Plastic injection molding is an integral part of countless industries, ranging from automotive to medical, consumer goods to electronics, and beyond. It is a manufacturing technique where plastic material is heated until malleable and then injected into a mold to solidify, producing a variety of parts and components. The power and potential of this process, however, hinges on a critical factor – the choice of plastic material.
This selection determines not only the physical and chemical properties of the final product, but also the manufacturing efficiency and sustainability. Making an informed, strategic choice of material can greatly enhance the functionality, durability, and aesthetics of the final product, as well as the overall profitability and environmental impact of the manufacturing process.
This paper explores how to navigate the complex landscape of plastic materials in injection molding to make optimal choices.

Understanding Plastic Injection Molding
Injection molding is a versatile manufacturing process that has revolutionized the production of plastic parts. It involves melting plastic pellets and injecting them under high pressure into a mold cavity. Once inside, the material is cooled and solidifies into the shape of the cavity, creating a part or component. This process is highly repeatable, making it ideal for mass-producing complex plastic parts with high precision and low scrap rates.
However, the success of the process isn’t solely dependent on the technique itself but also the plastic material used. The selected material has a significant impact on the performance characteristics of the final product, including its strength, flexibility, temperature resistance, and visual appearance. For example, a plastic part used in a high-heat environment requires a material with a high melting point. In contrast, a plastic toy for a child needs to be made from a material that is safe, durable, and easy to color.
Furthermore, the chosen material influences the injection molding process itself, affecting factors such as melting point, cooling rate, shrinkage, and the pressure needed for injection. Thus, understanding and selecting the appropriate plastic material is not just about meeting product specifications; it’s also about optimizing the manufacturing process and achieving economic and environmental sustainability.
Categories of Plastic Materials
In the realm of plastic injection molding, there are numerous types of materials each with unique characteristics and applications. Broadly, these materials can be classified into three categories: thermoplastics, thermosets, and elastomers.
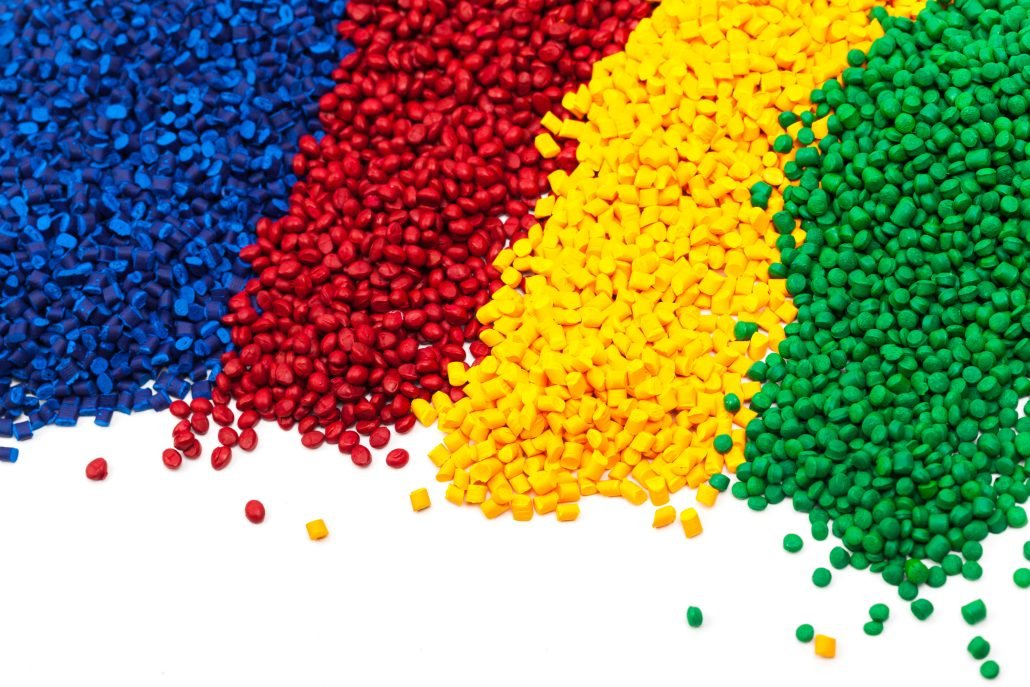
Thermoplastics
are plastics that become pliable or moldable above a specific temperature and solidify upon cooling. They are widely used in injection molding due to their versatility and recyclability. Here are 15 common thermoplastics:
1.Acrylonitrile Butadiene Styrene (ABS)
2.Polycarbonate (PC)
3.Polypropylene (PP)
4.Polyethylene (PE)
5.Polyvinyl Chloride (PVC)
6.Polystyrene (PS)
7.Polyethylene Terephthalate (PET)
8.Polybutylene Terephthalate (PBT)
9.Polyether Ether Ketone (PEEK)
10.Polyphenylene Sulfide (PPS)
11.Polymethyl Methacrylate (PMMA)
12.Polyoxymethylene (POM)
13.Polyurethane (PU)
14.Polyphenylsulfone (PPSU)
15.Polysulfone (PSU)
Thermosets
are materials that irreversibly cure. The curing process transforms them into a solid material that cannot be remolded or softened again. Here are 15 common thermosets:
1.Epoxy Resin
2.Phenol Formaldehyde Resin
3.Urea Formaldehyde Resin
4.Melamine Formaldehyde Resin
5.Polyester Resin
7.Bakelite
8.Vulcanized Rubber
9.Urea-Formaldehyde
10.Alkyd
11.Silicone
12.Polyurethane Resin
13.Duroplast
14.Cyanate Ester
15.Polydicyclopentadiene (pDCPD)
Elastomers
are polymers with viscoelasticity, meaning they exhibit both viscosity and elasticity. These materials are highly flexible and resilient, capable of significant deformation under stress. Here are 15 common elastomers:
