The issue of sink mark is an important issue often encountered in injection molding. During the injection molding process, molten plastic is injected into the mold, filling the entire cavity. However, due to the shrinkage of plastic during the cooling process, a sink like depression is formed on the surface of the product, which is called a sink mark.
In this article, we will delve into the causes of sink marks and provide solutions such as optimizing mold design, adjusting injection parameters, selecting appropriate materials and processing methods. Through these methods, we can help better address the issue of sink marks, improve product quality and appearance.
Causes of sink mark in injection molding
In injection molding, the formation of sink mark is caused by a variety of factors. The following are the main reasons for the sink mark in injection molding:
Reason 1:Temperature and cooling inhomogeneity
During injection molding, plastic molten material is injected into the mold and gradually solidifies during cooling. However, due to the difference in cooling speed between the mold surface and the inside, as well as the temperature difference between different parts, the molten plastic will not shrink evenly during the cooling process, forming a flume shaped depression trace.
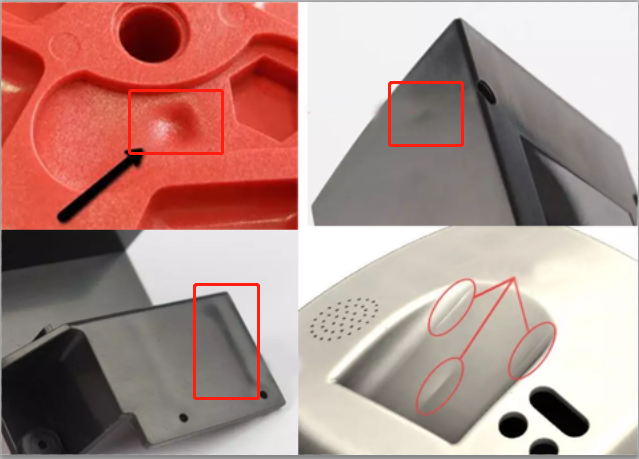
Reason 2:Effects of temperature differences and uneven cooling:
1.The formation of sink marks
temperature differences and uneven cooling can cause the molten plastic to shrink inevenly during cooling. The faster cooling area will produce a larger amount of shrinkage, forming a depression mark, that is, the sink mark.
2.Appearance defect
the sink mark makes the surface of the plastic parts appear uneven and concave traces. These marks will reduce the appearance quality of the product and affect the visual effect.
3.Size deviation
Temperature differences and uneven cooling can also lead to size deviation of injection parts. The inconsistent shrinkage of different parts will cause deformation of plastic parts in size, further affecting the quality of the product.
When controlling temperature differences and cooling inhomogeneity, the following temperature ranges need to be noted (the following is an example table) :
Injection molding part | Temperature range (℃) |
---|---|
Mold surface | 10 – 30 |
Cooling system | 5 – 20 |
Injection Unit | 180 – 250 |
Injection nozzle | 200 – 230 |
Plastic melting zone | 200 – 280 |
Different plastic materials have different melting temperatures and characteristics, and when selecting materials and setting injection molding parameters, the temperature range and control mode should be adjusted according to the requirements of the specific material to minimize the occurrence of sink marks.
Reason 3:Stress and liquidity differentials
Pressure differences can lead to uneven filling of plastics during injection molding. When the injection pressure is uneven or too high, the filling process of the plastic in the mold cavity will become uneven. Some areas may not be adequately filled, forming local depressions or sink marks.
In addition, during the injection molding process, the fluidity of the plastic is closely related to factors such as temperature and viscosity. When the fluidity of the plastic is different during injection molding, the filling process will become uneven. Some areas may have excessive flow, while others may be inadequately filled, leading to the formation of sink marks.
To solve the problem of sink mark caused by pressure and flow differences, we can optimize the injection parameters. Reasonably adjust the injection pressure, speed and time to ensure that the plastic is evenly filled in the mold and avoid the formation of hot spots.

