In this article, we cover everything you need to know about sheet metal fabrication cost.We hope this article has provided you with valuable insights into sheet metal fabrication cost.
Factors Affecting the Cost of Sheet Metal Fabrication
Sheet metal fabrication is the process of manufacturing a product or component using sheet metal. The cost of sheet metal fabrication depends on various factors, and understanding them can help you make informed decisions when it comes to your project.
Size and Complexity of the Product
The size and complexity of the product are the main factors that affect the cost of sheet metal fabrication. The larger and more complex the product is, the higher the cost will be. A larger product requires more material, and more time and effort to manufacture. Similarly, a more complex product may require additional tooling or processing steps, which can add to the cost.

Quantity of the Product
The quantity of the product also affects the cost of sheet metal fabrication. The more products that need to be manufactured, the lower the cost per unit will be. This is because the manufacturer can take advantage of economies of scale, such as bulk purchasing of raw materials, and streamlined production processes. However, it’s important to note that there is often a minimum order quantity, below which the cost per unit may be higher.
Material Used
The type of material used for sheet metal fabrication also affects the cost. The cost of raw materials varies depending on the availability, quality, and type of material. For example, stainless steel is more expensive than mild steel, and exotic alloys can be even more costly. The thickness of the material also affects the cost, with thicker sheets costing more than thinner ones. Additionally, the finish of the material can also affect the cost, with polished or plated finishes costing more than raw or unpolished finishes.
Manufacturing Process
The manufacturing process used for sheet metal fabrication also affects the cost. Some processes are more expensive than others, such as laser cutting or CNC machining. These processes require specialized equipment and skilled operators, which can add to the cost. On the other hand, simpler processes like stamping or bending may be less expensive, but may not be suitable for all products or materials.
Conclusion
Sheet metal fabrication cost can vary widely depending on several factors. It’s essential to work with a reliable and experienced sheet metal fabrication company to ensure that you get the best quality product at a fair price. When planning your project, consider the size and complexity of your product, the quantity you need, the type of material you want to use, and the manufacturing process that will suit your needs. By understanding these factors, you can make informed decisions and optimize the cost and quality of your sheet metal fabrication project.
Sheet Metal Fabrication Cost Breakdown
As a business owner or engineer, it’s essential to understand the cost breakdown of sheet metal fabrication. Knowing how much each component of the process costs can help you make informed decisions and optimize your budget. In this article, we’ll explore the key factors that influence sheet metal fabrication costs.

Material Costs
The selection of materials is one of the most critical factors that determine sheet metal fabrication costs. The cost of raw materials depends on their availability, quality, and quantity. The most commonly used materials in sheet metal fabrication include steel, aluminum, and copper. Each of these materials has a different price point, with steel being the most affordable and copper being the most expensive.
Labor Costs
Labor costs are another crucial factor to consider when calculating sheet metal fabrication expenses. The cost of labor depends on the complexity of the fabrication process, the level of expertise required, and the location of the facility. In general, labor costs for sheet metal fabrication can range from $50 to $150 per hour.
Equipment Costs
The cost of the equipment used in sheet metal fabrication also influences the overall cost. The equipment required for sheet metal fabrication includes cutting machines, bending machines, welding machines, and finishing equipment. The cost of this equipment varies depending on the type of machinery, its quality, and its age.
Design Complexity
The complexity of the design is another factor that affects sheet metal fabrication costs. More complex designs require more time and effort to fabricate, which increases the labor costs. Additionally, intricate designs may require specialized equipment or processes, which can further increase the cost of fabrication.
Volume of Production
The volume of production is another critical factor that determines the cost of sheet metal fabrication. High volume production runs are generally more cost-effective than small production runs. This is because the fixed costs associated with sheet metal fabrication, such as equipment and labor, can be spread out over a larger number of units.
Final Thoughts
Sheet metal fabrication costs can vary widely depending on several factors. By understanding the key cost drivers, you can optimize your budget and make informed decisions about your fabrication needs. Remember to consider material costs, labor costs, equipment costs, design complexity, and volume of production when calculating your sheet metal fabrication expenses.
