As an important component of the production process, injection molding plays a crucial role in modern manufacturing. However, with the intensification of market competition, manufacturers are beginning to think about how to improve product quality while reducing their production costs. Many people are questioning whether injection molding, a production process, is cost-effective.
In this article, we’ll explore the key drivers of injection molding costs and explain why this Injection molding process is one of the most cost-effective options available and explore the advantages and disadvantages of injection molding, and whether it is worth using injection molding to produce your product.
What is Injection Molding?
Before we dive into the economics of injection molding, let’s first define what it is. custom Injection molding is a manufacturing process in which molten plastic or metal is injected into a mold cavity. Once the material cools and solidifies, the mold is opened, and the part is ejected. Injection molding has several advantages over other manufacturing processes, including high production rates, consistency, and the ability to create complex shapes.

Why Use Injection Molding?
Injection molding offers many advantages over other manufacturing processes. Some of these benefits include:
1.High production speed
Injection molding is a highly automated process that can produce hundreds of thousands of molded parts in a matter of hours.
2.Consistency
The molding process ensures that each part produced is identical, ensuring consistent quality across the production line.
3.Cost-effectiveness
Injection molding is a cost-effective solution, especially when producing large quantities of parts, as the initial setup costs can be amortized over the production run.
4.Design flexibility
The mold used for injection molding can be customized to produce parts of various shapes and sizes. Additionally, inserts can be added to create additional features on the parts.
5.Material selection
Injection molding can use a wide range of materials, including polymers, metals, and ceramics.
The Benefits of Injection Molding
There are many benefits to using injection molding, including:
1.High Efficiency
Injection molding is a highly efficient process that can produce large quantities of products quickly and reliably. This makes it ideal for mass production, reducing lead times and increasing productivity.
2.Cost-Effective
Injection molding is a cost-effective process that can help businesses save money in the long run. The cost per part decreases as the quantity increases, making it a cost-efficient solution for both large and small orders.
3.Design Flexibility
Injection molding allows for a high level of design flexibility. Designs can be customized to meet specific requirements, and complex shapes can be produced with ease. This makes it an ideal solution for creating unique products that stand out from the competition.
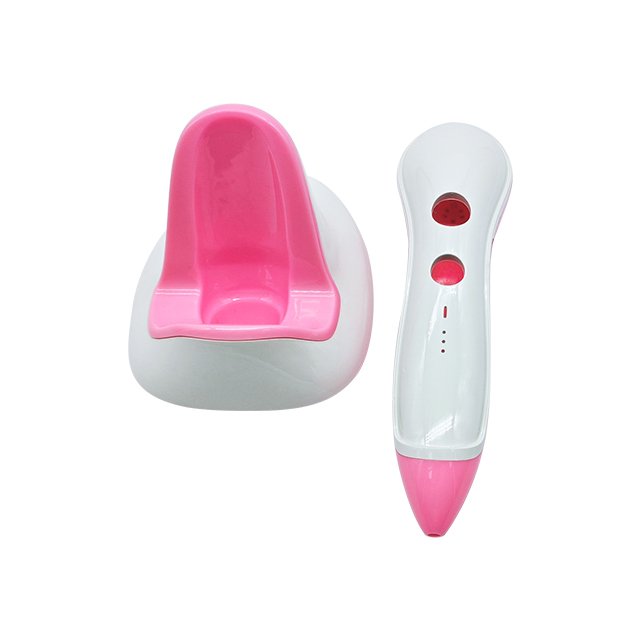
4.High-Quality Products
Injection molding is capable of producing high-quality products that meet strict industry standards. The process produces consistent, high-quality parts that are free of defects and inconsistencies.
5.Environmentally-Friendly
Injection molding is an environmentally-friendly process. The waste generated from the process can be recycled and reused, reducing the amount of waste that ends up in landfills.
Disadvantages of injection molding
The following are some drawbacks of injection molding:
1.High cost
Although injection molding has the advantage of high automation, the cost of control equipment and molds for this process is relatively high. During mass production, the cost of purchasing and maintaining equipment and molds may greatly affect production costs.
2.Difficulty in forming small-scale production
Due to the special properties of injection molding, this process is difficult to apply to small-scale production. Therefore, if small quantities of products need to be produced, the benefits of using injection molding may not be significant enough.
3.Long cycle
The manufacturing process of injection molding requires a long time to complete, as it requires multiple stages such as mold preparation, injection molding, and cooling. For some urgent orders, the injection molding cycle may not be suitable.
The Key Drivers of Injection Molding Costs
Now that we understand injection molding, let’s consider what drives its costs. The cost of injection molding is typically determined by four main factors:
1.Material Cost
Depending on the type of material used, the cost of materials can vary significantly. High-grade engineering polymers might be more expensive, while low-grade polymers are less costly.
2.Mold Cost
The molds used in injection molding are a significant cost factor, especially when producing complex parts. The more complicated the mold design, the more expensive it is to produce.
3.Tooling And Setup Costs
The initial tooling and setup costs can also be a barrier for smaller production runs. However, these costs can be amortized over longer production runs, reducing the overall per-part cost.
4.Design And Engineering Costs
injection molding design and engineering costs increase with the complexity of the product. Additionally, post-production processes such as finishing, assembly, and packaging can incur additional costs.
How to Optimize Injection Molding Costs
While injection molding is a cost-efficient manufacturing process, it’s important to optimize the process to ensure the best results. Here are some tips to help optimize injection molding costs:
1.Design for Manufacturability
Design products that are optimized for injection molding. Simple designs are easier and quicker to produce, reducing production costs.
2.Material Selection
Choose the right material for your product. Different materials have different properties that can affect the final product cost. Consult with your injection molding supplier to determine the most suitable material for your product.
3.Volume
Consider the volume of products you need to manufacture. Higher volumes typically result in lower production costs per part.
4.Tooling
Optimize the tooling process to reduce costs. By streamlining the tooling process, businesses can produce more parts in less time, resulting in a more cost-efficient process overall.

How Injection Molding Is More Cost-Efficient than Other Manufacturing Processes
While the initial capital investment to acquire and set up injection molding equipment may be quite substantial, the cost per unit decreases as the production volume increases. Therefore, the higher the volume of production, the more cost-effective injection molding becomes. Additionally, injection molding’s ability to produce complex parts with high consistency and fewer defects means that it produces less waste than other manufacturing processes. This waste reduction directly translates to cost savings.
Injection Molding: The Most Cost-Effective Manufacturing Option
In conclusion, injection molding is one of the most cost-effective manufacturing processes available. While initial costs can be high, the process becomes more cost-effective the higher the production volume, making it an ideal option for large-scale production. Its ability to produce consistent, high-quality parts with minimal waste further reduces costs and makes it the go-to option for many types of manufacturing.
Whether you’re a large-scale manufacturer or a small business owner, you should consider injection molding as an option if you’re looking to produce high-quality parts at a low cost. The initial investment may be daunting, but the long-term cost savings make it worth considering. So, is injection molding cost-efficient? The answer is a resounding yes!
I hope the above content can provide some assistance for your injection molding production
Author: Longsheng Technology