In the field of modern machining, CNC machine tools have become a very important process. It uses computer programs to control the machining process, and has more efficient, more accurate, more stable machining capacity. For those who need to manufacture parts and products with high repeatability, high complexity and high precision requirements, different types of CNC machining processes can produce complex and precise products to meet a variety of applications and user needs.
If you are considering CNC machining but are not sure which type of machining process to choose, then this article is just for you. In this article, we will detail 10 different types of CNC machining processes and their characteristics. We will cover a variety of machining processes including milling, turning, drilling and cutting. We’ll also cover the pros and cons of each process to help you better understand the scope of each process.
Cnc machining process introduction
CNC machining is based on CAD/CAM system, that is, computer aided design and computer aided manufacturing system. The CAD/CAM system can convert the 3D model of the product into the machine tool control program, which is convenient for the CNC machine tool to carry out automatic machining. Through CAD/CAM system, the whole process of digital and network management of product design and manufacturing can be realized.
It can manufacture parts, prototypes, handplates, fixtures and various precision mechanical parts. Compared with traditional machining, CNC machining has the advantage that it can be applied to the production of different parts through a simple modification procedure, so as to achieve high production efficiency and flexibility.
Different types of cnc machining processes
The following are ten different types of cnc machining processes commonly used in manufacturing:
Cnc milling
The motion of the workpiece in CNC milling is controlled by the numerical control system, which requires the CAD design of the parts to be processed first, and then convert the design drawings into numerical control programming language, and finally enter the written program into the numerical control system, and then by the numerical control system to the motion of the tool, cutting speed, feed speed and other parameters to control the precision machining of parts.

CNC milling offers higher precision and efficiency than traditional hand cutting and engraving methods. Because it uses a computer program to control the tool path, very precise cutting and engraving can be guaranteed. In addition, its degree of automation can also greatly improve work efficiency.
CNC milling can be used to process a variety of materials, including metals, plastics, wood and composite materials. The technique allows for a variety of complex shapes, such as holes, bumps, grooves and curves.
Below are the advantages and disadvantages of cnc milling.
Advantage | Disadvantage |
---|---|
Efficient machining, reducing machining time and costs | The machine tool structure is complex, and the machining of special shaped parts is limited |
Diversified machining methods, suitable for multiple materials | High equipment maintenance costs |
High accuracy, capable of handling complex shapes and contours | Small batch machining is expensive |
Automatic control, high stability in the machining process | |
Manufacturing multiple identical parts ensures accuracy and consistency. |
Cnc turning
CNC turning is a machining technique in which a workpiece is rotated and cut by a cutting tool. CNC lathes use computer programs to control the fineness and position of cutting tools and can precisely control the speed, strength, depth and direction of each machining operation, thus greatly improving production efficiency and product quality.
Through CNC turning technology, a wide variety of parts and components can be produced, such as shafts, gears, threads, planes, cams and so on. These components can be used to make a variety of different types of machines and equipment
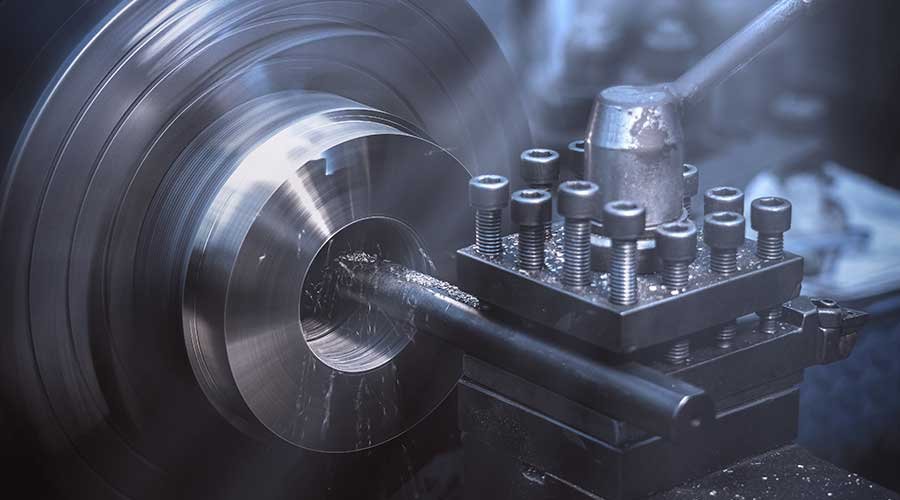
Compared to CNC milling, CNC turning is suitable for dealing with smaller materials and curved shapes, while CNC milling is suitable for dealing with large workpieces and projects requiring high precision cuts on a flat surface
The advantages and disadvantages are summarized as follows
Advantage | Disadvantage |
---|---|
High production efficiency | High technical content in operation |
Suitable for machining workpieces of various shapes and materials | Complex programming |
machining multiple parts simultaneously | High equipment purchase and maintenance costs |
Capable of meeting high-precision machining requirements | |
Improved surface roughness |
5-axis machining
5-axis machining refers to a high-efficiency and high-precision machining method by simultaneously controlling 5 axes on a machine tool. Among them, three axes are straight axes and two axes are rotation axes. The linear axis is responsible for X, Y, Z direction movement, while the rotary axis controls the spindle rotation of the machine tool and the rotation of the workpiece. By coordinating and controlling the movement of these five axes, the machine tool can be processed at multiple angles to form more complex shapes.
