Are you looking for a way to achieve consistent quality in your injection molding process? One of the essential parameters that you should consider is cavity pressure. The cavity pressure helps you to determine the quality of the molded parts, identify defects, and optimize the process.
Calculating cavity pressure may seem daunting, but with the right tools and knowledge, you can do it easily. In this guide, we’ll take you through the basics and provide practical tips on how to calculate cavity pressure in injection molding.
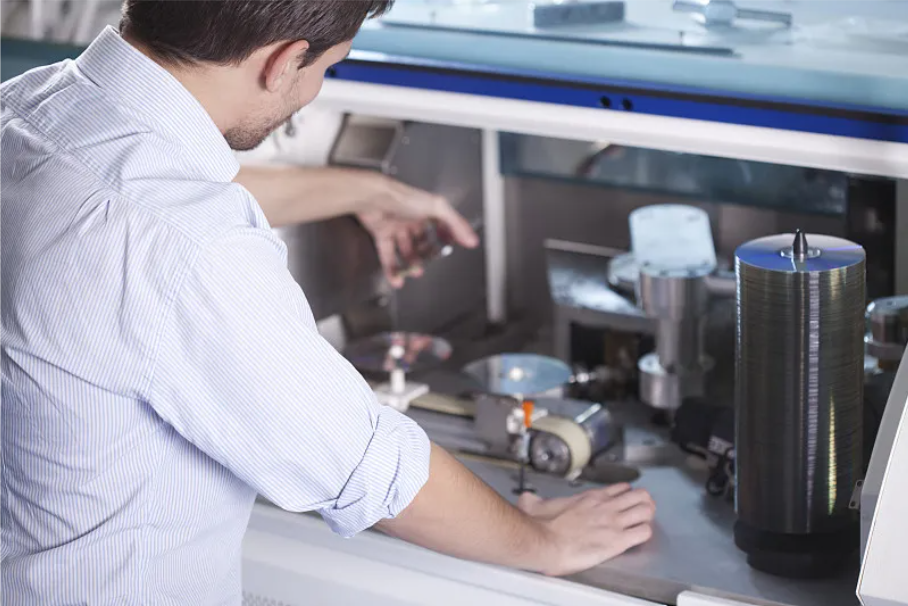
Understanding the Basics of Cavity Pressure
Cavity pressure is the pressure exerted on the mold cavity by the melted plastic during the injection molding process. The pressure changes as the plastic fills the cavity and cools down, and it can provide valuable insights into the process.
To measure cavity pressure, you need a pressure sensor that is installed on the mold. The sensor should be calibrated and positioned in the right location, depending on the part design and mold layout.
Why Cavity Pressure Matters
Cavity pressure refers to the pressure of molten plastic inside the mold cavity during injection molding. It’s a crucial parameter that determines the quality of the finished product. Here are some reasons why cavity pressure matters:
- Determines Part Quality: Cavity pressure affects the surface finish, dimensional accuracy, and mechanical properties of the molded parts. Low or high cavity pressure can result in defects such as voids, sink marks, warpage, and flash.
- Prevents Mold Damage: Excessive cavity pressure can damage the mold by causing cracks, deformation, or wear. It can also lead to plastic leakage, which can compromise the safety and efficiency of the injection molding process.
- Optimizes Process Control: Cavity pressure monitoring and analysis helps in identifying process inconsistencies, optimizing cycle times, and minimizing scrap rates. It also enables the injection molding process to meet the specific requirements of the end-user, such as environmental suitability, chemical compatibility, and mechanical strength.
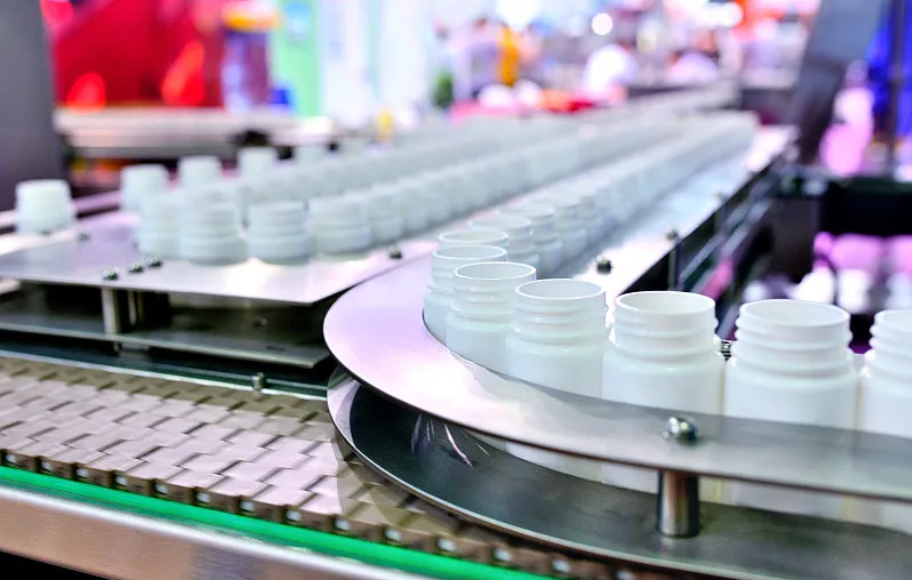
How to Calculate Cavity Pressure in Injection Molding
Calculating cavity pressure in injection molding involves several steps, which include setting up the injection molding machine, installing the cavity pressure sensor, collecting data, and analyzing the results. Here’s a detailed guide on how to calculate cavity pressure in injection molding:
Step 1: Set up the Injection Molding Machine
Before you can start monitoring cavity pressure, you need to ensure that the injection molding machine is set up correctly. This involves calibrating the machine, adjusting the injection speed, temperature, and pressure settings, and preparing the mold for production.