1.Natural Rubber
2.Polybutadiene Rubber (BR)
3.Styrene-Butadiene Rubber (SBR)
4.Ethylene Propylene Diene Monomer (EPDM)
5.Nitrile Rubber (NBR)
6.Chloroprene Rubber (CR)
7.Silicone Rubber
8.Fluorocarbon Elastomers (FKM)
9.Polyurethane Rubber
10.Butyl Rubber (IIR)
11.Ethylene-Vinyl Acetate (EVA)
12.Polysulfide Rubber (PSR)
13.Acrylic Rubber (ACM)
14.Ethylene Acrylic Rubber (AEM)
15.Fluorosilicone Rubber (FVMQ)
By understanding the distinct categories and their associated materials, one can make more informed decisions in the selection of materials for injection molding.
Specific material examples
Within the wide range of materials used for injection molding, certain plastics stand out due to their specific properties and wide applications. Let’s understand their unique characteristics, common uses, and injection molding considerations together through the following content, which can guide us in selecting the most suitable materials for specific applications.
Polyethylene (PE)
As the most common plastic in the world, PE is praised for its toughness, flexibility, and resistance to chemicals and moisture. It is often used for packaging films, bags, bottles, and containers. However, when using PE for injection molding, attention must be paid to its high shrinkage rate and low UV resistance, which may affect the design and lifespan of the molded components.
Polypropylene (PP)
PP is renowned for its excellent chemical stability, wear resistance, and fatigue resistance. It is widely used in automotive components, household goods, and medical equipment. However, due to its high melting point and crystal structure, PP requires special attention during injection molding, such as controlling the melting temperature and managing the cooling process.
Polyvinyl chloride (PVC)
PVC is one of the most commonly used thermoplastic materials and is widely used due to its high hardness and good flame retardancy. For example, it can be seen in door and window frames, pipelines, and non food packaging. However, handling PVC may release toxic smoke, so it is necessary to pay attention to ventilation and safety protection.
Polystyrene (PS)
PS is a lightweight and economical option commonly used for making disposable products such as tableware and containers. It may be crystal transparent, making it an ideal choice for food packaging and Laboratory equipment. However, its brittleness and weak resistance to ultraviolet radiation and harsh weather conditions limit its use in outdoor applications.
Polyethylene terephthalate (PET)
PET is a versatile plastic with excellent chemical resistance, dimensional stability, and electrical insulation properties. It is widely used in soft drink bottles, food packaging and Synthetic fiber. However, it should be noted that PET can absorb moisture from the environment, which may affect the molding process.
Key factors in material selection
The selection of materials has a significant impact on the molding process and the characteristics of the final product. The following are the key factors I have considered:
Mechanical properties: Depending on the application, different mechanical properties may be required. This includes tensile strength, impact resistance, flexibility, and hardness. For example, if it is expected that the part will withstand heavy loads, high-strength plastics such as polycarbonate or nylon may be preferred.
Thermal performance: If the product is used in high-temperature environments, materials with high thermal stability, such as PEEK or PSU, must be selected.
Chemical resistance: For applications exposed to various chemicals, materials with strong chemical resistance, such as polyethylene or polypropylene, are usually chosen.
Cost: The cost of raw materials will have a significant impact on the entire project budget. Finding a balance between performance and cost is crucial.
Regulatory compliance: For certain industries, such as healthcare or food and beverage, materials must comply with specific standards and regulations.
