Computer numerical control (CNC) machining has completely changed the manufacturing processes of various industries, and aerospace is no exception. The aerospace industry requires its products to have high precision, high accuracy, and high reliability, and CNC machining can accurately and efficiently produce complex parts to meet the needs of aerospace. This introduction explores how CNC machining is not only a part of aerospace, but also the core of its continuous development and success.
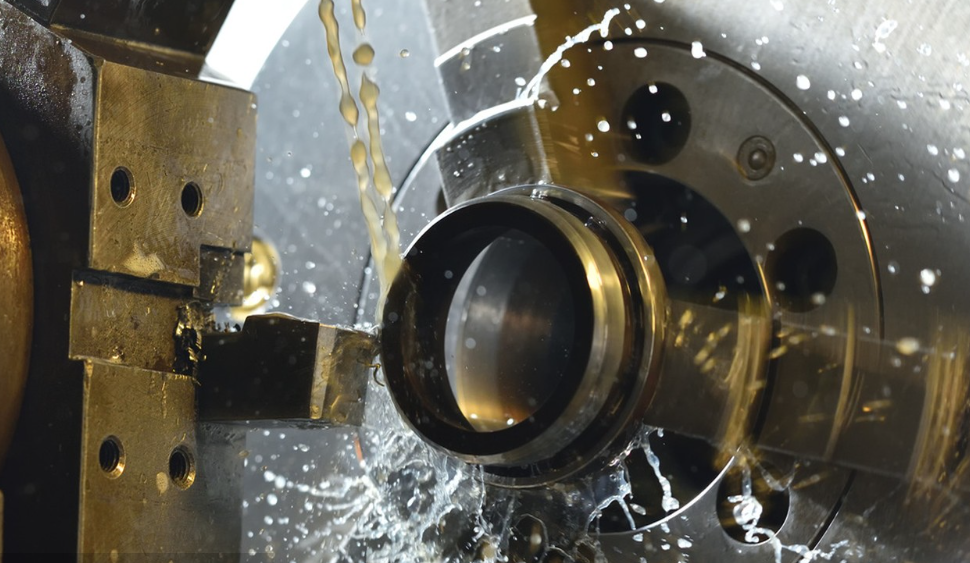
What is aerospace?
Aerospace is a term used to collectively refer to the atmosphere and outer space. Aerospace activities are very diverse, with many commercial, industrial, and military applications. Aerospace engineering includes both aviation and aerospace. Aerospace organizations research, design, manufacture, operate or maintain aircraft and spacecraft. The aerospace manufacturing industry is also rapidly developing, reaching new heights in innovation and efficiency, and CNC machining is the core of this transformation. It has brought many new changes to aerospace, redefining the manufacturing, performance, and design of aerospace parts.
What is aerospace CNC machining?
Aerospace CNC machining is one of the many applications of CNC machining technology, which is a specialized manufacturing technology, It will use CNC machine tools to process and produce according to specified trajectories and parameters according to instructions issued by the computer system, thereby achieving precise requirements for the shape, size, and technology of the parts.
In modern aerospace manufacturing, there are many related regulatory requirements, testing standards, and functional requirements, and component accuracy is very important. The production and assembly methods of airplanes are precise, so inconsistencies and defects may have a wide range of negative impacts. CNC machining is very suitable for manufacturing aerospace parts, as this process can achieve extremely strict tolerances for plastic and metal parts.
What materials are used in aerospace processing?
Generally speaking, the preferred metal for the aerospace industry is titanium or aluminum, and the use of carbon fiber is also increasing.
What is a key consideration for any aircraft? Weight. The lighter the aircraft, the higher the fuel efficiency, and therefore the higher the cost efficiency. Of course, in addition to being lightweight, airplanes also require flight safety. Therefore, metals with high strength but light weight are the best.
Aluminum and aluminum alloys
Aluminum is one of the most commonly used metals for processing aerospace parts, mainly due to its high tensile strength and light weight. In addition, aluminum has excellent formability, which makes it easy to process with CNC machines.
