As a product designer or manufacturer, choosing the right manufacturing process for your product is critical to its success in the market. Two popular methods used in manufacturing are thermoforming and injection molding. Both methods have their pros and cons, and the choice you make will have a significant impact on your product’s features, quality, and cost.
In this comprehensive guide, we’ll explore the differences between these two methods and help you make the best decision for your business. We’ll discuss everything from the types of products you can create, to the cost-effectiveness of each technique, to the impact of materials used. By the end, you’ll have a solid understanding of which option offers the most benefits for your specific needs.
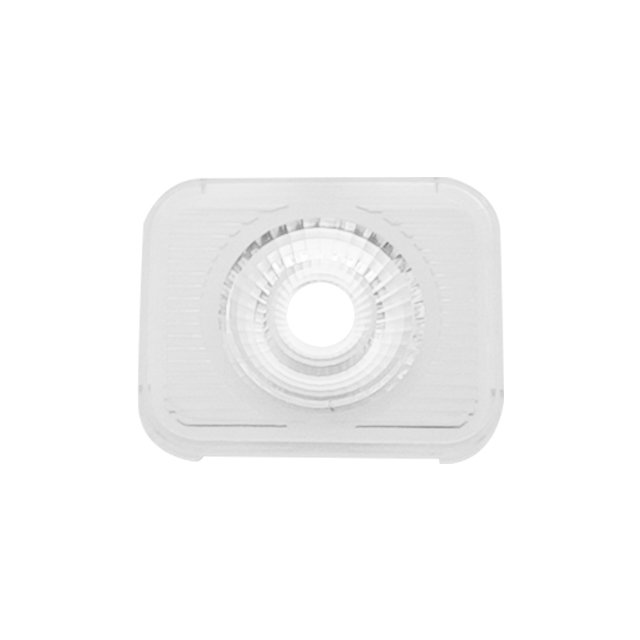
Thermoforming: An Overview
Thermoforming is a manufacturing process that involves heating a sheet of plastic until it is pliable and then forming it into the desired shape using a mold. The mold is a negative of the final product and can be made out of a variety of materials such as wood, plastic, or metal.
Advantages of Thermoforming
One significant advantage of thermoforming is that it is a relatively low-cost method of manufacturing compared to injection molding. Since the mold is not as complex as that used in injection molding, the set-up cost is much lower. Also, the production speed of thermoforming is faster than injection molding for small production runs.
Thermoforming is also very flexible in terms of material selection. A wide range of plastics, including polycarbonate, polyethylene, and PVC, can be used in thermoforming. Furthermore, materials can be easily added or removed from the product based on the requirements of the application.
Disadvantages of Thermoforming
While thermoforming is useful, it also has its disadvantages. For starters, the finish of the product in thermoforming is not as smooth as in injection molding. Thermoformed parts can have visible lines and imperfections on the surface, which may not be suitable for a high-end product.
Thermoforming is also not ideal for products that require tight tolerance or complex geometries. Since the mold is not as precise as in injection molding, the final product may not meet the exact specifications.
Injection Molding: An Overview
Injection molding process that involves injecting molten plastic into a mold under high pressure. The molten plastic then solidifies and forms the desired shape. This process can be repeated with a high degree of consistency, resulting in product uniformity.
Advantages of Injection Molding
Injection molding is ideal for products that require tight tolerances, high-quality finish, and complex geometries. The final product has a smooth surface finish and a high degree of accuracy. Injection molding can achieve higher production speeds than thermoforming, making it more cost-effective for larger production runs.
Injection molding is also more scalable than thermoforming. The molds used in injection molding are typically made of steel, making them more durable and suitable for larger production runs. This durability reduces the maintenance and replacement costs associated with thermoforming molds.
Disadvantages of Injection Molding
The biggest disadvantage of injection molding is the cost of setting up the manufacturing process. The molds used in injection molding are more complex and expensive to make than those used in thermoforming. Furthermore, any changes to the injection molding design require the creation of a new mold, which can be costly.
Injection molding is also less flexible in terms of material selection. While a range of plastics, as well as other materials like metal and glass, can be used in injection molding, the range is more limited than in thermoforming.
