Brass is a common metal material widely used in the manufacturing industry for the machining of various parts and components. In order to achieve efficient, accurate, and stable machining, it is crucial to understand the difference between feed speed and cutting speed in brass CNC machining. This article will explore the differences between feed speed and cutting speed in brass CNC machining, and provide some optimization suggestio
brass CNC machining Introduction
Brass is an alloy mainly composed of copper and zinc. It has excellent conductivity, thermal conductivity, and corrosion resistance, making it widely used in fields such as electronics, instruments, architecture, and decoration. The introduction of CNC machining technology has made the machining of brass more efficient and precise, improving production efficiency and product quality.

concepts of feed rate and cutting speed
In brass CNC machining, feed speed and cutting speed are two key parameters. They have a direct impact on machining efficiency and quality.
Definition and Function of Feed Rate
In CNC machining, feed rate refers to the movement speed of the workpiece relative to the tool during the machining process. It is usually represented by the feed rate per minute (mm/min). A higher feed rate can improve machining efficiency and shorten machining time, so the choice of feed rate directly affects machining time and surface quality. However, excessive feed speed may lead to vibration and resonance problems, affecting machining quality.
Definition and Function of Cutting Speed
Cutting speed refers to the linear velocity of the tool relative to the surface of the workpiece during the cutting process. It is usually represented by the cutting distance per minute (mm/min). Cutting speed has a significant impact on machining efficiency and cutting quality.
Brass, as a relatively soft material, can usually be cut at a higher speed. Higher cutting speeds can improve machining efficiency, but excessive cutting speeds may cause tool overheating, increased wear, and brass discoloration or burning.
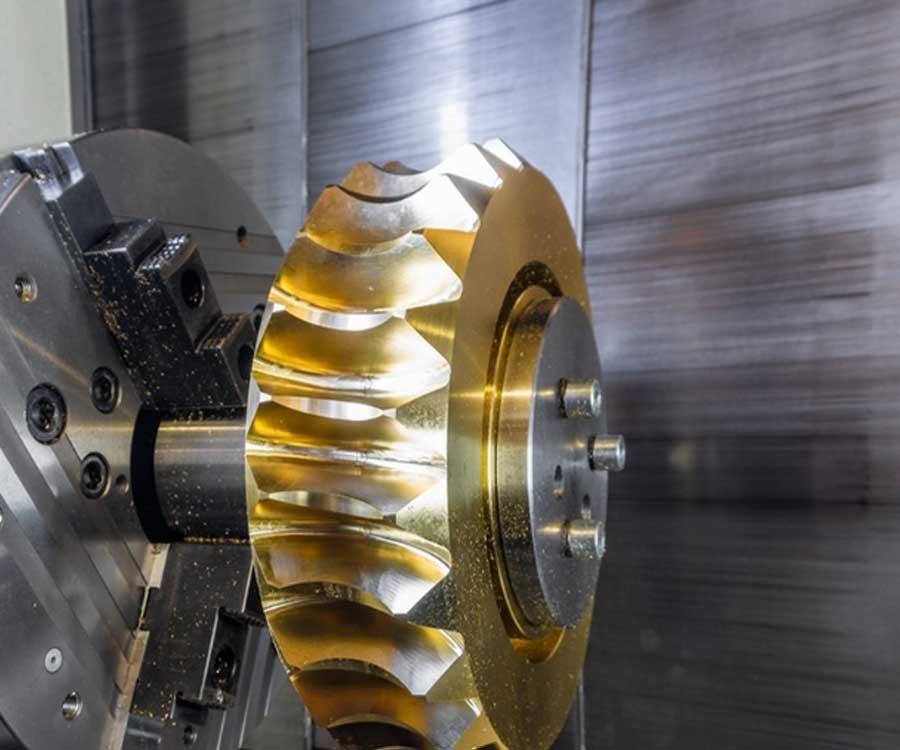
difference between feed speed and cutting speed in brass CNC machining
In brass CNC machining, there are some differences between feed speed and cutting speed. Please continue reading:
relationship between feed speed and cutting speed
In precision CNC machining, feed speed and cutting speed are closely related. The feed speed determines the movement speed of the workpiece during the cutting process, while the cutting speed determines the speed at which the tool contacts the workpiece. By selecting and controlling the feed rate and cutting speed reasonably, efficient machining of brass can be achieved.
Differences in requirements for feed speed and cutting speed for brass
There are some differences in feed speed and cutting speed in brass CNC machining:
Difference 1: Different objects of action
The feed speed mainly affects the movement speed of the workpiece, directly affecting the machining speed and efficiency. The cutting speed mainly affects the relative speed between the tool and the workpiece surface, directly affecting the cutting quality and surface roughness.
Difference 2: Different influencing factors
The selection of feed rate is limited by machining equipment, tool rigidity, and machining technology. When selecting the feed rate, it is necessary to consider factors such as the material, size, and shape of the workpiece. The choice of cutting speed mainly depends on the hardness of the material and the performance of the cutting tool.
