This article introduces the process of sheet metal fabrication and common types of metals. Sheet metal is typically made from different metals, each with unique properties that make it suitable for specific applications. This article lists several of the most commonly used metals in sheet metal fabrication and describes their characteristics and application scenarios. The article also discusses design considerations and common classification methods in sheet metal fabrication.
Sheet metal fabrication is a process of transforming sheet metal into various products through techniques such as cutting, bending, and welding. This process heavily depends on the type of metal being used. Different metals have unique properties that make them ideal for specific types of products. For example, steel is the most commonly used metal in sheet metal fabrication due to its affordability, strength, and durability.
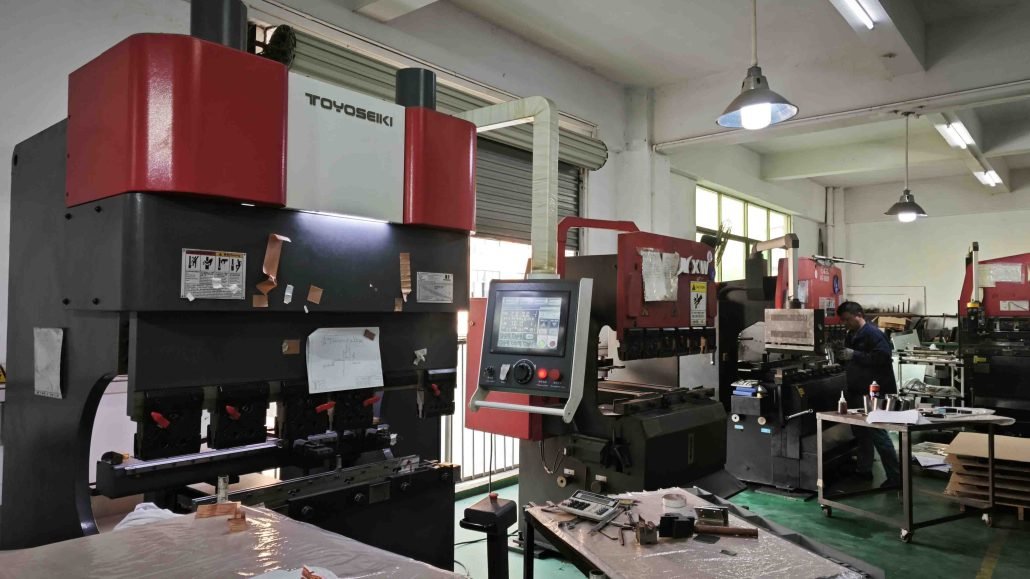
Additionally, this article examines the various industries that use sheet metal and the specific applications for which it is used. Sheet metal is a versatile material that is widely used in industries such as automotive, construction, electronics, medical, and chemical processing. The article discusses specific applications for sheet metal in these fields and highlights the advantages of using different types of metals in these applications. The article also covers various classification methods, design considerations, and measuring tools relevant to sheet metal fabrication.
Overall,this article provides readers with a comprehensive understanding of sheet metal fabrication, including the types of metals used, the fabrication process, application areas, and important design considerations. By reading this article, readers can better understand the processes and applications of sheet metal fabrication and use this knowledge to guide research and development in related fields.
Types of Sheet Metal Fabrication Metals
Sheet metal fabrication involves the process of shaping and forming metal sheets into various products. Sheet metals are usually made from different metals, each with its unique characteristics that suit specific applications. Here are some of the most common types of metals used in sheet metal fabrication:
- Steel: Steel is the most common metal used in sheet metal fabrication due to its affordability, strength, and durability. It is used to manufacture a wide range of products, including automotive parts, building components, and appliances.
- Aluminum: Aluminum is lightweight, corrosion-resistant, and has high thermal conductivity. These properties make it ideal for manufacturing products such as aircraft components, automotive parts, and electronic enclosures.
- Copper: Copper is highly conductive, making it ideal for electrical components and wiring. It is also used in roofing and plumbing applications due to its corrosion-resistant properties.
- Brass: Brass is a combination of copper and zinc, making it highly corrosion-resistant and ideal for manufacturing decorative items, musical instruments, and plumbing fixtures.
- Stainless Steel: Stainless steel is highly resistant to corrosion, making it ideal for manufacturing products that require high durability and hygiene, such as kitchen appliances, medical devices, and chemical processing equipment.
These are just a few of the many types of metals used in sheet metal fabrication, and each has its unique properties that make it ideal for specific applications.
