Are you looking for an all-encompassing guide to the knowledge of injection molding? Look no further than this comprehensive article! As a professional in the field, I have personally refined my knowledge and expertise over many years, and am excited to share it with you.
Injection molding refers to the process of melting a material—usually plastic—and injecting it into a mold to create a specific shape or size. This process has become increasingly popular due to its cost-effectiveness, efficiency, and flexibility. In fact, many of the products we use and interact with on a daily basis are made using injection molding, from water bottle caps to car parts. This guide will provide an in-depth explanation of the injection molding process, from start to finish.
Through various sections, this guide will cover the following topics:
Introduction to Injection Molding
Injection molding is a manufacturing process used to produce parts by injecting molten material into a mold. This technology has been around for decades and has revolutionized the way we make plastic products.
The History of Injection Molding
In The Beginning
The first injection molding machine was patented in 1872 by John Wesley Hyatt, who used it to create objects from celluloid. The patent was obtained in 1872. As small as it was by today’s standards, it was quickly adopted by the nascent plastic industry, which made plastic combs, buttons, and a variety of other items.
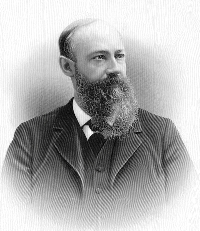
world war II
There was no doubt that World War Two had a profound effect on human history. The war manufacturing industry in the United States expanded dramatically during World War II, trigerring dramatic advances in automotive technology as well as the development of the post-war industrial revolution in the United States. Plastics were also in high demand during this period due to their low cost and mass production.
After World War II
By the year 1946, American inventor James Watson Hendry constructed the world’s first screw injection machine known as the extrusion screw injection machine. Hendry was able to improve the injection process itself with the help of a rotating screw. By doing so, the quality of the products could be drastically improved.
Hendry has also introduced the first gas-assisted injection molding process, which is a big step forward for manufacturing hollow, long products. In the 1970s, the plastic industry had made significant progress and had overtaken that of steel due to the use of materials with increased strength and decreasing weight. In the 1990s, aluminum molds became a popular manufacturing trend because they are a faster and cheaper alternative to steel molds at a similar price point.
The name Hendry is synonymous with manufacturing history. The plastic injection molding industry would NOT be as advanced today without his inventions.
In Modern Times
After World War II, the material shortages that resulted from the war influenced the desire for this product. There were also disruptions in the rubber production industry as a result of wars across Asia and attacks on the shipping lanes. War applications such as tanks as well as other types of military machinery created a large demand for the metal.
As a result, plastic-filled that void, providing an affordable alternative to metal. Plastic injection molding gained popularity along with the popularity of plastics. The efficiency, affordability, and large-scale manufacturing capabilities of this technology have contributed to its effectiveness in this era.
It was during the post-war period that plastics became very popular. In the early part of the 20th century, business leaders learned that plastics offered a lot of cost advantages over competing materials, resulting in a radical re-evaluation of global supply chains, which led to the widespread use of plastics in the economy and manufacturing processes.
The Injection Molding Process
Injection molding is the process of using the thermophysical properties of plastics to add materials from the hopper into the barrel, which is heated by the heating ring outside the barrel to melt the materials.
The material is gradually plasticized, melted, and homogenized by the dual action of external heating and screw shearing.
When the screw rotates, the material is pushed to the head of the screw under the action of the friction and shear force of the screw groove, which has been molten. At the same time, the screw recedes under the counteraction of the material, so that the screw head forms a storage space to complete the plasticizing process.
Then, the screw injects the molten material in the storage space into the mold cavities through the nozzle at high speed and high pressure under the action of the piston thrust of the injection cylinder.
After the molten material in the cavity is pressurized, cooled, and cured, the mold is opened under the action of the mold closing mechanism, and the shaped product is ejected from the mold by the ejector device.

Here’s a step-by-step breakdown of the injection molding process:
- Mold Preparation: The mold is prepared by coating it with a release agent and preheating it to the desired temperature.
