Appliances are an integral part of our daily lives. From refrigerators to washing machines and everything in between, these appliances make life more convenient and comfortable. However, at times, these appliances break down and need to be repaired. A faulty part may cause the appliance to malfunction, affecting the overall performance. This is where Longsheng’s Appliance Parts Plastic Injection Molding services come in.
Longsheng is a professional Plastic Injection Molding service provider that specializes in manufacturing high-quality appliance parts. We have more than ten years of experience, and our team is comprised of highly skilled engineers and technicians who utilize cutting-edge technology to produce the best quality products for our clients.

The Advantages of Injection Molding for Appliances
Why do so many appliance manufacturers turn to an injection molding company to play a role in supplying plastic parts? Based on a process that uses molten plastic forced into a highly precise mold under pressure and allowed to cool, injection molding has been one of the primary means for producing plastic components for more than half a century. Highly versatile and capable of delivering several advantages over other manufacturing processes, appliances use injection molded parts for many reasons:
- High-pressure injections enable plastics to reach into even the deepest parts of a mold, enabling intricate shapes and designs that minimize the need for additional processing after molding.
- Molding produces a high part volume at a very rapid pace. Although the design and finalization of each mold may take some time, the manufacturing process moves very quickly afterwards. Once you have mold designs in hand, you can use them indefinitely.
- Injection molding enables the easy addition of fillers for changing the properties of a plastic. Inserts and additional components inside the mold allow for even more complex processes, such as overmolding.
What Appliances Use Injection Molding Processes?
It’s easy to see why appliance manufacturers would favor a high-volume, highly replicable process for creating their plastic components — but what are those components? Let’s look at some of the most common examples you might find:
- Refrigerator components. In-door shelving units for holding condiments and jars and sliding drawer frames both likely use injection molding. Fridge and freezer door handles also come from a mold, as do many of the components used in ice makers, such as the plastic auger that dispenses ice on demand.
- Dishwasher components. Much of the interior of modern dishwashers comes from injection molds, including silverware caddies, the dishwasher racks themselves, and the water-spraying wash arms, and even the door or hatch to the detergent dispenser.
- Kitchen gadgets. A toaster’s exterior shell may come entirely from a plastic mold, as do blender housings and the blender’s container itself. Plastic food storage containers use molding, too.
types of injection molding techniques for home appliances
Precision Injection Molding
In home appliance manufacturing, precision injection molding has become a crucial technique. It ensures that products have both precise dimensions and consistent repeatability in weight. By leveraging this advanced molding technique, manufacturers can achieve high-pressure, high-speed injections.
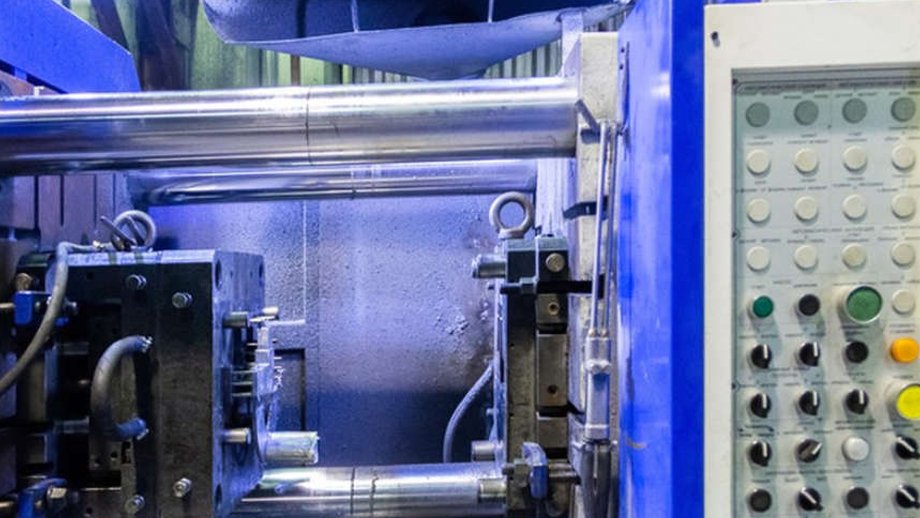
Open-Loop Vs. Closed-Loop Control In Precision Molding
One of the standout features of precision injection molding is its control mechanism. Typically, the process can be governed by either an open-loop or a closed-loop control system. This flexibility allows for meticulous adjustments to the injection molding parameters, ensuring the highest degree of accuracy throughout the process.
