Injection molding is one of the most popular manufacturing processes in the world. It is used to manufacture various products from toys to medical equipment. This process involves injecting molten material into the mold cavity, where it cools and hardens to form the desired object. The mold cavity is the most important part of the mold, as it determines the final shape and size of the object. However, it is only a part of the mold; The other part is the core.
Are you looking to produce plastic precision parts in large quantities? If yes, then injection molding is the perfect option for you. But before you get started with injection molding, it’s essential to understand the core and cavity in the process.
In this article, we’ll provide a comprehensive guide on what core and cavity are, how they work, and why they’re important in injection molding. From the basics to the advanced concepts, we’ll cover everything you need to know.
So, let’s dive in!
Understanding the Injection Molding Process
Before delving into the details of the core and cavity components, it is important to have a brief understanding of the injection molding process. The injection molding process involves melting plastic particles or resins and injecting the molten material into the mold cavity to form plastic components. Then let the plastic cool and harden, and then open the mold to release the finished product.
At a high level, the injection molding process consists of four main stages: clamping, injection, cooling, and ejection. The clamping stage involves closing the mold, which is made up of the core and cavity components. The injection stage involves injecting molten material into the mold cavity, which is where the plastic part is actually formed. The cooling stage involves allowing the plastic to cool and solidify, which is critical for producing high-quality parts. Finally, the ejection stage involves opening the mold and removing the finished part.
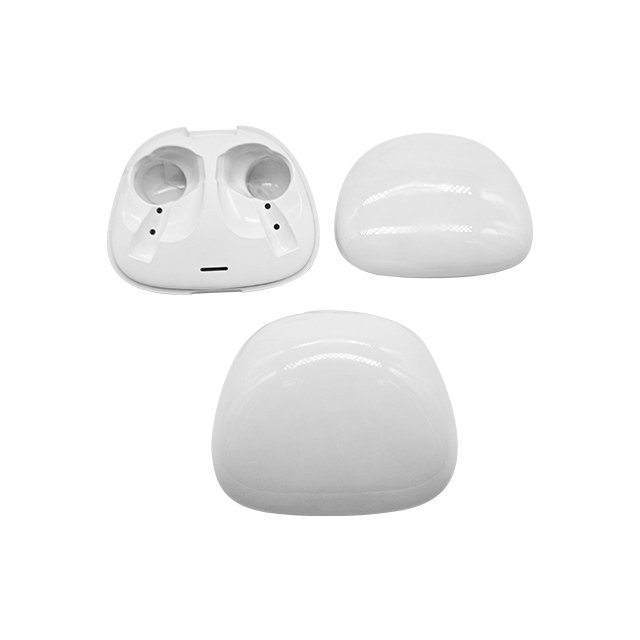
What is the Core?
The core is a part of an injection mold that creates the internal features of the molded object. It is usually located inside the cavity and can move or rotate to form different shapes. The core is usually made of a harder material than the cavity, which is the part of the mold that moves during the injection process.
What is the Cavity?
The cavity is the part of the injection mold that creates the external shape of the object. It is usually the stationary part of the mold and is the part that is filled with molten material during the injection process. The cavity is designed to be the exact size and shape of the final object and is often highly polished to ensure a smooth finish.
Conclusion
Core and cavity are the two primary components of an injection mold. The core is a solid steel or aluminum insert that forms the internal shape of the plastic part. The cavity, on the other hand, is the outer part of the mold that creates the external shape of the part.
The molten plastic is injected into the cavity, which then solidifies around the core to form the final product. It’s the combination of these two parts that makes it possible to create complex 3D shapes and intricate designs using injection molding.
What are Core and Cavity Components?
In the injection molding process, the core and cavity components are the two parts that make up the mold. The core component forms the internal features of the component, and the cavity component forms the external features of the component. During the injection molding process, the core and cavity components are combined to form the mold cavity, which is the space formed by the plastic components.
The core and cavity components can be made from a variety of materials, including steel, aluminum, and copper. The choice of material depends on the requirements of the part being produced and the number of cycles the mold is expected to run. Steel is the most common material used for core and cavity components, as it is durable and can withstand high temperatures and pressures.
