In the medical industry, we often see many complex and precise parts. Previously, traditional medical device machining was prone to errors and could no longer meet the higher accuracy requirements for medical parts. High precision CNC machining can accurately control the machining process and achieve high precision machining.
This technology can manufacture delicate and complex medical devices, thereby achieving more efficient treatment processes and providing safer and more effective medical services for patients.
In this article, Longsheng Technology will explore the role of high precision CNC machining in the medical industry, the equipment used, the machining process, and how to start your next project. Whether you want to know more about high precision CNC machining or are just interested in this machining technology, please continue reading to learn more information.
What is high precision CNC machining?
Everyone in google search will often see a lot of people are searching for “what is high precision CNC machining”, this problem has troubled a lot of people who have just entered the industry, in fact, it is very good to understand, if CNC machining is through the use of computer programs and the development of CNC machines for automatic and accurate engraving, cutting and blank manufacturing. So high precision CNC machining is on the basis of CNC machining, further improve the machining accuracy and production efficiency.
High precision CNC machining is mainly achieved through the use of high precision CNC machines and advanced CAD/CAM software. These machines and software can be controlled by computer to precisely cut and carve a variety of materials, including metal, plastic, wood and composite materials, with an accuracy of up to 0.0001 inch (2.5 microns) or less.
Because it can achieve high precision parts machining , in the medical industry, it is often used to manufacture a variety of medical devices and equipment, including scalpels, series machines and other common equipment. And important instruments used in the manufacture of surgical procedures, such as precision guided clamps, sutures, needles and sterile trays.

High precision CNC machining methods
The following are the high precision CNC machining methods. For different machining needs, we need to optimize the methods based on different CNC machining techniques to meet the final machining requirements of the parts. For more information, please continue reading.
1.High precision CNC milling
High precision CNC milling is the process of cutting, cutting, hole machining , slot machining , chamfering, and other operations on various materials using a CNC milling machine. This technology is very suitable for use in mass production of workpieces that require fast and accurate production. CNC milling machines, with their highly precise position control and computer-aided design technology, can process truly precise parts on the surface of materials. This can not only improve the machining efficiency, but also reduce the influence of uneven density distribution, bending and mutual interference on the machining quality.
Advantages
1.The accuracy is very high and can handle most materials.
2.Low production cost, suitable for large-scale production.
3.CNC milling can be used for machining various complex geometric shapes and shape accuracy parts.
4.Automatic machining can greatly reduce manual error rates.
Precautions
1.High demand machine tools, tools, and cutting tools.
2.When using, it is necessary to ensure the horizontal accuracy of the workpiece and spindle to ensure the full utilization of the tool’s lifespan.
3.During the machining process, attention should be paid to the safety of the workpiece and the stability of the design.
2.High precision CNC turning
High precision CNC turning is mainly used to produce precision parts with diameters ranging from a few millimeters to tens of centimeters, which are circular or spherical. Using this machining technology can significantly reduce the damage rate during machining . Modern CNC machine tools can provide higher accuracy and combination as needed, thus utilizing the most appropriate method for machining according to the requirements of the production parts.

Advantages
1.It can process precision parts with complex shapes while reducing manual operations and improving work efficiency.
2.It can achieve high machining accuracy, stability, and repeatability.
3.Some efficient CNC lathes can achieve a balance between low cost and high productivity.
Precautions
1.Require a very high degree of sphericity or circularity of the workpiece.
2.When using, it is necessary to ensure the stability of the blade handle and the correctness of the blade direction to prevent surface protrusions.
3.It is best to use internal thread drills for CNC machining with high accuracy, and the machining effect is incredible.
3.High precision 5-axis machining
High precision 5-axis machining is a high-level method in CNC technology. It processes complex curved surfaces or bases by manipulating a 5-axis machine tool, and moves freely above the material, allowing for simultaneous drilling and specification machining . High precision 5-axis machining also allows for special operations such as tool deformation correction and material rotation to fully utilize other advantages of modern machine tools.

Advantages
1.Can process precision parts with complex shapes.