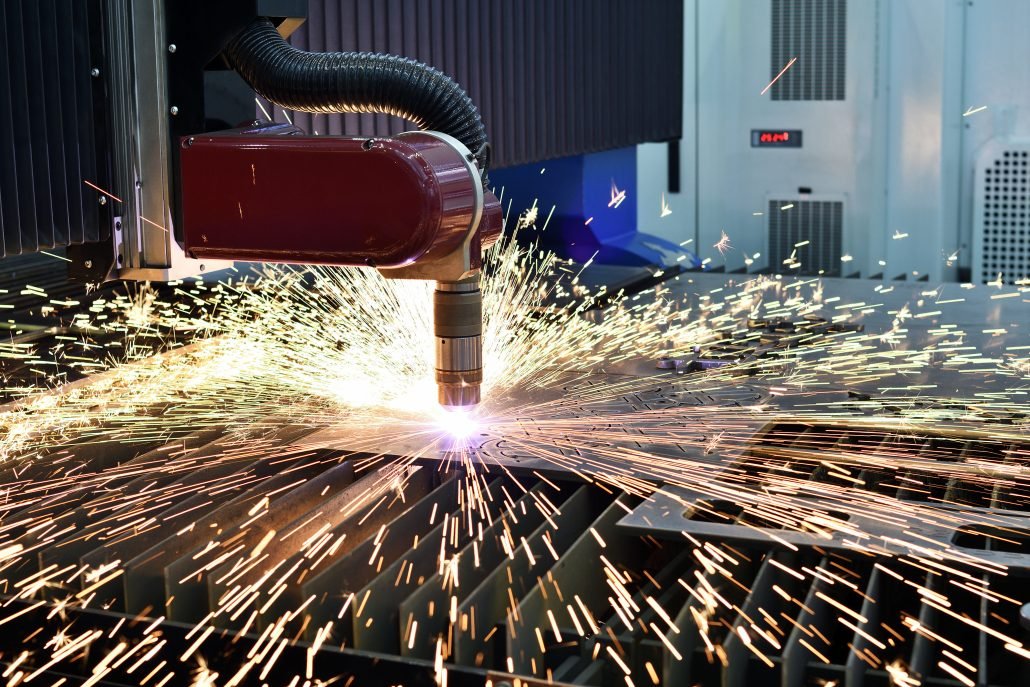
How is Sheet Metal Fabricated
Sheet metal fabrication is a process that involves taking metal sheets and transforming them into a wide variety of products. This transformation is achieved through a combination of techniques such as cutting, bending, and welding. Depending on the specific product being manufactured, the process of sheet metal fabrication can be done manually, using hand tools, or through the use of automated machinery.
The process of sheet metal fabrication is highly dependent on the type of metal being used. Different metals have unique properties that make them ideal for certain types of products. For example, steel is the most commonly used metal in sheet metal fabrication due to its affordability, strength, and durability. It is used to manufacture a wide range of products, including automotive parts, building components, and appliances.
Aluminum, on the other hand, is known for its lightweight and corrosion-resistant properties. This makes it ideal for manufacturing products such as aircraft components, automotive parts, and electronic enclosures. Copper, on the other hand, is highly conductive, making it ideal for electrical components and wiring. It is also used in roofing and plumbing applications due to its corrosion-resistant properties.
Brass is a combination of copper and zinc, making it highly corrosion-resistant and ideal for manufacturing decorative items, musical instruments, and plumbing fixtures. Lastly, stainless steel is highly resistant to corrosion, making it ideal for manufacturing products that require high durability and hygiene, such as kitchen appliances, medical devices, and chemical processing equipment.
In summary, sheet metal fabrication is a versatile process that involves the transformation of metal sheets into a wide variety of products. The process is dependent on the type of metal being used, the desired product, and the manufacturing process being employed. By using a combination of techniques such as cutting, bending, and welding, sheet metal fabrication can create products that are strong, durable, and fit-for-purpose.
What are Some Common Uses for Sheet Metal
Sheet metal is a versatile material that can be used in a wide variety of applications. One of the most common uses of sheet metal is in the manufacturing of automotive parts. The strength and durability of sheet metal make it ideal for use in car bodies, frames, and other components that are exposed to high levels of stress and strain.
Sheet metal is also widely used in building construction. It is used to manufacture components such as roofing, fascias, gutters, and downpipes. Sheet metal is an ideal material for these applications because of its corrosion-resistant properties, which allow it to withstand exposure to the elements.
In addition to automotive and building applications, sheet metal is also used in the manufacturing of appliances. Kitchen appliances such as ovens, stoves, and refrigerators often use sheet metal for their outer shells and internal components. Sheet metal is also used in the manufacturing of washing machines, dryers, and other household appliances.

