CNC machining is an innovative and efficient method of manufacturing that has revolutionized the manufacturing industry. However, for manufacturers to maximize productivity and profitability, it is essential to understand the normal scrap rate for CNC machining.
Scrap rate refers to the percentage of cnc machining parts produced that do not meet the quality standards of the manufacturer and must be scrapped or reworked. The scrap rate can vary depending on several factors, such as the complexity of the part, the quality of the raw material, the skill level of the operator, and the precision of the machine.
It is important to note that while a zero scrap rate is ideal, it is unrealistic to achieve. However, manufacturers can aim to achieve a normal scrap rate that is within an acceptable range. The normal scrap rate for CNC machining is typically between 2% and 5%.
To minimize scrap rate, manufacturers must have a well-designed manufacturing process that includes proper tool selection, programming, and quality control measures. Proper tool selection, for instance, ensures that the tools used in the manufacturing process are appropriate for the specific job, reducing the chances of defects.

Programming is also essential in minimizing scrap rate. The programming process involves creating a set of instructions that the CNC machine follows to manufacture a specific part. Proper programming ensures that the machine produces precision machining parts that meet the required quality standards.
Quality control measures are also essential in minimizing scrap rate. These measures involve inspecting parts during the manufacturing process to ensure that they meet the required quality standards. Manufacturers can also use statistical process control (SPC) techniques to monitor and control the production process. SPC involves collecting and analyzing data to identify trends and patterns that can help identify and eliminate sources of variation in the manufacturing process.
Regular maintenance of the CNC machine and proper training of operators can also help reduce scrap rate. Regular maintenance ensures that the machine is functioning correctly, reducing the chances of defects. Proper training of operators ensures that they have the skills required to operate the machine effectively, reducing the chances of operator errors that can lead to defects.
How do you calculate cnc machining parts scrap rate?
To calculate the scrap rate for CNC machining parts, you can follow the same formula as for any other manufacturing process. First, you need to determine the total number of parts produced. Then, you need to count the number of parts that do not meet the quality standards of the manufacturer and must be scrapped or reworked. Once you have these two numbers, you can calculate the scrap rate by dividing the number of defective parts by the total number of parts produced and expressing the result as a percentage.
It is important to note that the scrap rate can vary depending on several factors, such as the complexity of the part, the quality of the raw material, the skill level of the operator, and the precision of the machine. The normal scrap rate for precision CNC machining is typically between 2% and 5%.
By calculating the scrap rate, manufacturers can identify the areas of the manufacturing process that need improvement to reduce scrap rate and increase productivity. For example, if the scrap rate is high, it may indicate that the manufacturing process requires better quality control measures or operator training.
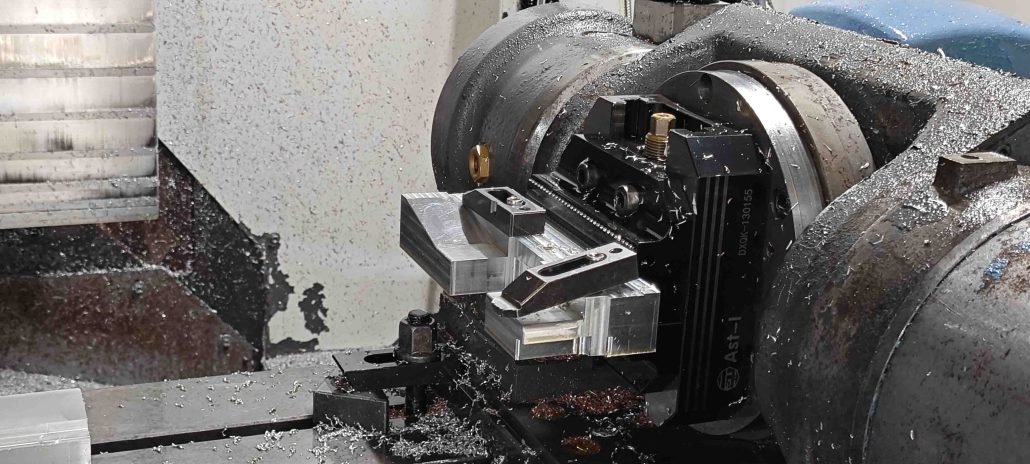
In conclusion, calculating the scrap rate for CNC milling machining parts is a straightforward process that can provide valuable insights into the manufacturing process. By understanding and reducing scrap rate, manufacturers can increase productivity, reduce costs, and remain competitive in the modern manufacturing industry.
To further illustrate how to calculate scrap rate for CNC machining parts, let’s consider an example. If a manufacturer produces 500 CNC machining parts and 20 of them are defective, the scrap rate would be (20/500) x 100% = 4%.
In conclusion, the normal scrap rate for CNC machining can vary depending on several factors, but it is typically between 2% and 5%. By implementing proper manufacturing processes, regular maintenance, and quality control measures, manufacturers can reduce scrap rate and increase productivity and profitability. Understanding and achieving a normal scrap rate is essential for manufacturers to remain competitive in the modern manufacturing industry.