In modern manufacturing, precision machining is crucial, and wire EDM cutting has aroused widespread interest. Many industry component manufacturers are using it because it can create complex designs and shapes.
This article will provide you with a comprehensive explanation of wire EDM cutting. From basic principles to practical applications, we will delve into this fascinating manufacturing process.
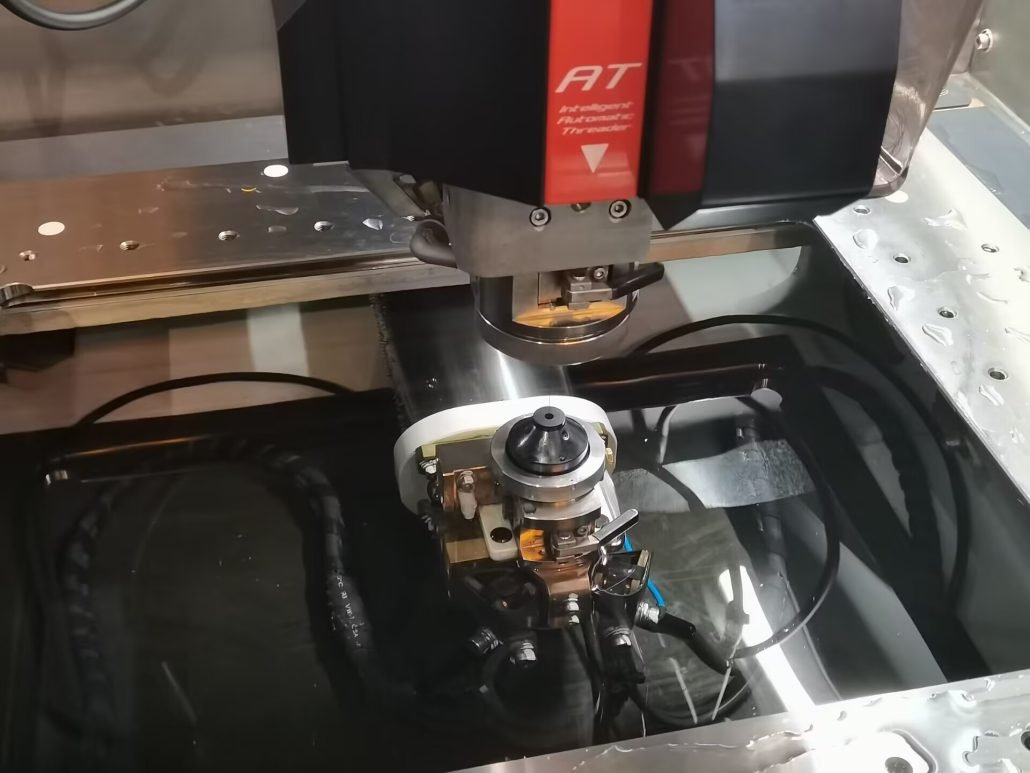
Wire EDM cutting: What is it?
Wire Electrical Discharge Machining (abbreviated as Wire EDM) is an advanced machining technology with its origins dating back to the 20th century in the field of manufacturing. The earliest electric spark discharge cutting technology can be traced back to 1943, when it was initially proposed by Soviet scientists Lazarenko and Rozhdestvensky. However, the modern form of Wire EDM began in the 1960s when Swiss engineer Dr. Hans Baumann first developed a method that utilized a thin wire electrode for cutting.
Wire EDM cutting can be used to manufacture complex parts and molds. It utilizes computer-controlled machines to achieve high-precision cutting through fine wire electrodes (usually metal wires). This innovative method has become increasingly important in the manufacturing industry as it can handle various complex shapes and materials.
How does wire EDM cutting work?
The working principle of wire EDM cutting is very simple.
It uses a fine wire electrode, usually copper or copper alloy, to cut the workpiece along a predetermined path through a computer-controlled machine. There is a small gap between the electrode and the workpiece, called the discharge gap. In this gap, the charge between the electrode and the workpiece generates discharge, melting and cooling a portion of the workpiece material, forming precise cutting. This process is carried out in a liquid medium (usually deionized water) to cool the workpiece and rinse off the melted material.

Materials for Wire EDM Cutting
Wire EDM cutting is suitable for many different types of materials, especially in situations where high precision, complex shapes, or difficulty in machining are required. Here are some of the most suitable materials:
Metals and alloys
Wire EDM is very suitable for cutting various metals and alloys, including steel, stainless steel, aluminum, copper, titanium alloys, and nickel based alloys. These materials are typically used for manufacturing parts and components.
Hard material
Wire cutting is also very effective for cutting superhard materials such as hard alloys (such as tungsten carbide), ceramics, and ceramic alloys, as it does not require the hardness of traditional cutting tools.
Composite materials
In aerospace and automotive manufacturing, composite materials such as carbon fiber reinforced composites and glass fiber reinforced composites can also be cut through Wire EDM.
Plastic
Wire EDM can be used to cut plastic materials, especially in the manufacturing of high-precision molds and plastic parts.
Conductive ceramics
When precision electronic components and sensors need to be manufactured, conductive ceramics can also be processed through Wire EDM.
Advantages and disadvantages of wire EDM cutting
Compared with traditional machining techniques, Wire EDM cutting, as a high-precision machining method, has many advantages and some limitations. The following are its main advantages and disadvantages:
Advantages of Wire EDM cutting
Advantage | Description |
---|---|
High Precision | Capable of achieving extremely high machining accuracy down to the micron level. |
Complex Geometries | Can easily manufacture complex internal and external profiles, small holes, and slots. |
Hard Material Machining | Suitable for high-hardness materials such as tool steel, titanium alloys, and ceramics. |
Low Heat Impact | Virtually no heat-induced deformation during the machining process, preserving material properties. |
Minimal Material Waste | No contact with the workpiece surface, reducing material wastage. |
disadvantages of Wire EDM cutting
Disadvantage | Description |
---|---|
Slow Processing Speed | Relatively slow machining speed, especially for thick materials. |
Surface Roughness | Surface roughness may not be as good as with some other machining methods, potentially requiring additional surface finishing. |
High Costs | High equipment acquisition and maintenance costs, and the need for trained operators. |
Not Suitable for All Materials | Not all materials are suitable for Wire EDM; certain non-conductive and non-metallic materials may not be compatible. |
Wire EDM cutting is particularly suitable for applications that require high precision and complex geometric shapes. However, it is not omnipotent and requires selecting the most suitable processing method based on specific processing needs and materials.