The most popular aluminum alloy used for CNC machining in the aerospace industry is 7075 aluminum, which is mainly composed of zinc. It has good fatigue strength. This material has been used to produce multiple wing, fuselage, and support structural components.For example, the fuselage and wings of Boeing 777 aircraft heavily use aluminum alloy materials.
Titanium and titanium alloys
Titanium alloy has the advantages of high strength and low density (only about 57% of steel), and its specific strength (strength/density) far exceeds other metal structural materials. It can produce components with high unit strength, good rigidity, and light weight. The engine components, frame, skin, fasteners, and landing gear in the aircraft are all made of titanium alloy.
Titanium alloy has become one of the most expensive metal materials due to its high melting point and difficult to process properties. However, the lightweight, high strength, and high temperature resistance of Ti6Al4V titanium alloy have attracted much attention in the aerospace field. Its application scope includes blades, discs, casings, and other parts that work in the low-temperature section of engine fans and compressors, with a working temperature range of up to 400-500 ℃. In addition, it is also used to manufacture fuselage and spacecraft components, rocket engine cases, and helicopter rotor hubs.
engineering plastic
Due to its extremely light weight, excellent impact and seismic resistance, strong sealing performance, and good chemical resistance, plastic may be a valuable substitute for metals. In addition, compared to metals, plastics have better electrical insulation and are an ideal choice for prototype CNC machining. PEEK、 Polycarbonate and Ultem are high-performance polymers used for aerospace processing.
Aerospace engineering plastics can be processed by CNC to manufacture various components and coatings to meet the special needs of aerospace. For example, polycarbonate (PC) is widely used in the manufacturing of aircraft cabin covers, lighting equipment, and bulletproof glass due to its excellent comprehensive performance (such as high strength, impact resistance, heat resistance, etc.).
Not all engineering plastics are suitable for aerospace CNC processing, as aircraft polymers must comply with specific toxicity, smoke, and flame standards. So this is a crucial factor.
The advantages of using CNC to process aerospace parts
- Repeatability:CNC machines can read commands and execute them repeatedly at high speed. This is particularly useful for the aerospace industry, as they must mass produce various complex components. The repeatability characteristic makes the application of CNC machines extremely beneficial in the aerospace industry, as it can improve productivity while maintaining product quality, and can well meet the demand for high-quality parts in large quantities in aerospace.
- Flexibility:This is another advantage of CNC machine tools in the aerospace industry. Aerospace and defense are industries with a large number of requirements, and CNC machine tools have the flexibility to adapt to different commands, which can help manufacture various parts required by the industry.
- Precision and Accuracy:The aerospace manufacturing industry requires the highest standards of accuracy and reliability. The components must meet strict tolerances and adhere to strict quality and safety standards. CNC machining provides unparalleled accuracy and precision, ensuring that aerospace parts meet precise specifications. This is particularly important for critical aerospace systems, such as turbine engines, landing gears, and structural components, where even slight deviations can seriously affect performance and safety.
- There is no room for error:CNC machines can effectively automate various processes involved in the manufacturing process. Due to full automation, there will be absolutely no errors. The core of CNC machines is repeatability, high precision, and error free precision machining.
CNC aerospace processing technology
CNC milling
CNC milling is a multifunctional process widely used in the aerospace field for manufacturing complex components such as fuselage, engine mounts, and aerospace prototypes. This process involves using rotating multi-point cutting tools to remove material from the workpiece, thereby forming precise shapes and details.
CNC milling can process a variety of materials, including aluminum alloys, titanium, and advanced composite materials, making it an ideal choice for lightweight and strength critical aerospace applications. Its accuracy allows for the production of parts with strict tolerances, which is crucial for the safety and functionality of aerospace components.
CNC Turning
CNC turning is another technology used in the aerospace industry, particularly for producing circular or cylindrical parts such as shafts, pins, and bushings. This process involves a single point cutting tool parallel to the material being cut, which can achieve high-precision machining.