Demands On Mold Precision And The Rise Of Compact Machines
Precision in injection molding for home appliances isn’t just about the process; it extends to the tools used. The molds, in particular, need to meet stringent accuracy standards. Recognizing this demand, the market has seen a growing popularity for compact precision injection molding machines. These smaller machines, while being space-efficient, do not compromise on the quality or precision of the products they produce.
Rapid Prototyping
As the home appliance industry witnesses a shift towards diversified product offerings and continuous upgrades, rapid prototyping technology has swiftly risen to prominence. This technique is primarily employed for crafting plastic casings for home appliances. One of the standout advantages of rapid prototyping is its ability to produce small batches of components without the need for molds, streamlining the production process.
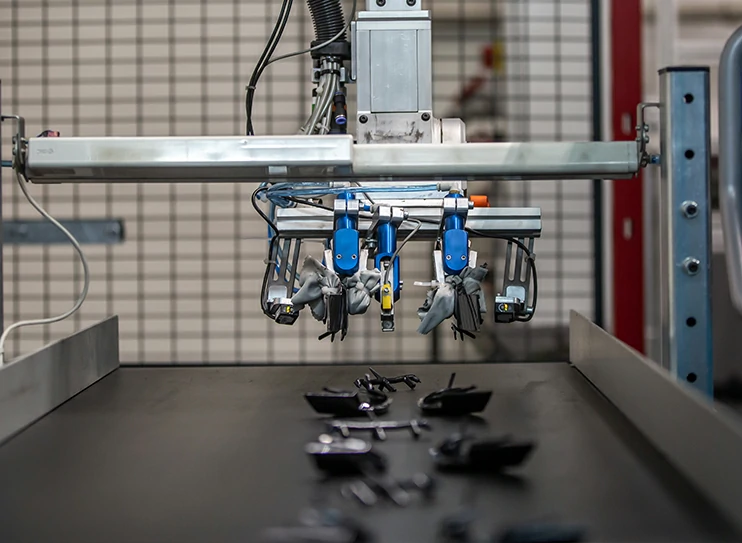
Laser Scanning Vs. Liquid Photopolymerization
Currently, the most mature methods in rapid prototyping are laser scanning molding and liquid photopolymerization. Among these, laser scanning molding sees more extensive applications. The equipment for laser scanning consists of a laser source, a scanning device, a powder dispensing unit, and a computer. The process involves a computer-controlled laser head that scans along a predetermined path. As the laser passes over specific areas, the plastic micro-powder heats up, melts, and bonds together. After each scan, a thin layer of powder is dispensed, and through repeated scanning, a product of a specific shape and size is formed.
Revolutionizing Home Appliance Injection Molding
The advent of rapid prototyping, especially laser scanning molding, has revolutionized the way home appliance components are produced. This technology not only ensures precision but also accelerates the production timeline, making it an invaluable asset in the ever-evolving world of home appliance manufacturing.
Fusible Core Injection Molding
usible core injection molding is a specialized technique. It is often chosen for molding products with intricate cavities that have high demands for surface roughness and precision. These are typically products that can’t be effectively produced using hollow molding or rotational molding methods.
Global Adoption And Working Principle
This technology has gained significant traction and maturity on a global scale. The underlying principle of fusible core injection molding is quite ingenious. Initially, a core that represents the cavity is molded. This core is then used as an insert during the injection molding process. As the molded part is heated, the core melts and flows out, leaving behind the desired cavity.
Material Considerations For The Core
One of the critical aspects of employing this technology is the selection of the right material for the core, ensuring it has a melting point that aligns with the injection molding process. Depending on the specific requirements, the core material can range from general-purpose plastics thermoplastic elastomers to low-melting-point metals like lead or tin. The flexibility in material choice is a key factor in home appliance injection molding processes. It allows for achieving the desired precision and quality, irrespective of the complexity of the design.
Gas-Assisted And Water-Assisted Injection Molding
Gas-assisted and water-assisted injection molding techniques have become increasingly popular due to their versatility in producing a wide range of injection-molded products. A prime example of their application is in the creation of television casings.

