Working in the plastic part production industry can be challenging. I know because I’ve been in this field for quite a long time. As an experienced engineer, one thing I’ve realized is that mastering the intricacies of injection molding is crucial. Today, I want to share my knowledge about one such intricacy: the puller groove. But first, let’s answer the question, what is a puller groove in injection molding?
A puller groove is a special feature in the mold design of an injection molding process, strategically created to facilitate the ejection of the molded part. It serves as a groove or undercut in the mold where ejector elements can grab onto, effectively pulling out the part after it has been formed.
This might seem like a small detail, Why should you care about this feature? Because it can significantly impact the effectiveness and efficiency of your injection molding process.
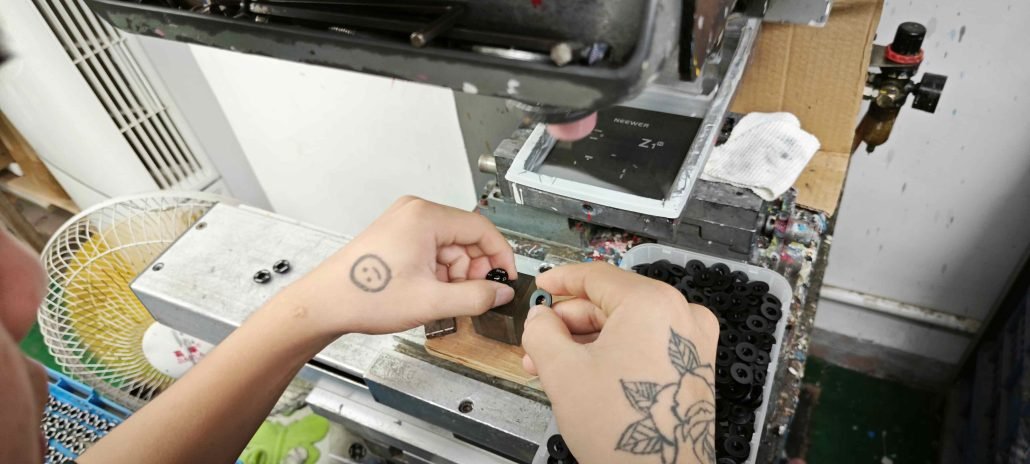
Why Are Puller Grooves Important?
Puller grooves are particularly important when dealing with complex shapes or parts with deep cavities. These conditions make part ejection a challenging task that, without an effective puller groove, can lead to part damage or increased cycle times.
Considering the high demand for custom plastic parts in industries like the medical, automotive, and aerospace sectors, it’s crucial to maximize efficiency while maintaining top-notch quality. And believe me, no one wishes to trade-off quality for speed!
How Do Puller Grooves Work?
Imagine trying to remove a sticky substance from a container without being able to scrape the sides. Not very efficient, right? That’s where a puller groove comes into play. It’s like the spatula you use to scrape out the last bit of your favorite peanut butter from the jar.
A puller groove allows the ejector elements of the injection mold machine to hook onto the part, providing leverage for an effective part ejection. It’s simple physics but significantly impacts the production process.

Are There Different Types of Puller Grooves?
Yes, indeed! The type of puller groove utilized depends on the part design and requirements. For instance, straight puller grooves are commonly used in relatively simple parts, while helical grooves are ideal for parts with rotational symmetry.
Another example is the use of multiple puller grooves in parts with complex geometries or those that require uniform force distribution during ejection. Therefore, understanding your part design and its ejection requirements is key in choosing the right type of puller groove.
To choose the right puller groove, consider the following:
1.Part Geometry: Review the shape and intricacies of the part design. For instance, a simple cylindrical part may just require a straightforward puller groove, while a complex, asymmetrical part might need a more sophisticated puller groove design.
2.Material Characteristics: Different materials react differently to the molding and ejection process. Some materials may require larger or deeper puller grooves, while others might need smaller or shallower ones.
3.Production Volume: For high-volume production, a well-designed puller groove that minimizes cycle times and maximizes efficiency is crucial.
Can Puller Grooves Be Customized?
Absolutely! In fact, puller grooves should be custom-designed for each mold to ensure optimal ejection. That’s part of our commitment here at Longsheng. We believe in delivering custom solutions to address each client’s unique needs.
After all, each product design presents unique challenges and requirements. For instance, medical parts may demand tighter tolerances and superior surface finishes compared to other parts. We understand these subtleties and cater to them diligently.
What Are The Considerations When Designing Puller Grooves?
Designing puller grooves isn’t a one-size-fits-all task. Some of the key considerations include the material used, the geometry of the part, and the mold design. For example, a puller groove design suitable for ABS may not work well with more flexible materials like TPE.
