As a professional CNC machining manufacturer, we know how important it is to select the right materials for our customers’ projects. The choice of material can directly impact the quality, durability, and performance of CNC machining parts. In this article, we will share our experience and knowledge on how to select suitable materials for CNC machining parts.
Material Selection Criteria for CNC Machining Parts
Before we delve into the various materials used in CNC machining, it’s essential to understand the factors that affect material selection. Here are some of the criteria that you should consider:
Mechanical Properties
The mechanical properties of a material, such as tensile strength, yield strength, hardness, and ductility, determine its ability to withstand load and deformation. Choosing a material with suitable mechanical properties is crucial for ensuring the part’s structural integrity and durability.

Thermal Properties
The thermal properties of a material, including thermal conductivity, coefficient of thermal expansion, and melting point, affect its ability to conduct, transfer, and withstand heat. Materials used in high-temperature applications require excellent thermal stability and resistance to thermal fatigue.
Electrical Properties
The electrical properties of a material, such as conductivity, resistivity, and dielectric constant, determine its ability to conduct or insulate electricity. Materials used in electrical and electronic components must have high conductivity and low resistance to ensure optimal performance.
Chemical Properties
The chemical properties of a material, such as corrosion resistance, chemical stability, and compatibility with other materials, affect its ability to resist degradation and maintain its properties over time.
Cost and Availability
The cost and availability of a material are essential considerations in any manufacturing project. While some materials may offer superior properties, they may also be more expensive or harder to source than other alternatives.
Processability
The ease of machining, welding, forming, and finishing a material affects the time, cost, and quality of the manufacturing process.
cNC machining parts common materials
Here are some of the more common materials used in machined parts and their key characteristics:
Aluminum: Like all metals, aluminum alloys come in a wide variety, but the most common are 6061-T6 (considered a universal alloy) or 7075-T6 (a favorite of the aerospace industry). Both materials are easy to work with, resistant to corrosion, and have a high strength-to-weight ratio. Aluminum is used in aircraft parts, computer parts, cookware, building parts, etc. (In case you were wondering, T-6 refers to the tempering of aluminum, or the way it is processed in a factory).
Cobalt-chrome: Need a knee or hip Replacement? It is likely to be made of cobalt-chromium (CoCr), a tough, wear-resistant alloy. The biocompatible metal, also known by its brand name stellite, is also widely used in turbine blades and other parts that require high strength and heat resistance. Unfortunately, it is difficult to cut and has machinability of around 15% (compared to 100% machinability for 1212 mild steel and 400% machinability for aluminum).
Inconel: Another heat-resistant super alloy (HRSA), Inconel is the best choice for extreme temperatures or corrosive environments. In addition to its use in jet engines, the Inconel 625 and its harder, sturdier sibling, the Inconel 718, are used in nuclear power plants, oil and gas RIGS, chemical processing facilities and more. Both are fairly weldable, but are expensive and even more difficult to work than CoCr, so they should be avoided unless needed.
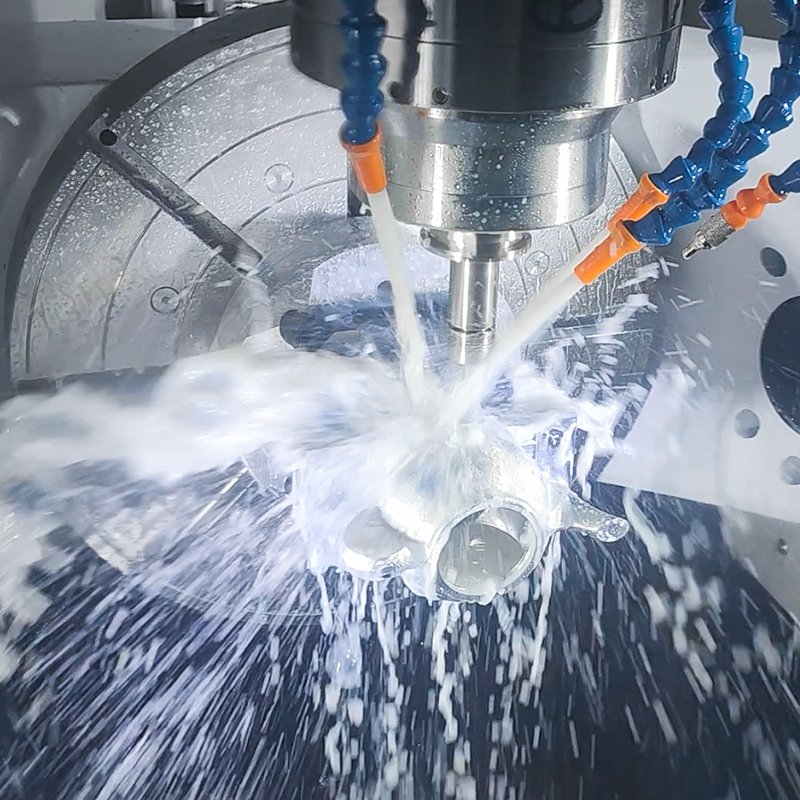
Stainless steel: By adding a minimum of 10.5 percent chromium, reducing the carbon content to a maximum of 1.2 percent, and adding alloying elements such as nickel and molybdenum, metallurgists turn ordinary rust-prone steel into stainless steel, the manufacturing industry’s anti-corrosion switch killer. However, with dozens of levels and categories to choose from, it can be difficult to determine which is best for a given application. For example, the crystal structure of austenitic stainless steel 304 and 316L makes them non-magnetic, non-hardenable, malleable and fairly ductile. Martensitic stainless steel (Grade 420 is grade 1), on the other hand, is magnetic and hardenable, making it ideal for surgical instruments and a variety of wear-resistant parts. There is also ferritic stainless steel (mostly in the 400 series), biphase steel (think oil and gas), and precipitate-hardened stainless steel with 15-5 PH and 17-4 PH, all of which are favored for their excellent mechanical properties. Machinability ranges from fairly good (416 stainless steel) to moderately poor (347 stainless steel).