Wire EDM cutting cost calculation
Wire cutting is divided into fast wire cutting and slow wire cutting. Ordinary wire cutting is generally calculated based on the wire cutting area, and the corresponding price will also be higher if the workpiece height is higher. The price of slow wire cutting is about 10 times that of regular wire cutting.
Slow wire processing is generally priced at $20 per hour in Europe and America (with an average cutting efficiency of 40-60mm/min), but cutting molds with higher accuracy costs $30 because once scrapped, material fees need to be paid.
Single piece or small batch processing
Wire cutting processing fee=(cutting cross-sectional area/1200) * 5 Note: 1 hour wire cutting of 1200 square millimeters, generally charged at $5.
Large batch: The price can be slightly lower than this standard
Processing time calculation: required time=processing cross-sectional area/(1200-1800). Note: 1200-1800 is a parameter that can be adjusted, but most processing will choose the median of 1500, which can be multiplied by the hourly processing fee to obtain the price of large-scale processing.
For fast silk, some can be priced at 0.01 US dollars/mm, others can be priced at 0.005 US dollars/mm, and there is also a processing cost of 10 US dollars/hour.
Slow wire cutting costs 0.03 US dollars/mm for one cut, 0.038 US dollars/mm for two cuts, 0.045 US dollars/mm for three cuts, and 0.055 US dollars/mm for four cuts.
The Widespread Application of Wire EDM Cutting
Wire EDM cutting has a wide range of applications in the fields of manufacturing and engineering, mainly due to its high accuracy, ability to handle complex geometric shapes, and suitability for various materials. The following are some of the widespread applications of Wire EDM cutting:
Automobile industry
In the automotive manufacturing industry, automotive components typically have complex shapes and strict dimensional requirements. Meanwhile, many car parts are made of hard materials. This is the shining moment of Wire EDM cutting technology, which shines brightly in automotive manufacturing with its unique processing method. Here are some examples:
1.Bumper Manufacturing: The front and rear bumpers of cars often require complex bumps and openings to absorb the impact of a crash. Wire EDM cutting can precisely manufacture these shapes and ensure their quality and safety.
2.Instrument panel production: The instrument panel is a key component in the interior of the car, which requires precision openings for mounting instruments and controllers. Wire EDM cutting cuts these openings precisely to ensure a perfect fit for the instrument panel.
3.Car doors often contain complex internal structures and openings for installing Windows, locks, and other components. Wire EDM cutting can be used to create these openings, ensuring their quality and consistency.
4.Engine parts: Automotive engines contain many sophisticated parts, such as cylinder heads and liner. Wire EDM cutting can be used to machine these parts to ensure their high precision and performance.
5.Brake component manufacturing: Brake components require precise holes and grooves to ensure the reliability of the brake system. Wire EDM cutting can help manufacture these parts to meet high standards.

Aerospace industry
In addition to the automotive industry, Wire EDM cutting is also widely used in the aerospace industry. The following is an example of Wire EDM cutting in the aerospace industry:
1.Aircraft engine manufacturing: The aerospace industry requires high-performance aircraft engine parts, which are typically made of hard materials. Wire EDM cutting can be used to machine and customize these parts to ensure they meet extremely high standards, including accuracy and strength.
2.Spacecraft building blocks: Spacecraft structures and building blocks often require complex bumps, holes, and openings to house scientific instruments, navigation equipment, and other critical components. Wire EDM cutting enables precise cutting of these complex structures.
3.Turbine blade manufacturing: Turbine blades are key components in aircraft and rocket engines that require extremely high aerodynamic performance. Wire EDM cutting can be used to manufacture these blades, ensuring their surface quality and precision.
4.Aerospace instruments and sensors: Spacecraft and aircraft require a variety of instruments and sensors for data collection and navigation. Wire EDM cutting can be used to manufacture these precision instrument components.
5.Rocket propulsion: Rocket propulsion requires complex nozzles and combustion chambers for propulsion and control. Wire EDM cutting can be used to manufacture these parts, ensuring their accuracy and performance.
6.Aircraft interiors: Whether commercial or private aircraft, interior components require high-precision openings and assembly points. Wire EDM cutting ensures the quality and assembly consistency of these parts.
conclusion: Future Prospects for Wire EDM Cutting
With the continuous development of technology, Wire EDM cutting will continue to play an important role in the manufacturing industry. Robotics, automation, and faster processing speeds will make this technology more efficient and accurate. This means that Wire EDM cutting will find applications in more fields to meet the growing demand for high-precision machining.
Is Wire EDM Cutting Machining Available at longsheng?
Yes, Longsheng provides wire EDM cutting. Longsheng has access to a full range of wire EDM cutting machining services.
Whether you need customized parts or complex parts production, we can meet your needs. Our wire cutting technology precisely cuts a wide range of materials, including metals, alloys, ceramics and composites, providing you with exceptional quality and precision.
Mobile:+86 185 6675 9667 (Gloria Wu)
E-Mail:gloria.wu@longshengmfg.com