As a sheet metal fabrication factory, one of the most important aspects of your work is sheet metal product design. This process involves not only creating products that are visually appealing but also ensuring that they are durable and functional. To achieve this, there are several principles that you should consider in your sheet metal product design. In this article, we will discuss those principles and provide you with a comprehensive guide to help you create high-quality sheet metal products.
Material Selection: Start with the Right Base
The selection of a base material for sheet metal products is critical. Factors like formability, strength, corrosion resistance, and more must all be considered. Aluminum, steel, and brass are frequently used in sheet metal manufacturing, but the selection depends on the product’s required properties and dimensions.

Some of the key factors to consider when selecting a base material for sheet metal design are its workability, the availability of raw materials, and its suitability for the intended use. A competent CNC machining manufacturer can help you determine the best base metal for your product.
You want to choose a material that is durable, cost-effective, and appropriate for the intended use of the product. Some common materials used in sheet metal product design include:
- Stainless Steel
- Aluminum
- Copper
- Brass
Each of these materials has its unique properties and benefits. For example, Stainless Steel is durable and has excellent corrosion resistance, making it ideal for outdoor and marine applications. On the other hand, aluminum is lightweight and has excellent thermal conductivity, making it suitable for electronics products.
Design for Manufacturing (DFM)
Design for manufacture (DFM) is a critical principle to consider in sheet metal product design. DFM considerations result in a product that is easier and more cost-effective to manufacture. A thoroughly designed product will reduce the number of production errors while lowering production costs, improving the overall efficiency of your manufacturing process.
The aim of DFM is to optimize the design so that it can be assembled and manufactured quickly and accurately. One important element to consider is the geometry of the product, including the number of bends, the angles, and the radius of each bend. Overly complex designs will cause delays and additional costs in the manufacturing process. Therefore, simplicity and functionality must be prioritized over aesthetics.
By considering DFM in your sheet metal design, you can reduce the manufacturing cost, improve the quality, and shorten the production time. Some DFM principles that you should consider include:
- Designing for Sheet Metal
- Standardizing Components
- Minimizing Parts
- Simplifying Assembly
Tolerances and Surface Finish
