Have you ever wondered about how CNC machining costs are calculated? Why are some larger machined parts cheaper than smaller machined parts?
This guide answers your questions!
From the aerospace to the automotive industry, clients want affordable machining prices that do not compromise quality. Therefore, we explain factors that affect costing and how to calculate CNC machining costs. We also discuss practical tips to keep your next CNC machined parts order affordable.
Understanding CNC Machining and its costing
CNC stands for Computer Numerical Control. Hence, CNC machining is the process of running automated or computer-controlled machines on a set of pre-programmed prompts to carry out precision manufacturing tasks.
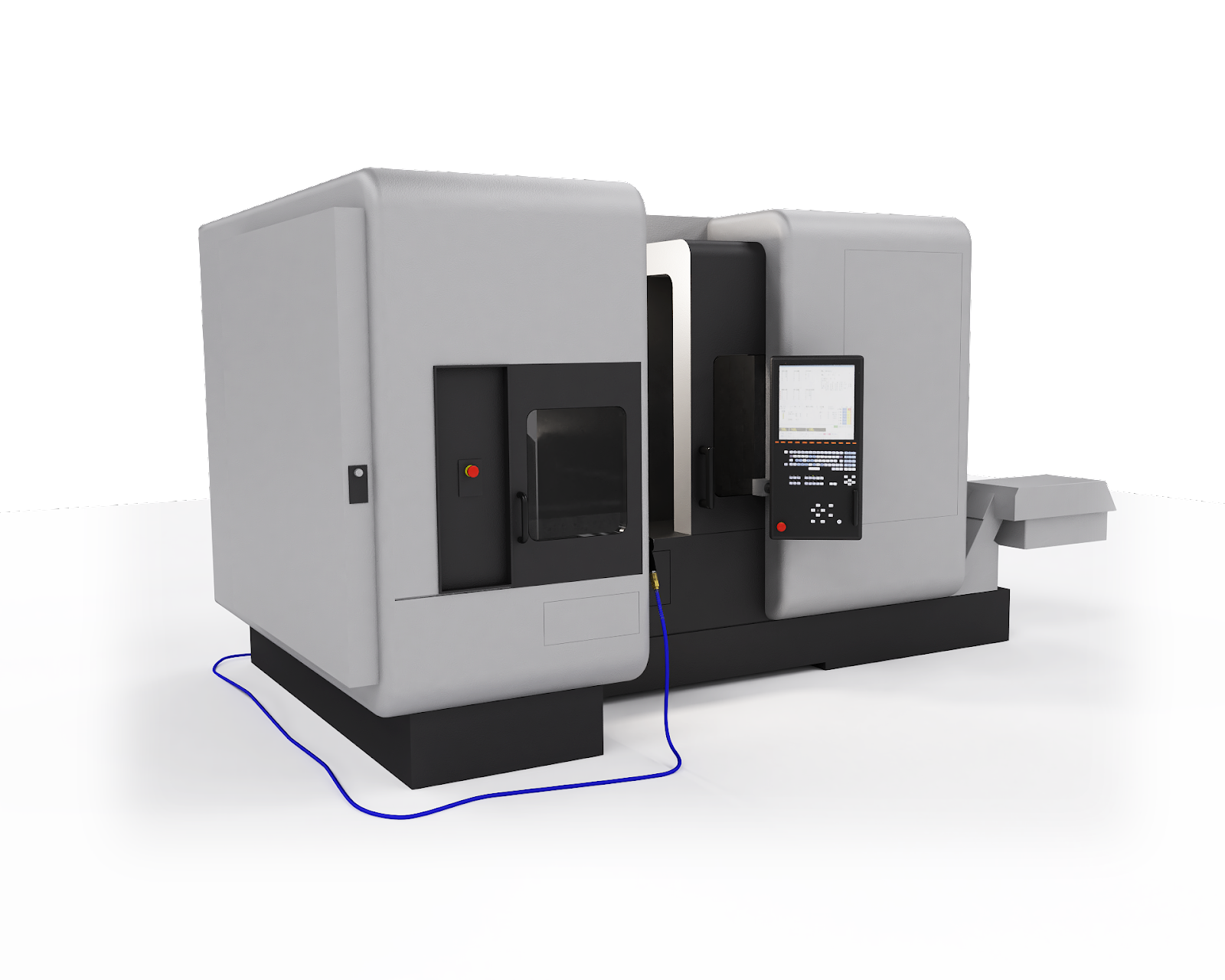
Production processes like cutting and shaping are performed in less time and with greater accuracy using CNC machines. In addition, CNC machining jobs only require a single line of code for some multiple processes.