2.Capable of cutting several holes and slots simultaneously.
3.By controlling the position accuracy and angle of the workpiece, a higher level of part design and production can be achieved, resulting in higher precision and quality of the processed parts.
Precautions
1.The use of high precision 5-axis machining machines is relatively complex, and experience and technology are relatively important.
2.When cutting deeply, attention should be paid to protecting the machined parts.
3.machining some materials may result in some difficult to handle problems, such as thermal deformation, which need to be controlled.
conclusion
Seeing this, you must have read the above paragraph and understood the methods of high precision CNC milling, high precision CNC turning, and high precision 5-axis machining, each with different characteristics and purposes. Milling is suitable for manufacturing flat or curved parts, while turning is suitable for manufacturing rotationally symmetric parts. 5-axis machining can be used to manufacture parts with more complex shapes and geometric structures.
For more information about high precision CNC machining methods, please click the link 【9 Different Types Of CNC Machining Processes】
High precision CNC machining tolerance standards
By understanding the above, although high precision CNC machining tools are very accurate, some machines still cannot reproduce part dimensions as accurately as in CAD blueprints. Therefore, we need to understand the standard range of tolerances for high precision CNC machining, please read on to learn more.
In high precision CNC machining, tolerance standards are very strict. In practice, tolerance refers to the maximum error allowed in the manufacture of a product. In the production of high precision parts, tolerances are usually very small, as these parts are mainly used in highly demanding applications such as aerospace, Marine, automotive, etc. In order to ensure the manufacturing quality of high precision parts, some very strict tolerance specifications have been developed.
Machining Technology | Tolerance |
---|---|
CNC Mliing | ±0.005mm |
CNC Turning | ±0.003mm |
CNC Drilling | ±0.002 |
CNC Grinding | ±0.001mm |
CNC Turn-milling Compound Machining | ±0.005mm-0.01mm |
Common tolerance standards
Understand various tolerance standards and practical application requirements.
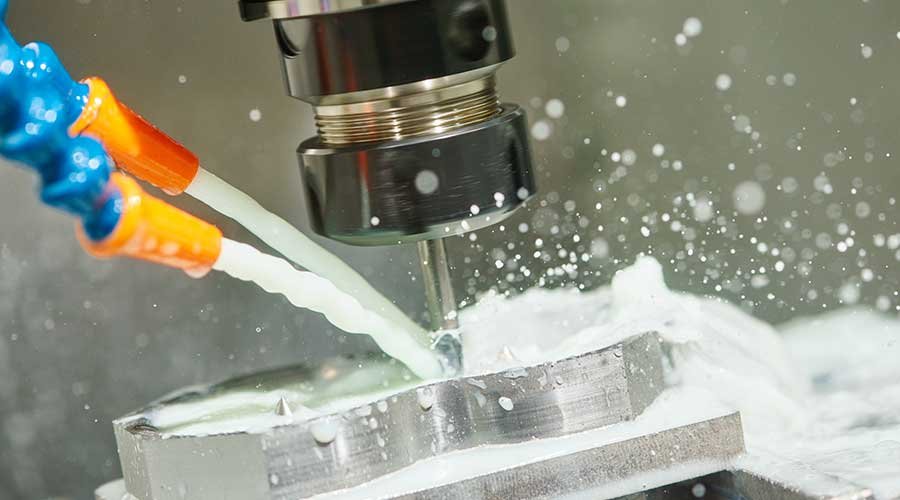
1.ISO 286-2 Tolerance Standards
This is a tolerance standard developed by the International Organization for Standardization (ISO) and widely used in the precision parts manufacturing industry. This standard defines a set of tolerance levels that can be used to represent tolerances in linear dimensions, angles, circular diameters, and other aspects.
ISO tolerance standards are usually divided into two types: IT grade and digital grade, and cover measurement ranges from 4mm to 500mm.
2.JIS tolerance standards
The Japanese Industrial Standards (JIS) have also defined a set of tolerance standards, which are widely used in the manufacturing industry. JIS tolerance standards include linear tolerance, dimensional tolerance, angular tolerance, and circular diameter tolerance.