- Material Preparation: The raw material (usually in the form of pellets or powder) is loaded into the injection molding machine and melted.
- Injection: The melted material is injected into the mold cavity under high pressure.
- Cooling and Solidification: The material cools and solidifies inside the mold cavity, taking on the shape of the mold.
- Ejection: The finished product is ejected from the mold by opening the mold and using ejector pins.
Injection molding cycle
The sequence of events during the injection mould of a plastic part is called the injection moulding cycle. The cycle begins when the mould closes, followed by the injection of the polymer into the mould cavity. Once the cavity is filled, a holding pressure is maintained to compensate for material shrinkage. In the next step, the screw turns, feeding the next shot to the front screw. This causes the screw to retract as the next shot is prepared. Once the part is sufficiently cool, the mold opens and the part is ejected.
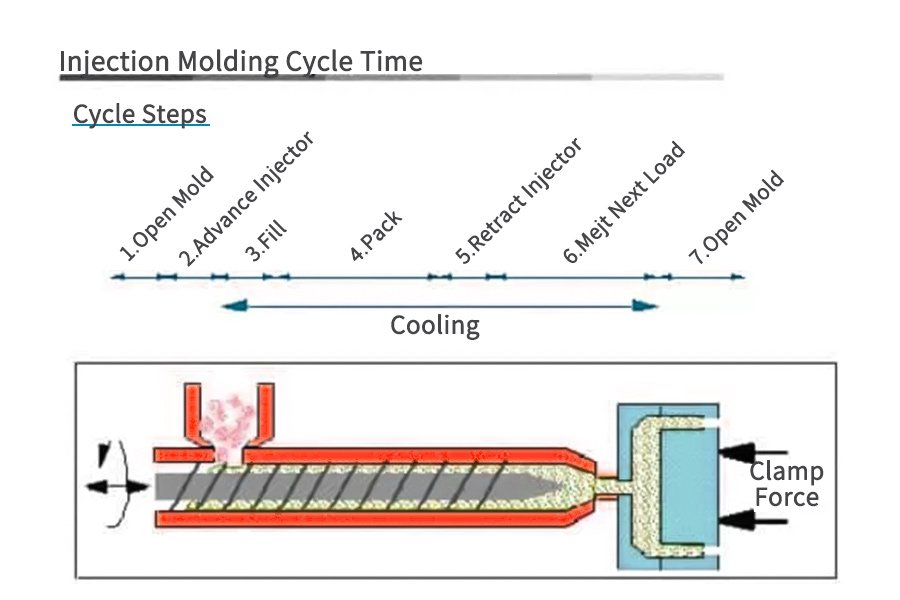
The cooling time, which is largely driven by the square of the maximal wall thickness, usually dominates in the cycle time,can be approximated as follows:
𝑡𝑐=ℎ²max÷π²𝛼 (log4(𝑇𝑖−𝑇𝑚)-logeπ(𝑇𝑥−𝑇𝑚))
where
hmax = maximum wall thickness of part, mm
Tx = recommended part ejection temperature, °C
Tm = recommended mold temperature, °C
Ti = polymer injection temperature, °C
α = thermal diffusivity coefficient, mm2/s
power requirements
The power required for this process of injection moulding depends on many things and varies between materials used. Manufacturing Processes Reference Guide states that the power requirements depend on “a material’s specific gravity, melting point, thermal conductivity, part size, and molding rate.” Below is a table from page 243 of the same reference as previously mentioned that best illustrates the characteristics relevant to the power required for the most commonly used materials.
