If you’re working in the manufacturing industry, you might already be familiar with injection molding. Injection molding is a popular manufacturing technique that uses a molten material, typically plastic, to create a unique product. But have you ever wondered how the mold, which shapes the material, is made? In this comprehensive guide, we’ll take a closer look at how molds for custom injection molding are made, from start to finish.
Step 1: Designing the Mold
The first step in creating an injection mold is designing it. Typically, this involves drafting a 3D model of the desired product and making necessary adjustments to create a mold that reflects the design. The mold must be able to withstand high temperatures and pressure during injection molding, so designers might use specialized software to ensure that the mold is structurally sound.
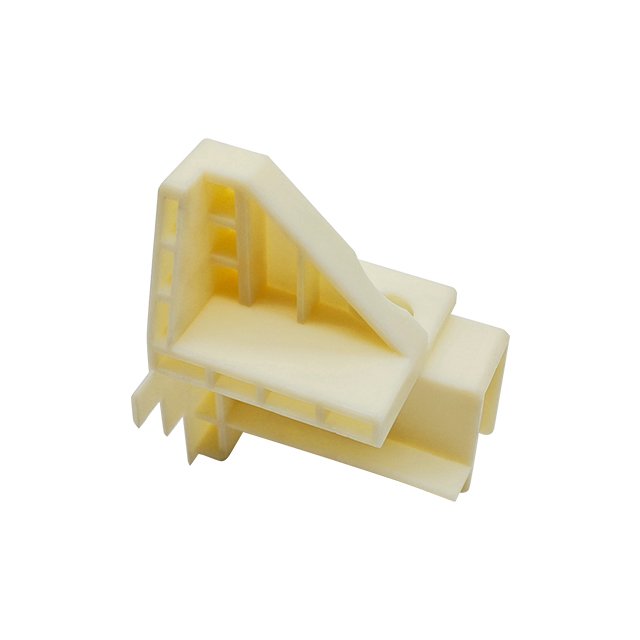
Step 2: Creating the Mold
Once a design has been approved, the next step is creating the mold. Molds for injection molding are typically made from steel or aluminum, as these materials can withstand the high pressure of the process. There are different techniques for creating molds, but some common methods include:
CNC Machining: This involves using specialized machines to carve the mold out of a steel or aluminum block.
EDM Machining: This technique uses an electrical current to create the mold shape by “burning” the material away.
3D Printing: Some manufacturers are using 3D printing to create molds, which can speed up the process and reduce costs.
Step 3: Polishing and Finishing the Mold
Once the mold has been created, it undergoes a series of finishing processes to ensure that it’s polished and smooth. It’s important to note that any imperfections or roughness on the mold surface can impact the quality of the final product. Some common finishing processes include:
Sandblasting: This involves using small particles to blast away any rough spots on the mold’s surface.
Polishing: The mold is polished to a high shine, which helps to prevent any imperfections from occurring on the final product.
Texturing: The mold’s surface might be textured to create unique patterns or finishes on the final product.
Step 4: Quality Control
Before the mold can be used in injection molding, it undergoes a series of quality control checks. This might include verifying that the mold is the correct size and shape, and that the surface finish meets the desired standard. If there are any issues, the mold might need to undergo further polishing or finishing processes.
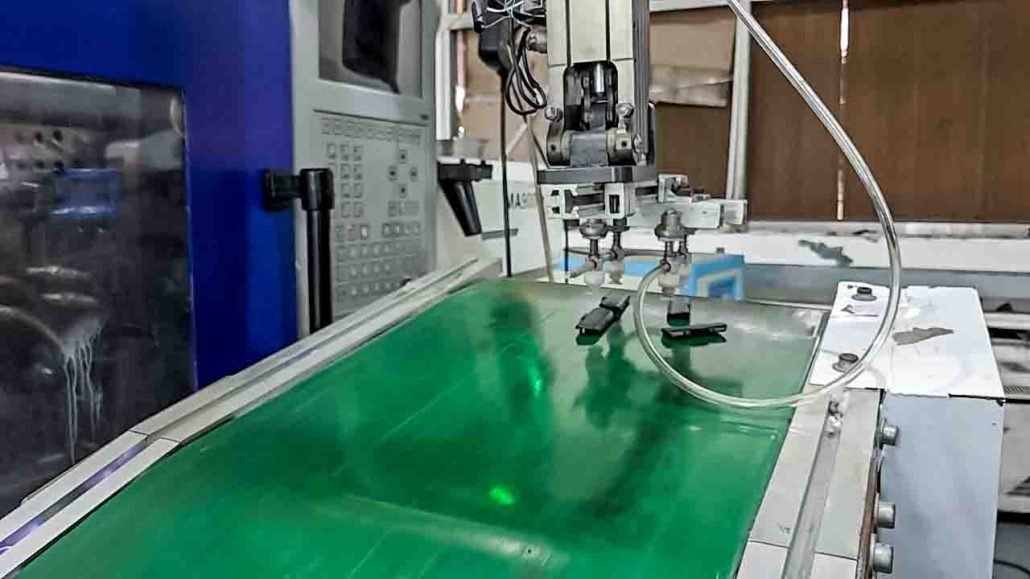
Step 5: Injection Molding
Finally, the mold can be used for injection molding. During this process, the molten material is injected into the mold under high pressure, creating the final product. The mold is typically cooled, and the final product is removed from the mold.
Materials Used to Make Molds for Injection Molding
The process of making injection molds involves several materials, including:
Steel: Steel is commonly used to make molds because of its strength, durability, and thermal conductivity. It can be used for both hot and cold injection molding processes.
Aluminum: Aluminum is widely used to make molds for low-volume productions. Its high thermal conductivity reduces cooling time, thus making it suitable for producing parts that require rapid cooling.
Copper: Copper is another popular choice for making molds in the injection molding process due to its high thermal conductivity, corrosion resistance, and durability.
Hardened and Ground Tool steel: Hardened and ground tool steel is generally used to create the core and cavity inserts, which are the most critical components of the mold.
Mold Making Techniques
Several techniques are used to make molds for the injection molding process, some of which include:
CNC Machining: CNC machining is a common technique used to make molds. It produces molds with high precision and accuracy, making it suitable for manufacturing complex parts.
EDM: EDM (Electrical Discharge Machining) involves burning or eroding the material using an electric spark, creating a mold cavity through the process.
Additive Manufacturing: Additive manufacturing involves printing the mold using a 3D printer, making it possible to create intricate mold designs.
Molds for injection molding are a critical part of product manufacturing, and creating them requires knowledge, expertise, and attention to detail. From designing and creating the mold to finishing and quality control, every step is important in ensuring a quality product. Whether you’re a manufacturer or just curious about the injection molding process, we hope this guide has provided valuable insights into how molds for injection molding are made.