Reason 4:Material selection and characteristics
Different plastic materials have different thermal properties and fluidity requirements, which will also have an impact on the formation of sink marks. The selection of materials should consider factors such as melting point, thermal conductivity, fluidity and shrinkage rate
Thermal properties: The thermal properties of plastics include aspects such as melting temperature and thermal conductivity. The lower the melting temperature, the plastic can become a flow state at a lower temperature, which is easy to fill the mold cavity, but also increases the risk of sink marks.
Fluidity requirements: Different injection molding materials have different fluidity requirements, including viscosity, flow speed and consistency of flow. Better flowing plastic fills the mold more evenly, reducing the risk of sink marks.
Suitable plastic material
·Polypropylene (PP)
·High density polyethylene (HDPE)
·Polystyrene (PS)
·Polycarbonate (PC)
·Nylon (Nylon)
·Polyvinyl alcohol (PVA)
·Polymethyl methacrylate (PMMA)
·Polyphenylene sulfide (PBT)
Solution 1:Optimize mold design
Die design principle
Reducing factors such as size differences and thickness variations can reduce the formation of sink marks. The mold design should consider the structural characteristics of the product and reasonably design the geometric shape and size of the product
Design consistent wall thickness
In the mold design, try to keep the wall thickness of the product consistent. Differences in wall thickness in different areas can lead to different cooling rates, resulting in dimensional changes and stress concentration. Through reasonable design and material selection, the wall thickness of the product is as uniform as possible, which helps to reduce dimensional differences and deformation.
1.Control size variance
Size difference refers to the size deviation of the product during the injection molding process. In order to reduce the size difference, consider the following aspects:
Control the thermal shrinkage of materials: different plastic materials have different thermal shrinkage rates, so the thermal properties of materials should be taken into account in the mold design, and the mold size should be reasonably adjusted to compensate for the size change caused by thermal shrinkage.
2.Reasonable cooling system design
The design of the cooling system is important to control size differences. By providing a cooling channel in the mold, the cooling medium can uniformly cool the product and reduce the size difference.
3.Control mold temperature
The control of mold temperature is also very important to reduce dimensional differences. By adjusting the mold temperature, the cooling rate and shrinkage rate of the product can be affected, thereby reducing the size difference.
4.Reduce thickness variation
In mold design, try to avoid sudden changes and drastic changes in product thickness. Excessive thickness changes can lead to a difference in cooling rate, which in turn causes the formation of injection molding sink marks. Through reasonable design and material selection, the thickness of the product changes as gently and evenly as possible.
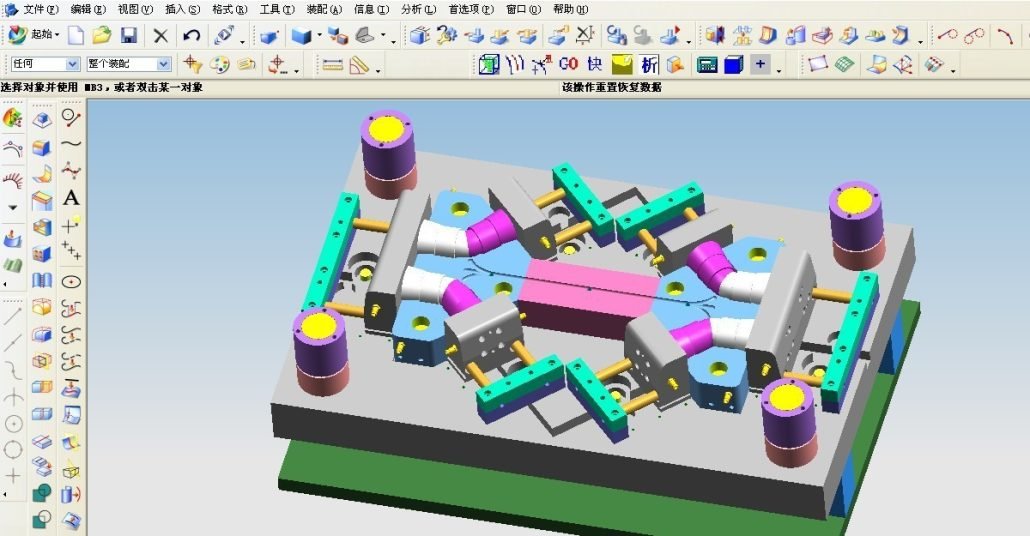
Avoid too thin and too thick parts
Too thin and too thick parts tend to form sink marks. Too thin part is easy to produce surface shrinkage, forming a sink mark; The cooling speed of the too thick part is slower, and it is also easy to form a sink mark. Therefore, the existence of too thin and too thick parts should be avoided in the mold design. There are several ways to solve this problem:
1.Mold design optimization
In the design phase, a reasonable structural assessment is carried out and the design of the product is ensured to meet the requirements of mold manufacturing and injection molding.
