With the development of technology, there are more and more cutting methods, such as laser cutting, water cutting, plasma cutting, wire cutting… What are the differences between them?
This article will compare the advantages and limitations of these four common cutting methods, as well as their applicable scenarios, to better understand their respective characteristics and help you make wise decisions when choosing the appropriate cutting method.

laser cutting: Overview
Laser cutting is a high-precision cutting technique that uses high-power laser beams to cut materials. It can cut various materials, including metal, plastic, and wood. The advantages of laser cutting include fast cutting speed, clean cuts, high cutting quality, and the ability to cut complex shapes. It is widely used in fields such as automotive manufacturing, aerospace, and electronic manufacturing.
Water cutting: Overview
Water cutting, also known as water jet cutting technology, is a machine that utilizes high-pressure water flow for cutting. Under the control of a computer, workpieces can be arbitrarily carved with minimal influence from material texture. Water cutting is divided into two methods: sandless cutting and sanded cutting.

Plasma cutting: Overview
Plasma cutting utilizes high-temperature plasma to melt and cut materials. Plasma cutting is suitable for cutting metals and conductive materials, and can be performed on materials with larger thicknesses. Plasma cutting can generate more heat affected zones, which can easily cause material deformation and have higher requirements for cutting gas.
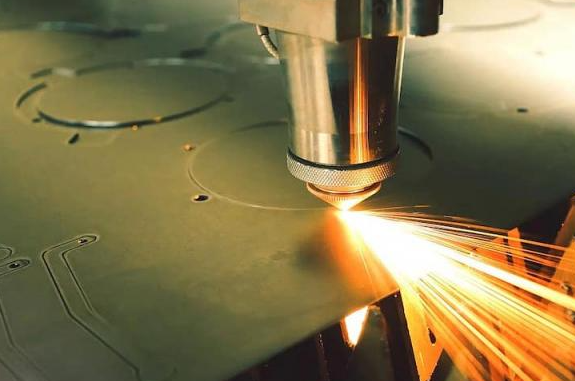
Wire cutting: Overview
Wire Electrical Discharge Machining (WEDM) belongs to the category of electrical machining, and is sometimes also known as wire cutting. Wire cutting can be divided into fast wire cutting, medium wire cutting, and slow wire cutting.
The wire speed of fast wire EDM is 6-12 m/s, and the electrode wire moves back and forth at high speed, resulting in poor cutting accuracy.
Medium wire EDM cutting is a new technology developed in recent years, which achieves frequency conversion and multiple cutting functions on the basis of fast wire cutting.
The wire cutting speed of slow wire EDM is 0.2m/s, and the electrode wire moves in a low speed unidirectional motion, resulting in high cutting accuracy.
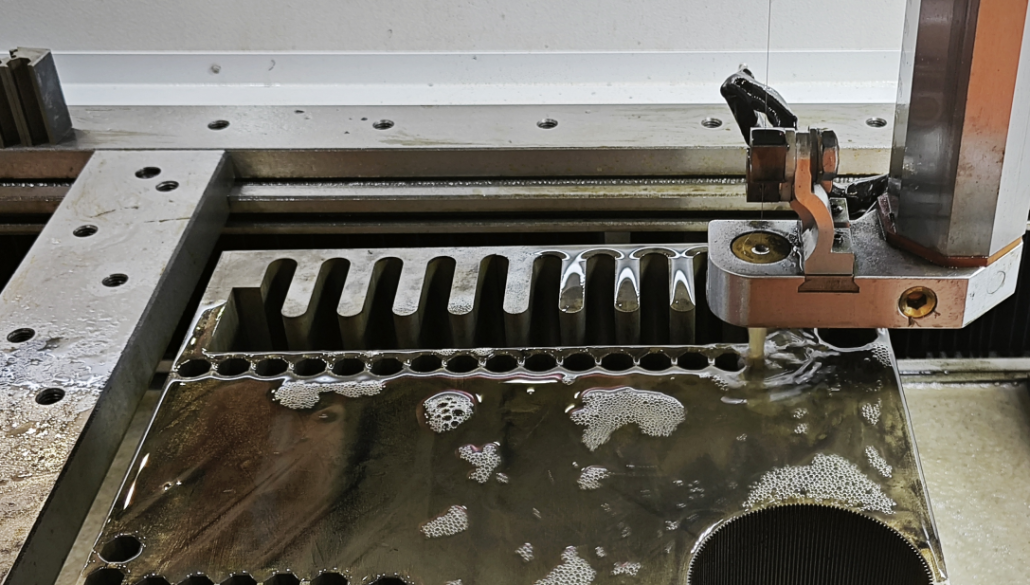
Comparison of application scope
Comparison table of the application of laser cutting, water cutting, plasma cutting and wire cutting on different materials:
Cutting Method | Materials | Advantages | Limitations |
---|---|---|---|
Laser Cutting | Metals, plastics, wood, textiles, stone, etc. | – High precision and detail – Non-contact cutting – Less material wastage – Suitable for complex shapes | – Less effective on transparent and reflective materials – Slower speed, not ideal for mass production |
Waterjet Cutting | Metals, stone, rubber, composite materials, etc. | – No heat-affected zone, no thermal cracking – Can cut thin and thick materials – Suitable for various materials | – Slower cutting speed – High energy consumption – Somewhat rough cut edges |
