Injection molding is a complex process in which numerous variables need to be monitored and controlled. One such variable is cavity pressure, which plays a critical role in ensuring that injection molded parts are defect-free and meet the desired quality standards.
In this article, we’ll discuss how to calculate cavity pressure in custom injection molding and explain why it’s important. We’ll also provide tips on how to optimize cavity pressure for better part quality and reduced risk of defects.
Understanding Cavity Pressure in Injection Molding
Cavity pressure refers to the pressure exerted by molten plastic on the walls of the mold cavity during injection molding. It’s a critical variable that influences several aspects of the injection molding process, including melt flow, part filling, and the level of packing pressure required to produce a defect-free part.
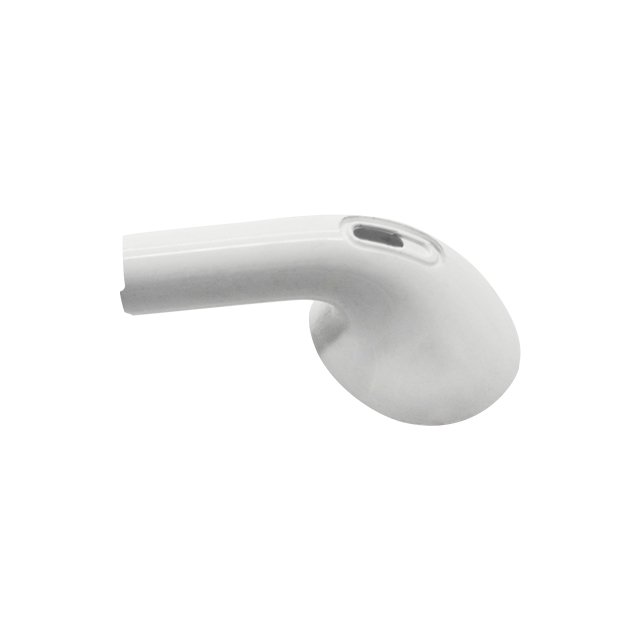
Measuring Cavity Pressure
Cavity pressure can be measured using a cavity pressure sensor, which is installed directly into the mold cavity. The sensor transmits real-time pressure readings to the injection molding machine, which can use the information to adjust various aspects of the process, such as filling time and packing pressure.
Calculating Cavity Pressure
The calculation of cavity pressure involves some critical details and equations. First, you need to consider the injection speed, the temperature of the molten plastic, and the mold cavity’s geometry.
In calculating cavity pressure, it’s essential to take into account various factors that may affect the pressure exerted on the mold cavity. These factors include:
Injection speed: the speed at which the molten plastic is injected into the mold cavity
Melt viscosity: the thickness of the molten plastic
Mold temperature: the temperature of the mold cavity
Wall thickness: the thickness of the part walls
Part geometry: the shape and complexity of the part
To calculate cavity pressure, you’ll need to use a formula that takes these factors into account. The formula for calculating cavity pressure is:
P = (K x Q) / A
Where:
P = cavity pressure
K = cavity pressure coefficient (typically between 0.9 and 1.3)
Q = volumetric flow rate of the molten plastic
A = part wall area

Optimizing Cavity Pressure
Optimizing cavity pressure can help improve part quality and reduce the risk of defects, such as warping, sink marks, and voids. Here are some tips for optimizing cavity pressure:
Monitor cavity pressure in real-time using a cavity pressure sensor
Adjust injection speed and molding parameters to ensure that cavity pressure stays within the desired range
Use a packing profile to ensure that the part is packed uniformly and with the correct amount of pressure
Optimize part design to reduce the risk of defect-causing factors, such as wall thickness variation and complex geometry
Factors affecting cavity pressure
Several factors can affect the cavity pressure during injection molding, including:
Material properties: The viscosity, flow rate, and temperature of the molten material affect its behavior during injection and can change the cavity pressure.
Mold design: The geometry, size, and venting of the mold cavity can influence the flow of the resin and the resulting pressure.
Process parameters: The injection speed, hold pressure, and cooling time can affect the filling and packing stages of the process and impact the cavity pressure.
Machine performance: The machine’s hydraulic system, screw speed, and control accuracy can affect the injection pressure and its consistency.
Importance of Cavity Pressure Calculation
Cavity pressure calculation is crucial because it helps predict the filling behavior of the mold cavity. By calculating the cavity pressure, you can identify potential defects, including sink marks, voids, and flash. This information can help you optimize the injection molding process to produce high-quality products with minimal defects, ensuring that your customers receive top-notch products.
Conclusion
Cavity pressure is a critical variable in the injection molding process, and it’s essential to monitor and control it to ensure that parts are defect-free and meet quality standards. By understanding how to calculate cavity pressure and optimizing it, injection molders can produce high-quality parts consistently and efficiently.
We hope this article has provided you with a comprehensive understanding of cavity pressure in injection molding and how to optimize it. If you have any questions or would like to learn more, don’t hesitate to contact us.