Reasonable selection of mold materials, taking into account its thermal conductivity and thermal expansion coefficient, in order to reduce the impact of temperature and cooling non-uniformity.
In the design process, CAD/CAM software is used for 3D modeling of the mold structure and mold flow analysis to help optimize the design and avoid the production of too thin and too thick parts.
2.Material selection and fluidity considerations
Select the right plastic material, taking into account its thermal properties and fluidity requirements. Some materials are more likely to produce sink marks, so their flow and shrinkage properties should be considered when selecting materials.
Consider using additives or modifiers to improve the fluidity and heat conductivity of the material.
3.Mold manufacturing quality control
In the process of mold manufacturing, the processing technology and quality are strictly controlled to ensure that the size and shape of the mold meet the design requirements.
Use high-precision machining equipment and processes to reduce dimensional differences and thickness variations.
Inspect the mold regularly and repair any damage or wear that may cause the parts to be too thin or too thick.
4.Mold cooling system design
Design an effective cooling system to improve cooling efficiency and uniformity during injection molding.
The cooling channel is reasonably arranged in the mold to ensure that the cooling medium can fully cover the surface of the mold and reduce the temperature evenly.
Use a suitable cooling medium, such as water or oil, according to the specific requirements and material properties to choose the appropriate cooling medium.
5.Injection parameter adjustment
By reasonably adjusting the injection speed and pressure, it is ensured that the molten plastic can evenly fill the mold cavity and avoid the formation of too thin and too thick parts.
Consider using a multistage injection process to control the flow behavior of the molten plastic, thereby reducing the thin and thick parts.
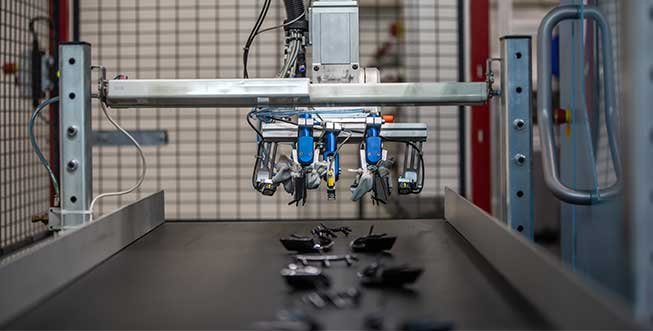
Cooling system design
Here are some tips on how to design an effective cooling system to improve cooling efficiency during injection molding, reduce product surface temperature, and reduce sink marks:
1.Cooling channel layout
In the mold design stage, the cooling channel is reasonably arranged so that it can cover the entire mold surface and have good contact with the mold.
Additional cooling channels are added to the thin-walled parts of the mold and areas prone to sink marks to enhance the cooling effect.
Adopt a reasonable cooling channel layout to avoid channel crossing and dead corners to ensure that the cooling medium can flow evenly.
2.Cooling channel size and diameter
The size and diameter of the cooling channel should be designed according to the heat transfer requirements during the injection molding process and the structural characteristics of the mold.
In areas requiring high cooling efficiency, a smaller diameter cooling channel is used to increase the contact area between the cooling medium and the mold surface and improve cooling efficiency.
For larger molds, consider increasing the number and density of cooling channels to provide adequate cooling capacity.
3.Cooling medium selection
Select the appropriate cooling medium, such as water or oil, according to the specific injection molding process and material requirements.
