Injection moulding is the widely used manufacturing process for producing plastic parts in the industry. It involves the use of materials like thermoplastics, thermosetting polymers, and elastomers to create components and other plastic parts. The process is widely applicable in numerous industries, such as automotive, consumer goods, and medical products, among others. This article will break down the process of injection moulding and its use in detail.
The Process of Injection Moulding
The process of injection moulding is suitable for producing a wide range of plastic products, from small parts to large products. The process is highly automated, making it efficient and relatively low-cost. There are two main types of injection moulding: cold-runner moulding and hot-runner moulding. Cold-runner moulding is a cost-effective option that’s suitable for producing simple parts, whereas hot-runner moulding is more expensive and is used to produce parts with complex geometry.

The injection moulding process involves six steps, which are:
Clamping: The first step is in the preparation stage, where two halves of the mould tools are clamped together.
Injection: After the clamping stage, the injection process begins. A molten plastic is heated up and is then injected into the mould cavity.
Dwelling: This is where the molten plastic is permitted to rest or dwell for the cavity capable of filling.
Cooling: Cooling is the process whereby the molten plastic cools down to form a solid shape. The cooling time depends on the thickness and material of the mould.
Ejection: After the previous four steps, the newly created part is then ejected from the mould tool.
Finishing: Lastly, the final product undergoes a surface finishing process, which aims to prepare the product for use.
Injection moulding has a myriad of applications and uses in various industries. It is prevalent in automotive manufacturing for creating parts of the car such as dashboard components, wheel covers, and more. Other industries that heavily utilize injection moulding include healthcare and medical products manufacturing. In the medical sector, injection moulding produces a wide array of products, including IV components, vials, and drug delivery systems.
How Injection Moulding is Used
Injection moulding is used in a wide range of industries, from automotive and aerospace to medical and consumer products. In the automotive industry, injection moulding is used to make a variety of parts, including bumpers, grilles, and interior trim. In the medical industry, injection moulding is used to make a variety of devices, including syringes, catheters, and medical implants. In the consumer products industry, injection moulding is used to make everything from toys and kitchen utensils to mobile phone cases and computer keyboards.
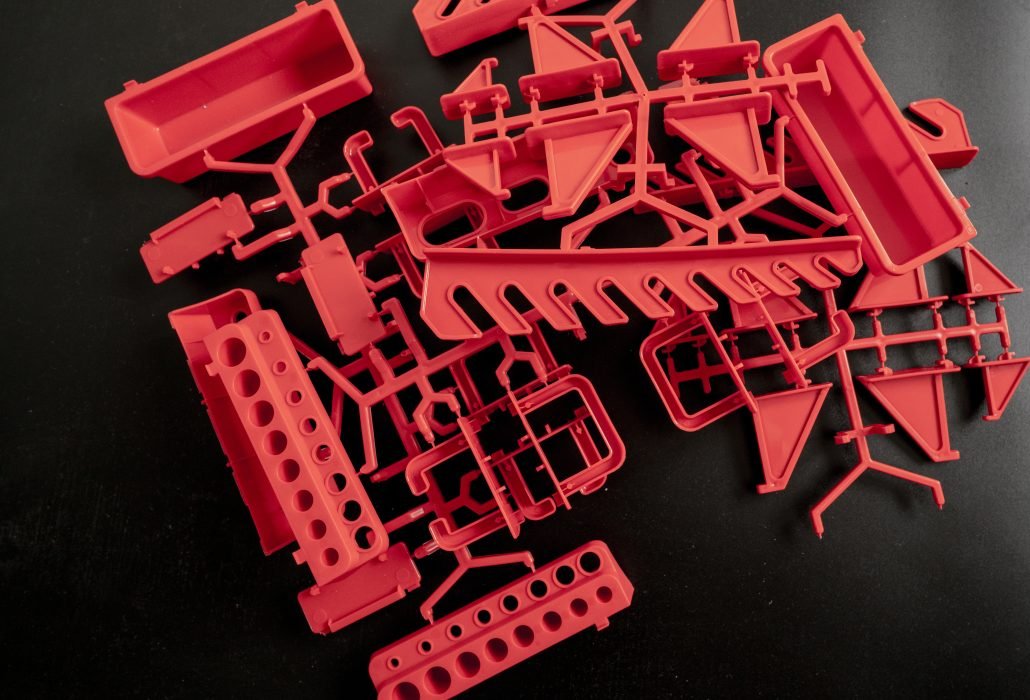
Applications of Injection Moulding
Injection moulding has a number of advantages over other manufacturing processes. It is highly versatile, allowing for a wide range of products to be made using the same basic process. It is also highly efficient, as it allows for large volumes of products to be made quickly and easily. In addition, injection moulding produces very little waste, as any excess material can be recycled and reused. This makes it an environmentally-friendly option for manufacturing.
Injection moulding is used in many industries, including:
Medical: Injection moulding is used to produce medical devices such as syringes, IV tubing, and connectors.
Automotive: Injection moulding is used to produce various parts used in vehicles, including dashboards, bumpers, and interior fittings.
Consumer Goods: Injection moulding is used to produce products such as toys, kitchen utensils, and electronic components.
Benefits of Injection Moulding
Injection moulding offers many benefits, including:
High production rates: Injection moulding is a highly automated process that allows for high production rates, making it an efficient and cost-effective manufacturing process.
Lower labour costs: Injection moulding requires minimal labour, reducing costs and increasing efficiency.
High accuracy and precision: Injection moulding ensures consistent and accurate product output, reducing waste and improving product quality.
Apart from producing recurring products, injection moulding has shown great potential in pushing innovation in numerous fields. It has permitted designers and engineers to create complex designs and structures that would have been impractical or impossible to produce before injection moulding technology.
In conclusion, injection moulding is a highly versatile manufacturing process that provides numerous benefits. Its ability to produce multi-material and multi-color parts allows for flexibility in designs and structures, while its speed and efficiency make it a popular choice for industries worldwide. If you’re looking for a manufacturing process that provides high-quality products, then injection moulding is the perfect solution.