In the modern manufacturing, the sheet metal manufacturing is widely used in the manufacturing process, which plays a vital role in connecting the prototype production and the mass production. However, while the application field is expanding, the cost of sheet metal manufacturing has also become one of the hot spots among product developers. Every aspect of each project has a related cost, from design to prototype production to precision machining process, meticulous implementation requires financial support. In addition to the process itself, material procurement is a cost that cannot be ignored.
In this context, it is particularly important to establish a scheme that can effectively reduce the cost of sheet metal manufacturing. This paper will conduct in-depth research on all factors affecting the cost of sheet metal manufacturing, and provide six practical skills to help you save costs as much as possible in the project and increase economic benefits.
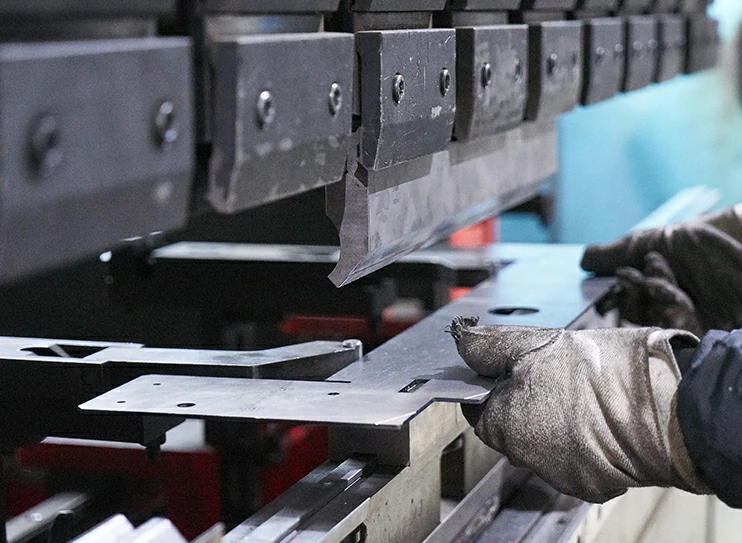
What is sheet metal manufacturing?
Sheet metal fabrication is the process of converting flat metal sheets like aluminum, copper, steel, or brass into manufactured parts. The different techniques to shape sheet metals include cutting, bending, stamping, and punching.

How To Fabricate Sheet Metal Parts?
The sheet metal fabrication process is a step-by-step approach that starts with determining the design requirements. It includes considering dimensional constraints, after which you choose the material for fabrication design. Subsequently, you create fabrication design blueprints that present sketches of the structure and geometry of sheet metal parts on paper. The creation of computer-aided design (CAD) comes next, where you have the model drawn to scale. Additional steps include considering the design for manufacturability (DFM), which involves evaluating manufacturing constraints, simplifying part geometries, and optimizing the number of manufacturing operations.

Common Materials Used In Sheet Metal Fabrication Process
Read about the standard material types for your CNC-fabricated sheet metal projects.
1.Stainless Steel
Stainless steel material types for sheet metal fabrication and design are durable, cost-effective, and have excellent mechanical strength.
2.Copper
While copper is expensive, its excellent durability, thermal properties, and chemical resistance make it a popular type of material for fabricated sheet metal parts.
3.Aluminum
Aluminum is an excellent pick for sheet metal fabrication design when an effective strength-to-weight ratio is a priority.
4.Brass
Brass is an alloy of copper and zinc, which indicates its combined hardness and corrosion resistance properties.
5.Pre-Plated Steel
Pre-plated steel is similar to regular steel except that it has undergone coating with another metal, usually zinc. Hence, it has enhanced corrosion resistance and can withstand harsh weather.

Estimate sheet metal fabrication costs
In today’s highly competitive market background, a comprehensive understanding of the cost structure of sheet metal manufacturing is the key basis to establish an appropriate pricing strategy. The sheet metal component production cycle covers all key stages, including cutting, bending, rolling molding, stamping and welding.
Estimate the raw material costs
We need to decompose the whole production cycle into several manageable units, and estimate these manageable units one by one to more accurately estimate the costs associated with each stage. On this premise, our focus should be on the calculation of raw material costs. Considering the product volume, material density and specific material cost, we can make an estimate of the raw material cost using the following formula:
Raw material cost = volumetric material density material cost (per kg)
As an illustrative example of the formula, assuming a density of 6.8 k g/dm3, a plate size of 700 x 300mm, a thickness of 1.5mm and a material cost of $0.8 per kilogram, we can calculate a value of unit raw material cost.

Mechanical processing cost
we can not ignore the processing cost, considering the hourly cost of the machine, the cycle working time and the processing efficiency of the system. The formula for calculating the machining cost is:
Efficiency / (cost per hour per unit of cycle time) = processing cost
For example, if the cycle time is 14 seconds, the efficiency is 84.5%, and the hourly cost is $78.8, we can calculate the processing cost per unit.
Total cost
the raw material cost and processing cost are summed up to get a total unit of direct production cost. By repeated calculation of this process in different production stages, we can fully grasp the cost structure of the whole production cycle, and provide a solid foundation for the development of effective cost and economic strategies. This detailed cost estimation plays an important role in the development of sustainable manufacturing plans and pricing strategies.

