In the process of CNC machining and production of precision parts, anodizing is a surface finishing method with mature technology, simple process and wide application. It can add an oxide layer to the parts, protect their surfaces from metal wear and Corrosive substance, and improve the beauty of these precision parts.
This technology is particularly common in the aerospace, automotive, and medical fields, as the requirements for high-strength and corrosion-resistant parts are becoming increasingly high.
This article will provide a detailed explanation of the application of anodizing in CNC machining parts, including its working principle, advantages, different types, and applications. Through the introduction of this article, readers will have a deeper understanding of this technology and expert skills in achieving optimal anodizing finish while saving costs and energy.
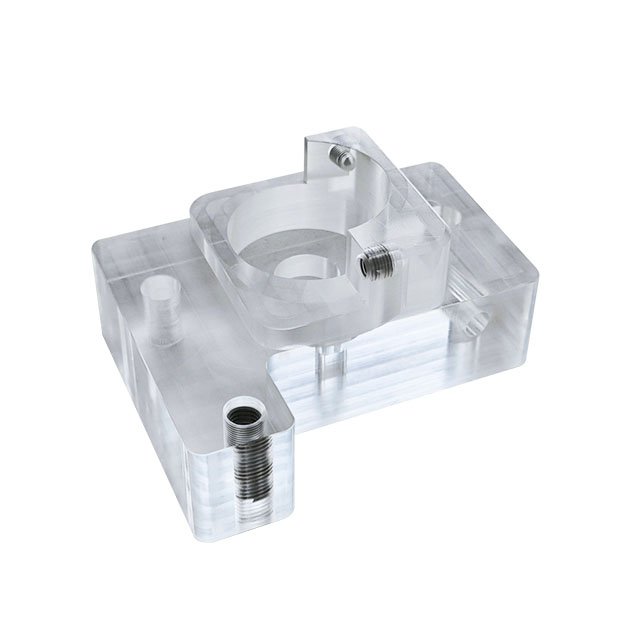
Definition and principle of anodizing
What is anodizing? What is its principle? Below is a detailed introduction to the definition and principle of anodizing, please continue reading:
Definition of Anodization
Anodic oxidation, also known as anodic oxidation electrolysis, is a special surface finishing method that utilizes anodic oxidation reactions to oxidize metal surfaces into a more corrosion-resistant and decorative oxide film, thereby achieving a certain degree of protection and beautification effect. It is mainly used to improve the surface characteristics of metal materials, such as needle shape, polishing, decoration, and corrosion resistance.
principle of anodizing
The principle of anodic oxidation is based on the electrochemical principle of the anode and cathode. When the metal serves as the anode, under the action of current, an oxidation reaction occurs on the surface of the anode metal, forming an oxide film layer.
The oxidation process is caused by the reaction between the oxide and oxide ions on the anode surface and the electrolyte. This process can be divided into four steps:
1.Initial oxidation stage: When the metal surface first comes into contact with the electrolyte, due to its strong adsorption ability of surface atoms, sodium ions (or other) in the electrolyte can be adsorbed, resulting in a layer of atomic adsorption layer on the metal surface.
2.Stage of pore formation: As the electrolysis process continues, the atomic adsorption layer gradually thickens, making it difficult for outward expanding metal ions to pass through the adsorption layer. As a result, many straight oxide film shells are formed on the surface of the anode, and holes appear inside the shell.
3.Hardening and film growth stage: pores grow upwards, and the film layer gradually thickens and solidifies, forming the same hard film. When the thickness of the film reaches an appropriate value, a so-called “hardening” phenomenon occurs, and the oxide film has sufficient grip and hardness to resist external forces.
4.Sealing and thickening stage: When the oxide film is formed until the end of the entire stage mentioned above, the cathode will no longer absorb current, and the oxide film gradually forms a type of microbubble to fill the holes and uneven surface micro areas. At this point, the oxide film is locked to prevent further expansion, and ultimately one of the representatives of excellent anti-corrosion technology is developed.
