Metal stamping is a widely used manufacturing process in various industries, known for its ability to cut, shape, and form metal into specific parts and components. Despite its many advantages, including high accuracy and repeatability, it also has some significant disadvantages that businesses must consider. This article will examine the main disadvantages of metal stamping and common problems that can affect the quality and reliability of stamped parts.
What are the Disadvantages of Metal Stamping
Metal stamping is a widely used manufacturing process in many industries, including automotive, aerospace, and electronics. It involves the use of machines to cut, shape, and form metal into specific parts and components. While metal stamping has many advantages, it also comes with some disadvantages. In this article, we will discuss the main disadvantages of metal stamping.
1. Tooling Costs
One of the major disadvantages of metal stamping is the high tooling costs. Tooling refers to the specialized equipment and tools used to cut and shape metal. The cost of tooling can be significant, especially for small production runs. This makes metal stamping less cost-effective for small businesses and startups.
2. Design Limitations
Another disadvantage of metal stamping is the design limitations. The stamping process can only produce parts with certain shapes and sizes. Complex shapes and designs may not be possible with metal stamping. This can limit the creativity and innovation of product designers.

3. Material Limitations
Metal stamping is also limited by the types of materials that can be used. The process is best suited for metals such as steel, aluminum, and copper. It may not be suitable for other materials such as plastics or composites. This limits the versatility of metal stamping in certain industries.
4. Production Time
Metal stamping can also be time-consuming. The process involves many steps, including tooling setup, material handling, and part inspection. This can result in longer production times compared to other manufacturing processes. This can be a disadvantage in industries where time is a critical factor.
5. Maintenance Costs
Finally, metal stamping equipment requires regular maintenance and upkeep. This can be costly and time-consuming, especially for older machines. Neglecting maintenance can result in decreased production efficiency and increased downtime.
In conclusion, while metal stamping has many advantages, it also has some significant disadvantages. These include high tooling costs, design limitations, material limitations, production time, and maintenance costs. It is essential to consider these factors when deciding whether metal stamping is the right manufacturing process for your business.
Common Problems And Solutions of Metal Stamping
Metal stamping is a popular manufacturing process used to fabricate various metal parts. Despite its popularity, there are common problems that can occur during metal stamping that can affect the quality of the finished product. Here are some of the common problems and their solutions.
1. Material Cracking
Material cracking is a common problem in metal stamping, especially when working with brittle materials such as stainless steel. This can lead to part failure and affect the overall quality of the product. To avoid material cracking, it is essential to use the right material for the job and ensure that the stamping process is done at the right temperature and pressure.

2. Die Wear
Die wear can affect the accuracy and precision of the stamping process. It can cause burrs, cracks, and other defects on the finished product. To avoid die wear, it is essential to use high-quality dies and maintain them regularly. Proper lubrication can also help reduce die wear.
3. Springback
Springback occurs when the metal material springs back after it has been stamped. This can lead to inaccurate part dimensions and affect the overall quality of the product. To reduce springback, it is essential to use the right type of material and adjust the stamping process accordingly.
4. Part Distortion
Part distortion can occur due to the stamping process or the material being used. This can lead to inaccurate part dimensions and affect the overall quality of the product. To avoid part distortion, it is essential to use the right type of material and adjust the stamping process accordingly.
5. Surface Defects
Surface defects, such as scratches and dents, can occur during the stamping process. This can affect the appearance and functionality of the finished product. To avoid surface defects, it is essential to use high-quality dies, reduce the stamping pressure, and ensure that the stamping process is done at the right temperature.
Metal stamping is a complex process that requires careful attention to detail to ensure quality and consistency. By understanding these common problems and their solutions, manufacturers can improve their stamping process, reduce defects, and produce high-quality metal parts.

Advantages of Using Metal Stamping
Metal stamping is a manufacturing process that involves creating metal parts through the use of a stamping press. This process has numerous advantages, including:
Cost-Effective
Metal stamping is a cost-effective method of manufacturing metal parts in large quantities. The stamping process can produce parts at a faster rate than other methods, which reduces labor costs and increases productivity. Additionally, the use of automated machines reduces the risk of human error, which can lead to costly mistakes.
High Precision
Metal stamping allows for precise and accurate manufacturing of metal parts. The use of computer-aided technology, such as CAD software and CNC machines, ensures that each part is made to exact specifications. This is especially important in industries such as aerospace and medical, where precision is critical.