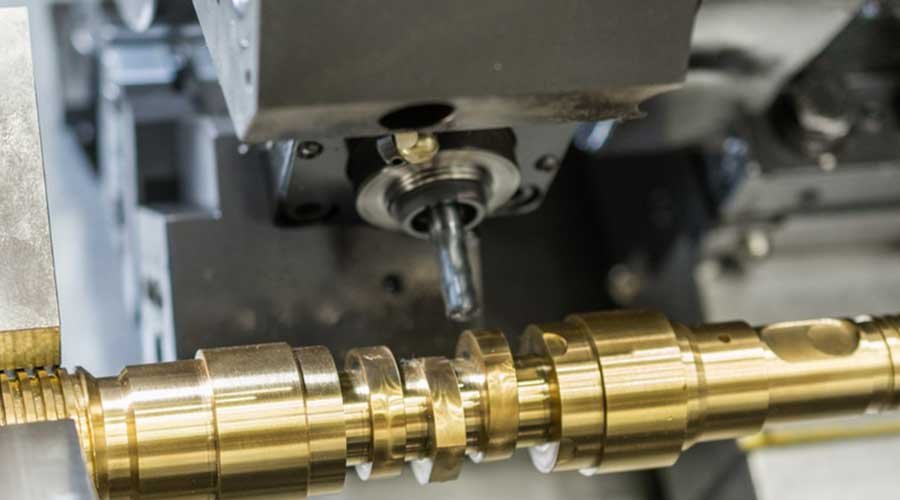
Difference 3: Different impacts on machining results
The change in feed rate directly affects the machining speed and surface quality. Higher feed rates can improve machining efficiency, but may lead to an increase in surface roughness. The changes in cutting speed mainly affect cutting heat and cutting force, which in turn affect tool life and machining accuracy.
Difference 4: Different adjustment methods
The feed rate can be achieved by adjusting the feed rate parameters of CNC machining equipment; The cutting speed is achieved by adjusting the spindle speed. In practical operation, the feed speed and cutting speed can be independently adjusted according to specific requirements and machining technology.
conclusion
Brass is relatively soft and suitable for higher feed speeds. A higher feed rate can improve machining efficiency and reduce machining time. However, an excessively high feed rate may cause vibration and resonance problems, affecting the quality of the machining surface.
Therefore, the specific requirements for feed rate will be influenced by factors such as machining equipment, tool performance, and the requirements for the processed workpiece. In practical applications, it is necessary to choose an appropriate feed rate based on the specific situation.
For cutting speed, brass can also use higher values. Due to the lower hardness of brass, higher cutting speeds can be used to improve machining efficiency. However, excessive cutting speed may cause tool overheating, increased wear, and brass discoloration or burning. Therefore, while ensuring machining efficiency, it is necessary to pay attention to controlling the cutting speed.
Optimizing the feed rate and cutting speed in brass CNC machining
In order to optimize the feed rate and cutting speed in brass CNC machining, the following are some optimization principles and suggestions.
Optimization principles for feed rate and cutting speed
In order to optimize the feed rate and cutting speed in brass CNC machining, the following are some principles and suggestions:
1.Select an appropriate cutting speed range based on the hardness of brass material. Through experimentation and practice, find the optimal cutting speed to ensure a balance between machining efficiency and cutting quality.
2.Select the appropriate feed speed range according to the performance and stability of the machining equipment. Consider the rigidity and dynamic response of the machine tool to avoid vibration and resonance problems caused by excessive feed speed.
3.Use appropriate tools and tool coatings to improve cutting efficiency and quality. The selection of cutting tools should consider the characteristics of brass materials and machining requirements.
4.Conduct experiments and optimizations to adjust feed and cutting speeds based on machining results and requirements. Continuously optimize machining parameters through experiments and feedback to achieve the best machining effect.

Practical Application Cases of Feed Rate and Cutting Speed
In order to better understand and apply the feed rate and cutting speed in brass CNC machining, the following are some practical application cases:
Case 1
For turning brass shaft materials with a diameter of 20mm, a feed rate of 200 mm/min and a cutting speed of 150 m/min can be selected to achieve high machining efficiency and surface quality.
Case 2
For the milling of brass plates, a feed rate of 300 mm/min and a cutting speed of 250 m/min can be selected to balance machining efficiency and cutting quality.
conclusion
In brass CNC machining, feed speed and cutting speed are two important parameters that directly affect machining efficiency and quality. Appropriate feed and cutting speeds can achieve efficient machining of brass.
However, adjustments and optimizations need to be made based on the characteristics, machining requirements, and equipment performance of brass. By selecting and controlling the feed rate and cutting speed reasonably, satisfactory brass machining results can be obtained.
This article introduces the differences between feed speed and cutting speed in brass CNC machining, and provides optimization suggestions. I hope this article is helpful to practitioners and researchers involved in brass CNC machining, in order to achieve more efficient, accurate, and stable brass machining.
Start your brass CNC machining services!
At Longsheng Technology, our equipment can accurately manufacture the products you need in the shortest possible time. When you cooperate with us, you can receive a complete service – from prototype to testing, and ultimately mass production. Our team always maintains open communication to ensure that your product can achieve the best results.
Whether you need rapid prototype production or mass production, we can help you achieve your dreams and provide you with the highest quality brass CNC machining services.
Contact us for more information and see how we can help you.
Mobile:+86 185 6675 9667(Gloria Wu)
E-Mail:gloria.wu@longshengmfg.com