These explanations illustrate that CNC machining is high-tech and might include some intrinsic cost planning. Let’s check out those factors that influence the cost of CNC machining.
Factors that determine CNC Machining costs
Learn about the factors affecting the final pricing of CNC machined parts. A proper understanding of these factors would later help to calculate CNC machining costs.
1.Materials
The choice of materials is an essential part of the machining cost process. Manufacturers consider parameters like type of raw material, machinability, quality, quantity, and availability. They also calculate raw material costing per-block basis before cutting into layers since CNC machining is subtractive, unlike 3D printing.
In addition, the primary materials for CNC machining projects are metals and plastics. Machinists commonly use the 6061/6063 aluminum plate series for metals because of their excellent machinability at budget-friendly prices.
7075 aluminum also works when a higher strength-to-weight ratio is required. Alternatively, Brass C360 and 303 Stainless steel have better machinability but subsequently higher costs.

Conversely, plastics could be substitute budget picks if pricing and faster machinability are the ultimate concerns. Plastics like Nylon, polyacetals (DELRIN), acrylic, and ABS are all great choices with good machinability. Polyetheretherketone (PEEK) is another excellent option but very expensive and only recommended when common plastics do not fit the project.
2.Setup & programming
Setup and programming are the next factors that determine CNC machining cost calculation. Setup involves the time spent configuring the machines for a new CNC machining project. Moreover, it could be the difference between different small-scale orders with separate setup costs and a single bulk order.

Other intrinsic considerations are the designer who prepares the CAD and the programmer who later converts to CAM. Some companies outsource to professionals at an extra cost. We also include the cost of the manufacturing engineer responsible for vetting the initial CAD for practical feasibility.
3.Labor
Since CNC machines’ processes are automated, one might wonder why labor is essential for calculating CNC machining costs. Lesser staffing is required, so why should labor costs count?
Regardless of the proposed machined part design, we already mentioned that you need a programmer and manufacturing engineer. Some CNC machine manufacturers might decide to outsource, depending on whether they have design and programming experts available.
However, they must consider training costs for their machine operators since the CNC manufacturing industry is fast evolving. Machinists must be up-to-date on the latest maintenance and production practices.
4.Machining and Tooling
Understand how to calculate CNC machining cost by estimating the total runtime of the machine for the year (in hours) and dividing by the CNC machine price. Also, include a percentage of the cost of special tool bits to cover for possibilities of wear out.

The CNC machining type and tooling required impact the setup budget and overall CNC machining prices. For example, a part with complex design and features can require 3 to 4 setups on a 3-axis machine. In contrast, a multi-axis machine like the 5-axis for the same machined part takes just 2 setups.
Of course, multi-axis machines have a higher machining cost per hour rate starting from $25/hr in Europe. However, you can obtain the same precision quality at only $8/hr (CNY55/hr) from a leading Chinese manufacturer like Longsheng.
5.Parts design & geometry
Complex CAM designs consume more time and have higher prices than simpler and less intricate drawings. Complex geometry also requires special toolings that might have to be custom-ordered, which is an extra cost.
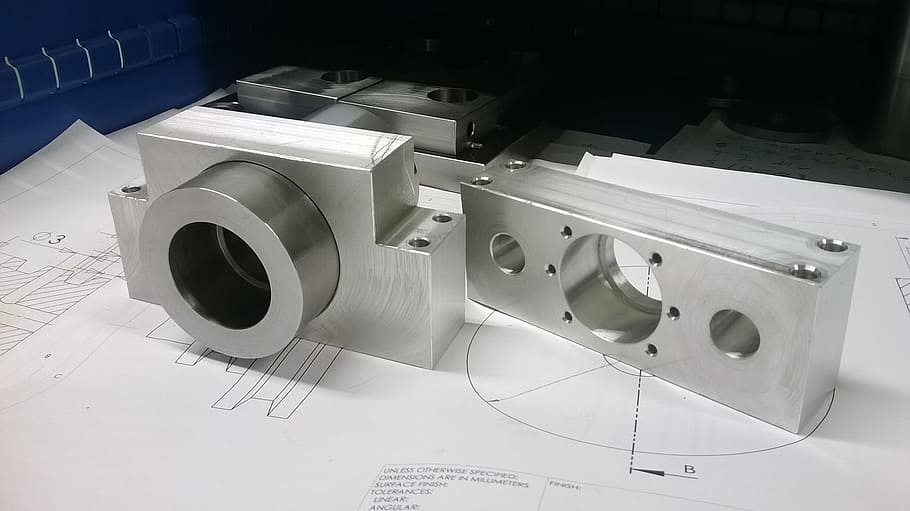
In addition, only specially trained operators can reproduce the design effectively. Therefore, choosing simple product designs and features is how to minimize CNC machining costs. You can even split the design into geometries for assembly with bolts instead of a single but complex structure.
