Injection molding is a popular manufacturing process used by various industries to produce high-quality plastic parts. This process has gained immense popularity over the years due to its efficiency, consistency, and ability to produce complex parts with high precision.
In this ultimate guide, we will delve deep into the world of custom injection molding and explore why it is used by countless industries. This guide is designed to provide you with a comprehensive understanding of the process, its benefits, and applications.
What is Injection Molding?
This chapter focuses on providing a clear understanding of the injection molding process. We begin by exploring the core principles of this process, how it works, and the various components that make up a typical injection molding system.
If you’re in the manufacturing industry, you’ve likely heard of injection molding. But what exactly is it, and how does it injection molding work? In essence, injection molding is a manufacturing process that involves injecting material – often thermoplastic polymers – into a mold to create a finished product. This process is used to create a wide variety of products, from simple plastic toys to complex medical devices. The injection molding process consists of several stages. First, the raw material is heated until it reaches a molten state. Then, it is injected into a mold under high pressure. The material cools and solidifies quickly, taking on the shape of the mold. Finally, the finished product is ejected from the mold. Injection molding has several advantages over other manufacturing methods. It is a highly efficient process, capable of producing large quantities of identical products quickly and inexpensively. It also allows for complex geometries and precise tolerances – something that would be impossible with other methods.

Benefits of Injection Molding
In this chapter, we will dive into the many benefits that injection molding offers. We highlight how this process offers exceptional consistency, the ability to produce complex geometries, and the ability to produce high-quality parts at high volumes. Additionally, we explore how injection molding is an economical option for large-scale production runs.
Advantage #1: Cost-Efficient
One of the biggest advantages of injection molding is its cost efficiency. Because it is a highly automated process, injection molding reduces labor costs and increases production rates. Additionally, the molds used in injection molding are durable and can be used for thousands of cycles, which saves money in the long run.
Advantage #2: Versatile
Another big advantage of injection molding is its versatility. Injection molding can be used to produce a wide variety of parts, from small, intricate components to large, complex structures. This flexibility makes injection molding an ideal process for a range of applications, including automotive, medical, and consumer products.
Advantage #3: High-Quality Output
Injection molding produces high-quality parts consistently and reliably. Because the molds used in injection molding are made to tight specifications, the parts produced are precise and consistent. Additionally, injection molding allows for tight tolerances, which ensures that parts fit together correctly and function properly.

Advantage #4: Eco-Friendly
Injection molding is an eco-friendly process. Because it is a closed-loop system, excess material is typically ground up and recycled. Additionally, injection molding produces less waste than other manufacturing processes, which results in a smaller environmental footprint.
Advantage #5: Quick Turnaround Times
Finally, injection molding offers quick turnaround times. Because the process is highly automated, it can produce parts quickly and efficiently. Mold changes are also relatively fast, which means that new parts can be produced quickly and easily.
As you can see, there are many benefits to using injection molding in your manufacturing process. From cost-efficiency to high-quality output, injection molding offers a range of advantages over other manufacturing processes. If you are looking for a proven, reliable, and versatile manufacturing process, then injection molding is definitely worth considering.
Applications of Injection Molding
Injection molding is used in an array of industries, from automotive and aerospace to healthcare, packaging, and consumer goods. In this chapter, we look at specific examples of how injection molding is used in these industries and highlight the many ways it has transformed manufacturing and design processes.
In this article, we will take a closer look at the various applications of injection molding and how they have transformed the manufacturing industry.
Automotive industry
The automotive industry is one of the largest users of injection molding. The process is used to manufacture a wide variety of components for cars, including dashboards, bumpers, and fenders. The use of injection molding in the automotive industry has revolutionized the manufacturing process, making it faster, more efficient, and more cost-effective.
Medical industry
Injection molding plays a crucial role in the production of medical equipment, including syringes, blood test tubes, and surgical instruments. The technique has enabled medical companies to produce complex equipment with incredible precision while reducing production time and costs. This has improved the quality of healthcare worldwide.
Consumer goods industry
Injection molding is widely used in the production of consumer goods such as electronics, home appliances, and housewares. It is a highly efficient process that can produce large volumes of products quickly and at a low cost. Injection molding has also enabled manufacturers to produce products with intricate designs and shapes, allowing for more creative and aesthetically pleasing products.
Toys and games industry
Injection molding has transformed the toy and games industry by making the production of plastic toys faster and more efficient. Toy manufacturers can produce large volumes of products in a short time, and with the help of 3D printing, create highly detailed designs. Injection molding has also allowed for the production of more complex toys and games with moving parts, electronic components, and intricate details.
