You may not realize that plastic is ubiquitous in our lives. Whether it’s a computer, a mobile phone case, a small pen or a cover, or even your Electric toothbrush, they may be made of injection molding plastic. The price difference of this plastic has a significant impact on manufacturers, suppliers, and consumers.
Explore the intricacies of injection molding plastics pricing with our detailed guide. Uncover the myriad factors contributing to price differences including plastic types, design complexity, production volume, geographic location, labor and overhead costs. Armed with this knowledge, navigate through varying quotes with ease and make informed purchasing decisions.
Why Injection Molding Costs Vary
The cost of plastic injection molding can vary greatly, depending on several key factors. These include the type and amount of plastic resin used, the design of the part, the complexity of the molding process, and the type and efficiency of the molding machine. If we were to simplify this into a single statement, we could say that the cost of injection molding is largely determined by the material, design, and production factors.
Material Costs
In the injection molding industry, a significant portion of the cost comes from the plastic resin used. The cost of these materials varies greatly, with commodity resins like polyethylene and polypropylene being less expensive than engineering resins like polycarbonate or ABS. Furthermore, the price of resin is subject to market fluctuations, making it a somewhat unpredictable factor.

Design Complexity
The design of the part also significantly affects the cost. Complex designs require more advanced and time-consuming mold fabrication techniques, which in turn raises the cost. Designs with intricate features, undercuts, or thin walls, for instance, require high-precision tools and longer production time, which can add to the overall expense.
Production Factors
The production factors, including the size and quantity of the parts, also greatly influence the price. Large parts require larger molds and more plastic, which increases the cost. Similarly, small production runs are generally more expensive per part due to the initial setup costs being spread across fewer parts. High-efficiency machines, on the other hand, can offset some of these costs by reducing production time.
Types and prices of Injection Molding plastics
In the world of plastics, there are many types, each with its unique properties and usage scenarios. At the same time, their prices also vary depending on the cost of raw materials, the complexity of the production process, and market demand
Common types of injection molding plastics
Common injection molding plastics and their characteristics and advantages:
1.ABS (Acrylonitrile Butadiene Styrene): ABS has good comprehensive performance, strong adhesion, good impact resistance and heat resistance, and is commonly used in the manufacturing of toys, household appliances, and computer hardware.
2.Polypropylene (PP): PP has excellent chemical resistance, wear resistance, and toughness. It has been widely used in packaging, automotive parts, textiles and other fields.
3.Polycarbonate (PC): PC is a very solid plastic with high impact resistance and transparency, which is commonly used to manufacture CDs, glasses, Bulletproof glass and medical devices.
4.Polyether ether ketone (PEEK): PEEK is a high-performance engineering plastic with excellent thermal stability and chemical stability, which is widely used in high-end fields such as aviation and medical treatment.
5.Polyethylene (PE): PE is a lightweight, chemical resistant, and wear-resistant plastic commonly used in the manufacturing of plastic bags, detergent bottles, and food packaging.
6.Polyethylene terephthalate (PET): PET has good barrier, transparency, and weather resistance, and is the preferred material for manufacturing beverage bottles and textiles.
7.Polyurethane (PU): PU has excellent elasticity, abrasion resistance and oil resistance, and is widely used in the production of foam, adhesives, auto parts, and sports shoes.
8.Polystyrene (PS): PS is easy to process, has good insulation and transparency, and is widely used in the manufacture of food packaging, Disposable tableware, and insulation materials.
9.Nylon (PA): Nylon has good wear resistance and high thermal stability, and is commonly used in the manufacturing of bearings, gears, and electronic components.
10.Polyoxymethylene: also known as engineering plastics, POM has excellent toughness and rigidity and is suitable for manufacturing high-precision gears and bearings.
