CNC milling machines are widely used in the manufacturing industry to create complex surfaces. These machines rely on various parts to ensure precision and accuracy during the milling process. The parts used in CNC milling machines are critical in determining the quality of the final product. In this article, we will discuss the essential components of CNC milling machines and their functions in detail.

Spindle
One essential component of CNC milling machines is the spindle. The spindle is responsible for rotating the cutting tool, which is used to remove material from the workpiece. The spindle’s speed and power are critical in determining the quality of the milling process. The spindle’s speed determines the rate at which the cutting tool removes material from the workpiece. The power of the spindle determines the amount of force the cutting tool can apply to the workpiece. The spindle’s accuracy is also crucial in ensuring that the milling process is precise.
Tool Holder
Another critical part of the CNC milling machine is the tool holder. The tool holder secures the cutting tool in place and ensures that it remains stable during the milling process. The tool holder also allows for quick and easy tool changes, which is essential when milling different types of materials. The tool holder’s stability is critical in ensuring that the cutting tool can remove material from the workpiece accurately. The tool holder’s design and material used in its construction also determine its ability to withstand the cutting tool’s force and vibration during the milling process.
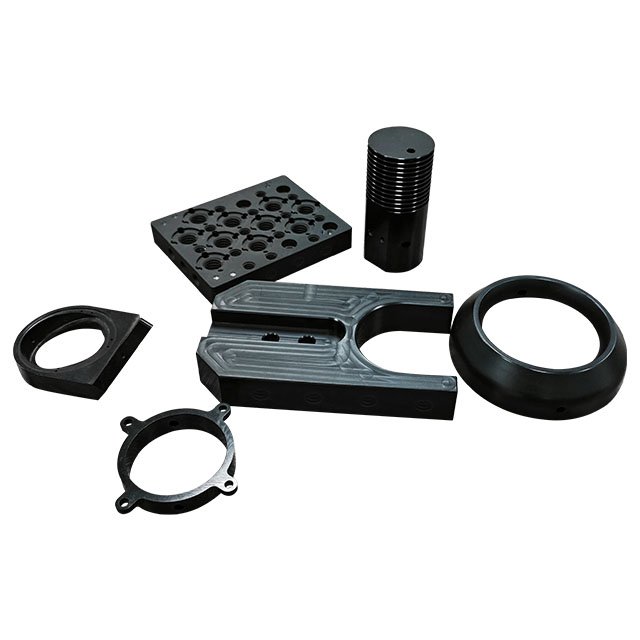
Control System
The CNC milling machine’s control system is also a critical component in the creation of complex surfaces. The control system uses computer software to control the machine’s movements and ensure that the milling process is precise and accurate. The software also allows for the creation of complex designs that can be replicated multiple times. The control system’s accuracy is critical in ensuring that the milling process produces the desired results. The software used in the control system also determines the complexity of the designs that can be created and the speed at which the milling process can be completed.
Clamping System
Finally, the workpiece’s clamping system is also an essential part of the CNC milling machine. The clamping system secures the workpiece in place during the milling process, ensuring that it remains stable and does not move. This is crucial in ensuring that the milling process is accurate and that the desired results are achieved. The clamping system’s design and material used in its construction determine its ability to hold the workpiece firmly in place during the milling process. The clamping system’s stability is also critical in ensuring that the workpiece does not move during the milling process, which can result in inaccuracies.
In conclusion, CNC milling machines rely on various parts to create complex surfaces. The spindle, tool holder, control system, and clamping system all play critical roles in ensuring that the milling process is precise, accurate, and efficient. Each part’s design, material, and accuracy are crucial in determining the quality of the final product. With the advancement of technology, CNC milling machines continue to evolve, and new parts and designs are being developed to improve the milling process’s quality and efficiency.