Step 2: Install the Cavity Pressure Sensor
To monitor cavity pressure accurately, you need to install a cavity pressure sensor on the mold cavity. The sensor consists of a pressure transducer, a signal amplifier, and a data acquisition system. The sensor should be mounted close to the cavity to minimize measurement errors.
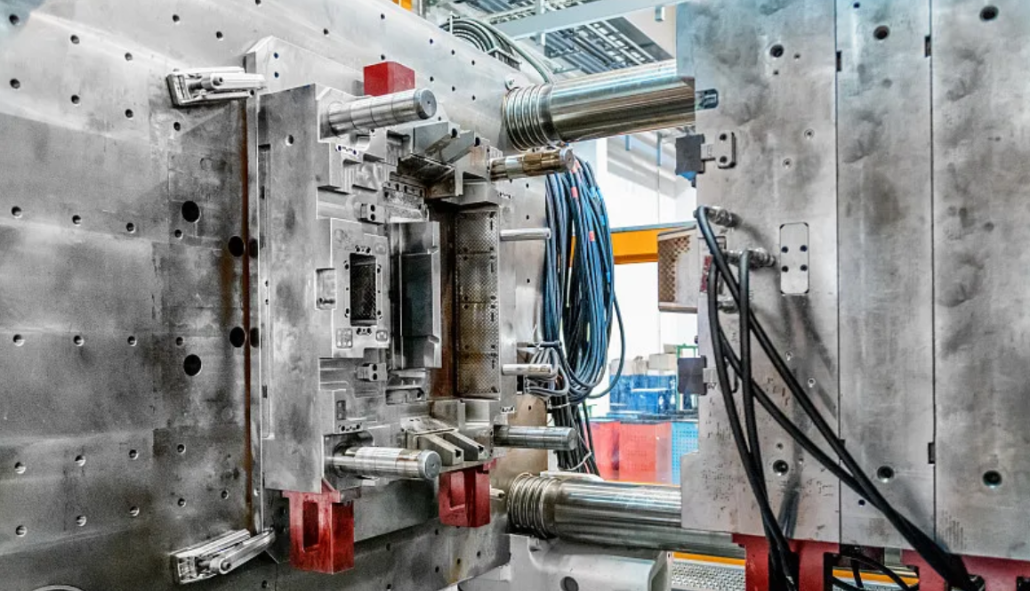
Step 3: Collect Data
Once you’ve installed the sensor, you can start collecting data on cavity pressure during the injection molding process. The data collection process should include monitoring the pressure-time curve, the pressure holding phase, and the cooling phase.
Step 4: Analyze the Results
Once you’ve collected the data, you can analyze it to determine the cavity pressure profile, the peak pressure, and the holding pressure. You can then use this information to optimize the injection molding process, prevent defects, and ensure product quality.
In conclusion, calculating cavity pressure in injection molding is a crucial process that determines the quality, consistency, and durability of the molded parts. With the right tools and techniques, you can optimize the injection molding process, prevent defects, and ensure product quality.
At Longsheng Technology Company, we offer a wide range of injection molding services that ensure optimal quality for your plastic products. Contact us today to learn more about our services and how we can help you achieve your manufacturing goals.
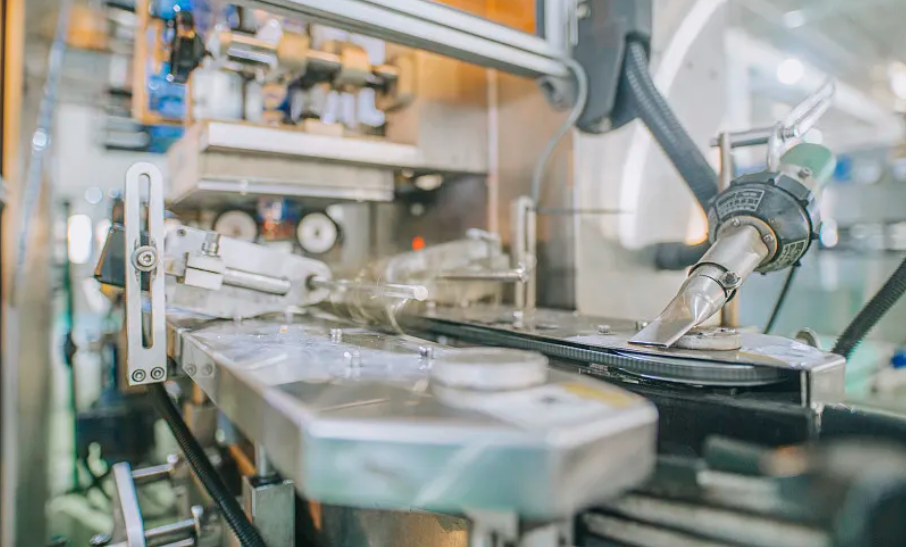
Interpreting Cavity Pressure Data
Once you have the cavity pressure data, you need to interpret it to identify any process deviations or defects. Here are some of the common signs that you should look for:
- Low cavity pressure may indicate insufficient packing or underfilling.
- High cavity pressure may indicate overpacking or flash.
- Variation in cavity pressure may indicate part distortion or warpage.
By analyzing the cavity pressure data and correlating it with other process data, you can optimize the process and improve the part quality.
Cavity pressure is a critical parameter in injection molding that can help you achieve consistent quality and optimize the process. By understanding the basics of cavity pressure, calculating and interpreting the data, you can identify defects and process deviations and make data-driven decisions.
We hope this guide has been informative and persuasive enough to convince you to start monitoring the cavity pressure in your injection molding process. Contact us at longsheng for more tips and tools to improve your injection molding process.