Another common use of sheet metal is in the manufacturing of aircraft components. The lightweight and corrosion-resistant properties of sheet metal make it ideal for use in the aerospace industry. Sheet metal is used to manufacture components such as wings, fuselages, and engine nacelles.
Sheet metal is also used in the manufacturing of electronic enclosures. The conductive properties of sheet metal make it ideal for use in electronic applications where it is necessary to shield sensitive components from electromagnetic interference.
In the medical industry, sheet metal is used in the manufacturing of medical devices. Sheet metal is an ideal material for use in medical devices because of its corrosion-resistant properties, which allow it to withstand exposure to bodily fluids and other harsh chemicals.
Finally, sheet metal is used in the manufacturing of chemical processing equipment. Sheet metal is an ideal material for use in these applications because of its resistance to corrosion and its ability to withstand exposure to harsh chemicals and high temperatures.
In summary, sheet metal is a versatile material that is used in a wide variety of applications. Its strength, durability, and corrosion-resistant properties make it ideal for use in automotive parts, building components, appliances, aircraft components, electronic enclosures, medical devices, and chemical processing equipment.
What are the Materials for Sheet Metal Working
Sheet metal fabrication involves the process of shaping and forming metal sheets into various products. Sheet metals are usually made from different metals, each with its unique characteristics that suit specific applications. Here are some of the most common types of metals used in sheet metal fabrication:
- Steel: Steel is the most common metal used in sheet metal fabrication due to its affordability, strength, and durability. It is used to manufacture a wide range of products, including automotive parts, building components, and appliances.
- Aluminum: Aluminum is lightweight, corrosion-resistant, and has high thermal conductivity. These properties make it ideal for manufacturing products such as aircraft components, automotive parts, and electronic enclosures.
- Copper: Copper is highly conductive, making it ideal for electrical components and wiring. It is also used in roofing and plumbing applications due to its corrosion-resistant properties.
- Brass: Brass is a combination of copper and zinc, making it highly corrosion-resistant and ideal for manufacturing decorative items, musical instruments, and plumbing fixtures.
- Stainless Steel: Stainless steel is highly resistant to corrosion, making it ideal for manufacturing products that require high durability and hygiene, such as kitchen appliances, medical devices, and chemical processing equipment.
These are just a few of the many types of metals used in sheet metal fabrication, and each has its unique properties that make it ideal for specific applications.
The process of sheet metal fabrication is highly dependent on the type of metal being used. Different metals have unique properties that make them ideal for certain types of products. For example, steel is the most commonly used metal in sheet metal fabrication due to its affordability, strength, and durability. It is used to manufacture a wide range of products, including automotive parts, building components, and appliances.

Aluminum, on the other hand, is known for its lightweight and corrosion-resistant properties. This makes it ideal for manufacturing products such as aircraft components, automotive parts, and electronic enclosures. Copper, on the other hand, is highly conductive, making it ideal for electrical components and wiring. It is also used in roofing and plumbing applications due to its corrosion-resistant properties.
Brass is a combination of copper and zinc, making it highly corrosion-resistant and ideal for manufacturing decorative items, musical instruments, and plumbing fixtures. Lastly, stainless steel is highly resistant to corrosion, making it ideal for manufacturing products that require high durability and hygiene, such as kitchen appliances, medical devices, and chemical processing equipment.
In addition to the above mentioned metals, there are many other types of metals that are used in sheet metal fabrication, including nickel, tin, and titanium. Each of these metals has its unique properties that make them ideal for specific applications.
The choice of metal used in sheet metal fabrication is highly dependent on the specific product being manufactured, the desired properties of the product, and the manufacturing process being employed. By using a combination of techniques such as cutting, bending, and welding, sheet metal fabrication can create products that are strong, durable, and fit-for-purpose.
Sheet metal is a versatile material that can be used in a wide variety of applications. The most common uses of sheet metal are in the manufacturing of automotive parts, building components, and appliances. However, sheet metal is also used in many other industries, including aerospace, electronics, medical, and chemical processing.
In summary, sheet metal fabrication is a versatile process that involves the transformation of metal sheets into a wide variety of products. The choice of metal used in sheet metal fabrication is highly dependent on the specific product being manufactured, the desired properties of the product, and the manufacturing process being employed. By using a combination of techniques such as cutting, bending, and welding, sheet metal fabrication can create products that are strong, durable, and fit-for-purpose.