Unlike ISO tolerance standards, JIS standards use accuracy levels to represent tolerances, such as accuracy levels A, B.
3.ANSI tolerance standards
The American National Standards Institute (ANSI) has also developed a set of tolerance standards, mainly applicable to the manufacturing industry in the United States.
Similar to ISO and JIS standards, ANSI tolerance standards include linear tolerances, dimensional tolerances, angular tolerances, and circular diameter tolerances.
Different types of machining tolerances
The application of different types of machining tolerances in machining is also different
1.Shape tolerance
Shape tolerance refers to the deviation during actual machining or design according to a specified shape. It includes flatness, roundness,straightness, cylindricity, etc.
2.Position tolerance
Position tolerance includes translation tolerance, orientation tolerance, and rotation tolerance that need to be considered during CNC machining and manufacturing of parts. These tolerances are used to ensure that the positional relationship between the machined part and another part can be accurately controlled.
3.Dimensional tolerance
Dimensional tolerance aims to control the size and shape of precision parts, including types such as float, transition, dynamic hole, precision fit, and ordinary fit.
4.Surface quality tolerance
Surface quality tolerance is a term used to describe the surface roughness and smoothness of precision parts. According to surface quality requirements, surface quality can be divided into different levels.
conclusion
High precision CNC machining tolerance is an important factor in ensuring that products meet the design accuracy requirements. Using the correct tolerance standards and control techniques can better ensure the stability of the structure, improve product quality, and have a wider range of applications
To learn more about tolerances, please click the link【CNC Milling Tolerances: Make Precision Parts】
Types of high precision CNC machining equipment
Due to the different application fields and machining processes of parts, different equipment is required for part machining . Some high precision CNC machines include:
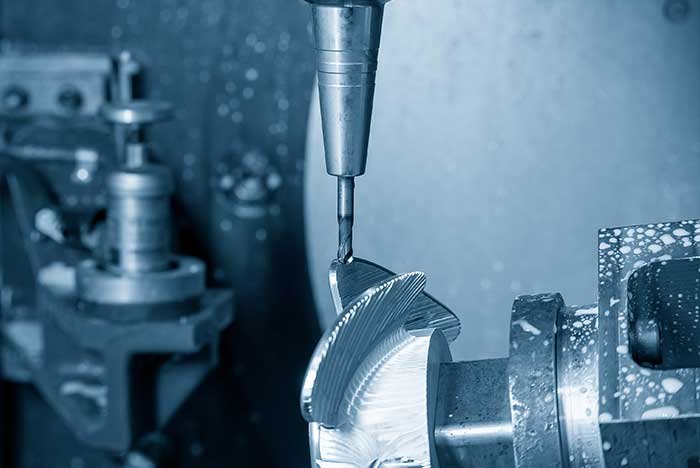
1.CNC lathe equipment
CNC lathe is used to process parts by rotating workpieces, covering various processes such as turning, turning and milling composite. The biggest feature of CNC lathes is that the surface smoothness and accuracy of the processed parts are very high, and the manufacturing cost is also lower than that of conventional lathes, making them more advantageous in the high-end manufacturing field.
CNC lathes are also divided into vertical CNC lathes and horizontal CNC lathes, and the following are some of their characteristics:
Vertical CNC lathe
The spindle of a vertical CNC lathe is perpendicular to the working surface, and the workpiece is machining on the working plane of the vertical lathe. It is suitable for machining columnar parts, such as gears, shafts, etc. Its biggest advantage is high machining efficiency, which can complete CNC machining in a short time according to the requirements of the workpiece. At the same time, the vertical machining center is small in size and floor area, suitable for factories with small space
Horizontal CNC lathe
The spindle of a horizontal CNC lathe is parallel to the working surface, and the workpiece is processed on the working plane of the lathe, which is suitable for machining base type parts. The horizontal machining center has a variety of machining tools, which can process various complex workpieces through different tool combinations, and is also suitable for large-scale machining . In addition, the horizontal machining center can achieve job automation and greatly improve production efficiency.