For more information on other surface finishing processes, please click the link【Various Surface Finishing Processes】
Compared to traditional painting and spraying methods, the advantages of anodizing
The following is a comparison list of the advantages of anodizing compared to traditional painting and spraying surface finishing methods:
Advantage | Anodizing | Traditional Painting/Spraying |
---|---|---|
corrosion resistance | High corrosion resistance, able to form a dense oxide layer | Additional corrosion protection coating is required |
hardness | Good hardness increases the wear resistance of the parts | Depending on the selected coating type and thickness |
Color and Appearance Effects | Multiple colors and appearance effects available | Limited color selection, requiring multiple layers of paint to achieve a specific appearance |
environmentally friendly | No harmful volatile organic compound emissions | May produce harmful volatile organic compounds |
Dimensional control and consistency | Maintain consistency in part size and shape | Affected by coating thickness and process |
thermal stability | Capable of withstanding high temperatures and thermal cycles | Limited by the thermal stability of the selected coating |
conductivity | Maintain good conductivity | Requires the use of conductive coatings or the addition of conductive fillers |
Maintenance and Durability | Relatively low maintenance requirements and longer lifespan | Regular maintenance and repainting may be required |
Cost-effectiveness | Relatively low long-term costs | The initial coating cost is lower, but may require more frequent re coating |
Case-hardening and lubricity | Improve surface hardness and lubricity | Additional coatings or additives are required to achieve lubricity |
For ways to improve the surface roughness of parts, see this article【Surface Roughness】
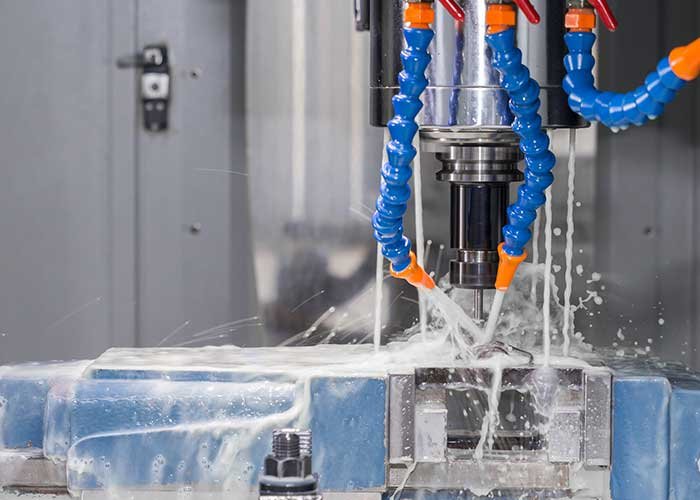
Why Anodizing Finish CNC machining parts
Anodizing is a chemical reaction that forms a film on the surface of a metal by oxidizing dust, aluminum oxide, etc. In CNC machining, anodizing has four important uses:
1.Improving the corrosion resistance of parts
After anodizing, a layer of oxide film is formed on the surface of CNC parts, which is almost impenetrable, making the surface of CNC parts harder and more wear-resistant. At the same time, it can reduce the erosion of various chemical reactions on CNC parts and improve the corrosion resistance of CNC parts.
2.Improving the overall appearance of parts
Anodizing can change the color of the surface of CNC parts, allowing them to have multiple color choices and improving the decorative effect of CNC parts, keeping the surface of CNC parts clean, beautiful, and less susceptible to external influences.
3.Improving the surface hardness of parts
After anodizing finish, a fairly hard oxide film is formed on the surface of CNC parts online, with a thickness generally between 5-15 microns, making CNC parts more wear-resistant and durable
4.Preventing electromagnetic interference
Some special parts, such as electronic parts, may generate certain electromagnetic waves during operation. If these electromagnetic waves are not effectively processed, they can have an impact and interference on other equipment, ultimately leading to equipment failure. After anodizing, CNC parts will form a sealed oxide film on the surface, which can effectively prevent electromagnetic interference and ensure that the equipment is not affected by any external factors.
The following table provides an overview of the five types of anodizing available in CNC machining parts and their characteristics:
Anodizing type | thickness range | characteristic | Applicable parts |
---|---|---|---|
Chromium sulfate type (Type I) | 5-15 μm | High hardness and wear resistance, good corrosion resistance, and high temperature resistance | Aerospace parts, automotive parts, industrial equipment |
Sulfuric acid type (Type II) | 5-25 μm | Uniform and dense oxide layer with good corrosion resistance and decorative properties | Household products, building materials, electronic products, automotive components |
Sulfuric acid hard type (Type III) | 25-100 μm | Extremely high hardness and wear resistance, good corrosion resistance, and good insulation | Firearm parts, tools, mechanical parts |
Boron sulfate type (Type II B) | 15-40 μm | Good corrosion resistance, wear resistance, and insulation of mechanical components | Electronic devices, Electrolytic capacitor, Electrical connector, auto parts |
Magnesium sulfate type (Type II C) | 10-25 μm | Good corrosion resistance, good wear resistance, lightweight | Aerospace parts, electronic products, motorcycle parts |
Anodizing Finish for different types of materials
The following is an overview of the anodizing processes applicable to different types of CNC machining materials and their process steps:
1.Aluminium alloy
Applicable technology
Commonly used processes are sulfuric acid (Type II) and chromium sulfate (Type I).