Material | Specific gravity | Melting point(°F) | Melting point(°C) |
---|---|---|---|
Epoxy | 1.12 to 1.24 | 248 | 120 |
Phenolic | 1.34 to 1.95 | 248 | 120 |
Nylon | 1.01 to 1.15 | 381 to 509 | 194 to 265 |
Polyethylene | 0.91 to 0.965 | 230 to 243 | 110 to 117 |
Polystyrene | 1.04 to 1.07 | 338 | 170 |
pressure requirement
The tonnage ranges from less than 10 tons to 6000 tons for injection molding machines. A tonnage is the power that the machine is able to exert to keep the core and cavity of the mold closed as it is being molded. The clamp force required for a given part depends on its projected area.
Types of Injection Molding Machines
There are several different types of injection molding machines, each with its own unique features and advantages. Here are some of the most common types:

Hydraulic Injection Molding Machines | Electric Injection Molding Machines | Hybrid Injection Molding Machines |
---|---|---|
All Hydraulic Injection Molding Machines is the only type of plastic injeciton molding machine before 1980s. until the year of 1983, a Japanese company introduced the first all-electric injection molding machine in the world. | Electric Injection Molding Machines is available in the 1980s and quickly became popular in high precision plastic parts manufacturing industry. The full electric servo drive injection molding machine`s positioning accuracy is extremely high (of ± 0.0001 in) in nowadays but with very expensive price. | Hybrid Injection Molding Machines combines hydraulics and electric motor drives into a single variable-power AC drive power source that operates on-demand. It have both benefits of two types of injeciton moulding machines: Electric Injection Molding Machines and Hybrid Injection Molding Machines. |
Advantages of Hydraulic Injection Machines: | Advantages of Electric Injection Machines | Advantages of Hybrid Injection Machines |
Lower initial price: The base price of these machines are significantly less than its alternatives. | Energy efficiency: Electric injection molding machines only use energy when in action—meaning the motor output is only equal to that of the load requirements. | Diversity: the possible combinations for hybrid injection molding machines open up new degrees of design flexibility. |
Cheaper parts: If a part on the machine needs to be replaced due to damage or the parts life-span reached its limit, the replacement parts are lower cost and easier to find. | Less-down time: There is no chance of leakage from oil. Also, no oil use means no filters to be replaced, which means consumable expenses are less. | Best of both: Hybrid molding machines combine the energy savings and accuracy of electric molders with the force-generating capacity of a hydraulic unit. |
Stronger parts: The hydraulic parts of the machine are more resistant to wear and tear—they are built to last. | Faster process: These machines are digitally controlled, meaning the process is entirely repeatable and needing no supervision. | Less downtime: These require less maintenance and experience less downtime than an all-hydraulic or all-electric molding machines. |
Power: Hydraulic molding machines have exceptional clamping force. | Clean operation: Since there is no use of oil for this machine, it is safe for use if you are manufacturing medical and food packing parts. Typically, these parts should be created in a clean-room area. | Price point: Falls nicely between all-hydraulic and all-electric molding machines, making it an affordable option. Especially for medical device manufacturers. |
Choosing the Right Machine
When choosing an injection molding machine, there are several factors to consider. These include:
Production Volume: If you have a high production volume, a hydraulic machine may be the best choice. However, if you have a lower production volume, an electric or hybrid machine may be more cost-effective.
Part Size and Complexity: If you need to produce large or complex parts, a hydraulic machine may be better suited to your needs. However, if you need to produce small or simple parts, an electric or hybrid machine may be more precise and efficient.
Material Type: Different materials require different processing conditions. Make sure the machine you choose can handle the type of resin you are using.
Choosing the right injection molding machine is essential to the success of your manufacturing operation. By understanding the different types of machines available and considering your production needs, part complexity, and material type, you can select the machine that will best meet your needs. Whether you choose a hydraulic, electric, or hybrid machine, remember that quality, reliability, and efficiency are essential to your success. With the right injection molding machine, you can produce high-quality parts and products and take your business to the next level.
Injection Molding Materials
As the field of plastic injection molding grows and evolves, so too does the variety of materials available for this process. Choosing the right material for your injection molding project can mean the difference between success and failure, so it’s important to know your options and select based on your unique needs.we’ll explore common injection molding materials and what makes them ideal for specific applications.

