This article provides an overview of Electrical Discharge Machining (EDM), a non-traditional machining process that uses electrical discharges to remove material from a workpiece. It describes the process of EDM, its advantages and disadvantages, and the types of materials that can be machined using this process.
What is Electrical Discharge Machining (EDM)
Electrical Discharge Machining (EDM) is a non-traditional machining process that uses electrical discharges to remove material from a workpiece. It is also known as spark machining, spark eroding, die sinking, wire burning or wire erosion.
In EDM, an electric spark is used to erode the material from the workpiece. The workpiece is connected to the negative terminal of a power supply and an electrode is connected to the positive terminal. The electrode is usually made of graphite or copper and is designed to have the desired shape.
When the electrode is brought close to the workpiece, a spark jumps across the gap and heats the material to a temperature of about 8000°C. This causes the material to melt and vaporize, forming a small crater in the workpiece. The electrode is then moved slightly and the process is repeated.
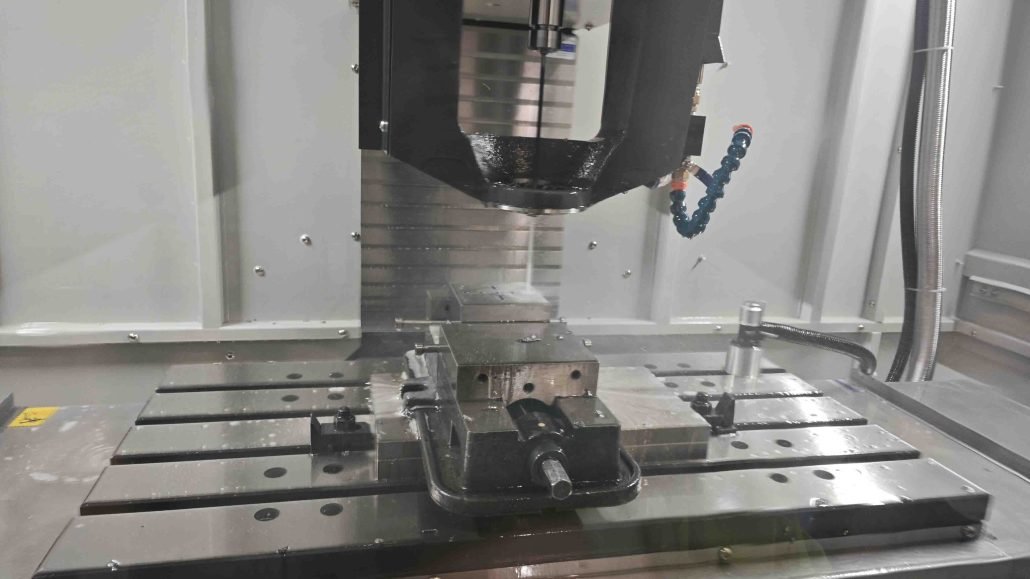
EDM is commonly used in the manufacturing industry to produce complex shapes and contours that are difficult or impossible to achieve with traditional machining processes. It is often used to make dies, molds, and other tools that are used in the production of other CNC parts.
There are two main types of EDM: wire EDM and sinker EDM. In wire EDM, a thin wire is used as the electrode and is fed through the workpiece, cutting it into the desired shape. In sinker EDM, the electrode is shaped like the desired cavity and is used to erode the material from the workpiece.
EDM has several advantages over traditional machining processes. It can be used to machine hard and brittle materials that are difficult to machine with conventional methods. It can also be used to machine very thin and delicate parts without causing damage. However, it is a slow process and can be expensive, making it unsuitable for high-volume production.
Overall, EDM is a useful process for producing complex shapes and contours in hard and brittle materials that are difficult to machine with traditional methods.
What are 3 types of EDM?
Electric Discharge Machining (EDM) is a technique used to shape and cut materials using electrical sparks. There are three main types of EDM, each with its own advantages and disadvantages depending on the material and the desired outcome of the machining process.
- Wire EDM – Uses a thin wire to cut through the material with the help of electric sparks. This type of EDM is often used for cutting complex shapes and thin materials. It is also useful for cutting materials that are difficult to machine using traditional methods.
- Sinker EDM – Uses a shaped electrode to create a cavity in the material. This type of EDM is often used for creating molds and dies. It is also useful for creating complex shapes and features that are difficult to machine using traditional methods.