Water is a common cooling medium with high thermal conductivity and low cost, suitable for most injection molding applications.
For high temperature injection molding or special materials, it may be necessary to use oil or other high temperature cooling media to meet the requirements.
4.Cooling medium flow and pressure control
Ensure that the flow and pressure of the cooling medium can meet the requirements of the injection molding process.
Excessive flow may cause the cooling medium to be unable to fully absorb heat, while too small flow will reduce the cooling effect.
Adjust the flow and pressure by adjusting the flow control valve of the cooling system or increasing the power of the cooling medium pump.
5.Temperature control
During the injection molding process, the temperature of the mold surface is adjusted by controlling the temperature of the cooling medium.
Reduce the temperature of the cooling medium in areas where better cooling is required.
Devices such as thermostats or cooling towers can be used to control the temperature of the cooling medium.
6.Thermal runaway detection
Install equipment such as temperature sensors or infrared thermometers to monitor temperature changes on the mold surface.
When the mold surface temperature rises abnormally, timely detection and adjustment of the cooling system to avoid the production of sink marks.
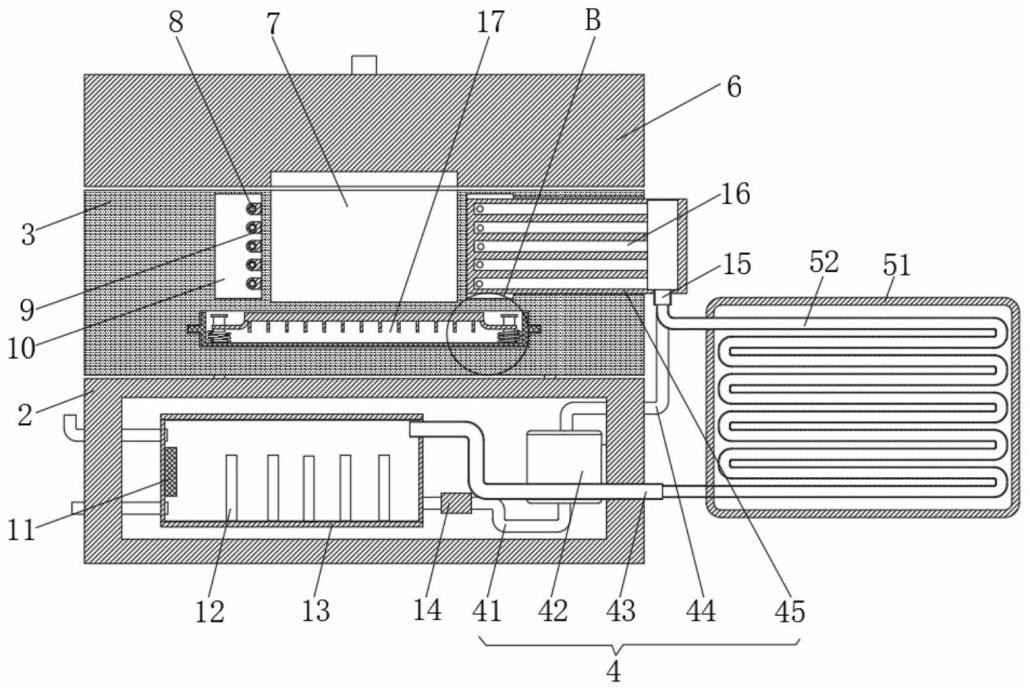
Solution 2:Injection parameter adjustment
Injection speed and pressure control
The following are suggestions on how to adjust injection speed and pressure in detail to reduce the impact of molten plastic during injection and reduce the formation of sink marks:
1.Adjustment of injection speed
Low injection speed in the initial stage: In the initial stage of the beginning of the injection, the injection speed is reduced, so that the molten plastic gradually enters the mold cavity, reducing the impact force and pressure gradient, thereby reducing the generation of sink marks.
Control the speed change in the intermediate stage: In the intermediate stage of filling the mold cavity with molten plastic, the injection speed is gradually increased to ensure full and uniform filling, avoid cavities and short shots, and reduce the impact force.