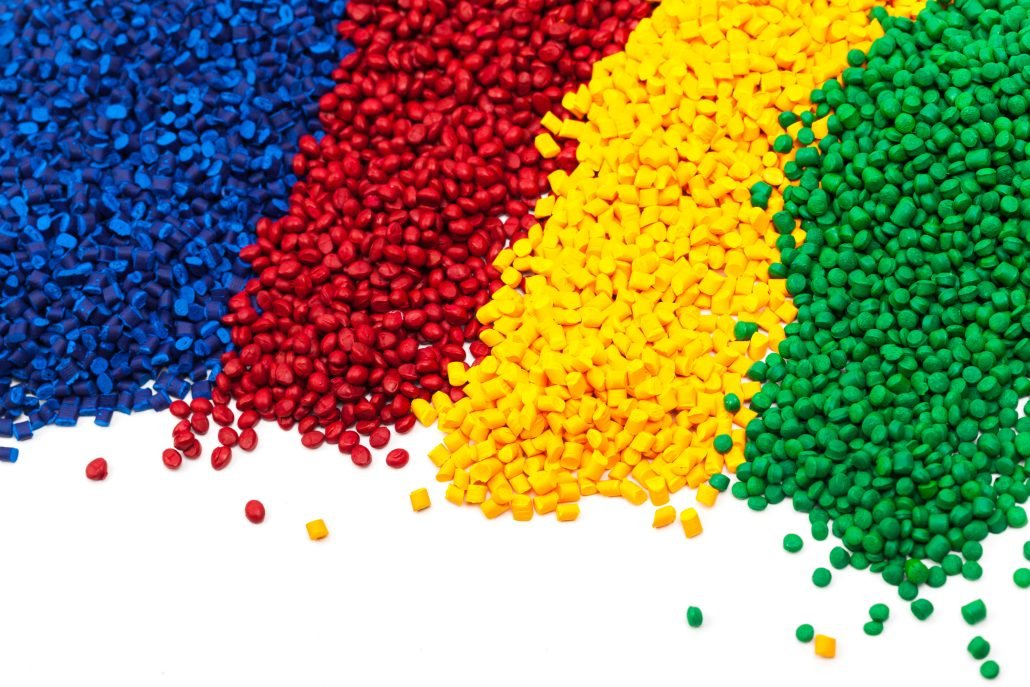
Injection molding plastic prices
The prices of injection molding plastics also vary due to various factors such as production costs, supply conditions, and market demand. Here are some common injection molding plastics and their prices (based on 2023):
Material Type | Average Price in 2023 (USD per pound) |
---|---|
ABS | 1.5 – 2.5 |
Polypropylene (PP) | 1.0 – 1.5 |
Polycarbonate (PC) | 2.0 – 3.0 |
Polyether ether ketone (PEEK) | 40.0 – 50.0 |
Polyethylene (PE) | 0.8 – 1.5 |
Polyethylene terephthalate (PET) | 1.0 – 1.5 |
Polyurethane (PU) | 2.0 – 3.0 |
Polystyrene (PS) | 1.0 – 1.5 |
Nylon (PA) | 2.0 – 3.0 |
Polyoxymethylene (POM) | 1.5 – 2.5 |
Overview of Plastic Injection Molding Costs
In order to better understand the cost of plastic injection molding for parts with different yields, let’s examine the injection molding cost structure in three different scenarios: low yield, medium yield, and mass production.
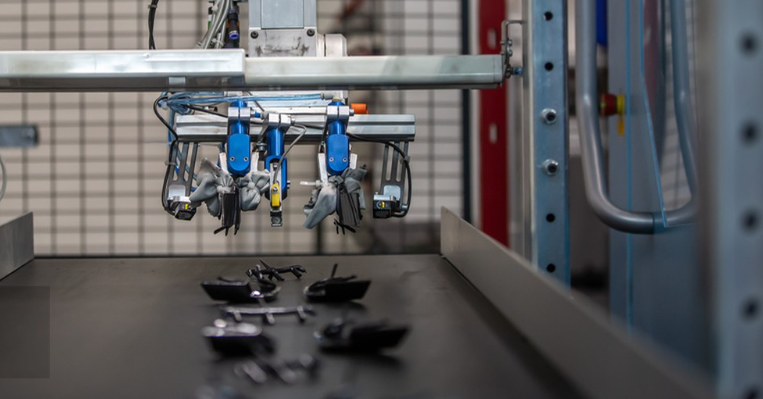
1.Low-Volume Production
Let’s assume we’re manufacturing a simple plastic part, and the order quantity is about 1,000 units.
Tooling Cost: The production of the mold is a significant upfront cost. A simple steel mold may cost around $1,000 – $5,000.
Material Cost: If we’re using ABS plastic at an average cost of $2 per pound, and each part weighs about 0.05 pounds, the material cost for 1,000 units will be around $100.
Labor and Overhead: This includes machine operation and maintenance, labor costs, utilities, and more. For a low-volume production, this could amount to around $500 – $1,000.
Total Cost: Adding these up, we’re looking at around $1,600 – $6,100 for 1,000 units.
2.Mid-Volume Production
Now let’s assume we’re manufacturing 50,000 units of the same part.
Tooling Cost: Higher production quantities may require a more durable mold, so the tooling cost may increase to around $5,000 – $15,000.
Material Cost: The total weight of plastic required now becomes 2,500 pounds, leading to a material cost of $5,000.
Labor and Overhead: For mid-volume production, this could rise to $2,500 – $5,000.
Total Cost: Summing these up, we get a total cost of $12,500 – $25,000 for 50,000 units.
3.High-Volume Production
Finally, let’s look at the cost for producing 1,000,000 units:
Tooling Cost: For this scale, you may need a premium, high-durability mold, which could cost $10,000 – $50,000.