Compared to other machining techniques, 5-axis machining is mainly used to create parts with complex geometric shapes. These parts are often needed in the aviation and medical equipment manufacturing industry because they require high precision and high quality requirements.
The following is a summary of its advantages and disadvantages.
Advantage | Disadvantage |
---|---|
High machining accuracy | Long machining time |
Wide machining interface range | High equipment costs |
Has good repeatability | Limitation of measurement range |
Strong machining ability for non-standard parts | |
High machining efficiency, achieving the machining of porous and multi-layer materials |
Turn-milling compound
Turning milling complex machining is a kind of machining which combines two kinds of machining methods: lathe and milling machine. By turning and milling at the same time, multi-sided machining in one center can be achieved. For example, boring, tapping, CNC contour milling, thread machining, interface machining, etc., for aerospace parts machining , turn-milling composite machining can realize the machining of complex surface parts
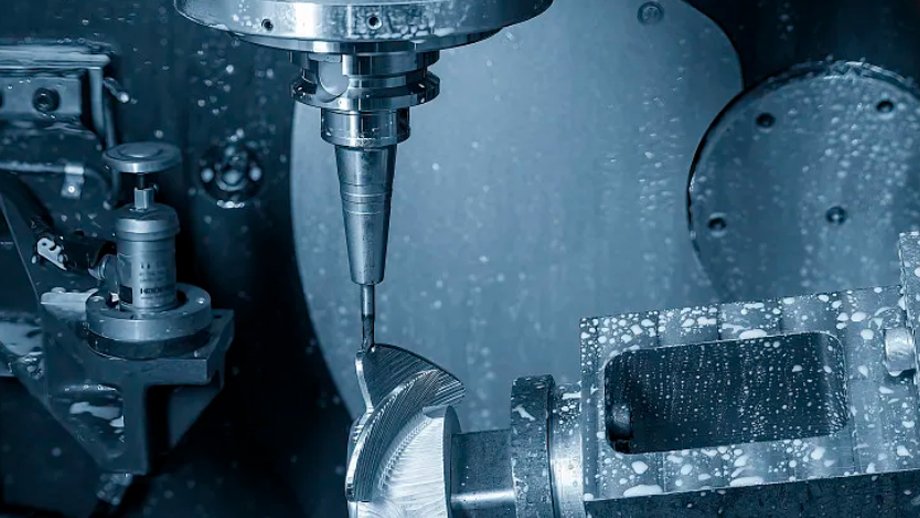
Compared with the traditional production mode, the compound machining of turning milling has obvious advantages. Compared with a single machining equipment, turn-milling complex machining equipment has more advantages in machining time, easy operation, precision, productivity and other aspects. In addition, turn-milling complex machining equipment occupies a small area, can replace a number of traditional machine tools, thus improving plant productivity and efficiency.
Learn more about the advantages and disadvantages of turning and milling composite.
Advantage | Disadvantage |
---|---|
Reduce errors between processes and clamping errors | The machining size is limited by the equipment size |
Capable of machining complex surfaces | Require highly skilled operators |
Low production cost and wide application range |
Cnc cutting
Cnc cutting using computer control system control cutting equipment, can achieve a variety of complex shape cutting. During the cutting process, the tool path can be controlled according to the desired shape, thus achieving accurate cutting. Cnc cutting can also automatically control the cutting speed and pressure, making the cutting work more stable and accurate.