Process step
Cleaning: Use alkaline cleaning agent or solvent to clean aluminum parts to remove surface impurities and grease.
Anodizing: The aluminum part is used as the anode and electrolyzed in a sulfuric acid solution to form an oxide layer by applying an electric current.
Dyeing (optional) : Dye the oxide layer with a dye or pigment solution to change the surface color.
Sealing: The oxide layer is exposed to hot water, so that it combines with water molecules to form a sealing layer, improving corrosion resistance and wear resistance.
2.Magnesium alloy
Applicable technology
Sulphate hard Type (Type III), Magnesium sulphate type (Type II C)
Process step
Cleaning: Remove surface impurities and grease.
Anodic finish: Electrolytic finish in sulfuric acid or magnesium sulfate solution to produce an oxide layer.
Seal: Seal the oxide layer in hot water.
3.Titanium alloy
Applicable technology
Commonly used processes are sulfuric acid Type (Type II B) and magnesium sulfate type (Type II C).
Process step
Cleaning: Use alkaline cleaning agent or solvent to clean titanium parts to remove surface impurities and grease.
Anodizing: The titanium parts are used as the anode and electrolyzed in sulfuric acid or magnesium sulfate solution to generate an oxide layer.
Sealing: The oxide layer is exposed to high temperature water so that it combines with water molecules to form a sealing layer.
If the desired surface effect and other factors vary, please contact our Longsheng engineers for accurate process guidance.
For information on surface finishing of stainless steel, please click the link 【Stainless Steel Surface Finishing Options】
Common Applications of Anodizing Finish for CNC Machining Parts
The anodizing finish of CNC machining parts can produce surfaces of different colors and textures, achieving surface design and possessing corrosion resistance, wear resistance, aesthetics, and other functions. The following are some common application areas:
Automotive parts
Anodizing finish can be used for automotive components, such as engine parts, chassis components, body exterior, hood, doors, etc. The aluminum components treated with anodizing not only have better corrosion resistance, but also can adsorb coatings, increasing the aesthetics of the car.
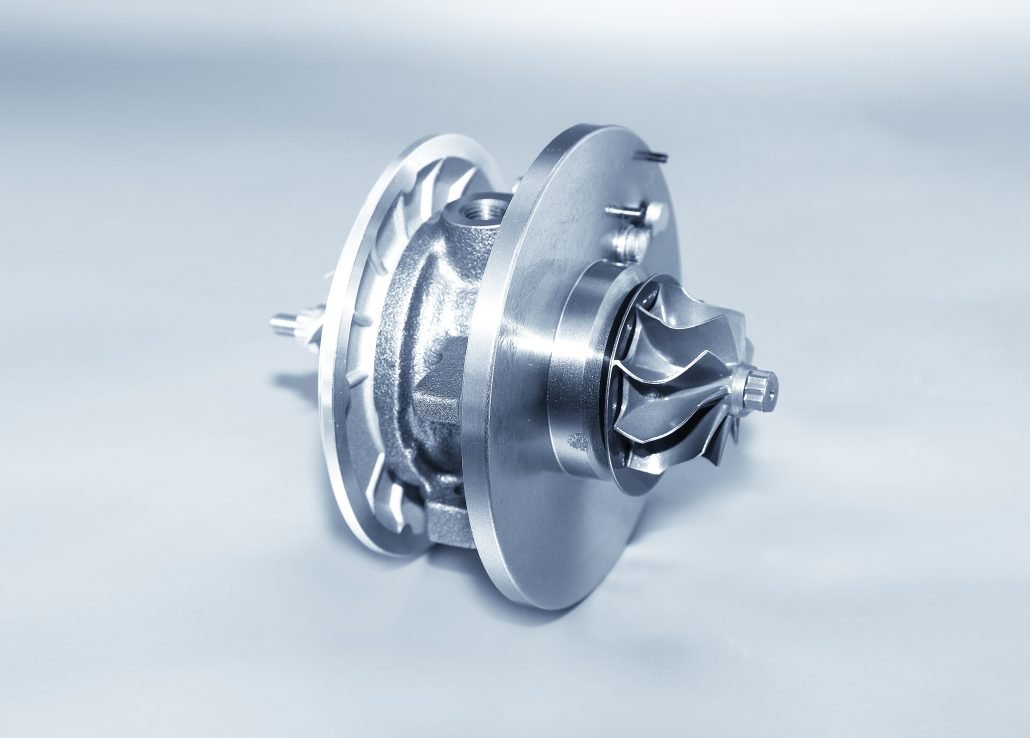
electronic product
In the manufacturing of electronic products, anodizing finish is often used for electronic parts and shells, such as radiators, electronic case, connectors, computer case, Mobile phone case, keyboard, etc., which need to be anodized to improve their conductivity, corrosion resistance, durability and diversity of appearance
Aerospace parts
In the field of aerospace, anodizing finish can be applied to aviation components, such as aircraft structural components, fuel filters, engine manufacturing, engine components, bolts, etc., which can increase surface hardness, wear resistance, corrosion resistance, pollution resistance, and other performance. In addition, anodizing finish can also be used to manufacture metal surfaces on the exterior of aircraft.