Versatility
Metal stamping can be used to manufacture a wide variety of metal parts, including complex shapes and intricate designs. The process can work with a wide range of metals, including stainless steel, aluminum, copper, and brass, which makes it a versatile option for many industries.
Durability
Metal stamping produces durable and long-lasting metal parts. The stamping process can create parts with high strength and resistance to wear and tear, making them ideal for use in heavy-duty machinery and equipment.
In conclusion, metal stamping is a cost-effective, precise, versatile, and durable method of manufacturing metal parts. Its advantages make it a popular choice for many industries, including automotive, aerospace, medical, and electronics.
Materials for Metal Stamping
Metal stamping is a process of shaping and forming metal sheets using a stamping press and a tool-and-die set. The process involves cutting, bending, and shaping metal sheets into a desired shape or form. Different types of metals can be used for metal stamping, depending on the application and requirements. Here are some of the commonly used materials for metal stamping:
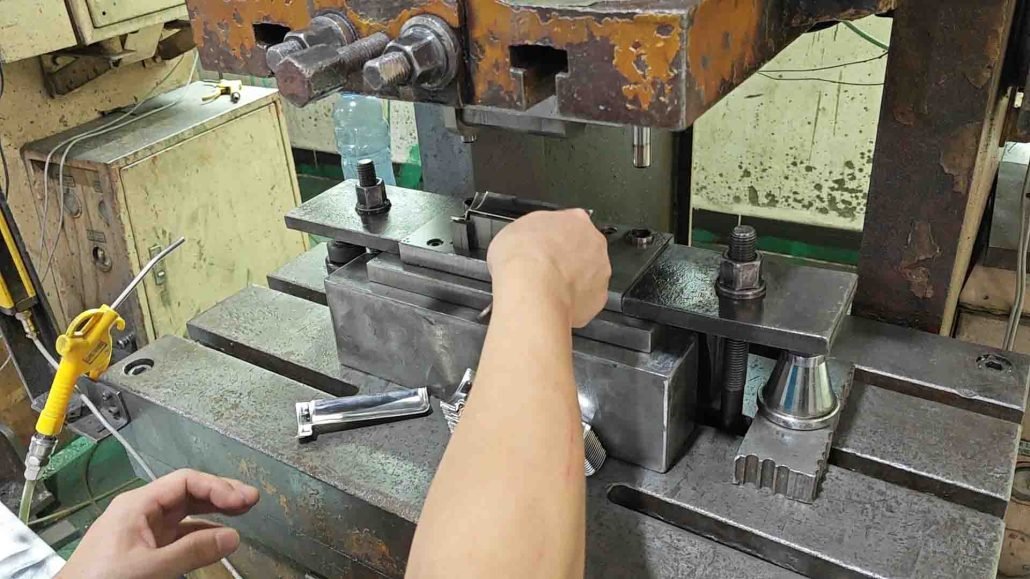
- Steel: Steel is one of the most commonly used metals for metal stamping due to its strength, durability, and affordability. It is used in a wide range of applications, including automotive parts, household appliances, and industrial equipment. Steel is a versatile material that can be easily formed into different shapes and sizes, making it an ideal choice for metal stamping. It is also strong and durable, which makes it suitable for heavy-duty applications that require high strength and toughness.
- Aluminum: Aluminum is a lightweight metal that offers good corrosion resistance and excellent thermal conductivity. It is often used in the aerospace, automotive, and electronics industries. Aluminum is a popular choice for metal stamping due to its lightweight and easy-to-form properties. It is also corrosion-resistant, which makes it suitable for outdoor applications that require resistance to weathering and environmental factors.
- Copper: Copper is a soft and malleable metal that offers good electrical conductivity and thermal conductivity. It is used in electrical and electronic applications, such as circuit boards and connectors. Copper is an excellent choice for metal stamping due to its excellent electrical and thermal properties. It is also easy to form and shape, which makes it suitable for intricate designs and complex shapes.
- Brass: Brass is an alloy of copper and zinc that offers good corrosion resistance and is easy to machine. It is used in decorative applications, such as jewelry and musical instruments. Brass is an ideal material for metal stamping due to its excellent machinability and corrosion resistance. It is also aesthetically pleasing, which makes it suitable for decorative applications that require a high level of visual appeal.