2.CNC milling machine equipment
CNC milling machines are different from CNC lathes in that they process parts by rotating cutting tools. Compared to CNC lathes, CNC milling machines can achieve more complex geometric shape parts machining .
However, CNC milling machines are more difficult in terms of machining accuracy compared to CNC lathes, and there are certain difficulties in operation. Different parts have different levels of complexity, and the milling machines used for machining are also different. Read on to see the characteristics between them
Horizontal milling machine
Although vertical milling machines are the most commonly used type of milling machine, horizontal milling machines are also a choice that cannot be ignored. Horizontal milling machines are suitable for applications that require machining large or long workpieces, such as ships, train bodies, wind turbines, and heavy machinery.
Horizontal milling machines are usually larger and more powerful than vertical milling machines, and can carry larger workpieces. But correspondingly, the price of horizontal milling machines is also higher.
The horizontal CNC milling machine also has an important advantage, which is that it can achieve multi station machining , greatly improving production efficiency.
Vertical CNC milling machine
Vertical milling machines are suitable for most milling needs, whether it is single piece machining or batch production. Vertical milling machines are suitable for machining various materials, including aluminum, brass, titanium, copper, steel, tungsten steel, and cast iron. They have a compact structure, simple operation, and easy maintenance.
Vertical CNC milling machines have the characteristics of light weight, convenient movement, and simple operation, which can be used for milling various shapes of workpieces. It is particularly suitable for machining parts, such as tool teeth, gears, and workpiece without disc threads.
3.5-axis machine
CNC 5-axis machines can be customized as needed to meet different machining needs and requirements. They can manufacture parts based on complex designs and geometric shapes
The CNC 5-axis machine uses five directions for machining : vertical, horizontal, up, down, and rotation. Use a computer controller to operate the machine with an accuracy of one thousandth of a millimeter or higher. The control system is equipped with highly accurate sensors and regulators to ensure the final size and quality of the product.
Therefore, compared to lathes and milling machines, CNC 5-axis machines can complete more complex tasks in a smaller space. Their multi axis motion also allows them to cut and process multi face shapes, which is often impossible for lathes and milling machines to achieve.
conclusion
After reading the above content, when choosing a machining machine for the project, there are the following recommendations: If you need to perform more complex cutting and detailed machining , and want to automate the process and use fewer operators, the CNC 5-axis machine may be a good choice, even if it is more expensive. However, if your requirement is for more general simple cutting and milling of parts or components, then milling machines and lathes are still good choices.
To learn more about CNC machines, please click the link 【Understanding The G-Code And M-Code For CNC Milling Machine Parts】
Suitable for high precision CNC machining materials
In the high precision CNC machining of parts, different applications, the choice of machining materials is different, in Longsheng technology, we will provide you with the appropriate machining materials according to your requirements. Here are some examples of materials:
Metallic material
1.Aluminum: light weight, high strength, good thermal conductivity, widely used in aerospace, automotive, electronics and other fields.
2.Copper: good electrical conductivity, good workability and corrosion resistance, usually used in circuit boards, pipelines and other fields.
3.Steel: high strength, high hardness, good corrosion resistance, suitable for mechanical parts, auto parts, building structures and other fields.
4.Stainless steel: good corrosion resistance, high strength, beautiful, suitable for kitchen utensils, medical equipment, building structures and other fields.
5.Tungsten: high melting point, high hardness, high density, suitable for cutting tools, electrodes, alloys and other fields.
6.Iron: high strength, good magnetic conductivity, suitable for magnetic materials, motors and other fields.
7.Nickel: good corrosion resistance, good physical properties, suitable for chemical machining , electroplating, aerospace and other fields.
8.Titanium: light weight, high strength, good corrosion resistance, suitable for aerospace, automotive, medical equipment and other fields.
9.Brass: high strength, good electrical conductivity, good machining , suitable for music equipment, water pipes and other fields.
10.Zinc alloy: high strength, good corrosion resistance, easy machining , suitable for automotive parts, TV shell and other fields.