6.Post-processing and finishing
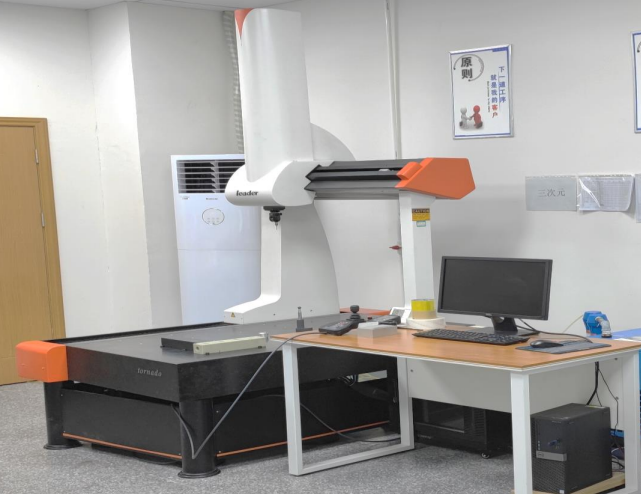
Even though post-processing and finishing count as extra costs, they are vital for optimal production quality. The post-processing stage involves conducting quality assurance inspections on the manufactured parts, cutting out excess materials, and testing the parts.
Subsequently, finishing entails different coating methods like powder coating, anodizing and bead blasts. Other miscellaneous expenses like packaging and transporting the manufactured parts fall in this category.
How to calculate CNC Machining cost?
While there is no fixed price for machining costs, some companies offer instant quotations to help with budget planning. However, we can determine the calculation process.
Firstly, a comprehensive CNC machining cost calculation formula would include the abovementioned factors. That implies the total cost of materials, setup & programming, labor, machining and tooling, parts design & geometry and post-processing.
Post-processing covers the costs of inspection, treatment, surface finishing, packaging and transportation. Similarly, we interpret the parts design & geometry as the cost of special toolings.
In addition, we must account for value loss through the wear and tear of special tools purchased/hired. That also includes hourly depreciation of the CNC machines and maintenance costs.
Therefore, we can express the machining cost formula as
CNC Machining Cost = Materials cost+Setup & Programming costs+Machining & Tooling costs
+ Labor costs+Cost of special toolings+Post Processing costs+Depreciation costs+Maintenance costs
Effective tips to minimize CNC Machining cost and keep it affordable
Did you get a cost quotation from your manufacturing company and think it is a little above your budget? Relax! This section explains how to reduce CNC machining costs without affecting desired quality.
1.Review your choice of material
Reconsider your material choice to help minimize CNC machining cost calculations. Are there cheaper alternatives with good machinability? Will you be compromising quality by going for a less expensive option?
While machinability is essential, you should opt for materials that offer an optimal mix of good machinability and low cost. The table below summarizes the average bulk cost for common metals/plastics.
Observe how aluminum 6061 would be preferred over stainless steel 303 despite the slightly higher machinability. Similarly, experts don’t recommend PEEK for simple plastic manufacturing because of its very high cost.
Plastics | Metals | ||
Type | Average Bulk cost | Type | Average Bulk cost |
ABS | $17 | Aluminum 6061 | $25 |
Polyacetals (Delrin) | $27 | Aluminum 7075 | $80 |
Nylon | $30 | Brass C360 | $148 |
Polyetheretherketone (PEEK) | $300 | Stainless steel 303 | $150 |
2.Simplify your design
Except it is absolutely necessary, avoid complicated design features if you want to reduce CNC machining cost calculations. The following are some essential design simplification tips to minimize costs.
– Include a radius for internal vertical edges
Adding a radius to the inside vertical edges lowers the machining time and subsequently minimizes CNC costs. We advise a constant radius for the different vertical edges with a value lesser than ⅓ of the depth.
– Avoid very thin walls
Correct machining of very thin walls takes longer durations because of their high susceptibility to vibrations and deformation. For metals, work within a thickness < 0.8mm and employ a thickness > 1.5mm for plastics.
– Limit depth of cavity
The recommended design depth for cavities is less than 4 times the diameter. Understand that CNC machining tools have limited cutting lengths. Therefore, unnecessarily deeper depths might require special tooling.
– Do not specify tolerance except it is absolutely necessary
Unspecified or standard tolerance values allow smooth machining that can reduce CNC machining cost. However, specified tolerance indicates more machining time and manual inspection. Standard tolerance is usually ±0.005’’.
