What Is CNC Milling?
CNC milling, short for Computer Numerical Control milling, is a revolutionary machining process that has transformed manufacturing across industries.
Dating back to the 1940s, CNC milling has evolved into a sophisticated method for creating precise and complex components with remarkable efficiency.
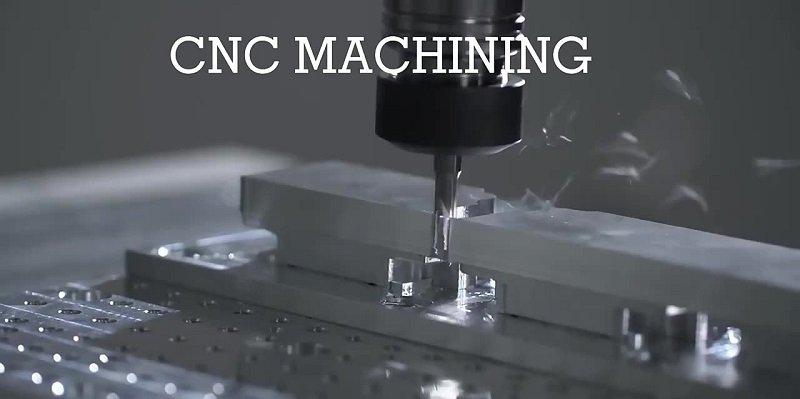
How CNC Milling Works
At its core, CNC milling involves using computerized controls to manipulate and guide cutting tools across various materials.
The process begins with a digital design, translated into a programming language that instructs the milling machine on tool movements, speed, and depth of cut.
This marriage of technology and craftsmanship ensures unparalleled accuracy and consistency in the final product.
Types Of CNC Milling Machines
There are several types of CNC milling machines, each tailored to specific applications. Vertical milling machines are ideal for intricate designs, while horizontal milling machines are suitable for heavier cutting tasks.
Gantries and routers are versatile options that find applications in various industries.

Materials Used In CNC Milling
CNC milling, a versatile machining process, transcends the boundaries of traditional metalworking. It opens its arms to a wide array of materials, making it a cornerstone in various manufacturing processes.
Metals
Traditionally associated with metal machining, CNC milling excels in working with metals such as aluminum, steel, brass, and titanium. Its precision and ability to handle intricate designs make it a preferred method for crafting components used in aerospace, automotive, and other metal-centric industries.
Plastics
CNC milling proves equally adept at working with plastics, offering a precise and efficient method for shaping materials like ABS, acrylic, and nylon. This capability extends CNC milling into the realm of product design, prototyping, and custom manufacturing where plastic components play a pivotal role.
Composites
In the contemporary manufacturing landscape, composites have gained prominence for their unique properties.
CNC milling has emerged as a reliable technique for processing composite materials like carbon fiber and fiberglass.
The method ensures the integrity of these composite structures, making it indispensable in industries such as marine and aerospace.
The adaptability of CNC milling across these materials highlights its versatility.
Whether crafting intricate metal components for aerospace applications, precision plastic parts for consumer electronics, or composite structures for advanced engineering, CNC milling stands as a universal tool in the modern manufacturing arsenal.
Its ability to seamlessly transition between these diverse materials underscores its significance in meeting the evolving needs of various industries.
What Are The Advantages Of Computer Numeric Control For CNC Milling?
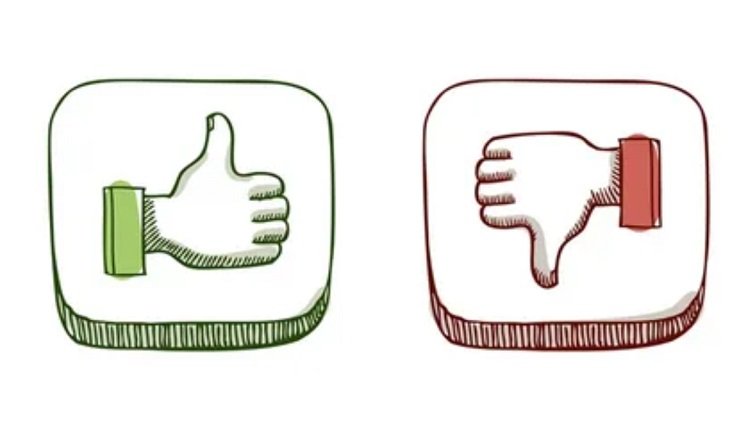
CNC milling, empowered by Computer Numerical Control, offers a myriad of advantages that have revolutionized the manufacturing landscape. The integration of digital precision and automation brings about efficiencies and capabilities that traditional milling methods struggle to match.