- Hole Drilling EDM – Creates holes in the material using long electrodes. This type of EDM is often used for creating small, deep holes in hard materials. It is also useful for creating holes with complex shapes and features.
Overall, EDM is a versatile technique that can be used to cut and shape a wide range of materials. Each type of EDM has its own unique advantages and disadvantages, making it important to choose the right type of EDM for your specific machining needs.

Electrical Discharge Machining (EDM) Process
The EDM process works by creating an electrical discharge between the tool and the workpiece. The electrical discharge creates a spark that melts and vaporizes the material from the workpiece. The melted material is then flushed away by a dielectric fluid, which also cools the workpiece and tool.
There are two main types of EDM processes: wire EDM and sinker EDM. Wire EDM uses a thin wire as the tool, while sinker EDM uses an electrode in the shape of the desired cavity. Both processes are used in a variety of industries, including aerospace, automotive, medical, and electronics.
EDM has several advantages over traditional machining processes. It can machine hard, brittle materials that are difficult to machine by other methods. It can also produce complex shapes and features with high accuracy and precision. However, EDM is a slow process and is typically used for small parts or low-volume production.
In conclusion, EDM is a non-traditional machining process that uses electrical discharges to remove material from a workpiece. It is commonly used to machine hard, brittle materials and can produce complex shapes with high accuracy and precision.
Electrical Discharge Machining (EDM) Advantages
Electrical Discharge Machining (EDM) is a non-traditional machining process that uses an electrical discharge to erode metal. This process has gained popularity in recent years due to its several advantages over traditional machining processes.
One of the most significant advantages of EDM is its high precision. It can create intricate and complex shapes with high accuracy and precision, achieving tolerances of up to +/- 0.005mm. This precision makes it a popular choice for manufacturing components that require high accuracy.
Another advantage of EDM is that it does not require any physical contact between the tool and the workpiece, making it a “no contact” machining process. This means that there is no tool wear or deformation, resulting in longer tool life. The lack of physical contact also minimizes the risk of damage to the workpiece, making it an ideal process for machining delicate and fragile components.
EDM is also capable of machining hard and tough materials that are difficult to machine using traditional methods. Materials such as tungsten carbide, titanium, and hardened steel can be machined with ease using EDM. This ability to machine hard materials makes EDM a popular choice in the aerospace and medical industries, where components made from these materials are commonly used.
Another advantage of EDM is that it does not produce any heat-affected zones, which can cause thermal damage to the workpiece. This makes it ideal for machining delicate and heat-sensitive materials. Additionally, EDM can be used to machine a wide range of materials and shapes, including thin and delicate parts, complex geometries, and small features.
In conclusion, EDM offers several advantages over traditional machining processes, making it a popular choice for precision machining applications. Its ability to machine hard materials, create intricate and complex shapes with high accuracy and precision, and lack of thermal damage make it a versatile and reliable process for a wide range of industries.

Electrical Discharge Machining (EDM) Applications
Electrical Discharge Machining (EDM) is a non-traditional machining process that is widely used in the manufacturing industry. EDM is used to create complex shapes, holes, and contours in hard metals that are difficult to machine using traditional machining processes. Here are some of the most common applications of EDM:
- Aerospace Industry: EDM is extensively used in the aerospace industry to create complex shapes and contours in turbine blades, engine components, and other critical parts. EDM can produce high-precision parts with tight tolerances that are required in aerospace applications.
- Medical Industry: EDM is used in the medical industry to create molds for medical devices and instruments. EDM is also used to machine parts for medical implants, such as artificial joints, dental implants, and pacemaker components.
- Mold and Die Making: EDM is widely used in mold and die making industries to create complex shapes and contours in tooling. EDM can produce high-precision molds and dies that are used to manufacture plastic injection molded components, die-cast parts, and other precision components.
- Automotive Industry: EDM is used in the automotive industry to create molds for plastic parts, such as dashboards, door panels, and other interior components. EDM can also be used to create complex shapes and contours in engine components, transmission parts, and other critical components.
- Tool and Die Making: EDM is extensively used in tool and die making industries to create high-precision cutting tools, such as drills, reamers, and taps. EDM can also be used to create complex shapes and contours in dies for stamping and forming sheet metal parts.
In conclusion, EDM is a versatile machining process that is widely used in various industries to create complex shapes and contours in hard metals. EDM can produce high-precision parts with tight tolerances, which makes it an ideal choice for applications that require high accuracy and precision.