The Process Explained
During the injection molding process, gas or superheated water is introduced almost simultaneously with the plastic melt into the mold cavity. This results in the plastic melt enveloping the gas or water, leading to a laminated structure in the molded product. Once the product solidifies, the gas or water is released, allowing for easy demolding.
Distinct Advantages
Products manufactured using these techniques boast several benefits. They are material-efficient, exhibit minimal shrinkage, possess an appealing exterior, and maintain good rigidity. A crucial component of the molding equipment is the gas or water auxiliary device and its associated control software, ensuring the precise delivery and control of the gas or water during the molding process.
Rapid Adoption In China
In recent years, China has shown a keen interest in these techniques, conducting extensive research and rapidly integrating them into their home appliance injection molding industry. This adoption underscores the potential and efficiency of gas-assisted and water-assisted molding in producing high-quality products for the consumer electronics sector.
Electromagnetic Dynamic Molding
Electromagnetic dynamic molding is a cutting-edge technique in the realm of home appliance injection molding. This method leverages electromagnetic forces to induce an oscillating motion in the screw axially.

The Microscopic Plasticization Process
During the pre-plasticization phase, this technology ensures microscopic plasticization of the material. As a result, when the molding enters the pressure-holding phase, the structure of the molded product becomes more compact. This not only strengthens the product’s structure but also significantly reduces its internal stress, ensuring a more durable and resilient final product.
Applications And Benefits
While electromagnetic dynamic molding is particularly beneficial for products with stringent molding requirements, such as optical discs, its advantages aren’t limited to specialized items. When applied to everyday products, this technique can substantially enhance the overall quality, making it a valuable asset in the home appliance manufacturing.
about long sheng’s injection molding sevice for appliance parts
Our Plastic Injection Molding services are specifically designed for appliance parts, as we understand the importance of durable and high-performance appliances. We have a vast range of plastic molding services, including thermoplastic molding and thermoset molding, to cater to your specific requirements. We can produce complex geometries, high-precision and intricate parts, and more.

Our team of experts can produce parts that are not only aesthetically pleasing but also highly functional. We use advanced software to create designs, and our state-of-the-art machinery ensures that the manufacturing process is precise and efficient. Our experience and expertise allow us to produce stable and consistent parts that meet your exact specifications.
Our injection molding services help you save time and money on product development. The turnaround time for design feedback is only a few hours, and we offer free injection molding quotes.
- OEM ODM MOQ 1 PCS
- Tolerances down to +/- 0.005mm
- Suitable for continuous production of plastic parts
Want to turn creativity into tangible products? We are your reliable supplier of plastic injection molding services. Through our professional technology and high-quality service, we will help you achieve unique plastic products. Whether you need personal customization or mass production, we can meet your needs.
Injection Molding Capabilities
Please check our injection molding parts manufacturing capabilities, For custom tolerances, mark them clearly on your drawing.
Types | Size Tolerance |
---|---|
Maximum Part Size | 1000 × 800 × 300 mm 39.37 × 31.49 × 11.81 inch |
Minimum Part Size | 1 × 1 × 1 mm 0.039 × 0.039 × 0.039 inch |
Mold Cavity Tolerances | +/- 0.1 mm +/- 0.0039 inch |
Part to Part Repeatability | +/- 0.15 mm or less +/- 0.0059 inch or less |
Production Grades Available | From 105 grade (prototype tools) to 101 grade (high production tools) |
Tool Ownership | Customer-owned with mold maintenance |
Lead Time | Starts at 3 business days, including fast quote responses with design-for-manufacturing (DFM) feedback |
couclution
At Longsheng, we are committed to providing our clients with the best quality products and services. We take pride in our work, and our clients’ satisfaction is our top priority. We use only the best quality materials to produce our products and ensure that they meet industry standards.
We understand the importance of timely delivery, which is why we strive to deliver our products within the stipulated time frame. We follow strict quality checks at every stage of the manufacturing process to ensure that our products meet the highest standards. We also offer secondary services, such as welding and assembly, to provide comprehensive solutions to our clients.
In conclusion, Longsheng’s Appliance Parts Plastic Injection Molding services are the perfect solution for all your appliance parts needs. With our experience, expertise, and commitment, we guarantee high-quality products, timely delivery, and exceptional customer service. Contact us today to learn more about our services and how we can help you with your appliance parts requirements.

fAQs
What is injection molding?
Injection molding is used to manufacture plastic parts and products. During the injection molding process, melted plastic is injected into the mold, then cooled and hardened to form the required parts or products.
What is injection molding process steps?
- Injection: Heat the plastic into a molten state and inject it into the mold.
- Plastic filling: Ensure that the plastic fills the cavity of the mold to form the required parts.
- Cooling: Allow plastic to cool and harden, usually using a cooling system to accelerate.
- Mold opening and discharge: Open the mold and remove the formed parts, and then proceed with subsequent processing.
How does injection molding work?
Injection molding involves heating plastic materials to a molten state, then injecting them into a mold, allowing them to cool and solidify within the mold, ultimately forming the required parts or products. This process combines the plasticity of plastics with the precise shape of molds, allowing the manufacturing of various shapes and sizes of parts, from small parts to large components, to meet the needs of different industries and applications.