- Nickel: Nickel is a hard and ductile metal that offers good resistance to corrosion and high temperatures. It is often used in the aerospace and chemical industries. Nickel is a popular choice for metal stamping due to its excellent mechanical properties and resistance to corrosion and high temperatures. It is also ductile, which makes it suitable for applications that require high strength and toughness.
These are just a few examples of the materials that can be used for metal stamping. The choice of material depends on various factors, such as the application, the required properties, and the cost. By selecting the right material for the job, you can ensure that your metal stamping project is a success. Metal stamping is a versatile process that can be used for a wide range of applications, from simple components to complex parts that require intricate designs and precise tolerances. With the right material and equipment, you can achieve high-quality results that meet your specific requirements and exceed your expectations.
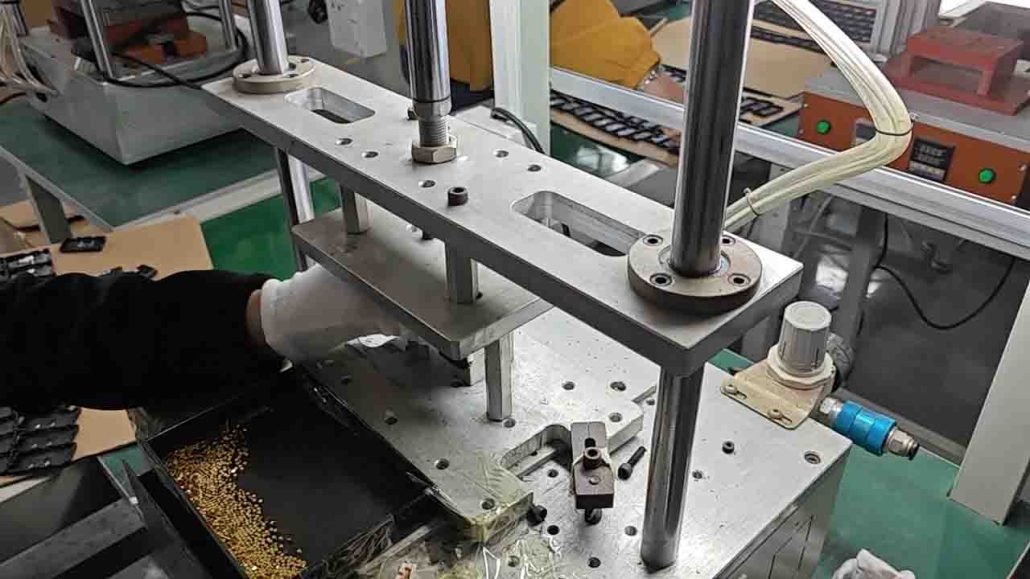
Metal Stamping Technology
Metal stamping is a manufacturing process that uses a die and a press to convert flat sheets of metal into a desired shape. The process involves feeding a metal sheet into the press and using a punch to cut, bend or shape the metal into the desired form.
Metal stamping technology has evolved significantly over the years, with advances in materials, machinery and processes. The use of computer-aided design (CAD) and computer-aided manufacturing (CAM) software has made it possible to create complex parts with high precision and accuracy.
One of the key advantages of metal stamping is its ability to produce parts quickly and cost-effectively. The process is highly automated, which means that large quantities of parts can be produced in a short period of time, with minimal labor costs.
Metal stamping is commonly used in the automotive, aerospace, electronics and appliance industries, among others. It is used to create a wide range of parts, including brackets, clips, connectors, housings, and more.
In conclusion, metal stamping technology is a versatile and cost-effective manufacturing process that has applications in a wide range of industries. Its ability to produce parts quickly and accurately makes it an attractive option for manufacturers looking to increase production efficiency and reduce costs.
FAQ
To minimize common stamping problems and improve the overall efficiency of the manufacturing process, regular maintenance, proper tooling setup, and adequate material handling are essential. It is crucial to identify and address these issues promptly to ensure the success of your stamping operations.
Regular maintenance of stamping equipment can help prevent tool wear or damage, which can lead to increased scrap rates, decreased production efficiency, and higher tooling costs. Proper tooling setup can help prevent misaligned or missing features, which can affect the functionality of the final product. Adequate material handling can help prevent material distortion or warping, which can affect the dimensional accuracy of the part, making it unsuitable for its intended use.
Metal stamping is widely used in many industries, including automotive, aerospace, and electronics. It is a critical process that helps produce high-quality, reliable, and cost-effective parts and components.