Reduce the speed at the end stage: near the end stage of filling the mold cavity, gradually reduce the injection speed, so that the molten plastic is filled smoothly, reduce the impact force too fast, and avoid the generation of sink marks.
2.Pressure adjustment
Low pressure control in the initial stage: In the initial stage of injection, lower injection pressure is used to avoid the impact of instantaneous high pressure on the mold and reduce the formation of sink marks.
Gradually increase the pressure: During the process of filling the mold cavity with molten plastic, the injection pressure is gradually increased to ensure full and uniform filling.
Control the maximum pressure: Avoid too high injection pressure to prevent the molten plastic from producing too much impact during the injection process, resulting in the formation of sink marks.
Reduce the pressure at the end stage: near the end stage of filling the mold cavity, gradually reduce the injection pressure, so that the molten plastic is smoothly filled, reducing the impact impact on the mold.
3.Adjustment of injection speed and pressure
The adjustment of injection speed and pressure is the key, which needs to be optimized according to the actual situation during the injection process.
The relationship between injection speed and pressure should be kept coordinated, and when the injection speed is low, the corresponding injection pressure should also be reduced accordingly to avoid excessive impact force caused by too high pressure.
Temperature regulation and matching
Here are some tips on how to ensure temperature regulation and matching to avoid excessive temperature differences leading to sink mark problems:
1.Mold temperature control system
The use of accurate temperature control system: the use of high-precision mold temperature control system to ensure the stability and accuracy of mold temperature. The temperature control system should be able to precisely control the heating and cooling process of the mold to avoid temperature fluctuations and differences.
Uniformly distributed temperature control device: Arrange uniformly distributed temperature control device in the mold, such as hot oil circulation system or temperature control waterway. This ensures uniform temperature throughout the mold surface and reduces sink marking problems caused by temperature differences.
2.Heating and cooling processes of molten plastics
Ensure preheating of the molten plastic: Preheat the molten plastic to the appropriate injection temperature before the injection process begins. This ensures that the temperature of the molten plastic matches the mold temperature and reduces the impact of temperature differences on the sink marking.
Control the cooling rate of molten plastic: After the injection process, the cooling rate of molten plastic is adjusted by controlling the cooling time and the flow rate of the cooling medium. The proper cooling time and cooling rate can reduce the temperature gradient on the surface of the molten plastic and avoid the formation of sink marks.
3.Temperature analysis and optimization
Perform temperature analysis: Use tools such as thermal imagers to perform temperature analysis of molds and molten plastics to detect temperature distribution and differences. By analyzing the temperature data, it is determined whether there are areas with large temperature differences, and timely measures are taken to adjust and optimize.
Optimize the temperature setting: According to the results of the temperature analysis, the temperature setting of the mold and molten plastics is optimized. Adjust the parameters of the temperature control system to ensure that the temperature of each part of the mold is uniform and matches the temperature of the molten plastic.
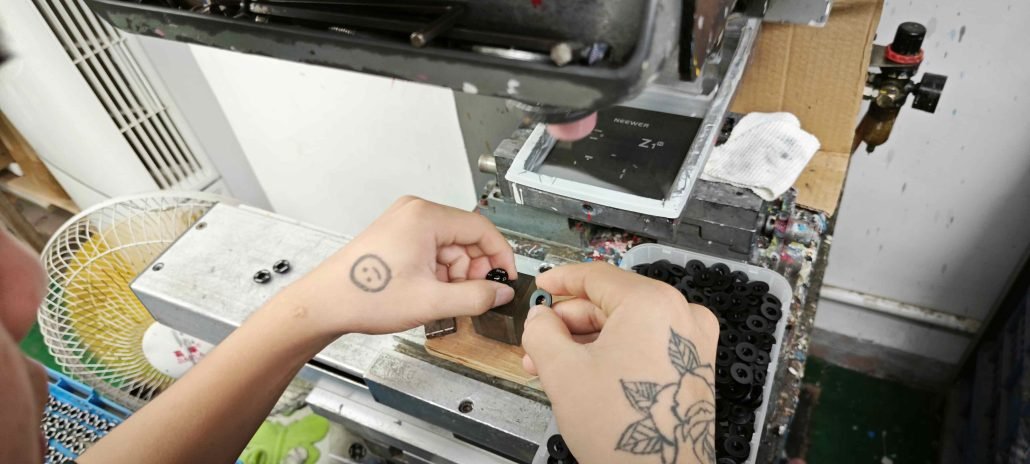
Injection cycle control
Control the injection cycle to ensure the stability of the injection process to help reduce the production of sink marks. Here are some tips on how to control the injection cycle:
1.Injection time control
Determine the appropriate injection time: Determine the appropriate injection time based on the size, shape and material characteristics of the product. The injection time should fully ensure that the molten plastic fills the entire mold cavity, and avoid excessive overheating and molten plastic flow due to too long injection time.