Cnc cutting equipment usually uses high energy density laser, plasma, or water flow to achieve cutting. These devices can cut a variety of materials, including metal, plastic, glass, stone and more. Cnc cutting has the advantages of high speed and precision, can complete a large number of cutting work in a very short time, while ensuring high quality cutting effect.
Cnc cutting technology is usually used to make auto parts, billboards, kitchenware, furniture, tools, building components and so on.
Cnc cutting machining technology specific advantages and disadvantages are as follows
Advantage | Disadvantage |
---|---|
Capable of achieving various cutting forms, such as planar cutting, 3D cutting, etc | Need precise CAD drawings |
Ensure a balance between production speed and accuracy | Only supports cutting of specific file formats |
Short cutting time can reduce waste and save costs | Limited to material thickness |
High degree of automation |
Cnc drilling and milling
CNC drilling and milling machines look similar to ordinary drilling and milling machines on the outside, but have a more complex control system inside. It uses computer control technology, the electronic computer program input into the control system, and then through the electronic control system to control the machine tool machining .
It can complete a variety of complex cutting tasks, such as drilling, milling, hole machining, boring, tapping and so on. Not only can be used in steel, copper, aluminum, plastic and other materials machining , but also can be used in composite materials, aerospace, automotive, mold and other fields of machining .
If you need to manufacture small or deep hole parts as opposed to cnc milling, CNC drilling and milling is the best choice
The following are the advantages and disadvantages of cnc drilling and milling
Advantage | Disadvantage |
---|---|
Can write programs according to different machining needs | The learning curve is steep |
Capable of rapid tool change and positioning | There are compatibility issues with control software |
Highly precise positioning and machining capabilities | |
Implement machining of various shapes and sizes according to program settings | |
Increase process production and reduce waste |
Cnc grinding
CNC grinding is a kind of cutting machining method, which uses the grinding head, grinding wheel and other tools on the equipment to cut the workpiece. Compared with traditional manual grinding, CNC grinding has the advantages of high numerical control precision, fast speed and good repeatability. By presetting machining path and parameters in computer program, CNC grinding can realize precise machining of workpiece and mass production.
Compared with traditional machining methods, CNC grinding can greatly improve machining accuracy and quality, and reduce the influence of human factors and errors. Because CNC grinding can realize automatic production, also reduce labor costs.
See the pros and cons table below for more cnc grinding information
Advantage | Disadvantage |
---|---|
Can quickly complete large-scale grinding tasks | Some complex shapes are difficult to machine |
Achieving high-quality surface finishing | Difficulty in controlling surface temperature |
Reduce the generation of waste and reduce its impact on the environment | The cutting tools will wear out and require regular inspection and replacement |
Flexible design is allowed | |
Suitable for grinding workpieces of different shapes and sizes |
Wire cutting
Wire cutting is carried out by a special electrolytic machining. This method involves conducting an electrolyte along the surface of the material being cut and sending an electric arc through the electrode to finely cut the material into the desired shape. This method is particularly suitable for producing large quantities of complex parts and small tools.
Compared with traditional machining methods, wireline cutting has higher precision and less cutting error. The technique allows workers to cut quickly while ensuring a perfect match and avoiding waste. In addition, wire cutting is also an energy saving and environmental protection method, because it does not cause excessive heating of materials and high temperature generated waste. In manufacturing, each technology upgrade makes production more efficient and produces less waste, thereby improving energy efficiency.
Comparison of advantages and disadvantages of wire cutting
Advantage | Disadvantage |
---|---|
Contactless machining | Cutting thickness limit |
Less welding residue | Cutting speed is relatively slow |
Suitable for hard materials | Cutting surface roughness |
Suitable for small batch machining needs, capable of quickly cutting complex shaped workpieces | |
Can achieve very narrow cutting gaps, with a minimum of tens of micrometers | |
Complex shape cutting ability |
Laser cutting
Laser cutting uses high power laser beams to cut objects. The material heats up and melts rapidly in the area of the laser beam, and as the beam moves, the corresponding cutting lines are formed.
Compared with traditional cutting methods, laser cutting has many advantages. First of all, laser cutting precision, high accuracy, can cut very fine lines. Second, laser cutting speed, can greatly save time and cost. Finally, laser cutting can be used in a variety of materials, from metal, plastic to wood, ceramics, etc., has a wide range of application prospects.
