This article discusses common defects that can occur during the milling machining process of stainless steel, as well as ways to improve its machinability. Strategies to minimize defects include selecting appropriate milling parameters, choosing the right cutting tools, and using coolant during the milling process. The article also covers how to improve the machinability of stainless steel, including using high-quality cutting tools, optimizing milling parameters, choosing the right coolant, maintaining the machine properly, and considering alternative machining processes. By implementing these strategies, it is possible to produce high-quality finished products with minimal defects.
Milling Machining Defects in Stainless Steel
Stainless steel is a popular material used in various industries due to its unique properties. However, during the milling machining process, several defects can occur, affecting the quality of the finished product. Some of the common milling machining defects in stainless steel include:
1. Built-Up Edge (BUE)
BUE occurs when the material being machined sticks to the cutting tool, causing a buildup on the edge. This can result in a poor surface finish, reduced tool life, and increased cutting forces.

2. Chatter
Chatter is a vibration that occurs during the milling process, leading to uneven surface finish and reduced tool life. Chatter can be caused by various factors such as improper tool selection, incorrect cutting parameters, and poor machine rigidity.
3. Work Hardening
Work hardening occurs when the stainless steel material becomes harder and more brittle during the milling process. This can lead to increased cutting forces, reduced tool life, and poor surface finish.
4. Tool Wear
Tool wear is a common defect in milling machining and occurs when the cutting tool becomes dull or damaged. This can lead to poor surface finish, increased cutting forces, and reduced tool life.
5. Thermal Cracking
Thermal cracking occurs when the stainless steel material is exposed to high temperatures during the milling process. This can cause cracks in the material, reducing its strength and durability.
To avoid these defects, it is crucial to use proper cutting parameters, select the right cutting tools, and maintain the machine properly. Additionally, using coolant during the milling process can help reduce the risk of work hardening and thermal cracking.
Challenges in Machining Stainless Steel
Stainless steel is a material with unique physical and chemical properties that is widely used in various industries. However, during the milling machining process, several defects can occur, affecting the quality of the finished product. Milling machining is a high-precision cutting process that requires a deep understanding of the properties of the material being machined. Machining stainless steel is difficult mainly due to the following reasons:
1. High Hardness and Stickiness
Stainless steel has high hardness and stickiness. This means that during the milling machining process, friction and heat can occur, causing stainless steel particles to accumulate on the surface of the cutting tool, resulting in Built-Up Edge (BUE), and also leading to work hardening.
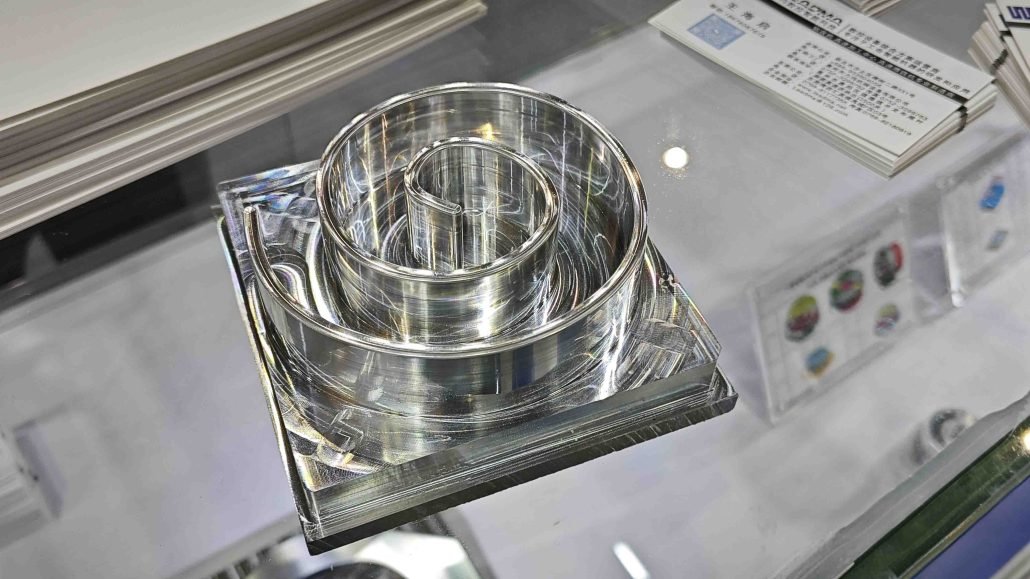
2. Thermal Cracking
During the milling machining process, stainless steel may be exposed to high temperatures, resulting in thermal cracking. This not only affects the quality of the finished product but also reduces the strength and durability of the stainless steel material.
3. High Cutting Forces
Due to its high hardness, stainless steel needs to withstand significant cutting forces during the milling process. If the cutting parameters are not appropriate or the tool selection is incorrect, it can easily lead to tool wear and impact the quality of the machining.