Control injection speed curve: The design of injection speed curve also affects the control of injection cycle. The proper injection speed curve can smoothly push the molten plastic into the mold cavity, reducing the impact force of the molten plastic and the generation of sink marks.
2.Injection pressure control
Determine the appropriate injection pressure: Determine the appropriate injection pressure according to the melting characteristics of the material and the requirements of the product. Proper injection pressure can ensure the smooth entry of molten plastic into the mold cavity, and avoid excessive injection pressure resulting in molten plastic overflow and sink marks.
Control of the pressure curve: The design of the pressure curve during injection is also critical to the control of the injection cycle. A reasonable pressure curve can smoothly push the molten plastic into the mold cavity, avoid pressure spikes and abrupt changes, and reduce the formation of sink marks.
3.Cooling time control
Determine the appropriate cooling time: Determine the appropriate cooling time based on the size of the product, the thickness and the thermal properties of the material. The cooling time should fully ensure that the molten plastic is fully cured and cooled in the mold, and avoid too short cooling time leading to incomplete product release and the production of sink marks.
Optimize cooling system design: Design an effective cooling system to ensure that the cooling medium flows evenly and covers the entire mold surface, improving cooling efficiency. A proper cooling system can help reduce the surface temperature of the product and reduce the formation of sink marks.
4.Injection cycle monitoring and optimization
Use monitoring equipment: Install appropriate injection process monitoring equipment, such as temperature sensors, pressure sensors, etc., to monitor key parameters such as temperature and pressure during the injection cycle in real time. These monitoring data can provide feedback to help engineers understand changes and anomalies in the injection molding process, adjust and optimize injection molding parameters in a timely manner, and reduce the generation of sink marks.
Injection process optimization: Through experiments and data analysis, optimize injection process parameters, such as injection speed, pressure, temperature, etc., to improve the stability and consistency of the injection process. Continuous optimization of process parameters can reduce the impact force of molten plastics and the formation of sink marks.
Solution 3:Material selection and processing
Thermal performance and flowability requirements
Choosing the right material can effectively reduce sink marks problems. The following are recommendations regarding thermal properties and fluidity requirements for material selection and handling:
1.Thermal performance requirement
Melting temperature: Different materials have different melting temperature ranges. Choosing a material with a lower melting temperature can reduce the accumulation of heat energy and the fluidity of the molten plastic during the injection molding process, thus reducing the generation of sink marks.
Thermal conductivity: The thermal conductivity of the material affects the cooling rate of the molten plastic during injection molding. Choosing a material with a higher thermal conductivity can speed up the cooling of the molten plastic and reduce the formation of sink marks.
2.Liquidity requirement
Viscosity: Different materials have different viscosity characteristics. Choosing a material with a lower viscosity allows the molten plastic to flow more easily, reducing the production of sink marks.
Fluidity Index (MFR/MFI) : The fluidity index is a measure of the fluidity of a material, which represents the flow of a material through a standard aperture in a unit time. Selecting a material with an appropriate fluidity index can ensure the uniform flow of molten plastic during injection molding and reduce the formation of sink marks.