Sports and outdoor products
Anodizing finish can be applied to sports equipment and outdoor equipment, such as bicycle parts, hiking equipment, outdoor lighting equipment, etc., to improve their durability and corrosion resistance.
Advantages and disadvantages of anodizing Finish
Anodizing finish has a variety of different benefits in different application areas, can improve the corrosion resistance of the metal, hardness, scratch resistance and aesthetics, etc., although there are many advantages of anodizing, but there are some disadvantages, in this section, will study the advantages and disadvantages of anodizing finish in custom manufacturing.
Anodizing Finish advantages
1.Improved corrosion resistance: Anodizing finish can form a dense oxide layer, increase the corrosion resistance of the material, so that it can be used in harsh environments for a long time.
2.Increased surface hardness: The surface hardness of the anodized material is significantly increased, which enhances the scratch resistance and wear resistance.
3.Aesthetic appearance: Anodizing finish can change the surface color and appearance of the material, providing more choice and design flexibility.
4.Improved insulation performance: The oxide layer has good insulation performance, which can improve the insulation capacity of the material, and is suitable for some electronic devices and electrical applications.
5.Environmentally sustainable: Anodizing uses an aqueous solution and electrolytic process, which is relatively environmentally friendly, and the waste liquid can be recycled and treated.

Anodizing Finish disadvantages
1.Size increase: Anodizing finish will form an oxide layer on the surface of the material, which will lead to a small increase in size, which may affect some parts with high precision fit or assembly requirements.
2.Process complexity: Anodizing finish requires a series of process steps, including cleaning, pretreatment, electrolysis, etc., the operation is relatively complex, requiring professional equipment and technology.
3.Limitations on materials: Anodizing finish is mainly suitable for specific materials such as aluminum, magnesium and titanium, and has a poor effect on other materials such as steel and brass.
4.Yield control: The yield of anodizing finish is affected by many factors, such as process parameters, equipment conditions, etc., and requires strict control and monitoring.
Longsheng Technology: Provide CNC machining parts one-stop service
When you are ready to start your next custom CNC machining parts project, Longsheng Technology is ready to serve you. We believe that anodizing is a reliable, economical and proven precision CNC machining process, and we meet the requirements of different industries requiring high strength, high precision, or special materials and special surface finish
We use the expertise of our technicians to provide the best anodizing finish . No matter how complex your project, you can be sure to get the best results, customers can customize the design to their requirements, and then we can tailor the parts for machining, ensuring the precision and quality of the product
If you have any questions or inquiries about custom CNC machining parts and anodizing finish , please contact us through the following ways
Call us on +86 195 5106 7050 or email us at info@longshengmfg.com
conclusion
Anodizing finish is a very useful surface finishing technology that can help improve the surface quality and function of parts in CNC integrated manufacturing production lines. Of course, before conducting anodizing finish , it is necessary to ensure the quality and applicability of the material to ensure the quality and durability of the final product.
Before choosing anodizing, you need to consider the needs, material characteristics, and desired efficacy, and ultimately choose the type that suits you. Therefore, whether you can obtain the best surface finish for your CNC machining parts depends on your manufacturing partner. So contact Longsheng Technology immediately for your next project. We have been looking forward to working with you
I hope the content discussed in this article about “Anodizing finish : Application in CNC Machining Parts” can be helpful to everyone. For more technical articles, please follow us
FAQ
Anodizing finish can increase the hardness and corrosion resistance of the surface layer of aluminum materials. Therefore, this technology can be used to improve the performance and lifespan of CNC machining parts, thereby improving product quality and reliability. In addition, the oxide layer can also be used to add color to the product, where various colorants can be used, including colorless and colored ones.
Anodizing method can be used for Metalloid materials and some plastic materials. In CNC machining, anodizing is widely used in the processing of metals such as aluminum and its alloys, copper, magnesium, zinc, and steel.
Cost is a very important factor, and in the field of CNC machining, the cost of anodizing is usually related to multiple factors such as the size, thickness, and processing volume of the product. If you are calculating costs for the next project, please contact us and provide a quotation based on your requirements