Because of its high precision, fast speed and versatility, laser cutting has become one of the first choice of modern cutting technology. However, it also limits its use to such applications. Some other advantages and disadvantages are:
Advantage | Disadvantage |
---|---|
Small Heat-affected zone | Difficulty in fine machining |
No need to use cutting fluid and coolant, reducing environmental pollution and energy consumption | Limited cutting surface quality |
Flexibility and complex shape cutting ability | Easily influenced by process parameters and material characteristics |
Can achieve very narrow cutting gaps, with a minimum of tens of micrometers | |
Concentrate heat in small areas to reduce the impact of heat on materials | |
No waste of materials |
The basic steps of different cnc parts production
CNC machining can be programmed by a computer to control the movement of a tool machine to make complex parts. The following are the basic steps of CNC parts online production.
Step 1: Design CAD drawings
The first step of CNC machining is to design CAD drawings. CAD is short for computer-aided cnc parts design, which allows engineers and designers to create accurate 2D or 3D graphics. These drawings will become blueprints in the manufacturing process.
In CAD software, operators can create front, back, side, and section views. They can also add dimensions and constraints to the parts and export all the necessary geometry information into the CNC code.
Step 2: Design the G code
G code refers to the language that controls CNC machine tools. It specifies the path of the tool and the cutting parameters. After designing the CAD drawing, the CAD software generates the G code and exports it to the CNC controller or server.
G code can contain many different instructions. For example, G01 represents linear interpolation motion, while G02 represents circular interpolation motion. All of these instructions must be correct to ensure the accuracy of the final part.
Step 3: Set up CNC machine
Before CNC machining, the machine must be set up correctly. This includes installing the correct type of tool, selecting the correct cutting speed and feed rate, and ensuring the correct workpiece holding.
In addition, the exact position and attitude of the workpiece must be determined. The operator shall measure the workpiece using a three-dimensional coordinate measuring instrument and import its coordinates into the controller of the machine tool.
Step 4: Run the CNC program
Just like any other computer software, CNC programs can be run directly on the controller. After running the program, the CNC controller will control the movement of the machine tool according to the specified path and parameters.
The operator must be alert during the process. They should observe the cutting area and the workpiece to make sure everything is going well.
Step 5: Finish machining and check quality
Once the CNC is finished, the operator should check the quality of the parts. They can use measuring tools to check the size and position of edges, planes, and holes. If needed, they can readjust machine tools and cutting parameters to correct any problems that may arise

cnc machining process tips
CNC technology is widely used in automobile, aircraft, robot and other manufacturing industries. Different types of parts need different machining technology and parameter Settings.
In the automobile industry, CNC technology is mainly used in the production of engine, brake system, transmission system and other parts. These parts need to be characterized by high precision, high reliability and high strength.
In the aircraft industry, CNC technology is mainly used in the production of various types of aircraft parts, such as rim, engine frame, disc, etc., these parts are directly related to the safety of the aircraft.
In the robot industry, CNC technology is mainly used in the production of communication equipment, electronic components, robot joints, etc., these components need high precision and high accuracy.
CNC technology in the machining of different parts of the basic steps No matter what kind of parts, its machining basic steps are similar. These steps involve preheating the machine, positioning the center of rotation, clamping the part, selecting the correct machining parameters, starting machining, and completing the part.

Outsource your cnc parts to Longsheng Technology
We provide a full range of CNC manufacturing services, including CNC milling, CNC turning, and other CNC parts manufacturing services. We can also provide CNC parts customized according to your requirements or design drawings. Our complete production process is smooth and smooth, and ensure to provide you with a complete production process within the expected time.
If you are looking for a reliable CNC parts manufacturer, Longsheng Technology is your best choice. Please contact us to learn more about the services we offer and how our team can provide you with the best CNC machining experience possible.
FAQ
The main limitation of CNC machining is equipment cost and design, programming and other skills. For small businesses or individuals, buying CNC equipment can be an expensive investment. In addition, because CNC machining requires skilled programming skills, some people may need to receive professional training or hire professional programmers.
CNC processing can process metal, wood, plastic, glass and other materials. According to different materials, the processing method will be different. For example, metals often require higher cutting speeds and more oil.
The advantages of CNC machining are its ability to provide high precision results, short cycle processing time and enhanced production efficiency. CNC machining can also realize precision shape and complex geometric graphics processing, for mass production and custom processing has a very important application significance. In addition, CNC machining can also reduce the impact of human factors on the quality of finished products, improve the consistency and stability of production.