Metal machining can be a complex and challenging process, but with the right tools, knowledge, and experience, it can produce precision cnc parts and components for a wide range of applications.In this article, we will discuss what is metal machining, what are the three stages of metal machining and the three metal machining techniques
What is Metal Machining?
Metal machining is the process of shaping and removing material from a metal workpiece to create a desired product or part. This can be done through a variety of methods such as cutting, drilling, milling, and turning. Metal machining is often used in manufacturing and fabrication industries to create parts for various applications. The process requires specialized equipment and skilled operators to ensure precision and accuracy in the final product.
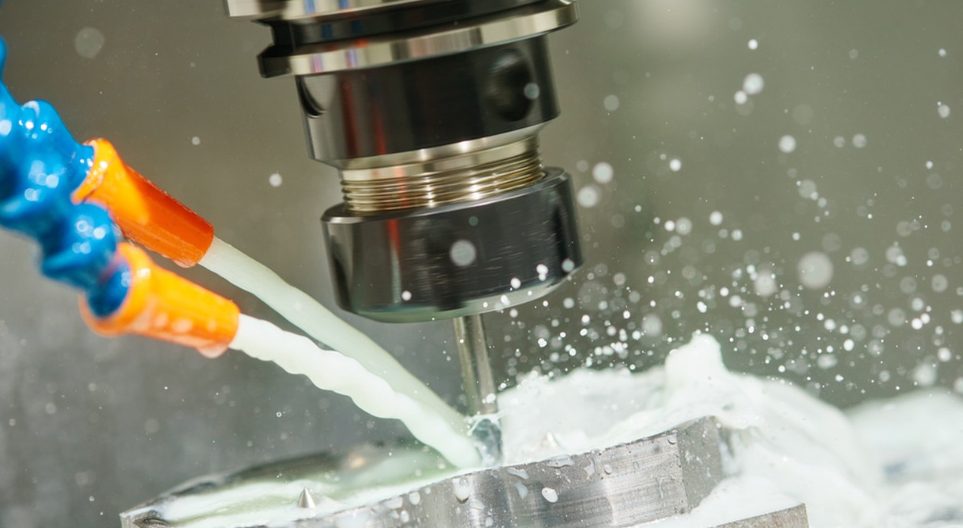
The Three Stages of Metal Machining
Metal machining is the process of shaping and cutting metal materials into a desired shape or form. It is a crucial process in the manufacturing industry and is used to create a wide range of products, from small parts and components to large machinery and structures. There are three primary stages of metal machining, each of which plays a critical role in the overall process.
Stage 1: Preparation
The first stage of metal machining is preparation. This involves selecting the appropriate metal material for the project and preparing it for the machining process. The metal may need to be cut to size, cleaned, or polished before it can be machined. Additionally, the machining tools and equipment must be selected and set up for the specific project at hand.
Stage 2: Machining
The second stage of metal machining is the actual machining process. This involves using various cutting and shaping tools, such as lathes, drills, and mills, to remove material from the metal and create the desired shape or form. The process may involve several different machining techniques, depending on the complexity of the project and the desired outcome.
Stage 3: Finishing
The final stage of metal machining is finishing. This involves applying various finishing techniques to the metal, such as sanding, polishing, or coating, to achieve the desired surface finish and appearance. Finishing is an essential part of the metal machining process, as it can impact the functionality and durability of the final product.
In conclusion, the three stages of metal machining are preparation, machining, and finishing. Each stage plays a critical role in the overall process and requires careful attention to detail to ensure a high-quality final product. By understanding these stages, manufacturers can optimize their metal machining processes and create products that meet their customers’ needs and expectations.

The 3 Main Types of Machining Technologies
Machining is the process of shaping a material into a desired form by removing unwanted material through various methods. There are different types of machining technologies based on the tool and process used. However, the three main machining technologies are:
- Turning: Turning is a machining process that involves the rotation of a workpiece around its axis while a cutting tool removes material from the workpiece. Turning is mostly used to create cylindrical shapes.
- Milling: Milling is a machining process that involves the use of a rotating cutting tool to remove material from a workpiece. The cutting tool moves along different directions to create a wide range of shapes and sizes.
- Drilling: Drilling is a machining process that involves the creation of holes in a material. A rotating cutting tool called a drill is used to create holes in a workpiece.
Each of these technologies has its own advantages and disadvantages. Choosing the right machining technology depends on the type of material, shape, and size of the workpiece, and the desired end product.
FAQ
Most metals can be machined, including steel, aluminum, brass, copper, and titanium. The specific type of metal will determine the machining parameters and tooling required.
The main machining processes include turning, milling, drilling, and grinding. Turning involves rotating the workpiece while a cutting tool removes material. Milling uses a rotating cutter to remove material from the workpiece. Drilling creates holes in the workpiece using a drill bit. Grinding uses an abrasive wheel to remove material and create a smooth surface finish.
Several factors can affect the machining process, including the material being machined, the type of machining process, the cutting tools and tool holders used, the cutting speed and feed rate, and the coolant or lubricant being used.
Metal machining can produce precise, high-quality parts with tight tolerances and a smooth surface finish. It can also be used to create complex shapes that would be difficult or impossible to produce using other methods.
Common challenges in metal machining include tool wear and breakage, chip formation and evacuation, and heat generation and management. Machinists must also be careful to avoid damaging the workpiece or tooling during the machining process.
To ensure a successful metal machining process, it is important to select the appropriate machining parameters and tooling for the specific application. Machinists should also be properly trained and familiar with the equipment and processes being used. Regular maintenance and inspection of the equipment and tooling can also help prevent issues and ensure consistent quality.