In recent years, the automotive industry has been booming and full of potential, one of the important catalysts is the continuous advancement of automotive technology, covering aspects such as engine systems, on-board electronics, body construction and so on. These technological advances also mean an increasing demand for precision sheet metal fabrication .
In this article, we will explore the automotive industry’s need for precision sheet metal fabrication and why precision manufacturing has a key role in automotive manufacturing. We will also highlight key manufacturing processes and commonly used sheet metal materials in the automotive industry. Read on to learn more.

introduce
The application of metal in automobile manufacturing has experienced a long evolution. The earliest cars used wooden chassis, which were soon replaced by steel due to limited strength and durability. Steel provides a stronger and safer structure. Over time, automobile manufacturers began to adopt sheet metal manufacturing techniques, further improving the strength and shape adaptability of automotive parts. In the late 20th century, aluminum alloy became a popular choice for the manufacture of hoods, bumpers, suspension arms and other components to reduce overall weight, improve fuel efficiency and crash safety.
In addition, carbon fiber is also emerging, due to its strength and stiffness in high-performance vehicles have been widely used, is expected to continue to develop in the future. In short, evolving materials technology plays a key role in the automotive industry, affecting vehicle performance, safety and sustainability.
The demand for precision metal fabrication in the automotive industry
The automotive industry has been constantly developing and evolving, and in order to meet the growing consumer demand and pursue higher performance and safety standards, the industry has a multifaceted demand for precision metal manufacturing. The following are some of the main demands for precision metal manufacturing in the automotive industry:
Lightweight design
Nowadays, car manufacturers are pursuing more fuel efficient and environmentally friendly cars. Lightweight design is the key to achieving this goal.
To achieve this, precision metal fabrication can provide lightweight but sturdy components, such as aluminum alloys, to manufacture the body and chassis. This makes the car lighter, more efficient in using fuel, and provides better performance.
High strength materials
We are all concerned about the safety of cars. So automotive components need to maintain stability and safety under various road conditions. Precision sheet metal fabrication can provide high-strength materials for manufacturing vehicle chassis, suspension systems, and airbags to ensure excellent performance in collisions and harsh road conditions.
Personalized configuration
Personalization is an important demand of modern consumers. We hope to have a unique car that reflects our own taste and style. Precision sheet metal fabrication provides manufacturers with customized solutions, allowing them to easily achieve appearance differences across different models and models. This includes different body colors, wheel hub designs, decorative strips, and interior options. Therefore, you can customize your car according to your personal preferences to make it unique.
Personalized configuration also includes the functionality and performance of the car. Through precision sheet metal fabrication , manufacturers can add or customize different functions according to user needs, such as advanced audio systems, navigation systems, seat materials, and interior decorations. This personalization makes cars more adaptable to personal needs, providing a more comfortable and enjoyable driving experience.
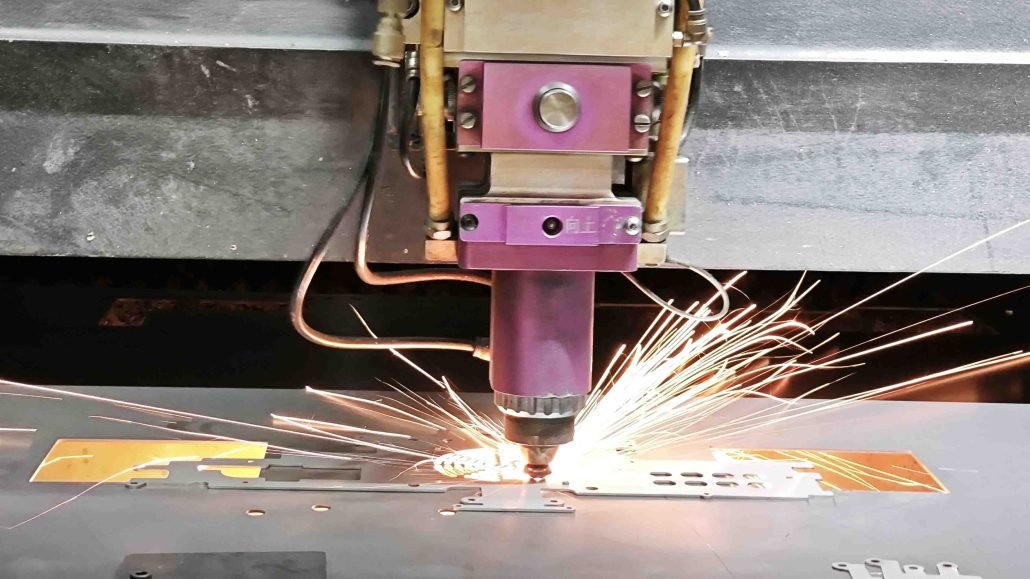
Electric vehicle technologies
Electric vehicles are the future trend, which requires lighter and more efficient battery and electric motor systems to achieve longer range and faster charging speeds.
Precision sheet metal fabrication is used to manufacture battery casings, motor components, and charging equipment, promoting the development of electric vehicle technology. The application of these technologies has made electric vehicles more practical and environmentally friendly, providing sustainable solutions for future travel.
customization
Car manufacturers need to customize between different models and models to meet the needs of different markets and consumers. Precision sheet metal fabrication can provide manufacturers with highly customized solutions, from exterior design to interior structure.
Automotive precision sheet metal fabrication process
In automotive manufacturing, sheet metal fabrication is a crucial process that involves a series of key steps to ensure that the car’s shell and structure can have high-quality, high-strength, and good appearance.
Material selection: the cornerstone of sheet metal
The first step in automotive sheet metal fabrication is material selection. Sheet metal materials must possess a series of characteristics, including corrosion resistance, strength, ductility, and processability. The following are commonly used sheet metal materials in automotive manufacturing:
1.Aluminum
Material of Choice for Lightweight Excellence: Aluminum is the go-to choice for applications requiring lightweight materials. Even in its unfinished state, this metal boasts impressive corrosion resistance.
Strength and Durability: Beyond its corrosion resistance, aluminum is well-suited for critical automotive sheet metal processes such as cutting, welding, and connecting.
Economic Viability: Aluminum comes in different grades with varying properties. It is known for its malleability, making it suitable for various manufacturing processes. Moreover, it offers cost-effective solutions.
2.Stainless Steel
Corrosion Resistance in Challenging Environments: Stainless steel is the ideal choice for manufacturing automotive enclosures and shells, especially for components exposed to moisture.
Versatile Formability: Stainless steel exhibits high formability, making it easy to process and shape for a variety of automotive parts.
High-Temperature Tolerance: It can withstand high-temperature environments, making it suitable for specific automotive applications.