11.Barium lead: good wear resistance, corrosion resistance, high temperature resistance, suitable for engine parts, ship construction and other fields.
12.Cobalt: high hardness, good corrosion resistance, suitable for cutting tools, alloys and other fields.
13.Chromium: good corrosion resistance, high hardness, suitable for steel, chemical industry and other fields.
14.Tin: flexible, good processability, not easy to rust, suitable for electronic components, jewelry and other fields.
15.Magnesium: Light weight, high strength, easy machining , suitable for aerospace, automotive and other fields.

Non-metallic materials
1.Plastic: light, flexible, wear-resistant, corrosion-resistant, can make a variety of parts, daily necessities, packaging and so on.
2.Polyimide (PI) : good insulation, high temperature resistance, corrosion resistance, suitable for the production of electronic components, aerospace parts and so on.
3.Carbon fiber: high strength, good stiffness, light weight, suitable for the production of aerospace parts, sports equipment, etc.
4.Vacuum ceramics: high temperature resistance, corrosion resistance, good insulation, suitable for making vacuum furnaces, chemical reactors and so on.
5.Glass: transparent, not easy to wear, acid and alkali corrosion resistance, suitable for making utensils, building materials and so on.
6.Graphite: good electrical conductivity, good thermal stability, suitable for making electrodes, liquid storage tanks and so on.
7.Silicone rubber: good elasticity, wear resistance, acid and alkali corrosion resistance, suitable for making seals, pipelines and so on.
8.Polyvinyl alcohol (PVA) : soluble in water, high temperature resistance, humidity resistance, suitable for making detergent, glue and so on.
9.Polyformaldehyde (POM) : high strength, good stiffness, wear resistance, corrosion resistance, suitable for the production of mechanical parts, auto parts and so on.
10.Neoprene rubber (CR) : wear resistance, oil resistance, acid and alkali corrosion resistance, suitable for making seals, rubber pipes and so on.
11.Polyether sulfone (PES) : high temperature resistance, corrosion resistance, good insulation, suitable for the production of electronic components, aerospace parts and so on.
12.Hydrorosin acid (HMA) : good viscosity, heat resistance, suitable for making glue, electronic components, etc.
13.Acrylic: transparent, wear-resistant, high strength, suitable for making utensils, building materials and so on.
14.Polypropylene: lightweight, flexible, wear-resistant, corrosion-resistant, suitable for making pipes, packaging materials, etc.
15.Modified nylon: high strength, good stiffness, wear resistance, corrosion resistance, suitable for the production of mechanical parts, auto parts and so on.
conclusion
The above are only the most common materials in high precision CNC machining, and the selection of different materials depends on specific application scenarios and machining requirements. The use of appropriate materials can improve production efficiency and product quality, reduce production costs and wear rates. Longsheng Technology provides hundreds of materials to meet your customized prototype design and production needs. To view the complete list of our materials, please upload your design to get an instant quote in a few minutes and start your project immediately!
To learn about other CNC machining materials, please click on the link 【10 Kinds Of Commonly Used CNC Machining Materials】
What is the cost of high precision CNC machining?
Usually, there is no exact cost of high precision CNC machining, the cost of high precision CNC machining is affected by a combination of factors such as machining difficulty, material cost, equipment maintenance cost and labor cost, if you need to carry out high precision CNC machining, you need to personalize the quotation according to the actual situation to ensure the accuracy of machining costs.
The following provides you with the calculation method of high precision CNC machining cost:
For different parts production links, the specific method of cost calculation will be different, below, we will give some examples to help you better grasp the calculation method of high precision CNC machining costs.
