If you’re in the manufacturing industry and looking for ways to produce high-quality metal parts for your products, there are two popular methods that you should consider: CNC machining and metal powder metallurgy. These two methods have their unique advantages, and the choice of method depends on your specific needs and requirements.
CNC Machining
CNC machining is a process that uses computer-controlled machines to cut and shape raw materials into finished products. The process involves designing a 3D model of the desired part using software, which is then converted into a series of instructions that the CNC machine parts follows to produce the final part. This process allows for high accuracy and precision, making it ideal for industries like aerospace and medical equipment.
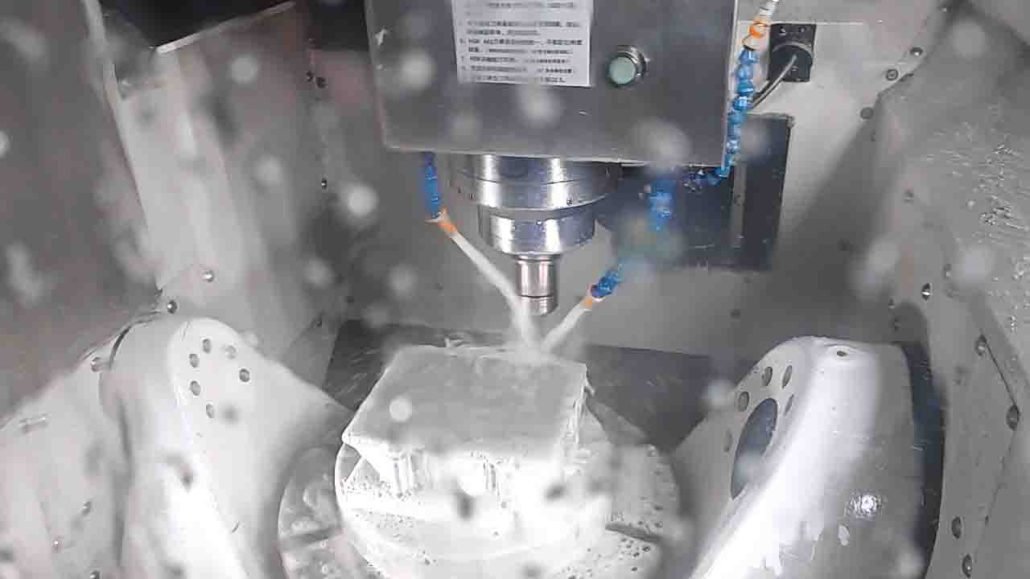
The benefits of CNC machining include:
- High accuracy and precision: CNC machines are capable of producing parts with extremely tight tolerances.
- Fast production speed: With the help of computer programming, CNC machines can produce parts much faster than traditional machining methods.
- Low production cost for large quantities: CNC machines can produce parts in large volumes, which reduces the overall cost per unit.
Metal Powder Metallurgy
Metal powder metallurgy is a process that involves creating metal parts by compacting metal powders in a die and then sintering them at high temperatures. This process is ideal for producing complex parts with a high degree of uniformity and consistency. The process begins with the selection of metal powders, which are then mixed with a binding agent and compacted into the desired shape using a die. The compacted part is then placed in a furnace and sintered at high temperatures to create a strong bond between the metal particles.
The advantages of metal powder metallurgy include:
- Ability to produce complex parts with a high degree of uniformity: This process allows for the creation of parts with intricate geometries and tight tolerances.
- High strength and durability of finished products: The sintering process creates a strong bond between the metal particles, resulting in parts with high strength and durability.
- Cost-effective for small production runs: Metal powder metallurgy is an economical choice for small production runs because it eliminates the need for expensive tooling.

Conclusion
Both CNC machining and metal powder metallurgy are effective methods for producing high-quality metal parts, and the best choice depends on your specific needs and requirements. If you need parts with high precision and complexity, CNC turning machining is the way to go. On the other hand, if you require high uniformity and strength, metal powder metallurgy is the better option.
At Dongguan City Longsheng Hardware Technology Co., Ltd, we specialize in both CNC machining and metal powder metallurgy. Our team of experts can help you determine the best method for your project and produce high-quality metal parts that meet your exact specifications. Contact us today to discuss your manufacturing needs and how we can help you achieve your goals.
In summary, CNC machining and metal powder metallurgy are two popular methods for producing high-quality metal parts. CNC Milling machining Center is a process that uses computer-controlled machines to produce parts with high accuracy and precision, while metal powder metallurgy is a process that involves compacting metal powders and sintering them to create strong and durable parts with intricate geometries. The choice of method depends on your specific needs and requirements, and our team at {Your Company Name} can help you determine the best method for your project.