperature, and the stress deformation of the workpiece is very small
④ High production efficiency. The weight of the spray material per hour is from a few kilograms to tens of kilograms, and the deposition efficiency is very high.
Applications of thermal spraying:
① Anti-corrosion: mainly used for large-scale sluice steel gates, paper machine dryer, coal mine underground steel structure, high voltage transmission tower, TV antenna, large steel Bridges, chemical plant tanks and pipelines anti-corrosion spraying.
② Anti-wear: repair worn parts by spraying, or spray wear-resistant materials on the parts easy to wear, such as fan spindle, blast furnace tuyere, automobile crankshaft, machine tool spindle, machine guide rail, diesel engine cylinder liner, oil field drill pipe, agricultural machinery blade, etc.
③ Special functional layer: Some special properties of the surface layer are obtained by spraying, such as high temperature resistance, heat insulation, conductivity, insulation, anti-radiation, etc., which are widely used in aerospace and atomic energy departments.
3.sandblast
Sandblasting is a process that uses the sand pellets and iron pellets sprayed at high speed to impact the surface of the workpiece in order to improve the mechanical properties of parts and change the surface state.
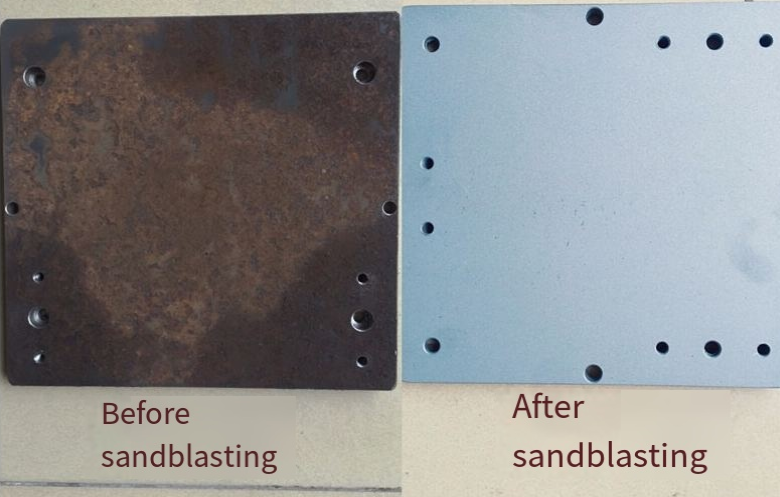
There are usually two methods of shot peening: manual operation and mechanical operation.
Shot peening is usually sand or iron pellets with a diameter of 0.5~2mm. The material of sand particles is mostly A12O3 or SiO2.
The effect of surface treatment is related to the size of the pellet, spraying speed and duration.
Shot peening is used to improve the mechanical strength of parts, wear resistance, fatigue resistance and corrosion resistance, and can also be used for surface extinction, skin removal and elimination of casting, forging, welding residual stress.
4.polishing
Polishing is a finishing processing method to modify the surface of the parts, generally can only get a smooth surface, can not improve or even maintain the original processing accuracy, with different pre-processing conditions, the Ra value after polishing can reach 1.6~ 0.008um.
1)Mechanical polishing
Wheel polishing: The high-speed rotating flexible polishing wheel and extremely fine abrasive are used to roll and micro-cut the workpiece surface to achieve polishing. The polishing wheel is made of multiple layers of canvas, felt or leather and is used for polishing larger parts.
Roller polishing and vibration polishing: the workpiece, abrasive and polishing liquid into the drum or vibration box, the roller slowly rolling or vibration box vibration, so that the workpiece and the workpiece, the workpiece and the abrasive friction, coupled with the chemical action of the polishing liquid, remove the oil, rust layer on the surface of the workpiece, grinding away the convex peak, so as to obtain a smooth surface. For the polishing of small and large parts, the latter has higher productivity and better polishing effect than the former.
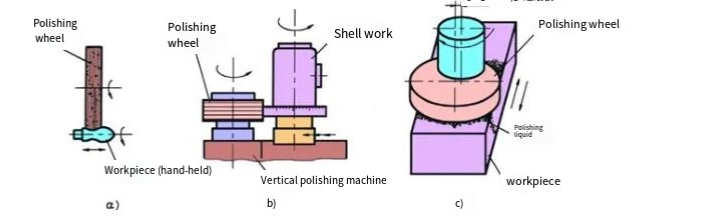
2) Chemical polishing
The metal parts are immersed in a special chemical solution, and the surface of the parts is polished by using the phenomenon that the convex part of the metal surface dissolves faster than the concave part.
3) Electrochemical polishing
Electrochemical polishing is similar to chemical polishing, the difference is that the direct current is also passed, the workpiece is connected to the positive newspaper, resulting in anode dissolution, but also the use of the metal surface of the convex part than the concave part of the dissolution speed of the phenomenon of polishing.
Application of metal surface finishing
Metal surface finishing has a wide range of applications in various industries and applications. The following are some applications of metal surface finishing in different fields:
Automotive Industry: Surface finishing is used in automotive manufacturing to improve appearance, corrosion resistance and wear resistance. For example, chrome plating and spraying are common methods.
Construction: In the construction industry, metal materials are often used for exterior walls, roofs and structures. Surface treatment can improve its corrosion resistance and appearance.
Electronic equipment: Metal components in electronic equipment usually require a fine surface treatment to improve electrical conductivity and corrosion resistance.
Aerospace: In the aerospace sector, metal products need to undergo rigorous surface treatment to improve their performance while remaining lightweight.
Food processing: In the food processing industry, metal products need to meet hygiene and hygiene requirements. The surface treatment ensures that it meets the standard.
Medical devices: The metal surface treatment of medical devices requires a high degree of biocompatibility and corrosion resistance.
conclusion
The precision machining process and technology of metal surfaces are crucial for improving the performance and appearance of metal products. In the future, we can look forward to the development of more environmentally friendly, automated, personalized, and high-performance metal surface finishing methods. The application field of metal materials will continue to expand, and metal surface finishing will continue to play a crucial role in meeting the growing demand.