Calculation of material cost
When calculating the cost of materials, it is necessary to consider the specific material type (copper, iron, aluminum, etc.) and the purchase quantity, unit price and other factors. Suppose we need to process a circular part with a diameter of 10mm and the material is SUS316 stainless steel, then the specific calculation formula is as follows:
Material cost = part weight x material unit price
Among them, the weight of the parts is:
Part weight = volume x material density
In this example, the formula for the volume of the cylinder is V=πr²h, where the radius is r=5mm and the height is h=10mm. So the weight of the parts is:
Part weight = πr²h x material density
= π5 ² x 10 x 8
= 1000 PI g
Assume that the unit price of SUS316 stainless steel is 500 yuan /kg, then the material cost is:
Material cost = 1000π / 1000x 500
= 1570.8 yuan
Labor cost
Labor cost refers to the labor cost of the required workers when operating the CNC lathe, including wages, insurance and other factors. So let’s assume that the labor cost per hour is $200.
In this example, assuming that it takes 1 hour to process a circular part with a diameter of 10mm, the machining cost is:
machining cost = equipment consumption + labor cost
= 100 yuan + 200 yuan
= 300 yuan
Calculation of total cost
When calculating the total cost, it is necessary to consider the cost of materials, machining costs and management costs. In this example, suppose that the equipment is used for 10 years, the annual maintenance cost of the equipment is 5,000 yuan, and the management cost is 3,000 yuan. Then the total cost is:
Total cost = material cost + machining cost + equipment maintenance cost + management cost
= 1570.8 yuan + 300 yuan x 10 + 5000 yuan x 10 + 3000 yuan
= 115,708 yuan
Through the above calculation methods, you can understand the specific composition of high precision CNC machining costs and related calculation methods.
Methods for reducing the cost of high precision CNC machining
The following methods can be used to reasonably reduce costs during the use of high precision CNC machining:
Reasonable use of processed materials
When purchasing materials, it is necessary to fully consider the variety, specifications, and quantity of materials, select suitable materials, and determine a reasonable procurement quantity based on the actual situation to reduce costs.
Energy conservation and emission reduction
Adopting energy saving and low-carbon production methods, such as using efficient lighting and energy efficiency technologies.
Optimize machining program
By optimizing the machining program and reducing repetitive machining time and cutting time, machining costs can be effectively reduced. In addition, timely maintenance and repair of equipment is also an important task in optimizing machining procedures.
If you need more information about CNC machining costs, please click on the link 【Metal CNC Machining Cost: Calculation Methods And Tips】

Application of high precision CNC machining in the medical field
The medical industry requires high precision parts and equipment to ensure that surgery and treatment can successfully achieve their goals. This is where high precision CNC machining technology is applied. This technology is widely used in various industries in the medical field, including:
1.Medical equipment and instruments
In the medical field, medical equipment and instruments also require high precision components to operate. For example, the manufacturing of diagnostic equipment such as ECG machines, B-ultrasound machines, electrocardiogram machines, operating room equipment, and various treatment robots and treatment equipment all require high precision components.
High precision CNC machining can provide high-quality and high precision accessories for these devices, and can maintain consistent quality during mass manufacturing.
2.Medical model manufacturing
CNC machine tools can quickly and accurately manufacture medical models, making it easier and faster for surgeries to undergo 3D technology training in advance. By utilizing CAD/CAM technology, medical image data can be transformed into physical models that can be actually manufactured, making it very suitable for laboratories, education, and equipment manufacturing.
3.Production of surgical instruments
The accuracy and quality of surgical instruments can directly affect the success rate of surgery and the treatment effect of patients. High precision CNC machining can produce various types of surgical instruments, such as scalpel, tweezers, scissors, etc.
Their manufacturing accuracy and quality are high, which can greatly reduce the risk of surgery and improve the efficiency and success rate of surgery.
4.Prosthesis manufacturing
The manufacturing of artificial joints, teeth, eyeballs and other prostheses is currently one of the most widely used CNC machining applications in the medical field. Due to the precise control of CNC technology over the machining of different materials, various forms of prostheses can be manufactured to achieve the most realistic degree. At the same time, CNC manufactured prostheses also have customization, which can be manufactured based on the patient’s physical characteristics.
advantages of high precision CNC machining
In the manufacturing process you choose for the project, high precision CNC machining will definitely bring many advantages, as follows:
1.Faster production speed
The use of high precision CNC machining technology can eliminate human factors in traditional machining methods and significantly improve the production efficiency of precision parts.
