This document explores the differences between CNC milling and electrochemical machining (ECM), two methods of material removal in manufacturing. While both are used to create complex shapes and features on metal parts, they use different techniques to achieve this. CNC milling is a subtractive manufacturing process that uses computer-controlled machines to remove material from a workpiece, while ECM is a non-traditional machining process that uses electrolysis to remove material from a workpiece. Each process has its own advantages and disadvantages, and the choice of process will depend on the specific requirements of the part being produced.
How Does Electrochemical Machining Work?
Electrochemical machining (ECM) is a manufacturing process that removes metal by an electrochemical process. It is used for mass production and is most commonly used to create complex shapes in hard metals that are difficult to machine by conventional methods.
ECM works by using an electrolyte (usually a salt solution) to dissolve metal from a workpiece. The workpiece is connected to the positive terminal of a DC power supply, while the tool is connected to the negative terminal. The tool is usually made of a conductive material, such as copper or brass, and is shaped to the desired form of the final product.
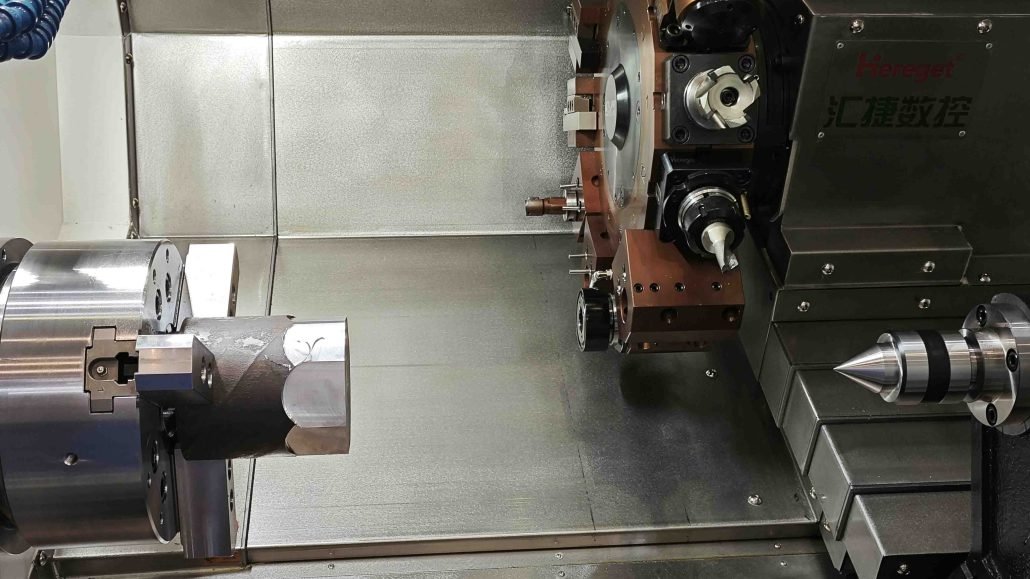
When the DC power supply is turned on, an electrochemical reaction occurs between the electrolyte and the workpiece. Metal ions are dissolved from the workpiece and carried away by the electrolyte, leaving a cavity in the shape of the tool. The process can be controlled by adjusting the voltage, current, and electrolyte concentration.
ECM has several advantages over traditional machining methods. It can machine complex shapes with high accuracy, and it can work with very hard metals that are difficult to machine by other methods. It is also a non-contact process, which means that the tool does not touch the workpiece, reducing the risk of damage or wear.
In conclusion, ECM is a highly specialized manufacturing process that uses electrochemical reactions to remove metal from a workpiece. It is a useful method for producing complex shapes in hard metals, and offers several advantages over traditional machining methods.
How Does CNC Milling Work?
CNC milling is a manufacturing process that involves the use of computer-controlled machines to remove material from a workpiece. The process involves the use of a cutting tool to remove material from the workpiece to create a desired shape.
The first step in CNC milling is to create a CAD model of the part that needs to be created. This model is then loaded into the CNC machine’s software. The software then generates a toolpath that the machine will use to cut the part.