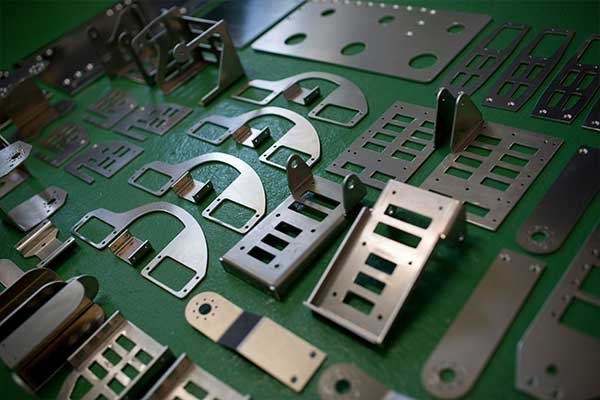
Sheet Metal Fabrication Cost Calculator
Sheet metal fabrication is a crucial process in many industries, including construction, automotive, and aerospace. However, it can be a costly process, especially if you don’t have a clear understanding of the various factors that affect the cost. This is where a sheet metal fabrication cost calculator comes in handy. In this article, we’ll show you how to use a sheet metal fabrication cost calculator to save money and improve your bottom line.
What is a Sheet Metal Fabrication Cost Calculator?
A sheet metal fabrication cost calculator is a tool that helps you estimate the cost of your sheet metal fabrication project. It takes into account several factors such as the type of material, the size and complexity of the project, and the quantity of parts needed. By inputting this information, the calculator provides an estimate of the total cost of the project.
Benefits of Using a Sheet Metal Fabrication Cost Calculator
Using a sheet metal fabrication cost calculator has several benefits, including:
- Accurate estimates: A cost calculator takes into account all the factors that affect the cost of your project, giving you a more accurate estimate of the total cost.
- Time-saving: With a cost calculator, you can quickly get an estimate of the cost of your project without having to go through the time-consuming process of manually calculating the cost.
- Cost-saving: By getting an accurate estimate of the cost of your project, you can make informed decisions and find ways to save money on your sheet metal fabrication project.
- Allows for better planning: With the help of a cost calculator, you can plan your sheet metal fabrication project more effectively. You can determine the most cost-effective materials and the quantity of parts needed, which can help you avoid overspending.
- Provides transparency: A cost calculator provides transparency in the pricing of your sheet metal fabrication project. You can see precisely how much each part of the project will cost, which can help you make informed decisions about cost reduction.
How to Use a Sheet Metal Fabrication Cost Calculator
Using a sheet metal fabrication cost calculator is a straightforward process. Here are the steps:
- Choose a reliable and accurate cost calculator tool. There are many cost calculators available online, so be sure to choose one that is accurate and reliable.
- Enter the project details. Input the details of your project, such as the type of material, the size and complexity of the project, and the quantity of parts needed.
- Get the estimate. Once you have entered all the necessary details, the cost calculator will provide you with an estimate of the total cost of your project.
- Evaluate the estimate. Review the estimate and consider ways to reduce the cost of your project if necessary.
- Make adjustments. If you need to reduce the cost of your project, consider making adjustments such as changing the material or the quantity of parts needed.
- Compare prices. Once you have received an estimate for your sheet metal fabrication project, compare prices with other cost calculators or suppliers to ensure you are getting the best deal.

Conclusion
A sheet metal fabrication cost calculator is an essential tool for anyone involved in sheet metal fabrication. By using a cost calculator, you can get an accurate estimate of the cost of your project, saving you time and money. Additionally, cost calculators provide transparency in pricing, allowing you to make informed decisions about cost reduction. So, if you’re involved in sheet metal fabrication, be sure to use a cost calculator for all your projects.
Sheet Metal Fabrication Cost Calculation Formula
Sheet metal fabrication cost refers to the total cost required to manufacture a sheet metal product, including material cost, labor cost, equipment depreciation cost, and other expenses. The calculation of these costs is the basis for setting the price of sheet metal products and the source of profit for sheet metal manufacturing companies.
Material Cost
Material cost is the cost of all raw materials required to manufacture a sheet metal product. The material cost calculation formula is:
Material cost = Sheet metal price × Sheet metal usage
Where sheet metal usage refers to the amount of sheet metal required to manufacture a sheet metal product, and sheet metal price refers to the purchase price of sheet metal per square meter.
Labor Cost
Labor cost refers to all labor costs required to manufacture sheet metal products, including wages, social security, and benefits for workers. In calculating labor costs, we need to consider workers’ wages and processing time. The formula for calculating labor cost is as follows:
Labor cost = Worker hourly wage × Processing time
Where worker hourly wage refers to the hourly wage of workers, and processing time refers to the total working hours required to manufacture a sheet metal product.
Equipment Depreciation Cost
Equipment depreciation cost refers to the cost of depreciating equipment that sheet metal manufacturing companies need to maintain normal operation. The formula for calculating equipment depreciation cost is as follows:
Equipment depreciation cost = Equipment purchase price × Depreciation rate × Processing time ÷ Equipment service life
Where equipment purchase price refers to the purchase price of equipment, depreciation rate refers to the annual depreciation rate of equipment, and equipment service life refers to the service life of equipment.