What are the Sheet Metal Design Considerations
There are several design considerations that should be taken into account when working with sheet metal. These include:
- Material selection: The choice of material used in sheet metal fabrication is critical to the success of the final product. Different metals have unique properties that make them ideal for specific applications. For example, steel is the most commonly used metal in sheet metal fabrication due to its affordability, strength, and durability. Aluminum, on the other hand, is known for its lightweight and corrosion-resistant properties.
- Thickness: The thickness of the sheet metal being used is an important consideration. Thicker sheets are generally stronger and more durable, but they may be more difficult to work with. Thinner sheets, on the other hand, are more flexible and easier to work with, but they may not be as strong.
- Bend radius: When bending sheet metal, it is important to consider the bend radius. The bend radius is the minimum radius that can be achieved without damaging the material. If the bend radius is too small, the material may crack or break.
- Holes and cutouts: When working with sheet metal, it is important to consider the placement of holes and cutouts. These features can weaken the material, so they should be placed strategically to minimize their impact on the overall strength of the product.
- Tolerances: Tolerances are the allowable variations in dimensions and other characteristics of the sheet metal. It is important to consider tolerances when designing sheet metal products to ensure that they will be manufactured accurately.
- Finishing: Finally, finishing is an important consideration when working with sheet metal. Finishing processes such as painting, powder coating, and anodizing can improve the appearance and durability of the final product.
By taking these design considerations into account, designers and manufacturers can create high-quality sheet metal products that are strong, durable, and fit-for-purpose.
What are the Classifications of Sheet Metal
Sheet metal can be classified into two main categories: ferrous and non-ferrous metals. Ferrous metals are those that contain iron, while non-ferrous metals are those that do not contain iron. Examples of ferrous metals include steel and iron, while examples of non-ferrous metals include aluminum, copper, and brass.
Sheet metal can also be classified based on its thickness. Generally, sheet metal is considered to be any metal that is less than 1/4 inch thick. However, the thickness of sheet metal can vary greatly depending on the specific application and manufacturing process being used.
In addition to these classifications, sheet metal can also be classified based on its finish. Sheet metal can be left unfinished, polished, painted, or coated with a variety of materials to improve its appearance and durability.

What Does a Thickness Gauge for Sheet Metal Mean
A thickness gauge for sheet metal is a tool that is used to measure the thickness of sheet metal. It is typically a handheld device that is pressed against the sheet metal, and the thickness is displayed on a digital or analog readout. The thickness gauge is an important tool for sheet metal fabrication because it allows manufacturers to ensure that the metal being used is the correct thickness for the desired application. The thickness of sheet metal can vary greatly depending on the specific application and manufacturing process being used, so it is important to have an accurate measurement of the thickness to ensure that the final product is strong, durable, and fit-for-purpose.
How Many Types of Steel Used in Sheet Metal
There are many different types of steel used in sheet metal fabrication, each with its unique properties that make it ideal for specific applications. Steel is the most commonly used metal in sheet metal fabrication due to its affordability, strength, and durability.
One of the most common types of steel used in sheet metal fabrication is carbon steel. Carbon steel is an alloy of iron and carbon, and it is known for its strength and durability. It is used in a wide range of applications, including automotive parts, building components, and appliances.
Stainless steel is another popular type of steel used in sheet metal fabrication. It is highly resistant to corrosion, making it ideal for manufacturing products that require high durability and hygiene, such as kitchen appliances, medical devices, and chemical processing equipment.
Galvanized steel is a type of steel that has been coated with a layer of zinc to protect it from corrosion. It is commonly used in outdoor applications, such as roofing and fencing, due to its resistance to rust and weathering.
In addition to these common types of steel, there are many other types of steel that can be used in sheet metal fabrication, including high-strength low-alloy (HSLA) steel, hot-rolled steel, and cold-rolled steel. Each of these types of steel has its unique properties that make it ideal for specific applications.
The choice of steel used in sheet metal fabrication is highly dependent on the specific product being manufactured, the desired properties of the product, and the manufacturing process being employed. By using a combination of techniques such as cutting, bending, and welding, sheet metal fabrication can create products that are strong, durable, and fit-for-purpose.
This article highlights the importance of sheet metal fabrication in various industries. Sheet metal fabrication is essential in producing high-quality products in fields such as automotive, construction, electronics, medical, and chemical processing. As a versatile material, sheet metal possesses strength, durability, corrosion resistance, conductivity, and thermal properties, making it useful for different applications. As technology continues to advance, sheet metal fabrication processes and applications will become more diverse and sophisticated, contributing to our lives and economic development.