Precision And Accuracy
CNC milling excels in achieving unparalleled precision and accuracy in the machining process. The digital control allows for exacting measurements, intricate designs, and tight tolerances, ensuring that the final product meets the desired specifications with consistency.
Complex Shapes And Intricate Designs
Unlike conventional milling, CNC milling effortlessly handles the production of complex shapes and intricate designs. The ability to execute detailed and multifaceted patterns is a distinctive advantage, making it the go-to method for manufacturing components with high intricacy.
Efficiency And Repeatability
Automation is a hallmark of CNC milling, leading to enhanced efficiency and repeatability. Once programmed, the CNC machine can reproduce identical components with minimal variation, streamlining mass production and reducing the likelihood of human errors.
Versatility In Materials
CNC milling is not confined to a specific type of material. Whether dealing with metals, plastics, or composites, the versatility of CNC milling allows for a broad range of materials to be machined with precision. This adaptability makes it a preferred choice across diverse manufacturing processes.
Time And Cost Savings
The efficiency and precision of CNC milling translate into significant time and cost savings. Reduced setup times, faster production rates, and lower material wastage contribute to a more economical manufacturing process, especially in large-scale production.
Customization Options
CNC milling machines offer extensive customization options. The flexibility to program specific toolpaths and parameters enables manufacturers to tailor the machining process to meet unique project requirements. This customization capability enhances the adaptability of CNC milling across various applications.
Minimized Human Intervention
Automation in CNC milling minimizes the need for constant human intervention during the machining process. This not only increases safety but also allows skilled operators to focus on programming and overseeing the CNC machines, optimizing the overall manufacturing workflow.
Integration With CAD/CAM Software
The integration of CNC milling with Computer-Aided Design (CAD) and Computer-Aided Manufacturing (CAM) software streamlines the entire production cycle. This digital integration enhances communication between design and manufacturing, reducing the likelihood of errors and ensuring a seamless workflow.
In conclusion, the advantages of Computer Numerical Control in CNC milling contribute to its widespread adoption across industries. From precision and efficiency to versatility and automation, CNC milling stands as a transformative technology that continues to shape the landscape of modern manufacturing.
Choosing The Right CNC Milling Machine

The selection of a CNC milling machine is a critical decision that significantly influences the outcome of the manufacturing process. To ensure optimal results, several key factors must be carefully considered in the decision-making process.
Type of Material
The nature of the material to be machined is a fundamental consideration. Different materials demand specific machining capabilities. For instance, metals may require high-speed milling with robust cutting tools, while plastics may need a machine capable of delicate and precise movements. Assessing the compatibility between the material and the machine’s capabilities is crucial for successful milling.
Desired Precision
Precision requirements vary across industries and applications. Some projects demand tight tolerances and intricate details, while others may allow for more leniency. Choosing a CNC milling machine with the appropriate precision capabilities ensures that the final product meets the specified requirements. Consider the spindle speed, cutting tool options, and the machine’s overall rigidity in relation to the precision needed.
Customization Options
The ability to customize the CNC milling process is paramount. Look for machines that offer a range of customization options in terms of toolpaths, cutting parameters, and programming flexibility. A machine that allows for easy adaptation to specific project requirements ensures versatility and adaptability in a dynamic manufacturing environment.
Production Volume and Speed
The anticipated production volume and required machining speed play a crucial role in machine selection. For high-volume production, a CNC milling machine with rapid traverse rates and efficient tool change capabilities is essential. Balancing production speed with precision is key to achieving both efficiency and quality.
Machine Size and Capacity
The physical size and capacity of the CNC milling machine should align with the scale of the intended projects. Consider the size of the workpieces and the space available in the manufacturing facility. Oversized or undersized machines may lead to inefficiencies and limitations in project scope.
Ease of Use and Operator Skill Level
The ease of use and the skill level required to operate the CNC milling machine are critical factors. A machine that aligns with the skill set of the operators reduces the learning curve and enhances overall productivity. Additionally, intuitive controls and user-friendly interfaces contribute to a smoother workflow.