Plasma Cutting | Metals (especially stainless steel and aluminum), copper, aluminum alloys, etc. | – High cutting speed – Can cut thicker metal sheets – Suitable for industrial production | – Lower cutting precision – Prone to thermal distortion – Requires gas protection |
Wire Cutting | Foam, rubber, plastics, foam rubber, etc. | – Suitable for thin and soft materials – Faster cutting speed – No heat-affected zone | – Limited cutting thickness – Not suitable for hard materials – Somewhat rough cut edges |
laser cutting
The application range of laser cutting is very wide, whether it is metal or non-metal, it can be cut. CO2 laser cutting machines can be used to cut non-metals such as fabric and leather, and fiber laser cutting machines can be used to cut metals. The deformation of the board is small.
Water cutting
Water cutting belongs to cold cutting, without thermal deformation, with good cutting surface quality and no need for secondary machining. If necessary, it is also easy to perform secondary machining. Water cutting can punch and cut any material with fast cutting speed and flexible processing dimensions.
Plasma cutting
Plasma cutting can be used for cutting various metal materials such as stainless steel, aluminum, copper, cast iron, carbon steel, etc. Plasma cutting has obvious thermal effects, low accuracy, and it is not easy to perform secondary processing on the cutting surface.
Wire cutting
Wire cutting can only cut conductive materials, and cutting coolant is required during the cutting process, so it cannot cut materials that are not conductive, afraid of water, or contaminated by cutting coolant, such as paper and leather.
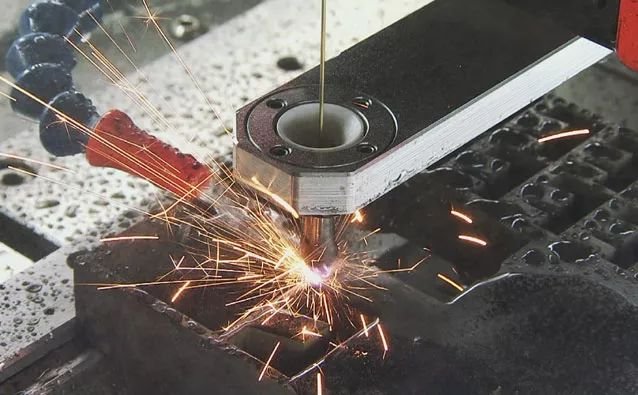
Comparison of cutting thickness
The application of laser cutting carbon steel in industry is generally below 20MM. The cutting ability is generally below 40MM. The industrial application of stainless steel is generally below 16MM, and the cutting capacity is generally below 25MM. And as the thickness of the workpiece increases, the cutting speed significantly decreases.
The thickness of water cutting can be very thick, 0.8-100MM, or even thicker materials.
The plasma cutting thickness is 0-120mm, and the optimal cutting quality range is around 20mm. The plasma system with a thickness of about 20mm has the highest cost-effectiveness.
The thickness of wire cutting is generally 40-60 millimeters, with a maximum thickness of up to 600 millimeters.
Comparison of cutting speeds
Using a laser with a power of 1200W to cut 2mm thick low-carbon steel plates, the cutting speed can reach 600cm/min; Cut 5mm thick polypropylene resin board with a cutting speed of up to 1200cm/min.
The cutting efficiency that electric spark wire cutting can achieve is generally 20-60 square millimeters/minute, with a maximum of 300 square millimeters/minute; Obviously, laser cutting speed is fast and can be used for mass production.
The water cutting speed is quite slow and not suitable for mass production.
Plasma cutting has a slow cutting speed and relatively low accuracy, making it more suitable for cutting thick plates, but the end face has a slope.
For metal processing, wire cutting has higher accuracy, but the speed is slow. Sometimes, other methods such as punching and threading are needed to cut, and the cutting size is greatly limited.