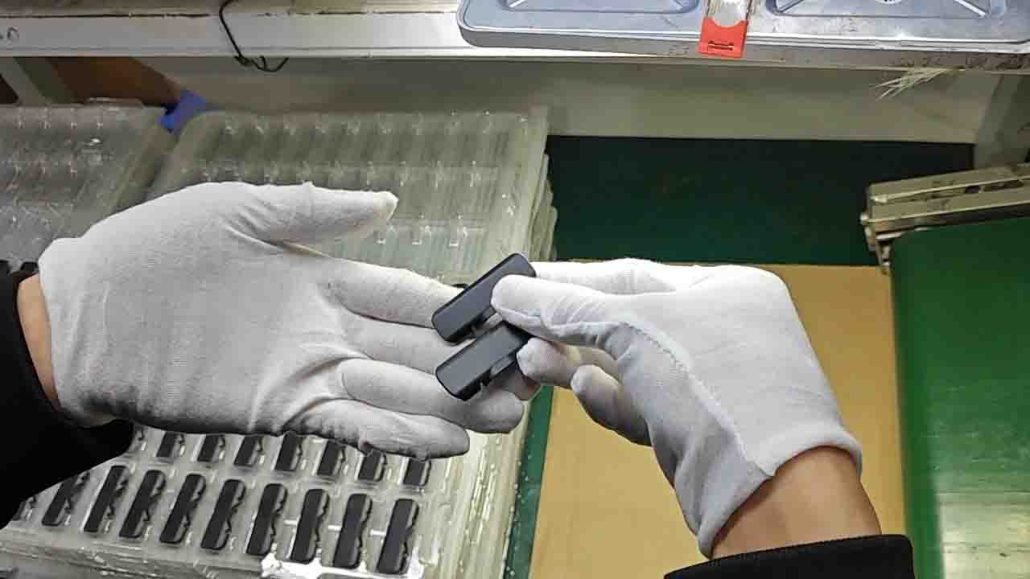
Injection molding is a powerful manufacturing process that plays a crucial role in various industries. Its versatility and efficiency have transformed the way we produce goods and equipment. From the automotive and medical industry to consumer goods and toys, the applications of injection molding are virtually limitless. If you are looking for a cost-effective and efficient manufacturing process, injection molding is definitely worth considering.
Design for Injection Molding
Design is critical for the successful application of injection molding. In this chapter, we delve into the various design considerations that manufacturers must take into account when designing parts for injection molding. We explore key design principles, such as the use of fillets, draft angles, and the importance of consistency in wall thickness.
Injection molding is a popular manufacturing process used to mass-produce a wide range of plastic products. In order to produce high-quality plastic parts that meet the requirements of manufacturers, it’s essential to design the mold correctly. Understanding the principles of design for injection molding is essential if you want to create a product that will meet your needs and exceed your expectations.
Selecting the Right Material
The first step in designing for injection molding is selecting the right material. Injection molding can be used with a wide range of materials, including plastic, metal, and even rubber. However, not all materials are created equal when it comes to injection molding. Some materials may be more flexible, while others may be more brittle. It’s important to consider your product’s requirements when choosing the material.
When selecting a material for your product, you should consider factors such as mechanical properties, chemical resistance, thermal stability, and cost. By keeping these factors in mind, you can select the best material for your product and ensure that it will perform well in the injection molding process.
Designing the Mold
Once you’ve selected the right material, it’s time to design the mold. A properly designed mold is the key to producing high-quality plastic parts. When designing the mold, you should consider factors such as wall thickness, draft angles, and parting lines.
Wall thickness is one of the most important factors to consider when designing the mold. Parts with uneven wall thickness can lead to warping, shrinkage or even part failure. It’s important to design your part with enough wall thickness to ensure that it will have the necessary strength and durability, but not so much that it becomes too thick and difficult to produce.
Draft angles are also crucial in injection molding. Draft angles can help to reduce stress and damage during the molding process by allowing the part to be easily removed from the mold. Parting lines are another important consideration, as they can impact part quality and production efficiency. By designing your part with the proper draft angles and parting lines, you can ensure that your injection molding process goes as smoothly as possible.
Designing for injection molding is a complex process that requires a lot of planning, preparation, and expertise. By selecting the right material and designing the mold properly, you can create a plastic parts that meet the requirements of manufacturers and exceed your expectations.
If you’re looking to design a mold for injection molding, it’s important to work with experienced professionals who can guide you through the process. By working with a team of experts, you can ensure that your design is optimized for injection molding and delivers the high-quality results you need.
At Longsheng Technology Company, we have years of experience in designing custom injection molds, and we have the expertise you need to create a mold that is optimized for your specific product. Contact us today to learn more about our design services and how we can help you achieve the results you need.
Materials Used in Injection Molding
The beauty of injection molding lies in the ability to produce parts from a wide range of materials. From plastic to rubber, and even metal, the versatility of materials used in injection molding is impressive. With this technology, the variations in material types and product shapes allow manufacturers to create parts that meet the exacting specifications of their clients. The materials used in injection molding can be mixed to create a unique combination of properties, making it a customizable process that can be tailored to specific manufacturing needs.
