Plastic injection molding is a popular manufacturing process that is used to create plastic products of varying complexities and shapes. However, one of the biggest challenges faced by this process is the high cost of mold making. The mold cost of plastic injection parts can be one of the most significant expenses associated with the process.
Mold making is a critical aspect of the injection molding process, and it can be costly due to the complex and intricate design requirements of many parts. However, there are ways to reduce the cost of mold making, which can ultimately reduce the overall cost of plastic injection parts production. In this post, we’ll explore some of the best ways to reduce mold cost for plastic injection parts.

What is the cost of injection molding?
While the initial cost of injection molding may seem higher compared to processes such as CNC machining and 3D printing. It is only when the number of parts is scaled up to thousands that it becomes a cost-effective solution. The most important factor determining the cost of injection molding is the time it takes to produce the mold, which means that the more complex the geometry of the part, the higher the cost of manufacturing. After the analysis of 16 million + parts manufacturing experience of Longsheng, it is found that no simple parts without bottom cutting or complex surface treatment are the most affordable.
In addition to unit cost, there are materials to consider. Many plastics overlap in strength and function, but some are easier to shape themselves, reducing the cost of parts. When you send the drawings to Sujia, our engineers will provide suggestions on process optimization according to the final use of the product, to help you quickly determine the product prototype.
Here are 10 design considerations for injection molding that can help you save on manufacturing costs:
- Eliminate bottom cuts
- Remove unnecessary functions
- Use the core cavity method
- Reduce finish and appearance
- Design self-fitting parts
- Modify and reuse the mold
- Pay attention to DFM analysis
- Use multiple molds – cavity or home molds
- Select the Production on Demand option
- Consider part size
Methods to reduce the cost of injection molded parts
Bottom cut
The bottom cut feature makes it difficult or even prevents the part from popping. If you can, it’s best not to, but maybe that’s not possible, for example, if you need a side action, slide off or take out. An alternative may be to use sliding globe valves and through cores, or to simplify die manufacturing by changing parting lines and drawing angles. This can avoid the addition of additional parts in the mold, and reduce the mold manufacturing cost. In addition to increased manufacturing costs using manual inserts, longer cycle times and manual tooling operations may also have an impact on the price of your parts.
Unnecessary function
Textured surfaces, molded part numbers, and company logos look cool, but these non-critical features cost extra to complete. That said, permanent part numbers are a requirement for many aerospace and military applications. Use a font suitable for factory use, such as CenturyGothicBold, Arial, or Verdana (san-serif font), and keep it at least 20 pounds deep and no deeper than 0.25mm to 0.38mm. In addition, if you are concerned about the part demoulding, please be prepared to increase the drawing die.
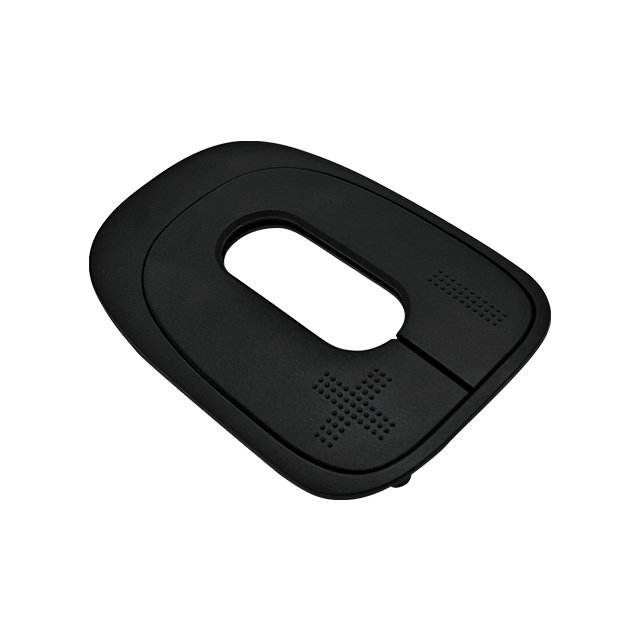
Core cavity
If you need an electronic case or similar box-shaped part, you can sink the wall cavity into the bottom of the mold, work the ribs into the mold using long, thin tools, or work the aluminum material down around the core and shape it around the part. The latter method, known as the core cavity, is a more cost effective molding method. Better yet, this method makes it easier to provide a smooth surface finish, adequate ventilation, improved pop-ups, and eliminates the need for ultra-steep draw angles.