3.Magnesium alloy
Magnesium alloy is commonly used in the manufacturing of wheels and is highly favored due to its lightweight characteristics and high strength. These wheels reduce the vehicle’s relentless weight and improve suspension performance.
4.Composite materials
Composite materials, such as carbon fiber reinforced plastic (CFRP), are used to manufacture high-performance automotive body panels and structural components. They combine lightweight and strength, providing excellent performance.
5.Copper Alloys
Superior Thermal Conductivity: Copper alloys are excellent choices for use in electronic components and heat exchangers within automobiles. Their superb thermal conductivity ensures efficient heat dissipation.
Outstanding Electrical Conductivity: Copper alloys offer low electrical resistance, making them ideal for use in automotive conductive parts.
High Malleability: These alloys are highly malleable, allowing for ease of processing and forming.
Forming: stamping and bending
The appearance and structure of cars require various shapes of sheet metal components, which require forming and bending. Sheet metal stamping and bending require high precision to ensure the quality and accuracy of the components. There are various methods for forming metal sheets, but the most common ones are stamping and bending.
Stamping is the process of placing sheet metal sheets on a punch and then using a punch to create the desired shape and holes. This is a common method for manufacturing automotive sheet metal components, such as door and window frames.
Bending is the process of clamping a sheet metal plate onto a bending machine and then using pressure to bend the plate to form the desired angle and curve. This is very common in the manufacturing of automotive chassis and body components.
Connection mode: welding, riveting and bonding
The various sheet metal parts in the car need to be connected together to build the structure of the vehicle. This involves joining methods such as welding, riveting and bonding.
Welding is a common method of joining sheet metal parts together by melting them at high temperatures. In automotive manufacturing, spot welding and laser welding are often used to join parts to ensure strong and long-lasting connections.
Riveting involves using rivets to hold sheet metal parts together and is a reliable method of connection. Riveting is commonly used to connect car body parts such as doors and hoods.
Bonding is a method of bonding sheet metal parts together using an adhesive. This method of connection is becoming more and more popular in automotive manufacturing because it can provide good structural strength and durability.

Surface treatment: spray paint, powder coating and electrophoretic coating
After connecting the individual sheet metal parts, the car needs to be finished to improve the appearance and protect the sheet metal parts. Spray paint, powder coating and electrophoretic coating are common surface treatment methods.
Painting can improve the appearance of the car while forming a protective layer to prevent corrosion and oxidation of sheet metal components and improve durability.
Powder coating is the application of dry powder to sheet metal surfaces to provide scratch, fade and corrosion resistance. This is widely used in the painting of automotive external parts.
Electrophoretic coating is a coating method in which the paint is uniformly attached to the sheet metal surface by an electrophoretic process. This method provides a uniform coating that improves surface quality and durability.
The application of sheet metal in automobile manufacturing
Sheet metal has a wide range of applications in automotive manufacturing, including various parts such as body, doors, hood, chassis, roof, interior and seats. These parts not only affect the appearance of the car, but also affect the performance, safety and durability of the car.
For example, the body and doors of a car need to be strong and corrosion-resistant to protect passengers and withstand various climatic conditions. The chassis needs to be stiff and strong enough to support the weight of the entire vehicle. The interior and seats need to be comfortable and aesthetically pleasing to provide riding comfort.
Longsheng’s high quality sheet metal fabrication for the automotive industry
In the field of automotive manufacturing, Longsheng is a highly respected sheet metal fabrication company. We have advanced equipment and an experienced team of professionals to provide automotive manufacturers with high quality sheet metal parts. Whether it’s prototyping or mass production, we can meet your needs.
In automotive manufacturing, quality is of Paramount importance and we have strict quality control measures and quality assurance processes in place to ensure that our sheet metal parts meet industry quality standards.
conclusion
Sheet metal plays a key role in automotive manufacturing, affecting the performance, appearance and safety of cars. Through precise cutting, forming, joining and surface treatment, automotive manufacturers are able to produce high-quality vehicles that meet the needs of consumers. If you need high-quality automotive sheet metal parts, please contact Longsheng, we will be happy to provide you with service.