If you are interested in the manufacturing industry or have a product that requires plastic components, then you are probably familiar with injection molding. Injection molding is a process of producing plastic parts by injecting molten plastic material into a mold. This technology has been around for a long time, and it is continuously evolving towards a more automated, efficient, and cost-effective process.
In this article, we will discuss some of the trends and innovations that we can expect to see in the future of injection molding. But before we dive deeper into the subject, let’s understand what injection molding is and how it works.
What is Injection Molding?
What is Injection Molding?Injection molding is a manufacturing process used to produce a wide range of plastic parts for various industries. This process involves melting plastic pellets into a liquid state, injecting mold cavities, and then cooling the molten plastic under pressure to form a solid part. The process requires a mold, which is usually made of steel or aluminum, and a machine equipped with an injection unit, a clamping unit, and a control system.
Injection molding is prevalent in the production of consumer goods, such as toys, electronics, food containers, automotive parts, and medical devices. The process offers many advantages over traditional manufacturing methods, such as high production rates, low scrap rates, and high repeatability. Injection molding also allows for the production of complex parts with intricate geometries, which would be impossible to produce using other methods.
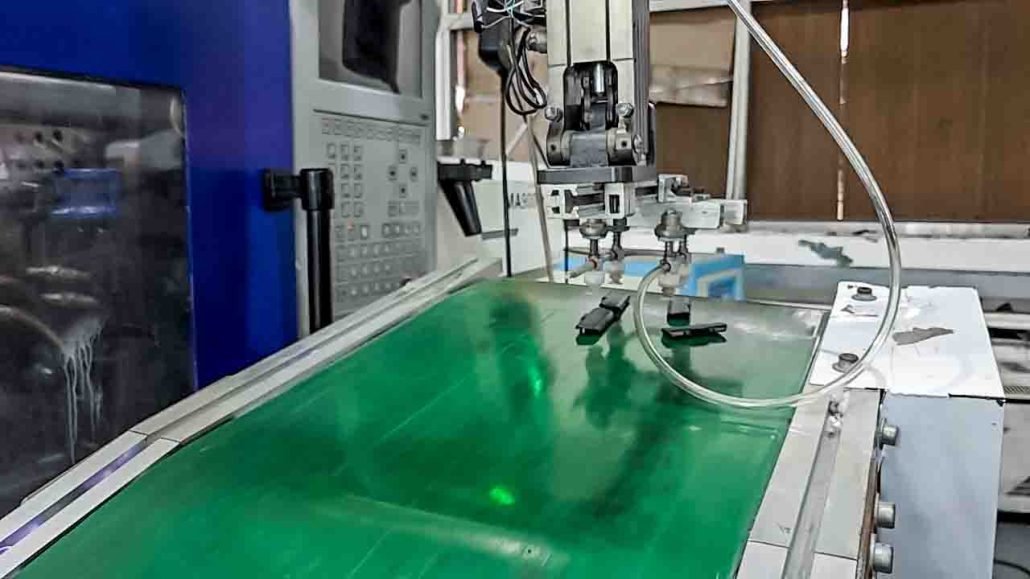
Trends in Injection Molding
Automation
The trend towards automation in injection molding is growing as manufacturers seek higher efficiency, productivity, and precision. Automation can significantly reduce the number of defects, minimize labor costs, and increase the speed of production. The latest generation of injection molding machines is equipped with advanced control systems, sensors, and robotics that can perform most of the process steps automatically.
Sustainability
Sustainability is becoming an essential concern for consumers and manufacturers alike. Many injection molding companies are exploring ways to reduce their environmental impact by using recycled materials, reducing waste, and minimizing energy consumption. Biodegradable plastics are also gaining popularity as a sustainable alternative to traditional non-biodegradable plastics.
Customization
The demand for custom injection molding services is increasing as consumers seek unique products tailored to their specific needs and preferences. The latest technologies in injection molding allow manufacturers to produce customized parts with high precision and efficiency. The process can be adapted to produce parts of various shapes, sizes, colors, and materials, making it an ideal solution for producing complex, customized parts.
Innovations in Injection Molding
3D printing
3D printing technology is making significant strides in injection molding, especially when it comes to producing molds. With 3D printing technology, manufacturers can produce complex injection molding designs in a fraction of the time it would take using traditional methods. 3D printing also allows for the creation of bespoke molds that would be difficult or impossible to produce using conventional techniques.
In-mold labeling
In-mold labeling is a process whereby a graphic label is placed inside the injection mold before the plastic is injected. This process ensures that the label becomes a permanent part of the product, eliminating the need for separate labeling operations. In-mold labeling is a cost-effective solution, especially for high-volume production of products such as food containers and consumer goods.
Micro-injection molding
Micro-injection molding is a specialized technique that allows manufacturers to produce miniature parts with complex geometries. This technology has revolutionized the medical device industry, enabling the production of smaller, more intricate medical devices that are less invasive and more comfortable for patients. Micro-injection molding is also useful in producing small, intricate parts for electronics and consumer goods.
The Importance of Custom Injection Molding Services
Custom injection molding services are becoming more popular as companies seek to create products that are unique and tailored to their specific needs. With custom injection molding, companies can produce complex parts that may not be possible with other manufacturing methods. The ability to create customized parts means that companies can differentiate themselves from their competitors and create products that cater to their customer’s needs.
Conclusion
The future of injection molding looks bright, with endless innovation and possibilities. The industry’s shift towards sustainability, automation, and advanced technology is opening up opportunities for manufacturers to produce high-quality, cost-effective products. As the demand for custom injection molding services grows, so too does the need for highly-specialized and skilled professionals in the field.
At [Longsheng Technology], we offer professional custom injection molding service with a focus on quality, efficiency, and customer satisfaction. Contact us today to learn more about how we can help you achieve your product goals.
Mobile:+86 185 6675 9667(Gloria Wu)
E-Mail:gloria.wu@longshengmfg.com