On the other hand, the geometry of the part may dictate the type and placement of the puller groov
e. Parts with deep cavities, undercuts, or protrusions may require multiple or specially designed puller grooves to facilitate ejection.
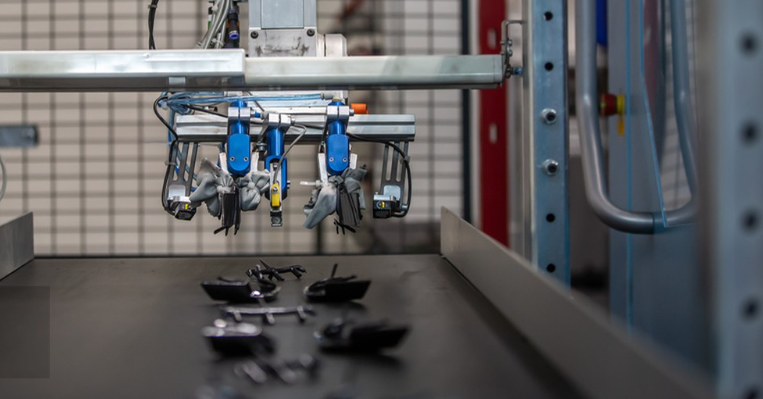
5 Ways to Master Complex Features in Injection-Molded Parts
Here are the top five ways to handle complex features in injection-molded parts.
1. Dive Deep into Design Analysis
Understanding the design of the part is crucial when dealing with complex features. Comprehensive design analysis is a prerequisite for successful injection molding.
This involves examining every tiny detail of the design – the curvature, the undercuts, the thin walls, the thick sections, and other intricate geometries. By doing a thorough design analysis, I can anticipate potential difficulties and prepare for them accordingly.
2. Material Science Matters
Selecting the right material is critical when dealing with complex features in injection molding. Materials have distinct characteristics and behave differently during molding.
I tend to consider aspects such as the material’s flow behavior, shrinkage rate, heat resistance, and toughness. A comprehensive understanding of these characteristics is critical when designing parts with complex geometries.
3. Mastering Mold Design
An optimized mold design is indispensable in handling complex features. A well-designed mold must align perfectly with the part’s design, and more importantly, with its complex features.
In designing the mold, I use strategies like multi-cavity molds, advanced gate types, and precisely crafted puller grooves. The mold design is pivotal to the process and plays a vital role in achieving high-quality results.
4. Harness Advanced Molding Techniques
In the world of injection molding, there are numerous advanced techniques that can be harnessed to tackle complex features. Techniques such as sequential valve gating, gas-assisted molding, and overmolding are just a few of the tools at our disposal.
Being well-versed in these advanced techniques can allow for the production of complex parts that would otherwise be difficult, if not impossible, to achieve with conventional methods.
5. Prioritize Validation and Iteration
Lastly, but by no means least, is the importance of rigorous validation and iteration. Injection molding is a complex process, and even the most experienced engineers encounter challenges along the way.
By implementing a validation process, I am able to test the design, mold, and process under realistic conditions. If any issues arise, I refine and iterate on the design and process, thereby ensuring optimal performance and quality.
Conclusion
In conclusion, a puller groove is a powerful tool in the hands of a skilled injection molding engineer. It allows for efficient and effective part ejection, ensuring a seamless, high-quality production process. Remember, every minor detail counts, and a puller groove is one such detail that can make a significant difference.
So, next time you think about injection molding, remember the importance of an efficient puller groove. After all, success often lies in mastering the details. At Longsheng, we understand this, and that’s why we ensure every element of your injection mold is tailored to perfection.
Mobile:+86 185 6675 9667(Gloria Wu)
E-Mail:gloria.wu@longshengmfg.com
FAQ
Material selection depends on the specific complexities of the part. Some materials may offer better flow characteristics for intricate geometries, while others might be more suitable for thick sections or parts with significant undercuts. An experienced injection molding engineer can guide you to select the most appropriate material.
It is always recommended to involve an injection molding engineer in the early stages of the design process. They can provide valuable insights on how to make your design more suitable for injection molding and how to handle any complex features effectively.
The number of iterations can vary widely depending on the complexity of the part, the materials used, and the specifics of the molding process. In some cases, just a few iterations may be sufficient, while in others, numerous iterations may be necessary to achieve optimal results.
Yes, it is generally possible to modify an existing mold to incorporate a puller groove. However, this will depend on the specifics of the mold and part design. An experienced injection molding engineer can advise you on the feasibility and implications of such a modification.
Yes, it is possible in some cases. However, for parts with deep or intricate features, a puller groove can often make the ejection process easier and more consistent, thereby enhancing the quality of the final part.