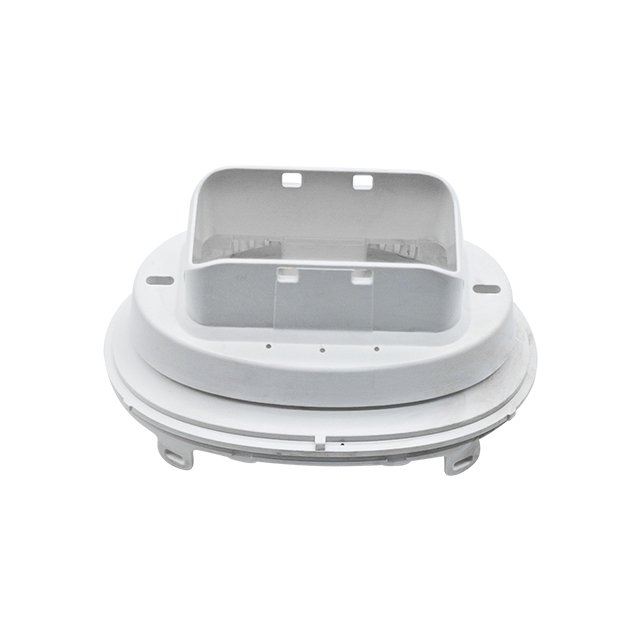
Comparison of Thermoforming vs Injection Molding
While both thermoforming and injection molding are effective manufacturing techniques, there are several key differences between the two. Here are a few of the most important factors to consider:
• Tooling costs: Injection molding requires a costly, complex mold, whereas thermoforming only requires a simple mold that is less expensive to create.
• Volume of production: Injection molding is best suited for high-volume production runs, whereas thermoforming is ideal for producing smaller quantities of products.
• Material options: Injection molding offers a wider range of material options, including specialized materials such as polycarbonate, whereas thermoforming is limited to only a select few materials.
• Customization options: Thermoforming offers a wider range of customization options, including the ability to create products with a variety of textures, colors, and finishes.
Ultimately, the best choice between these two manufacturing techniques will depend on your specific business needs. If you require a highly-detailed, complex part and anticipate large production runs, injection molding may be the best option for you. If you require a simpler, more cost-effective solution and have lower production needs, thermoforming is likely the better choice.
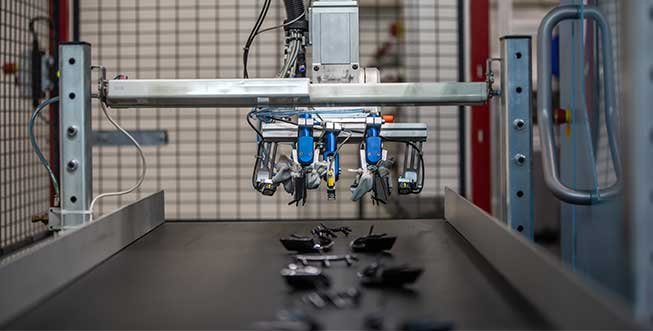
Which One to Choose?
It depends on what you’re looking for. If you’re working on products with complex, intricate designs or require precision with the product parts, injection molding may be the way to go. However, if you’re looking for larger, hollow objects or working with non-standard plastics such as biodegradable materials, thermoforming is your best bet.
Whichever type of manufacturing process you go for, always keep the product design and specifications in mind. Each method has its strengths and weaknesses, and the final decision will largely depend on the specific needs and goals of your business. Ultimately, you need to consider the type of product you’re producing, the materials you’re using, and the quality you’re expecting to determine which process to use.
As you can see, both thermoforming and injection molding offer significant benefits, but it’s up to you to decide which will give you the best results for your product manufacturing process. No matter which method you select, ensure that you partner with a reputable manufacturer and supplier committed to producing quality products.
Conclusion
Both thermoforming and injection molding have their advantages and disadvantages, and the choice you make will depend on the specific requirements of your product. To summarize, thermoforming is a low-cost and flexible manufacturing process that is ideal for small production runs but may not be suitable for products that require tight tolerances or a high-quality surface finishing. Injection molding, on the other hand, is more expensive to set up, but it offers a higher-quality finish, complex geometries, and tight tolerances, making it the better option for larger production runs.