4. Chatter
Because of its high hardness, if the machine tool rigidity is insufficient or the cutting force direction is unreasonable, it can cause machine tool chatter, affecting the surface roughness and machining accuracy of the finished product.
Therefore, to obtain a high-quality finished product in the milling machining process of stainless steel, it is necessary to select appropriate cutting parameters, choose the right cutting tools, ensure the stability of the machine tool, and adopt timely cooling measures to reduce the risk of tool wear and work hardening.
Improving the Machinability of Stainless Steel
Stainless steel is a challenging material to machine due to its unique physical and chemical properties. However, there are several ways to improve its machinability, such as:
1. Use High-Quality Cutting Tools
Using high-quality cutting tools, such as those made from carbide or diamond, can significantly improve the machinability of stainless steel. These materials are more wear-resistant and can withstand the high cutting forces and temperatures associated with milling machining.
2. Optimize Cutting Parameters
Optimizing cutting parameters, such as cutting speed, feed rate, and depth of cut, can help reduce the risk of work hardening and thermal cracking. It is essential to find the right balance between cutting parameters to achieve the desired surface finish and tool life.

3. Choose the Right Coolant
Using the right coolant during the milling process can help reduce the risk of work hardening and thermal cracking. Coolants such as mineral oil or synthetic oil can be used to improve the machinability of stainless steel.
4. Maintain the Machine Properly
Regular maintenance of the milling machine can ensure that it operates at its optimal level. This includes cleaning the machine, lubricating the parts, and replacing worn-out components.
5. Consider Alternative Machining Processes
If milling machining is not suitable for the specific stainless steel material, alternative machining processes such as turning or grinding can be considered. These processes may be more suitable for certain types of stainless steel and can improve the machinability of the material.
By implementing these strategies, it is possible to improve the machinability of stainless steel and produce high-quality finished products with minimal defects.
Stainless Steel CNC Milling Machining Services
If you are looking for high-quality stainless steel CNC milling machining services, you’ve come to the right place. Our team of experienced machinists is skilled in creating precise, custom parts for a variety of industries, including aerospace, automotive, medical, and more.
We use state-of-the-art CNC milling machines to ensure accuracy and efficiency in every project. Our machines are capable of handling a wide range of materials, including stainless steel, aluminum, titanium, and plastics.
Our team works closely with each client to understand their specific needs and requirements. We offer a range of machining services, including milling, turning, drilling, and tapping. We can also provide finishing services such as anodizing, powder coating, and painting.
At every stage of the process, we maintain strict quality control measures to ensure that each part meets our high standards. Our team is committed to providing exceptional service and delivering projects on time and within budget.
Contact us today to learn more about our stainless steel CNC milling machining services and how we can help with your next project.
FAQ
During the stainless steel milling machining process, common defects include Built-Up Edge (BUE), chatter, work hardening, tool wear, and thermal cracking. These defects can affect the quality and surface finish of the final product.
To avoid defects in stainless steel milling machining, it is crucial to select appropriate milling parameters, choose the right cutting tools, and maintain the machine properly. In addition, using coolant during the milling process can help reduce the risk of work hardening and thermal cracking.
To improve the machinability of stainless steel, the following methods can be adopted:
Using high-quality cutting tools, such as those made from carbide or diamond.
Optimizing milling parameters, such as cutting speed, feed rate, and depth of cut, to reduce the risk of work hardening and thermal cracking.
Choosing the right coolant to help reduce the risk of work hardening and thermal cracking.
Regularly maintaining the milling machine, including cleaning the machine, lubricating the parts, and replacing worn-out components.
Considering alternative machining processes, such as turning or grinding, which may be more suitable for certain types of stainless steel.
By implementing these strategies, it is possible to improve the machinability of stainless steel and produce high-quality finished products with minimal defects.
The stainless steel CNC milling machining service includes selecting appropriate milling parameters, cutting tools, and machine maintenance, as well as using coolant to reduce the risk of work hardening and thermal cracking. To improve the machinability of stainless steel, high-quality cutting tools, optimized milling parameters, appropriate coolant selection, regular machine maintenance, and consideration of alternative machining processes are necessary. By implementing these strategies, it is possible to improve the machinability of stainless steel, produce high-quality finished products, and minimize defects.
In summary, the milling machining process of stainless steel can lead to several defects that can affect the quality and surface finish of the final product. However, by selecting appropriate milling parameters, choosing the right cutting tools, and using coolant during the milling process, it is possible to reduce the risk of defects. Additionally, improving the machinability of stainless steel requires using high-quality cutting tools, optimizing milling parameters, choosing the right coolant, maintaining the machine properly, and considering alternative machining processes. By implementing these strategies, it is possible to produce high-quality finished products with minimal defects.