Polypropylene (PP) | One of the most common materials used in injection molding, polypropylene is a thermoplastic polymer that offers high strength, low density, and excellent resistance to fatigue. Its inertness to moisture, acid and alkalis, organic solvents, and most common chemicals make it an ideal choice for a wide range of applications, including packaging, automotive parts, medical devices, and consumer goods. |
Acrylonitrile Butadiene Styrene (ABS) | ABS is a versatile thermoplastic that blends the strength and rigidity of acrylonitrile and styrene with the toughness and flexibility of butadiene rubber. This material is commonly used for injection molding in the automotive, electronics, and consumer goods industries due to its high impact resistance, heat resistance, and ability to be easily modified with colorants or additives. |
Polycarbonate (PC) | Another popular choice for injection molding, polycarbonate is a thermoplastic polymer with exceptional impact strength, dimensional stability, and optical clarity. Its resistance to heat, chemicals, and UV radiation make it a popular choice for products that require durability, such as safety glasses, electronic components, and automotive parts. |
Nylon (Polyamide) | Nylon is a synthetic polymer that is known for its exceptional strength and toughness, as well as its resistance to abrasion and fatigue. It is commonly used in injection molding for applications such as gears, bearings, and other mechanical parts, and it also has a high melting point, which makes it well-suited for high-temperature applications. |
Polyethylene (PE) | Polyethylene is a highly versatile thermoplastic that is used in a wide range of industries, including packaging, construction, and medical devices. This material is known for its flexibility, durability, and chemical resistance, and it can be easily modified with additives to enhance its properties even further. |
Choosing the Right Material
When selecting a material for injection molding, it’s important to consider your specific needs and requirements. Ask yourself questions like: What type of product am I creating? What are the environmental conditions it will be exposed to? What level of strength or heat resistance is required? By understanding the properties and strengths of each material, you can make an informed decision that will lead to a successful outcome for your project.

Injection molding materials have come a long way in recent years, providing a wide range of options for manufacturers. From polypropylene to nylon, each material has unique properties and benefits, and selecting the right material can make all the difference in the success of your product. By taking the time to understand your options and asking the right questions, you can confidently choose the best material for your injection molding project.
Common Injection Molding Defects
Are you experiencing defects in your injection molding works process? If so, you’re not alone. It’s a common problem that can cost your company time and money.
Here are some common injection molding defects with its descriptions and causes.

Moulding defects | Descriptions | Causes |
---|---|---|
Burn marks | Black or brown burnt areas on the part located at furthest points from gate or where air is trapped | Tool lacks venting, injection speed is too high. |
Flash | Excess material in thin layer exceeding normal part geometry | Mould is over packed or parting line on the tool is damaged, too much injection speed/material injected, clamping force too low. |
Flow lines | Directionally “off tone” wavy lines or patterns | Injection speeds too slow (the plastic has cooled down too much during injection) |
Jetting | Jetting is a snake-like stream which occurs when polymer melt is pushed at a high velocity through restrictive areas. | Poor tool design, gate position or runner. Injection speed set too high. |
Weld lines | Small lines on the backside of core pins or windows in parts that look like just lines. | Caused by the melt-front flowing around an object standing proud in a plastic part as well as at the end of fill where the melt-front comes together again. |
Sink marks | Localised depression (In thicker zones) | Holding time/pressure too low, cooling time too short. |
Short shot | Partial part | Lack of material, injection speed or pressure too low, mould too cold, lack of gas vents. |
Weld line | Discoloured line where two flow fronts meet | Mould or material temperatures set too low (the material is cold when they meet, so they don’t bond). |
Warping | Distorted part | Cooling is too short, material is too hot, lack of cooling around the tool, incorrect water temperatures. |
Injection Molding Maintenance
As the title suggests, injection molding maintenance is an essential part of ensuring your equipment runs smoothly and efficiently. Neglecting to maintain your injection molding machinery can lead to expensive repairs and unscheduled downtime, both of which can have a significant impact on your bottom line. In this article, we’ll discuss the importance of injection molding maintenance and provide you with some tips on how to keep your equipment running smoothly.