– Do not add texts and lettering to CNC design
You can reduce CNC machining costs by excluding fonts and lettering that can slow down production. Instead, opt for engraved lettering options. You can also use alternatives like painting or silk screening.
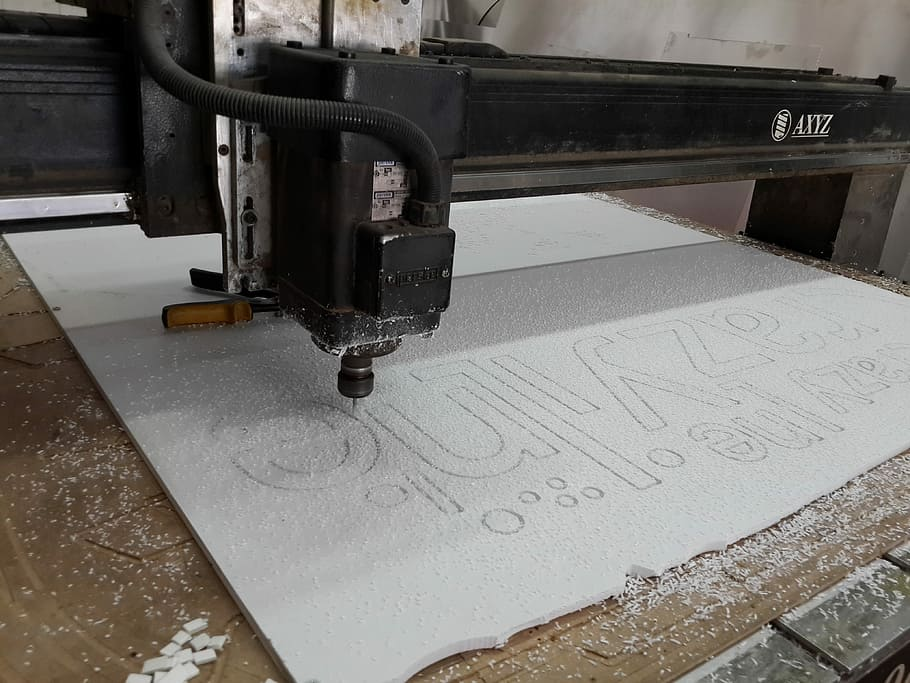
3.Optimize actual production time
Many shop owners only focus on the overall design process and ignore the critical assessment of the “actual” CNC production hours. Apart from the setup time, what percentage of the total production time does manufacture occur?
Improve that percentage by optimizing the cutting speeds, inlet rate of materials and choosing the correct tooling. In addition, regularly check the cooling system and ensure proper maintenance to avoid machine breakdowns that cause downtime in production hours.
4.Carry out larger production volumes
Shop managers who don’t know how to reduce CNC machining costs should try bulk purchases and large production volumes. A bulk order cuts down per unit cost, and setup cost is calculated once instead of differently for each production run. That implies profit maximization when you eventually subtract the production cost from revenue.
5.Optimize design tool paths
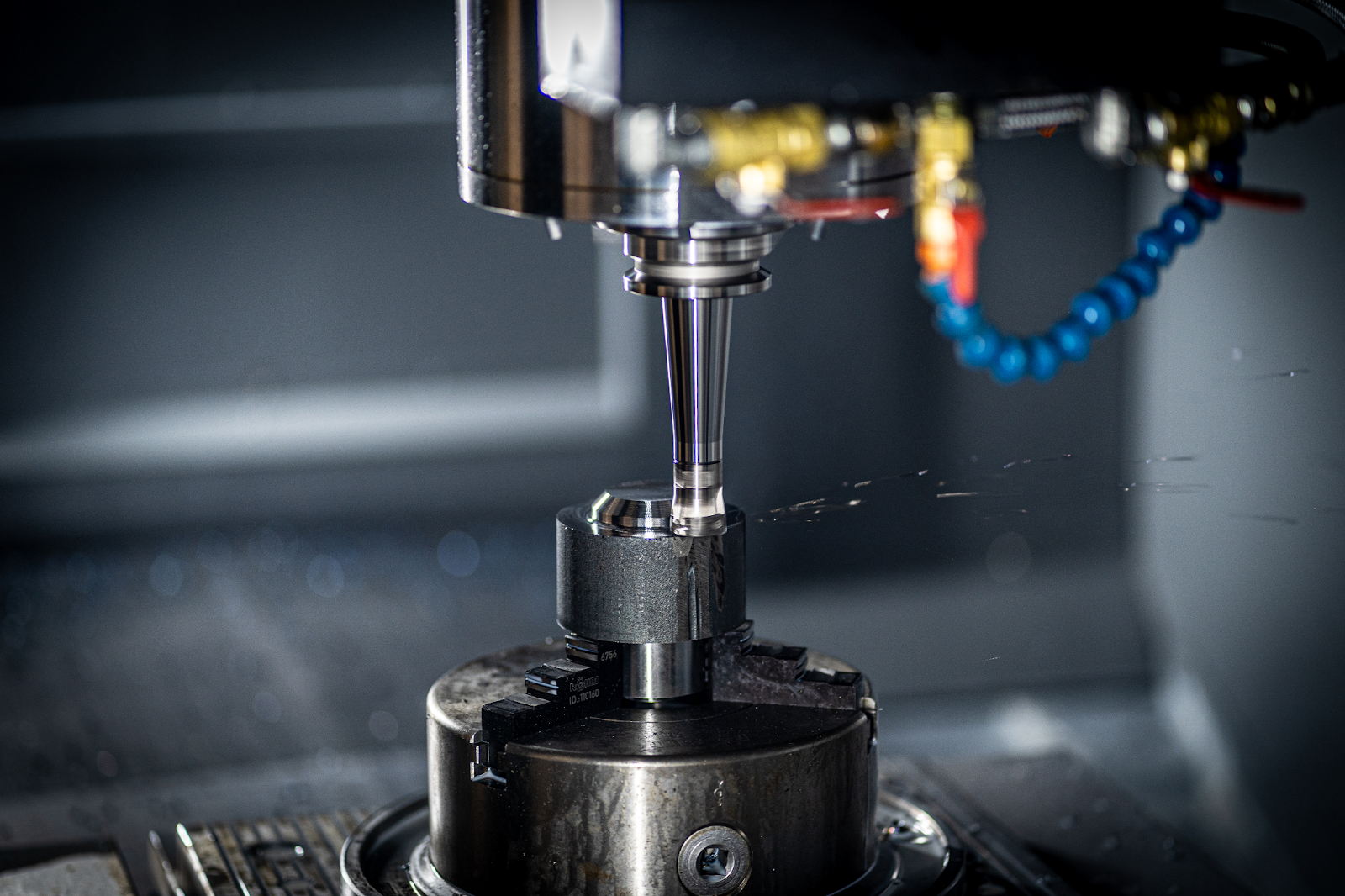
Does your CNC machine appear to cut more slowly than expected? Or could the surface finishing be much better? Optimizing the design tool path is what you need!
Start by selecting the correct tooling for separate CNC processes like milling, cutting or drilling. Correct tooling reduces the chance of wear and tear. Also, check for parameters like number of setups that affect the “actual” machining time.
6.Get a design software
Another practical tip to reduce CNC machining costs is getting reliable design software. Having one helps to assess the practicality of your design drafts and offers suggestions and improvements. Design software also helps with the material selection process, parts design & geometry, and optimization of design tool paths.