Digitally controlled machine tools can achieve synchronous machining through the use of multi axis machining centers, thereby reducing production cycles and completing orders faster. Throughout the entire production process. Longsheng Technology provides prototypes that meet manufacturing requirements and quality standards.
2.Higher accuracy
High precision CNC machining allows for the manufacture of more complex parts and components. By using computer-aided design (CAD) and computer-aided manufacturing (CAM) software, complex part manufacturing steps can be accurately executed, ensuring consistency in part accuracy and avoiding the influence of human factors in traditional machining.
3.Lower costs
High precision CNC machining has the advantages of high efficiency, high quality, low scrap rate, and low labor costs. Due to the computer numerical control technology of CNC machine tools having automatic adjustment and monitoring functions, which are very precise, it requires less manpower investment and relatively low labor costs.
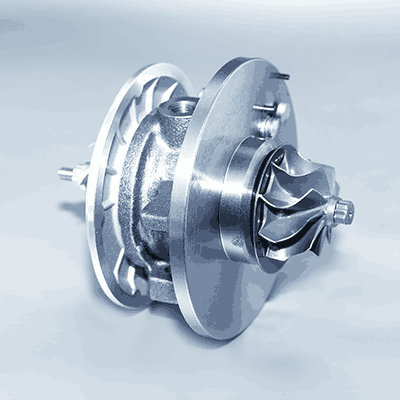
4.Capable of mass production
Traditional machining methods usually only produce one or several products, while high precision CNC machining can achieve mass production, which is very important for many enterprises.
Mass production can not only reduce production costs, but also improve production efficiency, shorten production cycles, lower product prices, and obtain more economic benefits.
conclusion
As mentioned above, the advantages of high precision CNC machining in the field of production and manufacturing are obvious. As long as enterprises use CNC machining technology reasonably according to their own development needs, they can improve the production efficiency of parts, while also ensuring the accuracy and quality of processed parts, meeting the requirements of various industries for parts. At Longsheng Technology, we provide high precision parts that meet manufacturing requirements and quality standards.
Longsheng Technology: Providing high precision CNC machining services
Longsheng Technology’s high precision CNC machining services can accurately process various materials, such as plastics, metals, aluminum alloys, etc., to meet the different needs of customers. Our machining techniques include wire cutting, turning milling composite prmachining cessing, drilling, milling, turning, and more.
Whether it is a single small part or a complex large device, we can provide customers with high-quality machining services. In addition, we can also provide customers with comprehensive solutions such as parts machining , industrial design, rapid prototyping, etc
At Longsheng Technology, we help you save costs in production by 20% lower than the average price of any supplier you can find anywhere. We provide you with the highest quality finished products using the latest CNC technology. Contact us immediately, upload the CAD files to our website, and we promise to receive the quotation within 24 hours. We look forward to working with you!
Contact us now to upload your design files and start your project!
conclusion
Looking at this, now everyone knows the answer to the question: What is high precision CNC machining? The different working methods of high precision CNC machining and the application advantages of high precision CNC machining in the medical industry enable manufacturers to produce higher quality products by using CNC machining, thereby meeting the constantly improving needs and standards of customers. In today’s constantly evolving machining technology, high precision CNC machining will continue to play its role and lead the manufacturing industry forward.
FAQ
High precision CNC machining is based on ordinary CNC machining, achieving higher precision and better machining quality through higher technical accuracy and better machining equipment. In high precision CNC machining, higher technology, better materials, and longer machining time are required, but the products produced are more precise, efficient, and of higher quality.
The requirements for materials in high precision CNC machining are very strict, and it is necessary to select materials with good hardness, stability, and other characteristics, and conduct sufficient inspection and testing before machining . Choosing materials with stable quality is crucial for ensuring the accuracy of the final product.
The accuracy of high precision CNC machining is influenced by multiple factors, such as equipment accuracy, material properties, process parameters, etc. In order to ensure machining accuracy, it is necessary to maintain the equipment, select high-quality materials, adjust machining parameters reasonably, and control the use of cutting fluid.