Other Expenses
When calculating fabrication costs, other expenses also need to be considered. These expenses include maintenance costs before and after processing, transportation costs, and other miscellaneous expenses. The formula for calculating other expenses is as follows:
Other expenses = Maintenance costs before and after processing + Transportation costs + Other miscellaneous expenses
Summary
The sum of the above four costs is the fabrication cost. Sheet metal manufacturing companies can improve their profitability and gain a competitive advantage in the market by controlling their costs reasonably. To reduce costs, sheet metal manufacturing companies can take measures such as optimizing processes, improving production efficiency, and reducing material waste.

How to Reduce Sheet Metal Fabrication Cost
Sheet metal fabrication is a crucial process in manufacturing various products, including automotive parts, electronics, and construction materials. However, the cost of sheet metal fabrication can be high, especially when the design is complex or requires a large amount of material. In this article, we will discuss some tips on how to reduce sheet metal fabrication cost without compromising quality.
1. Optimize Design for Manufacturing
One way to reduce the cost of sheet metal fabrication is to optimize the design for manufacturing. This means designing the part with the fabrication process in mind. Designers should consider the material, the thickness of the sheet metal, the bending radius, and the tolerances required. By doing this, the fabrication process can be simplified, and the part can be produced more efficiently, reducing the cost.
2. Choose the Right Material
Choosing the right material is another way to reduce sheet metal fabrication cost. Some materials, such as stainless steel, are more expensive than others, such as aluminum. By selecting the right material for the project, you can reduce the cost of the material, which will have a significant impact on the overall fabrication cost.
3. Minimize Scrap Material
Minimizing scrap material is another way to reduce the cost of sheet metal fabrication. When designing the part, try to minimize the amount of scrap material that will be generated during the fabrication process. This can be done by optimizing the design and nesting the parts efficiently. By doing this, you can reduce the material waste and the cost of the fabrication process.
4. Consider Outsourcing
Outsourcing the sheet metal fabrication process can also be a cost-effective option. Many companies specialize in sheet metal fabrication and can offer competitive pricing due to economies of scale. Outsourcing can also reduce the need for expensive equipment, labor, and training.
5. Use Standard Sizes
Using standard sizes for sheet metal can also reduce the cost of fabrication. Standard sizes are more readily available and can be purchased in larger quantities at a lower cost. By using standard sizes, you can reduce the cost of material and fabrication, as well as the lead time required to receive the material.
In conclusion, there are many ways to reduce the cost of sheet metal fabrication without compromising quality. By optimizing the design for manufacturing, choosing the right material, minimizing scrap material, considering outsourcing, and using standard sizes, you can significantly reduce the cost of the fabrication process.
Is Sheet Metal Cheaper Than Machining?
When it comes to manufacturing parts or components, cost is always a significant factor to consider. One common material used for manufacturing is sheet metal, while machining is another popular process. The question is whether sheet metal is cheaper than machining.
The answer depends on several factors, including the complexity of the part, the tolerances required, the quantity needed, and the equipment available. In general, sheet metal fabrication tends to be less expensive than machining for simple parts with basic shapes and features. Machining, on the other hand, is often the more cost-effective option for more complex parts or components requiring tighter tolerances.
Sheet metal fabrication involves cutting, bending, and forming metal sheets into the desired shape using specialized equipment. It requires less labor and is faster than machining, which involves removing material from a solid block of metal through cutting, drilling, and other processes to create the desired shape.
Another factor to consider is the quantity needed. Sheet metal fabrication is often more cost-effective for small to medium-sized production runs, while machining may be more economical for larger quantities.
In conclusion, whether sheet metal fabrication or machining is cheaper depends on the specific requirements of the part or component. While sheet metal may be less expensive for simple parts, machining may be the more cost-effective option for more complex components.
FAQ
Sheet metal fabrication is the process of transforming flat sheets of metal into a desired shape or form using various techniques such as cutting, bending, welding, and finishing.
Sheet metal fabrication cost is calculated based on several factors such as material, design, quantity, and production time. Material cost is determined by the type and thickness of the material used. Labor cost is determined by the complexity of the design, the number of parts, and the production time. Overhead cost includes all other expenses associated with sheet metal fabrication.
Yes, sheet metal fabrication cost can be reduced by choosing the right material, simplifying the design, ordering in bulk, and optimizing production time.
The time required for sheet metal fabrication depends on several factors such as the complexity of the design, the number of parts, and the production time. Simple designs with fewer parts can be fabricated quickly, while complex designs with multiple parts may take longer.