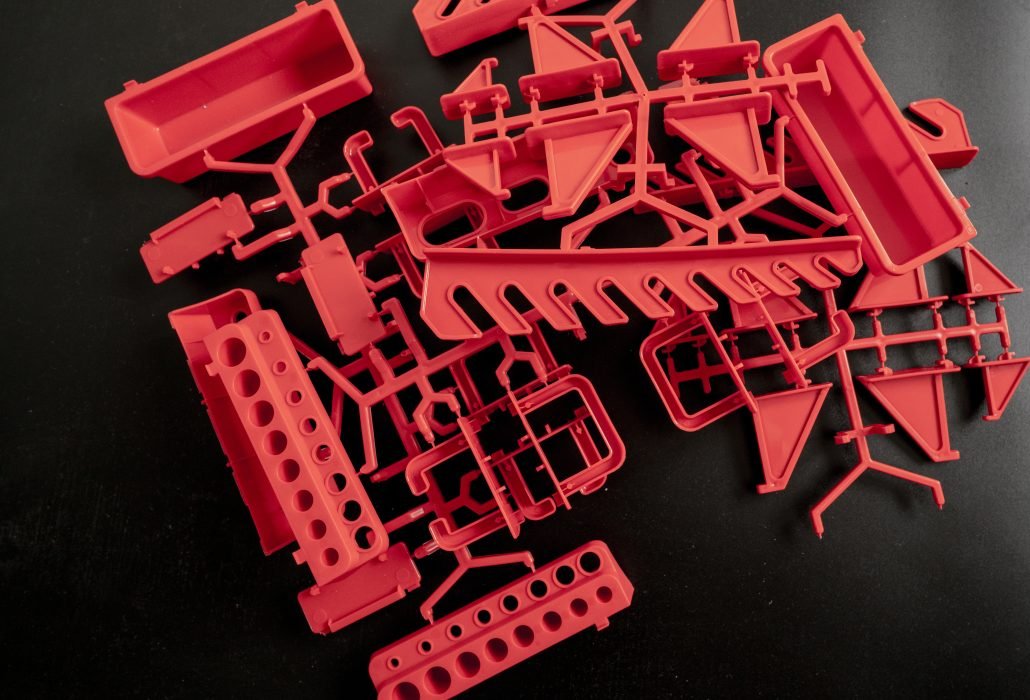
Why is Injection Molding So Popular?
Injection molding’s popularity comes from the unique combination of its benefits and applications. The high production output, precision, versatility, and quality of injection molding are essential to industries that demand superior standards. By streamlining the process of manufacturing and ensuring a consistent product, injection molding provides the foundation for innovation and growth in various industries.
Troubleshooting Injection Molding
Though the injection molding process is efficient and reliable, issues can sometimes arise. In this chapter, we look at some common issues that can occur in the injection molding process and provide strategies for troubleshooting them.
1. Warping: Warping is the deformation or bending of the part after it cools. It is caused by uneven cooling or a temperature difference between the mold and the part. To solve this problem, you can adjust the mold temperature or add cooling channels to the mold.
2. Flashing: Flashing is an excess plastic that protrudes from the part after it is ejected. It is usually caused by a poor mold design or excessive clamping force. To solve this problem, ensure that the mold is designed to prevent flashing or adjust the clamping force to prevent it from happening.
3. Sink marks: Sink marks are depressions or craters on the surface finishing of the part. This problem is usually caused by uneven cooling or insufficient packing pressure. To solve this problem, increase the packing pressure or adjust the cooling rate to ensure that the plastic cools evenly.
4. Short shots: Short shots occur when the plastic material does not fill the entire mold cavity. This can be caused by a variety of factors such as a cold runner system or a nozzle obstruction. To solve this problem, ensure that the mold cavities are properly vented and adjust any temperature settings if necessary.
5. Burn marks: Burn marks are dark brown or black streaks on the surface of the part, caused by excessive heat or poor lubrication. To solve this problem, adjust the temperature settings or lubricate the mold to ensure that it runs smoothly.
The Importance of Troubleshooting Effective troubleshooting is crucial to ensure a successful production run. Troubleshooting injection molding problems not only helps to prevent production downtime, but also maximizes the efficiency of the process, leading to higher quality parts. It is important to identify and solve problems as they occur to prevent them from becoming more severe and reducing the lifetime of the mold.
With this ultimate guide, we hope you have gained a comprehensive understanding of injection molding, its benefits, and applications. Whether you are an engineer, designer, or an industry expert, the knowledge you’ve gained from this guide will help you make informed decisions about incorporating injection molding into your manufacturing processes.