Steel: As with stainless steel, there are too many alloys and properties. But four important questions to consider are:
- The cost of steel is usually lower than that of stainless steel and superalloys
- All steel corrodes in the presence of air and moisture
- With the exception of some tool steels, most steels have good workability
- The lower the carbon content, the lower the hardness of the steel (indicated by the first two digits of the alloy, such as the three common choices of 1018, 4340, or 8620). That said, steel and its close relative iron are by far the most commonly used of all metals, with aluminum not far behind.
The list does not mention the red metals copper, brass and bronze, or titanium, another super-important superalloy. Nor does it mention that some polymers, such as ABS, which is the material of Lego bricks and drains, are both mouldable and machined, with excellent toughness and impact resistance.
Engineering grade plastics, acetals, are a notable example, applied to everything from gear to sporting goods. Nylon’s combination of strength and flexibility has replaced silk as the material of choice for parachutes. There are also polycarbonate, polyvinyl chloride (PVC), high density and low density polyethylene, etc. The key is that the choice of materials is wide, so it makes sense as a parts designer to explore what is available, what is good, and how it is processed. Speedplus offers over 40 different grades of plastic and metal materials.
Common Materials Used in CNC Machining
Some of the most commonly used materials in CNC machining include:
- Aluminum: Lightweight, corrosion-resistant, and easy to machine. It is often used for aerospace and automotive parts.
- Steel: Strong and durable, commonly used for structural and mechanical parts.
- Stainless Steel: Corrosion-resistant and can withstand high temperatures. It is often used for medical and food processing equipment.
- Plastics: Lightweight and cost-effective. They are often used for prototyping and low-volume production.

Factors to Consider When Selecting Materials for CNC Parts
Several factors should be considered before selecting materials for CNC parts, such as strength, durability, hardness, density, thermal properties, and abrasion resistance. Additionally, it’s crucial to choose materials that are easy to machine, available, and cost-effective.
Based on these factors, here are some common materials used in CNC machining:
Aluminum: Aluminum is a widely used material in CNC machining due to its excellent strength-to-weight ratio, easy machinability, and corrosion resistance. It’s suitable for a range of industries and applications, including aerospace, automotive, and electronics.
Steel: Steel is a durable and versatile material, making it a popular choice in popular machinery, automotive, and construction industries. Types of steel commonly used include stainless steel, carbon steel, and alloy steel.
Copper: Copper is an excellent choice for electrical and thermal conductivity, making it ideal for electronics and heating applications.
Plastics: Plastics are lightweight, cost-effective, and easy to machine, making them a common choice in industries such as packaging, medical, and consumer products.
Conclusion
At our CNC machining manufacturing facility, we specialize in providing high-quality CNC parts that meet or exceed our customers’ specifications. Material selection is a crucial factor in our product development process, and we have the expertise to provide the right materials for your project.
By following our guide, you can choose the right material for your CNC machining parts that ensure the consistent performance and longevity you expect. With our industry expertise and robust manufacturing capabilities, we can help you achieve your goals and exceed your expectations.
In conclusion, material selection is an essential part of any CNC machining project. The right materials can ensure the consistent performance, longevity, and quality of your parts. Whether you’re working on a large-scale project or a small-scale product, our CNC machining manufacturing facility has the resources and expertise to help you achieve your goals.