Why Injection Molding Maintenance is Important
Injection molding maintenance is important for a number of reasons. Here are just a few:
Maximizes productivity: Regular maintenance ensures that your injection molding equipment runs smoothly and efficiently, which maximizes your productivity and minimizes downtime.
Improves machine lifespan: Proper maintenance can extend the lifespan of your equipment, saving you money in the long run.
Ensures safety: Regular maintenance can identify potential safety hazards before they become a problem, keeping your workers safe and your equipment in compliance with safety regulations.
Reduces costs: Scheduled maintenance is less expensive than unscheduled repairs or replacement of equipment due to lack of maintenance.
Tips for Injection Molding Maintenance
- Now that we’ve established the importance of injection molding maintenance, here are some tips for keeping your equipment running smoothly:
- Regular Inspections: Conduct regular inspections of the equipment, identify areas that need maintenance and repair before they become a problem.
- Lubrication: Lubrication is an important part of injection molding maintenance. Ensure that all moving parts are well-lubricated to prevent wear and tear and improve efficiency.
- Replace Worn Parts: Replace worn parts before they fail. It will help to prevent downtime, improve quality and make the machine last longer.
- Keep the Machine Clean: Keeping your equipment clean can prevent build up of dust and debris. This can block ventilation systems, cause electrical faults and reduce the performance of the machine.
- Ensure Temperature Control is Optimal: Ensure the temperature control settings are adjusted for the material and the mold being used.
- Train Employees: Be sure to train your employees on proper maintenance, so that they can identify and address issues before they become problems.

In conclusion, injection molding maintenance is a vital part of the equipment life cycle that is often overlooked. By regularly maintaining your injection molding machinery, you can keep it running smoothly, efficiently, safely and be productive. If you’re looking for tips on how to keep your equipment running smoothly, these are the best practices to follow.
Benefits and Drawbacks to Injection Molding
Injection molding is a widely used manufacturing process in which molten plastic is injected into a mold to form a specific shape. This process is used to create a wide range of products such as toys, car parts, and medical equipment. While injection molding has many benefits, it also has some drawbacks that manufacturers should be aware of. In this article, we will take a closer look at the benefits and drawbacks of injection molding.
Benefits | Drawbacks | ||
---|---|---|---|
High Precision | This process creates products with tight tolerances and intricate injection mlding designs that would be impossible to achieve with other manufacturing methods. | High Initial Tooling Cost | The initial cost of tooling can be high, especially for complex products. This cost can take a significant amount of time to recover, causing delays and financial strain. |
High Volume Production | The production process is highly automated, giving manufacturers the ability to create thousands of products in a short amount of time. | Limited Design Flexibility | Injection molding is limited in terms of design flexibility. The mold is fixed, so any changes to the product design will require a new mold. |
Low Cost | The initial tooling cost can be high, but the cost of production is relatively low. The raw materials used in injection molding are also affordable. | Long Lead Times | Injection molding has a long lead time, from tooling design to production. This process can take several weeks to months, depending on the complexity of the product. |
Wide Range of Materials | Injection molding can use a wide range of materials, including thermoplastics, elastomers, and thermosets. This process can create products that are strong, flexible, and durable. | Material Restrictions | Injection molding has restrictions on the types of materials that can be used. Some materials are not suitable for injection molding due to their viscosity, chemical composition, or melting point. |
Minimal Waste | Injection molding creates minimal waste since the excess plastic can be reused. This process is environmentally friendly and reduces the cost of production. | Quality Control | Injection molding requires strict Quality Control measures to ensure that the products meet the required specifications. Any defects could result in wasted time, money, and materials. |
Advanced injection Molding Techniques
Advanced Injection Molding Techniques: Innovations in Manufacturing
Injection molding is a well-established manufacturing process that has transformed the modern industry. It is widely used to produce a range of products from medical devices to automotive parts among other applications. The process involves the melting and shaping of plastic or other materials to create a desired shape. However, the injection molding process has undergone major advancements over the years to enhance production, reduce cycle time, and improve overall product quality. In this article, we will explore the latest advanced injection molding techniques and how they have transformed manufacturing worldwide.