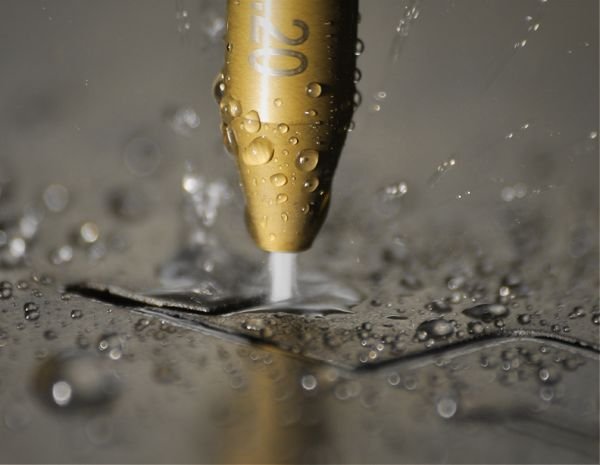
Comparison of cutting accuracy
The laser cutting incision is narrow, with both sides of the cutting seam parallel and perpendicular to the surface, and the dimensional accuracy of the cutting part can reach ± 0.2mm.
Plasma energy can reach within 1mm;
Water cutting does not produce thermal deformation, with an accuracy of ± 0.1mm. If a dynamic water cutting machine is used, the cutting accuracy can be improved, with a cutting accuracy of ± 0.02mm, eliminating cutting slope.
The machining accuracy of wire cutting is generally ± 0.01-0.02mm, with a maximum of ± 0.004mm.
Slit width comparison
Laser cutting is more precise than plasma cutting, and the slit is small, about 0.5mm.
Plasma cutting slit is larger than laser cutting, about 1-2mm;
The slit of water cutting is about 10% larger than the diameter of the knife tube, generally 0.8mm-1.2mm. As the diameter of the sand cutter tube is expanded, the incision is larger.
The slit width of wire cutting is the smallest, generally around 0.1-0.2mm.
Cutting surface quality comparison
The surface roughness of laser cutting is not as good as water cutting, and the thicker the material, the more obvious.
Water cutting does not change the texture of the material around the cutting seam (laser is thermal cutting and will change the texture around the cutting area.
Production input cost comparison
Laser cutting machine models for different purposes have different prices, cheap such as carbon dioxide laser cutting machine is only two or three million, expensive such as 1000W fiber laser cutting machine is now more than one million. Laser cutting has no consumables, but the equipment investment cost is the highest in all cutting methods, and it is not a little higher, and the use and maintenance cost is quite high.
Plasma cutting machine is much cheaper than laser cutting machine, according to the power of the plasma cutting machine, brand, etc., the price varies, the cost of use is higher, basically as long as the conductive material can be cut.
The cost of water cutting equipment is second only to laser cutting, high energy consumption, the use and maintenance cost is also high, and the cutting speed is not as fast as plasma, because all the abrasives are disposable, and they are discharged into nature after being used once, so the environmental pollution is also more serious.
Wire cutting is generally about tens of thousands of pieces. But wire cutting is consumable, molybdenum wire, cutting coolant and so on. There are two kinds of wire cutting commonly used, one is molybdenum wire (molybdenum is valuable ^^), for fast wire equipment, the advantage is that molybdenum wire can be reused many times; The other is to use copper wire (in any case, much cheaper than molybdenum wire), for slow wire equipment, the disadvantage is that the copper wire can only be used once. In addition, the fast wire walking machine is far cheaper than the slow wire walking machine, and the price of a slow wire is equal to 5 or 6 fast wire walking.

How to choose?
When choosing a cutting method, you should consider the following aspects:
Cutting material: Determine the type and thickness of material you need to cut in order to choose the appropriate cutting method.
Accuracy requirements: Determine your cutting quality requirements so that you can choose a cutting method that provides the required precision.
Cost and budget: Consider the purchase cost, operating cost and maintenance cost of the equipment, as well as the material waste associated with the cutting method.
Productivity: Determine your requirements for cutting speed and efficiency so you can choose the cutting method that best suits your production needs.
If you are a professional user and have high requirements for cutting accuracy, laser cutting may be your best choice. If you need to cut a variety of materials and want to achieve high productivity, water cutting may be a good choice. If you need to cut thicker metal materials, plasma cutting and wire cutting may be more suitable for your needs.
conclusion
Whichever cutting method you choose, it should be tested and evaluated on a case-by-case basis. Only through practical operation and comparison can you find the most suitable cutting method for your needs.
FAQ
Laser cutting has the highest cutting accuracy, which can reach tens of microns of accuracy. The cutting accuracy of water cutting, plasma cutting and wire cutting is relatively low, generally in the range of a few millimeters.
Laser cutting has the highest processing efficiency, which can reach several meters per minute. The processing efficiency of water cutting, plasma cutting and wire cutting is relatively low, depending on the hardness and thickness of the material.