Which Plastic Material Is Right for Your Injection Molding Project?
For plastic injection molding projects, the correct selection of suitable plastic materials is crucial. Different projects have different requirements and characteristics, so all factors need to be considered. Here are some specific examples:
Medical device parts
For medical device parts, hygiene and safety are the primary considerations. The material should have excellent biocompatibility and corrosion resistance to ensure that the product does not have adverse effects on the human body. Commonly used material choices include polypropylene (PP) and polycarbonate (PC), which have excellent medical grade performance.
Electronic product shell
The electronic product shell needs to have good electrical insulation performance and weather resistance. Material selection should consider characteristics such as anti-static, flame retardant, and high-temperature resistance. Common choices include polyimide (PI) and Polyphenylene sulfide (PPE), which can meet the special requirements of electronic product housings.
Household appliance parts
For household appliance parts, important considerations include heat resistance, wear resistance, and chemical resistance. The material should have good mechanical strength and stability to meet the requirements of daily use. Commonly used choices include nylon (PA) and polyamide (POM), which have a wide range of applications in the field of household appliances.
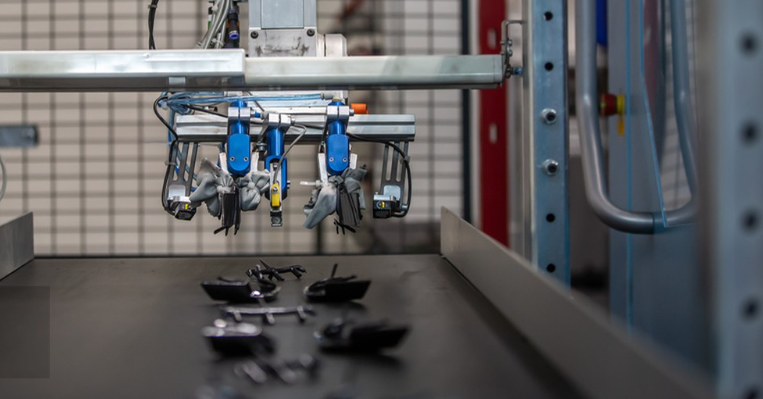
Case study
Now, let’s use some specific Case study to better understand how to select injection molding materials in the actual scene and the factors that need attention in this process.
Case 1: Food Packaging
A company plans to produce a new food packaging product that requires heat resistance, high transparency, and good chemical stability. After considering various possible materials, they chose polyethylene terephthalate (PET). PET has strong chemical resistance, high dimensional stability, and can withstand high temperatures, making it suitable for hot filling processes. It has high transparency and can clearly display the food inside the packaging. In addition, PET also has good recyclability and meets the company’s environmental requirements.
Case 2: Automotive Components
Automobile manufacturers need a material that is both wear-resistant and resistant to the high temperatures generated during the operation of the car to manufacture certain engine components. After comparing various possible materials, they chose polypropylene (PP). PP not only has good wear resistance and high temperature resistance, but also has a relatively low cost and is suitable for large-scale production.
conclusion
Through the discussion in this article, we can conclude the importance of selecting suitable materials in injection molding. Material selection directly affects the performance, appearance, cost, and environmental sustainability of products. In the process of injection molding, reasonable selection of materials can improve the functionality, durability, and appearance quality of products, as well as increase production efficiency and profits. At the same time, the correct material selection can also reduce scrap rates, save resources, and meet regulatory and environmental requirements.
Your best injection molding services
As a plastic injection molding manufacturer, we are well aware of the importance of selecting the right materials for product quality and customer satisfaction. We have rich experience and professional knowledge to help you make wise decisions in material selection.
Whether you need to produce automotive parts or medical devices, we can provide you with high-quality injection molding solutions. We collaborate with excellent global material suppliers to ensure that you receive the materials that best meet your product needs. We have advanced equipment and technology that can accurately inject and shape products that meet your requirements.
If you need to inquire or order injection molded products, please contact us immediately. Our professional team will work with you to understand your needs and provide you with customized solutions. We are committed to providing you with high-quality products and excellent customer service.
E-Mail:gloria.wu@longshengmfg.com
FAQ
Choosing the appropriate plastic material depends on the specific requirements of the product, such as strength, heat resistance, chemical stability, etc. We can provide professional advice based on your needs.
The cost of materials depends on multiple factors, including material type, procurement volume, and market supply and demand situation. We can provide competitive prices and help you strike a balance between cost and quality.
This depends on the usage conditions and required performance characteristics of your product. Thermoplastics can be repeatedly heated and reshaped, while thermosetting plastics cannot be reshaped after hardening.