Turning technology is highly valued in the aerospace field because it can achieve excellent surface finish and meet the strict tolerances required for parts that must withstand high stress and high temperature during flight.
CNC drilling
CNC drilling is used to drill holes in aerospace components, which are typically used to secure parts or hydraulic systems. This process uses a multi-point drill bit to accurately and efficiently drill holes on the material.
CNC drilling can be carried out on flat or curved surfaces, making it highly adaptable to aerospace applications. In this application, drilling precise holes is usually crucial for the structural integrity and functionality of the parts.
5-axis CNC machining
5-axis CNC machining stands out in the aerospace manufacturing industry because it can process extremely complex geometric shapes commonly required in modern aerospace design. Unlike traditional 3-axis machining, a 5-axis machine tool can rotate on two additional axes, allowing the cutting tool to approach the workpiece from any direction.
This feature reduces the need for multiple settings, improves production efficiency, and significantly shortens processing time. 5-axis CNC machining is particularly useful for components such as turbine blades, fuselage components, and wing panels, which require complex shapes and deep cutting with the highest precision.

Typical Surface Treatment of CNC Aircraft Parts
Although CNC aerospace machined parts have multiple surface treatments to choose from, not all surface treatments are suitable for use in aircraft components. The industry mainly uses the following four types.
Anodization
This surface treatment requires immersing aerospace components in an electrolyte solution to form a uniform oxide layer on the surface of the components. There are two types of anodizing used in aerospace components: Type II and Type III.
Type II anodizing forms a decorative layer on the surface of the parts. This layer is usually very thin, making the surface and aerospace parts susceptible to corrosion and wear when exposed. On the other hand, Type III anodizing forms a more protective hard coating on the surface of the parts.
passivation
Passivation is the process of coating materials in physical chemistry and engineering to make them less susceptible to environmental influences or corrosion. In the aerospace field, stainless steel components are usually passivated to remove surface contaminants and enhance corrosion resistance, ensuring service life and reliability.
burnishing
Polishing refers to the plastic deformation of the surface caused by sliding contact with another object. It makes the surface smooth and more shiny.
In addition, polishing can also improve the durability of aerospace materials. It achieves this by reducing the likelihood of fragmentation or cracking. The disadvantage is that polishing aerospace parts takes a long time and is costly.
powder coating
The most typical surface treatment for metal aviation components is powder coating, which is renowned for its functional diversity and durability. Powder coated aviation components are scratch resistant and will not fade over time. And the paint has color, which can add a touch of beauty to aviation parts.

Skills to understand when processing aerospace parts
operating simulation
Before actually producing aerospace parts, please use CNC machining simulation software to ensure that everything is perfect from beginning to end. With the help of simulation software, you can intuitively understand the working principles of aerospace components before entering production.
processing
According to the material, size, shape and other requirements of the parts, choose appropriate processing methods, such as turning, milling, etc., and control appropriate parameters to ensure the quality and accuracy of the parts during this process. It is also necessary to choose appropriate tools and fixtures to improve the accuracy of the parts processing.
Break down production into specialized parts
Viewing the product as a whole may be daunting, so it is best to break down the production line. Split the production system into specialized parts based on the quality and components of the product. When you choose the appropriate equipment for the task at hand, it helps simplify the production of aerospace parts.
Assembly and Inspection
Using advanced assembly technology, assemble each component to form the final product. Use precision testing equipment to conduct quality inspections on the parts, ensuring that they meet the design requirements, in order to produce high-quality parts.
The application of aerospace CNC machining
Turbine blades and impellers: Turbine blades and impellers are key components of engines that must withstand high temperatures and pressures. CNC machine tools can ensure that complex parts can achieve extremely high precision and meet the needs of engines through high precision, rigidity, and stability.