The following are some of the leading techniques in advanced injection molding.
1.Gas-Assist Injection Molding
Gas-assist injection molding (GAIM) is a technique that uses nitrogen to help mold the plastic part with hollow spaces inside. The use of gas keeps the cavity in the plastic part separate and prevents deformation during cooling. This technique is used for hollow parts that require uniform thickness like automotive parts, furniture, and toys. The process reduces warpage and sink marks, thus improving the overall cosmetic appearance of the part.
2.In-Mold Labeling
In-mold labeling (IML) is a process of nesting a pre-printed label inside the mold before the injection process. The label becomes a part of the product as it is molded simultaneously. The technique is commonly used for food containers, packaging, and thin-wall products. In-mold labeling eliminates the cost of post-production labeling, reduces packaging weight, and improves the products’ shelf life.
3.Rapid Heat and Cool Molding
Rapid heat and cool molding is a technique used to improve the cycle time of products. The technique uses an advanced heating and cooling system to melt and solidify the plastic in a shorter time. The process eliminates the need for cooling and heating stations, thus reducing the time needed for manufacturing. The product quality also improves as the process enhances the physical properties of the material, making it stronger and more resistant to wear and tear.
4.Co-Injection Molding
Co-injection molding is a process that uses two or more materials to create a single component. The technique creates a core layer and a cladding layer that is molded simultaneously. Co-injection molding is widely used for products that require multiple layers such as toothbrush handles, medical devices, and electrical connectors. The process reduces the need for post-production assembly, eliminates delamination issues, and improves the product’s appearance and strength.
Advanced injection molding techniques have revolutionized the manufacturing industry by providing more efficient and cost-effective ways of producing high-quality products. Gas-assist injection molding ensures uniformity in thickness, in-mold labeling eliminates post-production labeling, rapid heat and cool molding reduces cycle time while improving product quality, and co-injection molding reduces the need for post-production assembly. These techniques are just a few examples of how advanced injection molding techniques have made modern manufacturing more productive, cost-effective, and efficient. If you’re looking to improve your product’s quality or reduce production costs, consider incorporating advanced injection molding techniques into your manufacturing processes.
To learn more about the advanced injection molding techniques and how they can benefit your business, please feel free to reach out to our team. We are always here to help you stay up to date with the latest innovations in manufacturing.
fAQs
What is injection molding?
Plastic injection molding is a cyclical manufacturing process that allows for cost-efficient production of a mass number of identical parts made from either thermoplastic or thermoset materials.
How to Improve Consistency in Injection Molding?
Cushion values in injection molding ultimately are an indication of a part’s quality, especially its dimensions. A consistent cushion will create consistent part dimensions.
How to Get Rid of Bubbles in Injection Molding?
It is important to determine which type of bubble your part has, and what the root cause might be. Determining bubble type will allow you to pinpoint the source and determine your next course of action to eliminate the problem.
How can I improve my injection molding quality and productivity?
Most molders are still relying on “general-purpose” screw designs that go back 30 years. With all of the technical improvements that have been made on machines over that time, nothing has been done to improve melt uniformity. We still use “general-purpose” (GP) screws, which well-known screw designer Bob Dray wisely has called “no-purpose” screws. That is they do not melt plastic uniformly. Processing with a uniformly melted plastic would seem like a high priority, but it has seen little if any attention.
resource
https://en.wikipedia.org/wiki/Injection_moulding
https://4spepublications.onlinelibrary.wiley.com/doi/abs/10.1002/pen.760271802