Surface finish machining is a critical process in manufacturing that involves enhancing the surface of a workpiece to reach a desired level of roughness, smoothness, or texture. The surface finish of a product can have a significant impact on its performance, functionality, and overall aesthetic appeal. Therefore, choosing the right surface finish machining method is crucial to achieving the desired outcome.
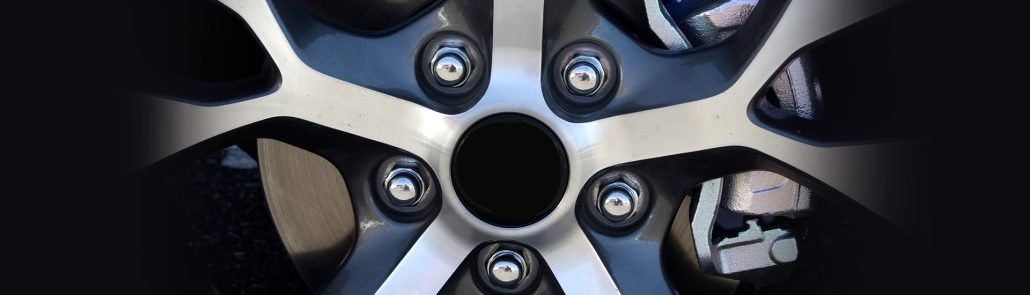
Surface Finish Machining Methods
There are several methods of surface finish machining that manufacturers can use, each with its own unique advantages and disadvantages. Let’s take a closer look at some of the most commonly used methods.
Grinding
Grinding is a widely used surface finish machining method that involves using an abrasive wheel to remove material from the surface of the workpiece. This method is commonly used to achieve a high level of precision and smoothness, making it ideal for applications where tight tolerances are required. Grinding can be performed on a variety of materials, including metals, plastics, ceramics, and composites.
Polishing
Polishing is another popular surface finish machining method that involves using a polishing wheel or abrasive compound to smooth the surface of the workpiece. This method is often used to achieve a highly reflective surface or to remove scratches and other imperfections. Polishing is commonly used on metals, plastics, and other materials that require a smooth, shiny surface.
Honing
Honing is a surface finish machining method that involves using a honing tool to remove small amounts of material from the surface of the workpiece. This method is often used to achieve a specific level of roughness or texture and is commonly used in applications where a tight tolerance is required. Honing can be performed on a variety of materials, including metals, plastics, and ceramics.
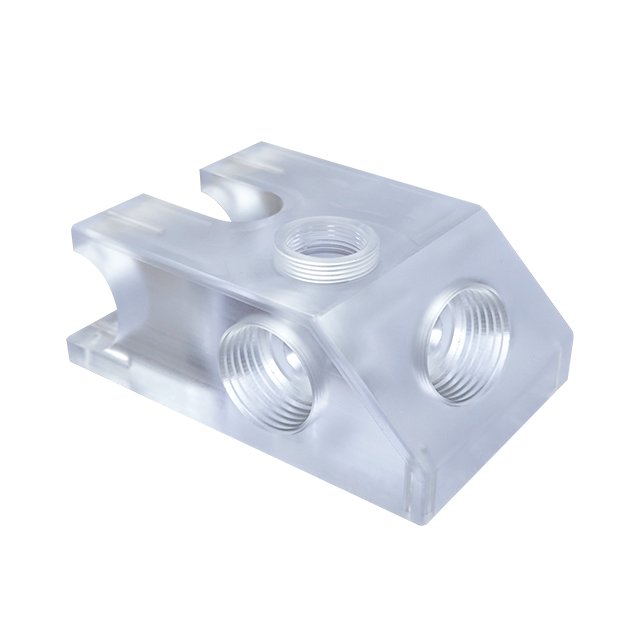
Lapping
Lapping is a surface finish machining method that involves using a lapping tool and abrasive slurry to remove material from the surface of the workpiece. This method is often used to achieve a high level of precision and smoothness, making it ideal for applications where a mirror-like finish is required. Lapping is commonly used on metals, ceramics, and other materials that require a high degree of flatness and parallelism.
In addition to the methods mentioned above, other surface finish machining methods include burnishing, electroplating, and shot peening. Each of these methods has its own unique advantages and disadvantages and is suitable for different applications.
When choosing a surface finish machining method, manufacturers must consider various factors, including the material being machined, the desired surface finish, the required tolerances, and the production volume. By selecting the right surface finish machining method, manufacturers can achieve the desired level of surface finish for their products, improving their performance, functionality, and overall aesthetic appeal.
In conclusion, surface finish machining is a crucial process in manufacturing that can significantly impact the quality of a product. Manufacturers must carefully consider the various surface finish machining methods available and choose the one that best suits their specific needs. By doing so, they can produce high-quality products that meet or exceed their customers’ expectations.