APPLICATION | CONTNET |
Turbine blades and impellers | Turbine blades and impellers are key components of engines that must withstand high temperatures and pressures. CNC machine tools can ensure that complex parts can achieve extremely high precision and meet the needs of engines through high precision, rigidity, and stability |
Electrical connector | CNC machining helps to produce aircraft electrical systems, which are crucial components. The production of aircraft electrical systems typically depends on their weight and space limitations |
Valve components | These small components have a wide range of applications in the aerospace field, and CNC machined valves ensure the accuracy and effective and safe operation of the parts |
Material processing | High strength and high-temperature stability materials are required for aerospace, and the tools and systems equipped with CNC machine tools can achieve the processing of these materials, meeting the high-precision parts requirements of aerospace |
The future of CNC machining in the aerospace industry
TREND | CONTENT |
Automation and digitization have become trends | Artificial intelligence, machine learning and other technologies have pushed CNC machining towards a more automated and digital direction, with the use of robots, artificial intelligence (AI), and machine learning (ML) algorithms achieving real-time data monitoring and adaptive machining processes. This will further improve the efficiency and quality of aerospace manufacturing processes. |
Processing of high-precision and complex parts | Aerospace applications typically require complex and highly specialized components with challenging geometric shapes. And CNC machining meets these needs with its high precision, high efficiency, and high flexibility. |
Materials Innovation | The aerospace industry is increasingly utilizing advanced materials and composite materials, such as high-strength aluminum alloys, titanium alloys, carbon fiber composite materials, etc., to produce lighter, stronger, and more durable aviation parts. |
Integrated with 3D printing | Combining additive manufacturing (3D printing) with traditional CNC machining can produce complex parts with unique geometric shapes that were previously impossible to produce or had high manufacturing costs. |
Choose Longsheng to provide services for your CNC machining aerospace project
As an international high-end OEM/ODM manufacturer, Longsheng has nearly 15 years of development experience. We process CNC parts with a tolerance of up to 0.005mm, quote on the same day, and deliver within 72 hours. We have produced over 80000 different quantities of different parts. Our goal is to provide high-quality and efficient metal parts processing services for prototype design and mass production customers. We have processes such as CNC milling, CNC turning, 5-axis CNC machining, and surface treatment. We understand that the aerospace industry has extremely high reliability and quality requirements for components, so we strictly adhere to quality standards to ensure that the produced components meet industry performance and safety standards. Whether you are developing new aircraft components or need to update and improve existing ones, Longsheng has the ability to meet your needs.
conclusion
Numerical control machining is extremely important for the aerospace industry, and at the same time, the needs of aerospace are perfectly aligned with the characteristics of numerical control machining. Numerical control machining can flexibly and repeatedly manufacture the parts required for aerospace, and the produced parts have an accuracy of up to 100% and no errors, meeting the high precision, high accuracy, and high reliability required for aerospace. In short, numerical control machining is one of the indispensable and important technologies in the aerospace industry.
FAQs
Do CNC machining aerospace components have special surface finish requirements?
Yes, to a certain extent, CNC machining can achieve extremely strict tolerances, thereby achieving various surface qualities that are often required for aerospace applications.
Is accuracy important when CNC machining aerospace parts?
Precision machining is an important aspect of producing aerospace parts. The production standards in this industry are very high, and the safety regulations for CNC machining of aircraft parts are also stricter.
What is important aviation machinery certification?
There are several major certifications within the industry that emphasize a commitment to excellence and compliance in the aerospace industry.
- AS9100: If your company provides or manufactures aerospace machinery and parts, the AS9100 standard lists specific quality system management requirements to ensure that you provide the highest quality service to customers and customers.
- AS9110: The AS9110 standard is a set of requirements for aerospace maintenance stations. Although it contains roughly the same content as AS9100, it provides multiple specific standards for the maintenance and repair of aircraft machinery.
- AS9120: The AS9120 standard is an updated version of AS9100, designed and developed specifically for organizations in the aviation, military, and aerospace industries.
- AS6081: In the aerospace industry, suppliers selling fraudulent or counterfeit parts and equipment can pose significant risks to organizations. The AS6081 standard reduces these risks by simplifying the requirements of procurement, inspection, and management processes.