Material Cost: Now, you need 50,000 pounds of plastic, costing around $100,000.
Labor and Overhead: This could increase to around $10,000 – $25,000 for such large-scale production.
Total Cost: Adding up these components, the total cost could range from $120,000 – $175,000 for 1,000,000 units.
As you can see, for mass production, the injection molding cost of each part is significantly reduced. Therefore, large-scale projects have the best cost-effectiveness for injection molding costs.
Factors affecting the price of injection molding plastics
The changes in plastic prices are determined by various factors. The following are five main factors that affect the price of injection molding plastics:
1.Material and Design
The type of plastic material used is the cornerstone of the cost. Plastics vary in their properties, durability, and prices. Commonly used plastics like Polyethylene (PE) or Polypropylene (PP) may be cheaper than engineering plastics like Polyetheretherketone (PEEK) or Polysulfone (PSU).
Moreover, the complexity of the design impacts the cost. A more intricate design requires a complex mold, which escalates the price. The number of cavities in a mold can also affect the price. Multi-cavity molds, while costly, can produce more parts per cycle, lowering the unit price.
2.Energy Costs
The process of creating plastics is energy-intensive. Thus, changes in energy costs can directly affect the production costs of plastics, consequently influencing their prices. Higher natural gas or electricity prices translate to increased costs to manufacture plastics. Inversely, if energy prices dip, the savings can be passed on to the consumers through reduced plastic prices.
3.Transportation Costs
The costs associated with transporting both the raw materials and the finished plastic products also play a significant role in the overall pricing of plastics. An increase in fuel prices can lead to heightened transportation costs, which are usually passed on to the consumer. Additionally, logistics-related challenges, like a lack of available shipping containers or transport capacity, can also lead to increased prices.
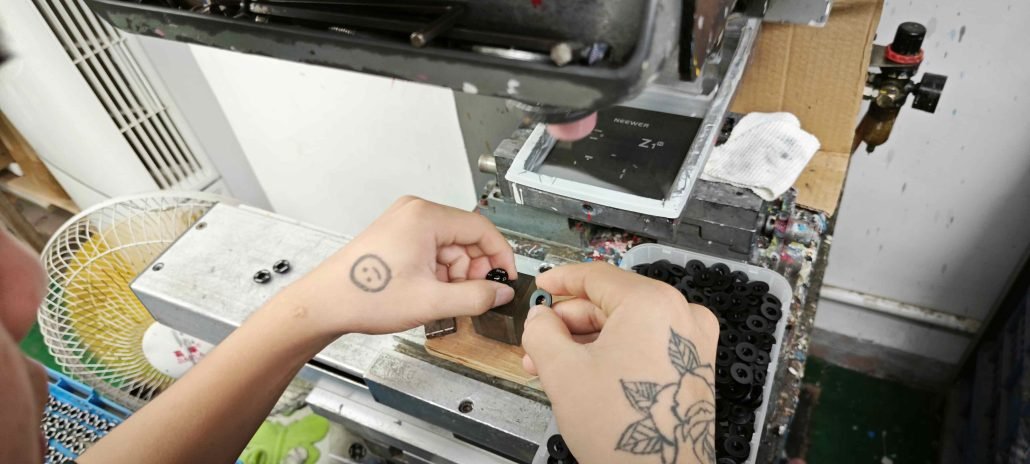
4.Currency Exchange Rates
Since plastic raw materials and products are traded globally, fluctuations in currency exchange rates can affect their prices. If a currency depreciates compared to others, the cost of plastics priced in that currency might increase. Conversely, if a currency appreciates, it can make those same plastics less expensive for buyers using other currencies.
5.Policies and Regulations
Government policies and regulations can have a considerable impact on plastic prices. For instance, if a government imposes new environmental regulations that require plastic manufacturers to employ greener production methods, this could increase production costs and, in turn, raise prices. Alternatively, subsidies or tax incentives could help to reduce the prices of certain types of plastics.
Conclusion
To sum up, the price difference for injection molding plastics results from a blend of factors, including the type of plastic, design complexity, production volume, geographic location, labor, and overhead costs. Understanding these factors will empower you to make informed purchasing decisions and potentially uncover cost savings without compromising quality.
FAQ
Depending on the specific requirements of your project, alternative processes such as 3D printing or CNC machining may offer cost advantages for smaller production runs or complex geometries. It’s essential to evaluate each process’s suitability for your specific needs.
Yes, injection molding can be used to create prototypes. Prototyping allows you to test and refine your design before investing in mass production. However, it’s important to note that prototype molds may have different costs and lead times compared to production molds.
Yes, there are eco-friendly alternatives such as biodegradable or recycled plastics that can be used for injection molding. These materials can help reduce environmental impact and meet sustainability goals.