LONGSHENG: Get your quality CNC machine parts at the best prices
Are you still unclear about how to calculate CNC machining costs? Or do you feel your budget might not adequately get your desired parts?
Reach out to LongSheng today! We are a professional precision technical parts manufacturer with verifiable ISO 9001: 2015, ISO 14001: 2015, and IATF 16949 quality certifications.
You can also get an instant quote once you upload your CAD file. Whether it is prototype demand or mass-scale production, our team of experts is always ready to make your design ideas a reality. Quality is our watchword with exceptional customer service.
Frequently Asked Questions (FAQs)
The correct CNC machining cost calculation formula is in this guide. However, your final cost estimations would vary depending on whether it is a small-scale or large-scale production. For example, machining plus material for a $3 per part metal costs $103/unit at a $100 setup cost. However, the price per unit is $4 for 100 units produced.
Both manufacturing equipment are excellent and depend on the intended purpose. You should use CNC machining when smooth finishing is of utmost priority with high precision requirements.
Plastics and metals are the most commonly used materials, but alternatives like wood can fit for selected design features. Wood has excellent machinability, but plastics might work best for harsh environmental conditions. Contact us or reach out to your professional design experts for clarification.
The cost of CNC machining per hour ranges from $25/hr for 3-axis machines to $100/hr for 5-axis machines. However, Chinese manufacturers like Longsheng offer affordable rates starting from $8/hr. Costing is negotiable, especially for high-volume production projects.
Conclusion
This guide explains how to calculate CNC machining costs and practical tips to get top-quality and affordable parts. You can make Longsheng your sole supplier for machined parts if you need help with custom and durable designs. Get an instant quote for your next project now.