Difference between CNC and EDM
CNC and EDM are two different processes used in manufacturing. CNC stands for Computer Numerical Control while EDM stands for Electrical Discharge Machining. Here are the differences between these two processes:
CNC
CNC is a subtractive manufacturing process that uses computerized machines to remove material from a workpiece. In CNC, a computer program is used to control the movement of cutting tools to shape the workpiece. CNC machines can be used to create complex shapes with high precision and accuracy. CNC machines are commonly used in industries such as aerospace, automotive, and medical.
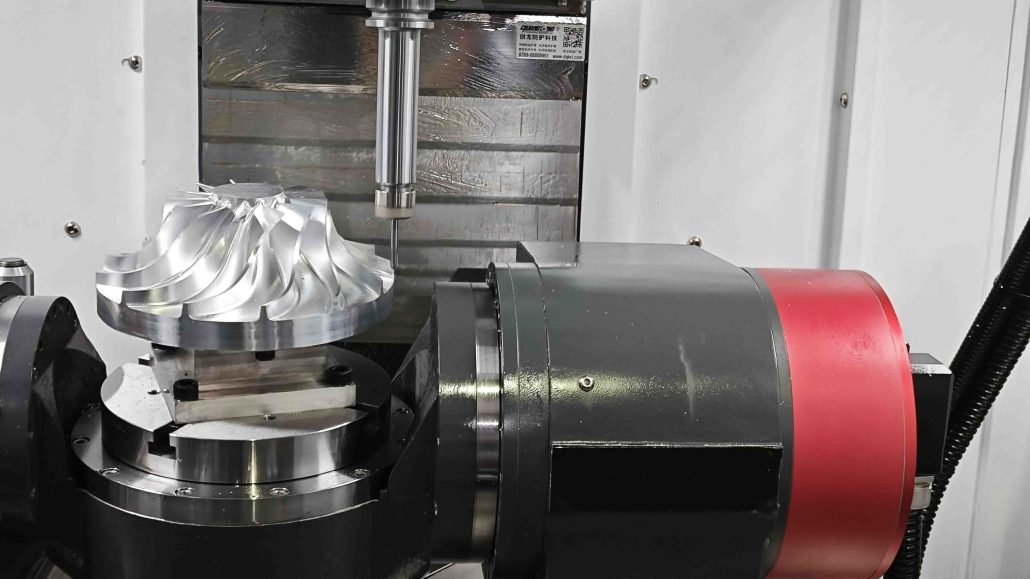
EDM
EDM is a non-traditional manufacturing process that uses electrical discharge to remove material from a workpiece. In EDM, an electrically charged wire or electrode is used to create a spark that erodes the material from the workpiece. EDM is commonly used in the production of complex parts and components that are difficult to machine using traditional methods. EDM is used in industries such as aerospace, medical, and die and mold making.
In conclusion, both CNC and EDM are important manufacturing processes used in different industries. CNC is a subtractive manufacturing process that uses computerized machines to remove material from a workpiece while EDM is a non-traditional manufacturing process that uses electrical discharge to remove material from a workpiece.
Difference between Wire EDM and EDM
EDM stands for Electrical Discharge Machining, and it is an advanced machining method that uses electrical sparks to remove material from the workpiece. Wire EDM, on the other hand, is a subtype of EDM that uses a thin wire to cut the workpiece, allowing for precise and intricate cuts.
The primary difference between EDM and Wire EDM is the method used to cut the workpiece. In EDM, an electrode and workpiece are submerged in dielectric fluid, and electrical sparks are used to erode the workpiece. In Wire EDM, a thin wire is used to cut the workpiece while submerged in the dielectric fluid.
Wire EDM is preferred over EDM for intricate and precise cuts, as it allows for tighter tolerances and more complex shapes. However, EDM is ideal for rough cuts and larger pieces due to its faster cutting speed.
In summary, Wire EDM is a subtype of EDM that uses a thin wire to cut the workpiece, while EDM uses electrical sparks to erode the material. Wire EDM is preferred for precise and intricate cuts, while EDM is ideal for rough cuts and larger pieces.
FAQ
EDM can be used to machine hard and brittle materials, such as tungsten carbide, titanium, and ceramics, that are difficult to machine with conventional methods.
EDM can be used to machine very thin and delicate parts without causing damage. It can also be used to machine hard and brittle materials that are difficult to machine with conventional methods.
The electrode is usually made of graphite or copper and is designed to have the desired shape.