Once the toolpath has been generated, the operator loads the necessary tools into the machine’s tool changer. The machine then automatically selects the appropriate tool for each step in the toolpath.
The workpiece is then loaded into the machine’s work area and secured in place using clamps or vises. The machine then begins to remove material from the workpiece according to the toolpath.
As the machine is cutting the part, it constantly checks the cutting tool’s position and adjusts it as necessary to ensure that the part is being cut to the correct specifications. The machine also monitors the cutting tool’s wear and automatically replaces it when necessary.
Once the part has been completely machined, it is removed from the machine and inspected to ensure that it meets the desired specifications.
CNC milling is used in a variety of industries, including aerospace, automotive, and medical device manufacturing. It offers a high level of precision and repeatability, making it an ideal choice for creating complex parts with tight tolerances.
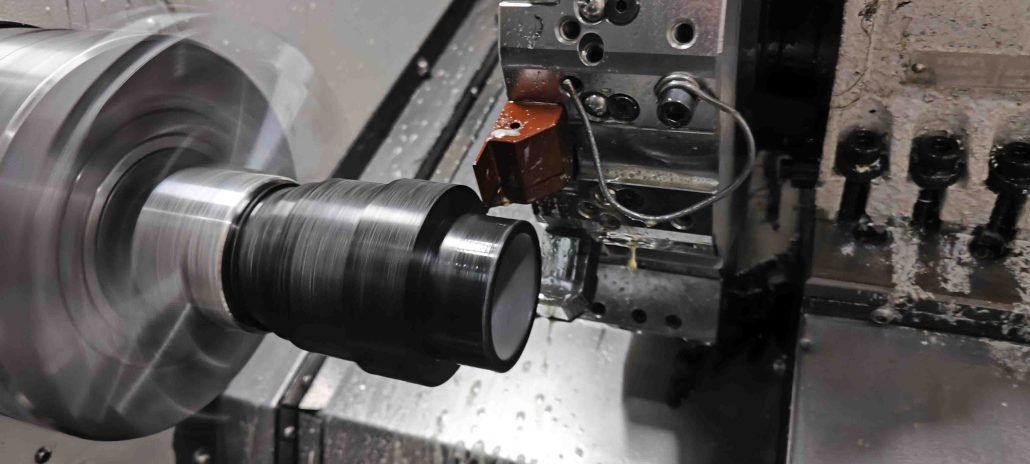
Difference Between CNC Milling and Electrochemical Machining
Manufacturing is a complex process that involves various techniques to shape and form materials into a desired product. CNC milling and electrochemical machining (ECM) are two different methods of material removal in manufacturing. Both processes are used to create complex shapes and features on metal parts, but they use different techniques to achieve this.
The main difference between CNC milling and ECM is the way they remove material from the workpiece. CNC milling uses a cutting tool to remove material, while ECM uses an electrical current to remove material. CNC milling is often used to create parts with high precision and accuracy, while ECM is often used to create complex shapes and features that are difficult to machine using traditional methods. CNC milling is also faster than ECM, but ECM can be used on more materials, including materials that are difficult to machine using traditional methods.
CNC milling is a versatile and reliable process that is widely used in manufacturing. It is ideal for producing parts with high precision and accuracy, and can be used on a wide range of materials. However, it is not suitable for creating complex shapes and features that require intricate designs.
ECM, on the other hand, is a highly specialized process that is ideal for creating complex shapes and features that are difficult to machine using traditional methods. It is also highly efficient and can be used on a wide range of materials. However, it is not suitable for producing parts with high precision and accuracy.
In summary, both CNC milling and ECM are important manufacturing processes that are used to create complex shapes and features on metal parts. However, they use different techniques to achieve this, and each process has its own advantages and disadvantages. CNC milling is often used for high precision and accuracy, while ECM is often used for creating complex shapes and features that are difficult to machine using traditional methods.
What are the Advantages of CNC Milling Compared to Electrochemical Machining?
CNC milling and electrochemical machining are two popular manufacturing techniques used in the production of precision parts. While both methods offer their unique benefits, CNC milling has several advantages over electrochemical machining.