Importance of Core and Cavity in Injection Molding
The core and cavity components play a crucial role in the injection molding process, as they determine the final shape and size of plastic components. Any errors or inconsistencies in the core and cavity components can lead to defects in the final component, such as warping, dents, or flashing. Therefore, it is necessary to design and manufacture core and cavity components with the highest precision to ensure that plastic components meet the required specifications and quality standards.
In addition to accuracy, the design of the core and cavity components has a significant impact on the cycle time and cost of injection molding. The more complex the part design, the more intricate the core and cavity components need to be, which can increase the manufacturing time and costs. Therefore, it’s important to balance the part design complexity with the manufacturing feasibility, to optimize the injection molding process.
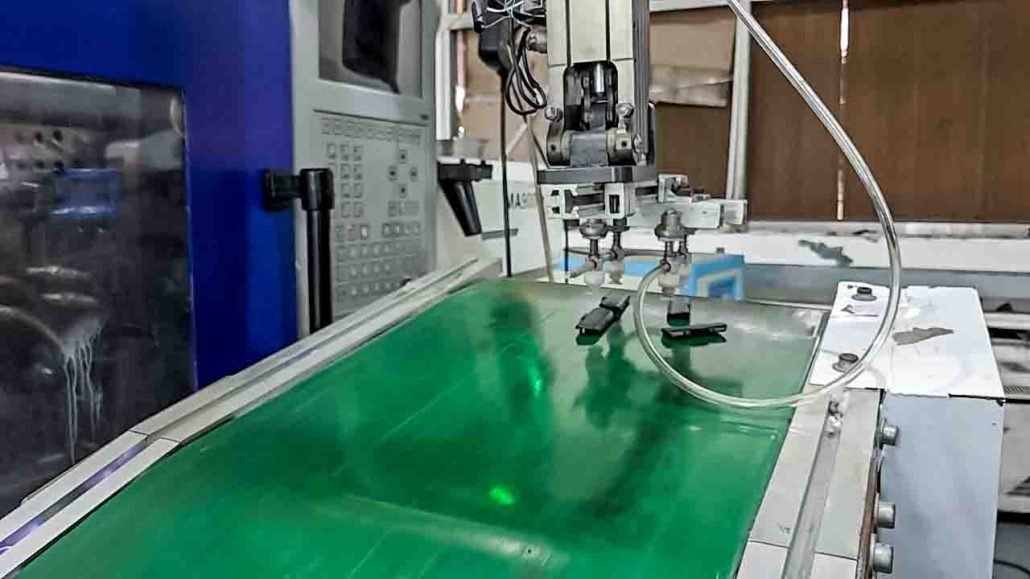
How are Core and Cavity Created?
The core and cavity are created using several methods. The most common method is to use metal processing, usually stainless steel or aluminum. This process involves using a CNC machine tool to cut the metal into the desired shape and size. Another method is to use additive manufacturing techniques, such as 3D printing, to create cores and cavities. This method is becoming increasingly popular due to its flexibility and cost-effectiveness.
How Do Core and Cavity Work?
The core and cavity work together to shape the molten plastic into the desired part. Here’s how it works:
- The mold is closed, and the molten plastic is injected into the cavity under high pressure.
- As the plastic enters the cavity, it flows around the core, taking the shape of the internal features of the part.
- Once the plastic has filled the cavity, it’s left to cool and solidify.
- The mold is opened, and the part is ejected from the cavity.
The process is repeated for each part, producing identical copies every time. The accuracy and precision of the core and cavity are crucial to ensure the parts are consistent in size, shape, and quality.
The core and cavity are essential components of the injection molding process. Without them, it wouldn’t be possible to create the complex and intricate designs that are required for many products.
The accuracy and precision of the core and cavity are crucial to ensuring that the parts produced are consistent in size, shape, and quality. This helps to minimize wastage and reduce the overall cost of production.
Furthermore, the use of high-quality materials in the construction of the core and cavity ensures that they last longer and produce consistent results over an extended period. This ultimately translates to cost-savings for the manufacturer.
Conclusion
In this article, we discussed what cores and cavities are, how they work, and why they are important in injection molding. Understanding the core and cavity in the injection molding process is essential as it enables manufacturers to produce high-quality plastic parts in large quantities.
If you are considering using injection molding for your manufacturing needs, it is important to communicate with a reputable manufacturer who understands the importance of cores and cavities in the process. With the right manufacturer and the right mold, you can produce high-quality parts that meet your specifications.