When selecting materials, it is necessary to consider the requirements of the product and the characteristics of the injection molding process. For products that need to avoid sink marks, it is generally recommended to choose materials with the following characteristics:
High fluidity: has a low viscosity and appropriate fluidity index to ensure the uniform flow of molten plastic during injection molding.
Low melting temperature: has a lower melting temperature range to reduce heat accumulation and the flow of molten plastic, reduce the generation of sink marks.
Excellent thermal conductivity: With high thermal conductivity, it can speed up the cooling rate of molten plastics and reduce the formation of sink marks.
In addition, in the processing of materials, the following matters should also be noted:
Reasonable melting temperature control: According to the melting characteristics of the material and the requirements of the injection molding process, the heating and cooling process of the melting temperature is controlled to ensure that the temperature of the molten plastic matches the mold temperature.
Effective drying treatment: For some materials that are easy to absorb moisture, adequate drying treatment is needed to reduce the impact of moisture on the injection molding process and product quality.
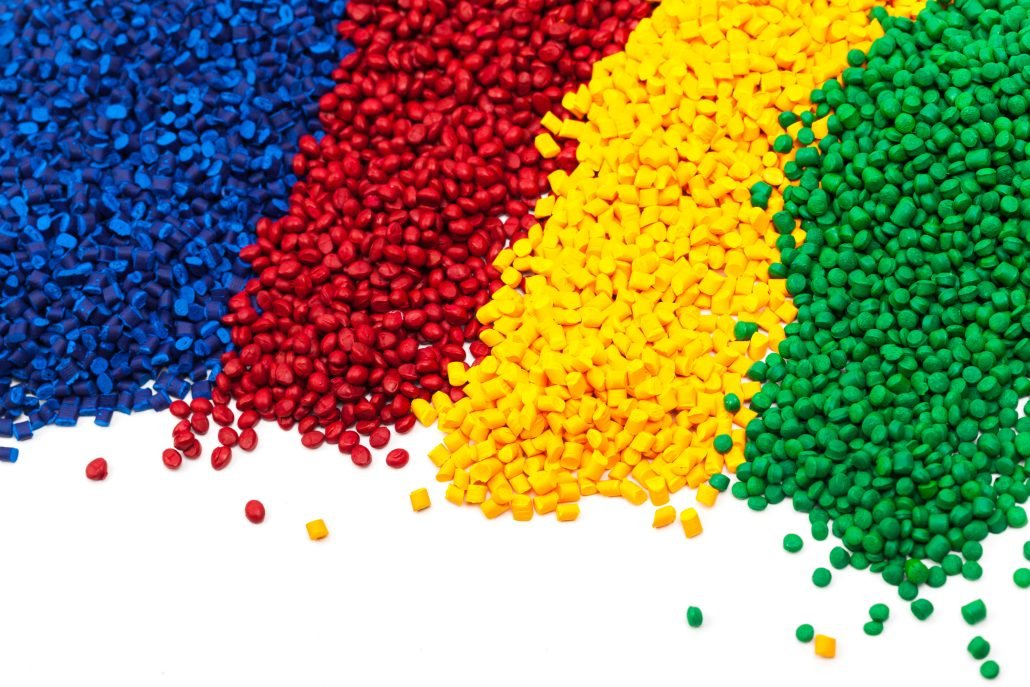
Selection and characteristics of plastic materials
Different types of plastic materials have their own characteristics and advantages and disadvantages. The following is an analysis of the characteristics of commonly used plastic materials and their advantages and disadvantages in reducing sink mark:
1.Polypropylene (PP)
Characteristics: Polypropylene is a plastic material with good fluidity and low melting point. It has good heat resistance, chemical stability and mechanical strength.
Advantages: Polypropylene has a lower melting temperature, which reduces heat accumulation and fluidity, thus reducing the production of sink marks. It also has good fluidity, which is conducive to the uniform flow of plastics in the injection molding process.
Disadvantages: Due to the low melting point and fluidity of polypropylene, for some complex product structures, more cooling time may be required to avoid the formation of sink marks.
2.Polyethylene (PE)
Characteristics: Polyethylene is a common plastic material with good heat resistance, chemical stability and mechanical strength. It can be divided into high density polyethylene (HDPE) and low density polyethylene (LDPE).