Precision and Accuracy
CNC milling has a high level of accuracy and precision, which allows for the production of complex and intricate parts. Electrochemical machining, on the other hand, is limited in terms of the complexity of the parts it can produce.
Material Compatibility
CNC milling is compatible with a wide range of materials, including metals, plastics, and composites. Electrochemical machining, however, is limited to conductive materials, which restricts its use when working with non-conductive materials.
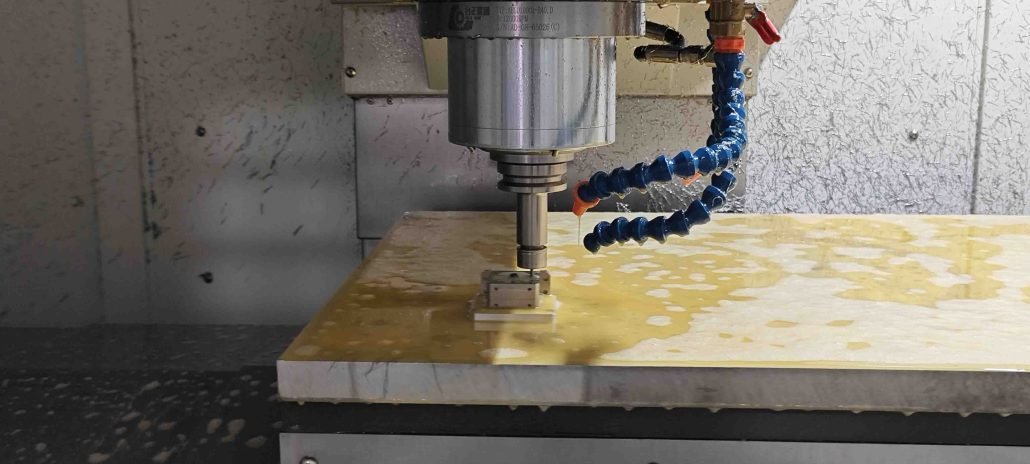
Surface Finish
CNC milling produces a smooth and uniform surface finish, which is ideal for parts that require a high level of precision and accuracy. Electrochemical machining, on the other hand, can produce rougher surfaces, which may require additional finishing operations.
Cost and Time Savings
CNC milling is a faster and more cost-effective process compared to electrochemical machining. CNC milling machines can produce parts at a faster rate, which reduces the overall production time. Additionally, CNC milling parts can be automated, which further reduces labor costs.
Overall, CNC milling offers several advantages over electrochemical machining, including precision, material compatibility, surface finish, and cost and time savings. However, the choice between the two manufacturing techniques ultimately depends on the specific requirements of the part being produced.
What are the Advantages of Electrochemical Machining Compared to CNC Milling?
Electrochemical machining (ECM) and computer numerical control (CNC) milling are two popular industrial processes that are used for cutting and shaping metals. While both processes are effective in their own ways, ECM has several advantages over CNC milling.
1. No Thermal Damage
ECM is a non-thermal process that uses electrical energy to remove metal from the workpiece. This means that there is no thermal damage to the workpiece, which can occur in CNC milling due to the high temperatures generated by the cutting tool. In CNC milling, the high temperature generated by the cutting tool can cause the metal to expand, leading to deformation and changes in the material properties, such as hardness, strength, and ductility. This can result in reduced product quality and performance. However, with ECM, since there is no thermal damage, the material properties remain unchanged, leading to superior quality and performance.
2. No Tool Wear
ECM does not use a cutting tool, which means that there is no tool wear. This is in contrast to CNC milling, where the cutting tool wears out over time and needs to be replaced. Tool wear in CNC milling can result in reduced accuracy, surface finish, and dimensional stability, leading to increased production costs and lower product quality. However, with ECM, since there is no tool wear, the accuracy, surface finish, and dimensional stability remain consistent over time, resulting in higher productivity and better product quality.
3. High Precision
ECM is capable of achieving high levels of precision, which makes it ideal for applications that require tight tolerances. CNC milling can also achieve high precision, but it is generally not as precise as ECM. This is because ECM uses a cathode tool that is shaped like the desired workpiece, which means that the final product is an exact replica of the tool. In contrast, CNC milling uses a cutting tool that is larger than the desired workpiece, which can result in errors due to tool deflection, vibration, and thermal expansion. These errors can be minimized through the use of advanced machine tools and techniques, but they cannot be completely eliminated.