Surface treatment
Good looking parts often require sandblasting, EDM, or advanced die finishes, which undoubtedly add to the cost. Any injection molded parts with a finish greater than PM-F0 (e.g. machined) will require a secondary finish, such as polishing to SPI-A2 mirror finish using a 2-stage diamond polishing wheel. Avoid such fine finishes unless necessary for your job.
Self-fitting part
Suppose you’re designing a cartridge for a medical component, or a splice case for a portable radio. Why design two parts when you can use one? The splicing part is designed as a clasp so that the two halves can be safely assembled from either side to build a so-called “universal” part, which requires only the manufacture of a mold.
Mold modification
It is relatively easy to remove metal from existing metal molds, but it is difficult to add metal, or practically impossible to use rapid injection molding. From a part point of view, you can add plastic, but you can’t take it away. Keep in mind the “metal safe” design.
Some injection molds go through multiple iterations until a workable design emerges, eliminating the need to build a new mold for each change. You can start with the smallest, most basic part design, mold as many parts as needed, and then rework the mold to include other part features, or larger, higher versions of the same part, and mold it again. It’s not an exact science, but given the right pieces, this reuse approach can save money on tool development.
Formability -DFM analysis
Longsheng can provide a free Design for Manufacturability (DFM) analysis for your injection parts quotation, which can identify potential problem areas or opportunities for design improvement. Inadequate drawing angles, “unmachinable” features, impossible geometry — these are just a few examples where part design can and should be improved before it is finally put on the machine. Be sure to read these recommendations carefully and contact Longsheng’s process engineers for any design-related questions.
Multi-cavity and series of molds
Perhaps you need more parts? You can still use aluminum molds with two -, four -, or eight-cavity molds to achieve high yields, depending on the size and geometry of the part. Although this will affect your mold costs, it can reduce the price of the part.
Do you have a series of parts that can be put together? How about multiple molding projects at once? There is no need to make a mold for each individual part, as long as everything is made of the same plastic, each part is roughly the same size, and can be extruded into the same cavity while allowing the mold to operate properly. Alternatively, movable hinges can be used to connect the parts.

On-demand option
Depending on the number of parts you have, another way to reduce molding costs is to consider on-demand manufacturing. At speed, two injection molding service options are available (see table below). One is best for those who need smaller parts quantities and is usually associated with prototyping. The other option, which Longsheng calls on-demand manufacturing, is ideal for those who need slightly larger parts quantities, often as many as 10,000 or more aluminum mold parts. On-demand production is an excellent choice for managing fluctuations in parts demand, reducing total cost of ownership, and utilizing cost-effective bridge tools.
Another way to reduce the cost of injection molding is to consider on-demand manufacturing. Longsheng provides four injection molding service options, including single-color injection molding, two-color injection molding, plastic injection molding and insert injection molding. By providing different levels of on-demand manufacturing services based on your project requirements, SpeedPlus is an effective tool for managing fluctuations in parts demand and reducing total cost of ownership.
Part size
Part size is also a factor to consider. Different size parts need to use different tonnage injection molding machines, which will affect the cost of mold and parts. At present, Longsheng supports the largest size of injection parts for 900800400mm.
Conclusion
Reducing the mold cost of injection parts is a crucial factor in successful injection molding. By simplifying the mold design, opting for high-quality materials, optimizing the molding process, and partnering with the right injection molding company, you can save on mold costs while still receiving high-quality and efficient parts. Remember, the most significant savings in mold cost come from the initial design of the mold itself, so it is essential to invest time and resources in this area. By following these tips and working with a trusted partner, you can achieve successful injection molding at an affordable cost.
Of course, if your molding project is still in the proofing stage, only need a few parts, don’t worry, Longsheng can provide you with very cost effective mold, the fastest delivery in 2 hours. Click this link and upload 2D/3D drawings to get the order quotation!