Maintenance Requirements
Assess the maintenance demands of the CNC milling machine. Regular maintenance is essential for optimal performance and longevity. Machines with accessible components, clear maintenance guidelines, and reliable support from the manufacturer simplify the upkeep process.
Cost Considerations
While cost should not be the sole determinant, it is a practical consideration. Evaluate the initial investment, as well as the long-term costs associated with maintenance, tooling, and energy consumption. A well-balanced investment ensures value for money over the machine’s lifecycle.
By carefully weighing these factors, manufacturers can make informed decisions when choosing a CNC milling machine. This strategic approach not only aligns the machine with current production needs but also positions the operation for future growth and adaptability in the dynamic manufacturing landscape.
CNC Milling vs. Traditional Milling
The choice between CNC milling and traditional milling methods represents a pivotal decision in the manufacturing world. Understanding the distinctions between these two approaches sheds light on the advantages and considerations that can impact the efficiency and quality of the machining process.
Advantages of CNC Milling:
Automation
CNC milling is synonymous with automation. Once programmed, the CNC machine operates autonomously, executing precise tool movements and machining sequences without constant human intervention. This automation minimizes the risk of errors associated with manual operation, leading to consistent and reliable production.
Precision and Accuracy
The hallmark of CNC milling lies in its exceptional precision and accuracy. Computer Numerical Control ensures that every movement of the cutting tool is precisely calculated, resulting in intricately detailed and dimensionally accurate components. This level of precision is challenging to achieve consistently with traditional milling.
Efficiency and Repeatability
CNC milling machines excel in efficiency and repeatability. Once a program is established, the machine can replicate the same process over and over again with minimal deviation. This capability is invaluable in mass production scenarios, where consistent quality and high production rates are paramount.
Complex Shapes and Intricate Designs
The digital nature of CNC milling allows for the machining of complex shapes and intricate designs with ease. This flexibility makes it the preferred choice for industries that demand intricate components, such as aerospace and medical manufacturing.
Considerations for Traditional Milling:
Manual Operation
Traditional milling relies heavily on manual operation. Machinists manipulate the cutting tools and guide the milling machine, introducing a level of skill and experience into the process. While skilled operators can achieve impressive results, the human element introduces the potential for variability and errors.
Limited Precision
Achieving the same level of precision as CNC milling manually is challenging. Human limitations, including fatigue and varying skill levels, can result in inconsistencies in the final product. Traditional milling may be suitable for less intricate projects where precision requirements are more forgiving.
Setup Time and Adjustments
Traditional milling often involves lengthy setup times and adjustments. Machinists must manually configure the machine for each job, leading to increased downtime between projects. CNC milling, in contrast, streamlines this process with faster and more efficient tool changes.
Human Error
The reliance on human operators in traditional milling introduces the risk of human error. Factors such as fatigue, distraction, or miscalculations can impact the quality and accuracy of the machined components. CNC milling significantly reduces these risks through automated, computer-controlled processes.
In summary, while traditional milling methods have their merits, CNC milling stands out as a transformative technology that addresses many limitations associated with manual processes. The advantages of automation, precision, and efficiency position CNC milling as the preferred choice for industries demanding high-quality, consistent, and intricate machining results.
FAQs About CNC milling
Is CNC milling limited to metal materials only?
No, CNC milling can be used on a variety of materials, including metals, plastics, and composites.
How does CNC milling differ from traditional milling?
CNC milling involves computerized controls for precise and automated machining, whereas traditional milling relies on manual operation.
What safety measures should be taken when operating CNC milling machines?
Operator training, adherence to safety protocols, and the use of safety features on machines are crucial for a secure working environment.
Can CNC milling machines be customized for specific applications?
Yes, CNC milling machines can be customized based on the type of material and precision requirements for a particular application.
What are the future trends in CNC milling?
The future of CNC milling involves increased automation, integration with digital technologies, and potential applications in nanotechnology.
Conclusion
CNC milling stands as a testament to the marriage of craftsmanship and technology, offering unparalleled precision and efficiency in manufacturing.
As we look to the future, advancements in automation, integration with digital technologies, and a commitment to sustainability will continue to shape the landscape of CNC milling.