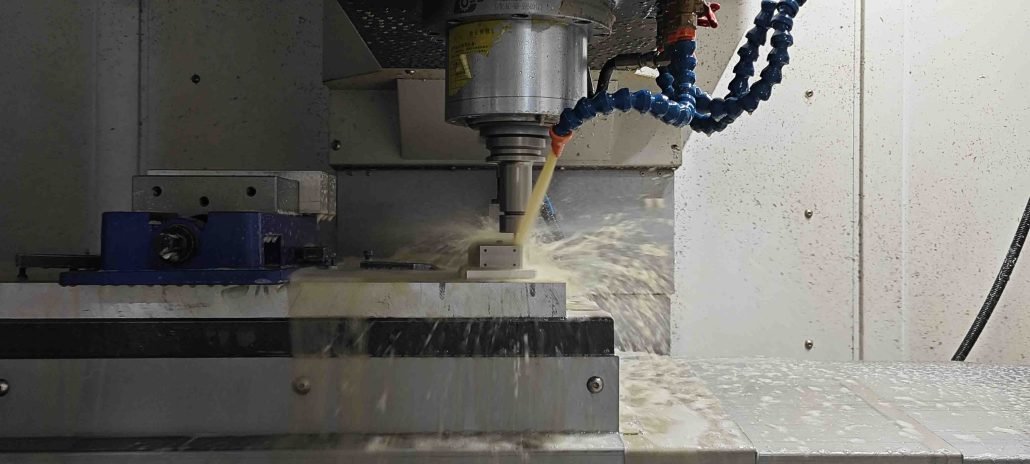
4. No Burr Formation
ECM produces no burrs, which are small, unwanted pieces of metal that can be left behind by CNC milling. Burrs can cause problems in downstream processes, such as assembly, painting, and coating, as they can interfere with the fit and finish of the product, leading to increased rework and scrap. However, with ECM, since there is no burr formation, the downstream processes are smoother and more efficient, resulting in higher throughput and lower costs.
5. Versatility
ECM is a versatile process that can be used to machine a wide range of metals, including those that are difficult to machine with CNC milling. This is because ECM is a non-contact process that does not generate heat or mechanical stress, which means that it can be used to machine materials that are sensitive to these factors, such as titanium, nickel alloys, and hardened steels. In contrast, CNC milling is limited by the physical properties of the cutting tool, which means that it can only be used to machine materials that are compatible with the tool.
Overall, the advantages of ECM make it a popular choice for many industrial applications. While CNC milling is still widely used, ECM offers several advantages that make it a more attractive option in certain situations. As such, it is important for manufacturers to evaluate their machining requirements and select the process that best meets their needs.
FAQ
CNC milling is faster than ECM. However, the speed of the process is dependent on several factors, including the size and complexity of the part, the material being used, and the desired level of precision.
CNC milling can be used on a wide range of materials, including metals, plastics, and composites. ECM can also be used on a wide range of materials, including metals, ceramics, and composites. The choice of material will depend on the specific requirements of the part being produced and the capabilities of the machine being used.
CNC milling is a subtractive manufacturing process that uses computer-controlled machines to remove material from a workpiece. The process involves a cutting tool that rotates at high speeds and removes material from the workpiece to create a desired shape. The cutting tool can move in three or more axes to create complex shapes and features. CNC milling is often used to create parts with high precision and accuracy, and it can be used on a wide range of materials, including metals, plastics, and composites.
Electrochemical machining (ECM) is a non-traditional machining process that uses electrolysis to remove material from a workpiece. In ECM, a conductive tool is used to remove material from the workpiece by applying an electrical current. The tool and workpiece are submerged in an electrolyte solution, which conducts electricity and helps to remove the material. ECM is often used to create complex shapes and features that are difficult to machine using traditional methods. ECM can be used on a wide range of materials, including metals, ceramics, and composites.