Advantages: The melting temperature of polyethylene is relatively low, which can reduce heat accumulation and flow, helping to reduce the generation of sink marks. Polyethylene also has good fluidity, which is conducive to the uniform flow of plastics during injection molding.
Disadvantages: The high fluidity of polyethylene is easy to produce thermal shrinkage and deformation, and attention needs to be paid to the cooling process and mold design to avoid the formation of sink marks.
3.Polystyrene (PS)
Characteristics: Polystyrene is a commonly used transparent plastic material with high rigidity and good optical properties.
Advantages: Polystyrene has a lower melting point, which helps reduce heat accumulation and fluidity, reducing the production of sink marke. Its fluidity is good, which is conducive to achieving better filling and uniform flow during injection molding.
Disadvantages: Due to the rigidity and transparency of polystyrene, it is easy to form sink marks for some complex shapes and thin-walled products. Special attention is needed in mold design and cooling system design.
4.Polycarbonate (PC)
Characteristics: Polycarbonate is an engineering plastic with excellent mechanical strength, thermal stability and transparency.
Advantages: Polycarbonate has a higher melting point and lower thermal shrinkage, which helps reduce the formation of sink marks. It also has good fluidity, which is conducive to achieving uniform plastic flow.
Disadvantages: Due to the high melting point and viscosity of polycarbonate, cooling control during injection molding is required to avoid the formation of sink marks.
Effects and use of additives
Additives are chemicals added to the base plastic during plastic processing that can change the properties of the plastic and improve its fluidity. Here are some common additives and their effects on plastic properties and fluidity:
1.plasticizer
Impact: Plasticizers can increase the flexibility and ductility of plastics, reduce their glass transition temperature, and improve fluidity.
Applicable materials: Often used in rigid plastics such as polyvinyl chloride (PVC).
2.stabilizer
Impact: Stabilizers protect plastics from thermal oxidation and light degradation, extending their service life.
Applicable materials: Commonly used in plastics that are susceptible to heat and light, such as polyethylene (PE), polypropylene (PP) and polycarbonate (PC).
3.Toughening agent
Impact: Toughening agent can increase the toughness and impact resistance of plastics, improve its heat resistance and mechanical strength.
Applicable materials: Often used in brittle plastics such as polypropylene (PP) and polystyrene (PS).
4.filler
Impact: Fillers (such as glass fiber, carbon fiber, etc.) can increase the strength, rigidity, and heat resistance of plastics, but may also reduce their fluidity.
Applicable materials: Often used in engineering plastics requiring higher strength and rigidity such as polyamide (PA) and polyester (PET).
5.lubricant
Impact: Lubricants reduce the viscosity of plastics and improve their fluidity and processability.
Applicable materials: Often used in high-viscosity plastics such as polypropylene (PP) and polyethylene (PE).
6.Flame retardant
Impact: Flame retardants can improve the flame retardancy of plastics and reduce the risk of fire.
Applicable materials: Commonly used in flammable plastics such as polyurethane (PU) and polycarbonate (PC).

conclusion
By implementing these methods and technologies, we can effectively reduce sink markings, improve product quality, reduce scrap rates, and meet customer requirements. However, in different cases, you can adjust and modify according to your own needs and specific circumstances.
Longsheng Technology: Your Best Injection Molding Supplier
If you are looking for the best injection molding supplier, Longsheng Technology is the wise choice for you. We provide our customers with DFM analysis free of charge to ensure that defects such as indentation do not damage the appearance of your product.
Please contact our sales team and we will be happy to provide you with the best solution and the best quality products.
gloria.wu@longshengmfg.com
FAQ
Sink marks can be predicted using injection molding simulation software. By analyzing the part design, material properties, and process parameters, simulation software can help identify potential sink mark areas and provide insights into how to address them.
While it may not always be possible to eliminate sink marks entirely, they can be minimized to acceptable levels through proper design, process optimization, and material selection. The goal is to reduce sink marks to a level that does not affect the functionality or appearance of the part.