In sheet metal product design, tolerances and surface finishing are essential aspects to consider to ensure that the product meets the required specifications. Tolerance refers to the allowable deviation from the desired dimensions, while surface finish refers to the quality of the surface. Some common tolerances and surface finish considerations include:
- Flatness
- Parallelism
- Surface Roughness
- Surface Coating
Sheet Metal Bending
Sheet metal bending is a process that involves creating a bend in a sheet of metal to form a particular shape or angle. Proper sheet metal bending is an essential aspect of sheet metal product design, as it affects both the product’s strength and appearance. Some factors to consider when bending sheet metal include:
- Material Thickness
- Bend Angle
- Bend Radius
- Tool Selection
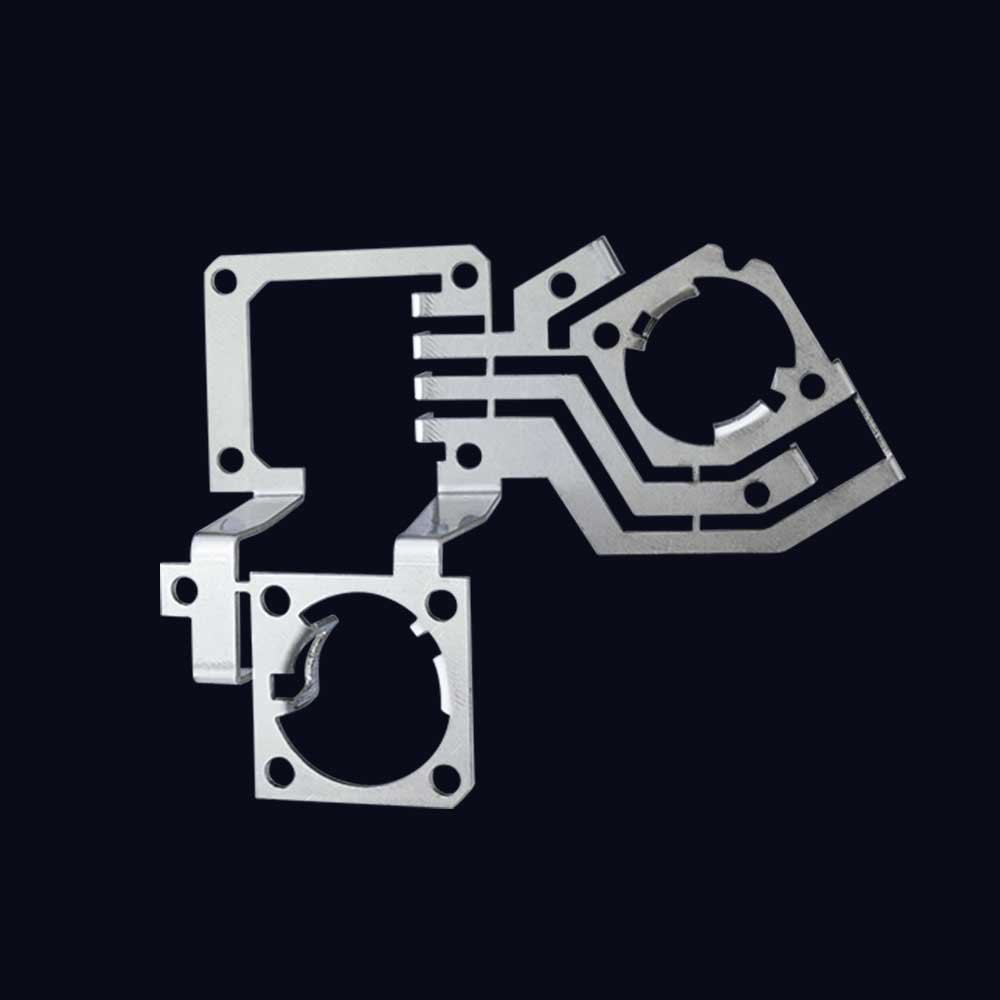
Assembly Method
The assembly method you choose for your sheet metal product design is crucial. You want to select an assembly method that is both cost-effective and functional, while also ensuring that it is easy to disassemble for maintenance or repair. Some common assembly methods include:
- Welding
- Riveting
- Screws
- Adhesives
Design for Assembly (DFA): Simplify Your Product
Design for assembly is another significant principle to consider when designing sheet metal products. A well-thought-out assembly design ensures that the product can be assembled efficiently and expediently. A sheet metal product’s assembly must be simple enough even to be done by a novice worker, thereby ensuring that assembly is error-free and efficient.
The number and size of fasteners, the number of screws necessary for assembly, and the types of assembly methods used should all be considered in this design. A product designed with assembly in mind will save time and money, thus giving your company a competitive edge.
Cost Optimization: Balance Quality with Affordability
Cost optimization is one of the most important factors when it comes to sheet metal product design. A good design should balance the quality of the end product with the manufacturing costs. A product that is durable and has a longer lifespan may be more expensive to manufacture, thus making it less competitive.
The balance point between cost and quality must be carefully considered, with the end goal of creating a product that performs well while being affordable.
Conclusion
Sheet metal product design is a precise and creative process that requires expert knowledge and attention to detail. The concepts of DFM, DFA, material selection, and cost optimization are critical principles that must be considered during the design stage. Each of these principles could make a big difference to the product’s efficiency, quality, and affordability.
We hope this article has been helpful, and we encourage you to consider these principles to create high-quality sheet metal products that meet your customer’s satisfaction. Remember that every product has different requirements, and working with a professional CNC machining manufacturer like us could make all the difference in your final product design.