When it comes to CNC machining, scratches on the surface of a part are a common issue that can cause significant problems, from cosmetic imperfections to performance issues. However, with the right techniques and expertise, it is possible to minimize scratches and achieve high-quality results.
In this comprehensive guide, we will provide you with a deep understanding of the causes of scratches on CNC machined parts and explore some of the most effective techniques for addressing this issue. By following our expert tips and tricks, you can reduce or eliminate scratches on your CNC parts and achieve superior results every time.
Understanding the Causes of Scratches in CNC Machining
Scratches on CNC machined parts can result from numerous factors, including improper tool selection, improper cutting parameters, and machine instability. The severity and extent of the scratches will depend on factors such as the quality of the cutting tool, the type of material, and the machining process.
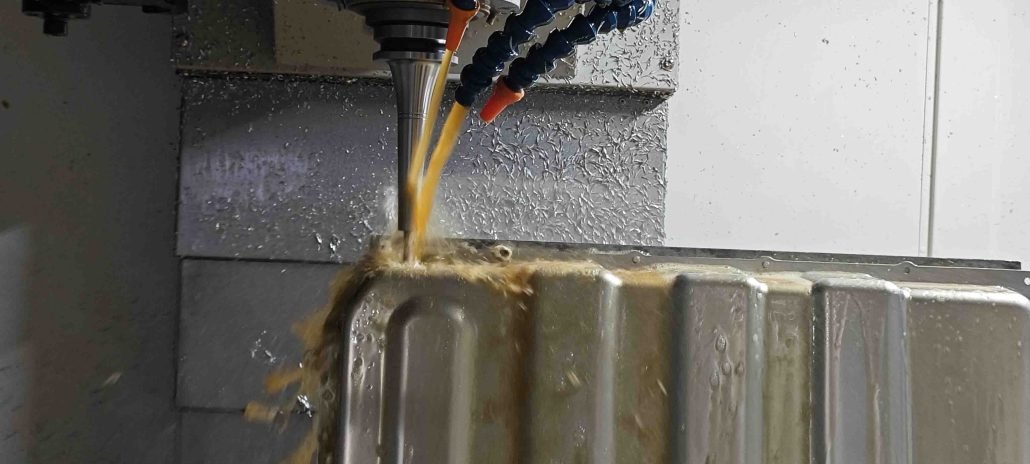
Here are some common causes of scratches in CNC machining:
- Poor tool selection: Choosing the wrong cutting tool for a specific material can lead to scratches and rough surfaces. It is essential to use the right tool and ensure that it is in good condition.
- Incorrect cutting parameters: The wrong cutting parameters such as feed, speed, depth of cut, and coolant can lead to scratches and damage the tool.
- Machine instability: Mechanical issues in the CNC machine, such as loose bearings or improper alignment, can cause vibrations, leading to scratches on the machined surface.
- Material-related issues: Some materials, such as plastics, can have surface defects, which can result in scratches during machining.
- Chip clogging: When chips accumulate on the cutting edge, they can cause scratches as they get dragged over the machined surface.
Expert Tips and Tricks for Reducing Scratches
Now that you have a better understanding of the causes of scratches let’s explore some of the best techniques and tips for minimizing them.
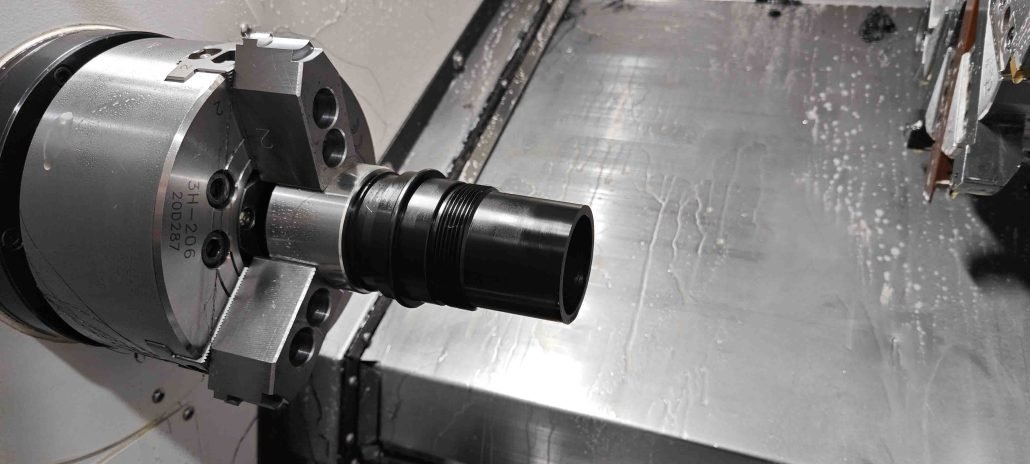
- Use a high-quality cutting tool: Always use cutting tools designed for the specific material you are machining. Ensure that it is sharp and in good condition.
- Optimize cutting parameters: Adjust the cutting parameters according to the material being machined, the cutting tool, and the CNC machine’s capabilities. This includes factors such as speed, feed rate, depth of cut, and coolant/lubrication.
- Check machine stability: Maintain your CNC machine to avoid any vibration, especially if you are machining thin materials. You should also ensure machine leveling to avoid machine imbalance.
- Reduce chip clogging: Keep chips clear from the cutting edge by using compressed air or coolant.
- Improve chip evacuation: Introduce chip guards or evacuate them using a vacuum to prevent chips from getting dragged over the machined surface.
- Use deburring tools: Deburring should be done with a soft abrasive such as a deburring tool to avoid scratching the machined surface.
Final Thoughts
Scratches on CNC machined parts are not only unsightly but can be a sign of deeper issues affecting your production process. By following the tips we have shared in this blog post, you can reduce or eliminate scratches and improve the quality of your CNC machined parts. Remember, the key to success lies in careful consideration of the causes of scratches, optimizing cutting parameters, careful inspection, and maintenance of the cutting tool. By mastering these techniques, you can produce consistently flawless CNC machined parts for your unique requirements.