Factors affecting sheet metal fabrication costs
Several factors are particularly important in the estimation of sheet metal manufacturing costs that will directly affect the economy and final cost of the project.
material cost | The cost of materials used in sheet metal processing accounts for a large part of the total cost. The cost of different materials varies greatly, such as stainless steel, aluminum alloy, carbon steel and other materials at different prices. |
Processing process | Different sheet metal processing processes will affect the cost, such as the complexity and time-consuming of stamping, welding, cutting and other processes will affect the cost. |
Equipment cost | The investment cost of the equipment, machinery and tools required for sheet metal processing is also an important factor affecting the cost. Advanced equipment and tools may increase productivity, but they will also increase costs. |
Labor costs | Labor cost is an important part of the sheet metal processing cost, including the wages, training and welfare of operators, technicians and managers. |
design requirements | The design requirements of products will directly affect the difficulty and cost of processing. Complex design requires more processing technology and precision, thus increasing the cost. |
Purchase quantity | Mass production can usually reduce costs, because the cost of materials, labor and equipment can be saved through effects of scale. |
quality requirements | High-quality products usually require stricter process requirements and inspection standards, which may increase costs. |
Tips to reduce sheet metal fabrication costs
If you want to reduce the cost of sheet metal manufacturing, you do need to use some clever techniques. Give us a deeper understanding of the various ways to ensure that the project is more cost-competitive:
Select raw materials
We prefer cost-effective materials such as aluminum or steel to more expensive materials such as stainless steel or titanium. In addition to making the design simpler, using economical and efficient materials can also significantly reduce the production cost of sheet metal. Although stainless steel or titanium may have its particular advantages, alternative materials such as aluminum or steel tend to exhibit similar excellent properties at a relatively low cost. When determining the most cost-effective material selection, specific functional requirements should be carefully considered and manufacturers consulted. Alternatively, note that the use of lower-cost materials may require subtle adjustments to their design to achieve optimal performance. By finding the correct balance between the function and the cost, we can effectively reduce the total cost of sheet metal production.

surface preparation
Consider the cost-effective surface treatments such as powder coating rather than chrome plating and anodic oxidation, etc.In addition to the manufacturing process, the surface finish selection also has a certain impact on the cost.When selecting materials, we tend to choose cost-effective options, such as a powder coating instead of the more costly chrome plating or anodized treatment. We recommend that you consult the manufacturer and evaluate different options for functional and aesthetic requirements to find cost-effective and effective solutions to meet project requirements.
tolerance control
One key factor to be considered when reducing the cost of sheet metal manufacturing is the tolerance requirement. While strict tolerances may be required for specific items, choosing looser tolerances can provide significant cost savings if they do not affect functionality or aesthetics. Before determining the tolerance level, the manufacturer must be consulted and all functional and aesthetic requirements carefully evaluated. Overall, realizing this can successfully reduce the cost of sheet metal manufacturing.

Simplify manufacturing steps
In collaboration with sheet metal processing manufacturers. Establishing close cooperation with trusted sheet metal processing manufacturers also saves costs in the manufacturing process. Simplify the process and eliminate unnecessary steps can save time and money. Please make further contact with your manufacturer to identify potential areas of improvement and work together to find ways to increase efficiency and reduce costs.
quantity ordered
Make the most of economies of scale by ordering more quantities at once. Another cost-saving strategy in sheet metal manufacturing is to take advantage of economies of scale by ordering more quantities at once. This can reduce manufacturing and transportation costs, thus saving on overall costs. Project requirements and storage capacity must be carefully assessed before placing bulk orders, but doing so can have a significant impact on reducing the cost of sheet metal manufacturing.
Invest In Technological Innovation And Sustainability
The introduction of technological innovation and sustainability practices is a long-term cost reduction strategy. The introduction of automation equipment can reduce labor costs and improve production efficiency. At the same time, the use of environmentally friendly materials and processes not only conforms to market trends, but also avoids additional costs due to environmental regulations. By constantly promoting technological innovation, enterprises can better adapt to market demand and improve competitiveness.

Longsheng: Your Trusted Sheet Metal Fabrication Design Company
At Longsheng, we are not only proficient in the various skills mentioned above, but we have a professional technical team that can provide leading sheet metal fabrication services to manufacture high quality parts for you at very competitive prices. As an ISO 9001:2015 certified company, we focus on the construction of quality management system to provide customers with reliable service.
Our team of experts has the experience to perform DfM (Design for Manufacturability) analysis to improve your design. We are not only a manufacturer, but also a partner, committed to providing full support and professional advice to our customers to ensure that the design can reduce manufacturing costs while still meeting high quality standards.
If you have a design model that needs to be manufactured, please upload it to us immediately and we will provide you with an immediate quote. Choose Longsheng, choose a quality, high technical level, cost-effective sheet metal fabrication partner, let us work together to create outstanding parts for your project to achieve greater success.

Conclusion
When designing sheet metal parts, manufacturing cost is a crucial consideration. By applying many of the techniques discussed above, the goal of reducing sheet metal fabrication costs can be effectively achieved. However, in addition to these tips, it is also crucial to choose a manufacturer with highly skilled technicians and extensive knowledge of custom sheet metal fabrication.
FAQ
How can we reduce cost of fabrication?
To reduce fabrication costs, focus on efficient material selection, streamline designs for simplicity, embrace automation for repetitive tasks, optimize energy usage, manage the supply chain effectively, invest in employee training, ensure rigorous quality control, explore reuse and recycling options, and foster a culture of continuous improvement. These strategies collectively contribute to cost savings without compromising on the quality of fabrication processes and end products.
How to do if the material waste occurs in the process of sheet metal processing?
Material waste is a common cost problem in sheet metal manufacturing. In order to reduce material waste, product design can be optimized and unnecessary use of materials reduced. Precise measurement and cutting techniques are used to ensure the maximum use of materials. Recycling and reuse of scraps and waste materials.
How to reduce the production cost caused by the complex process flow?
Existing processes are reviewed and optimized to remove unnecessary steps. Introduce automation and robotics to reduce manual operations. Use of advanced processing equipment and tools to improve production efficiency.
How to solve the cost increase caused by low equipment efficiency?
Equipment inefficiency may lead to longer production cycles and increased costs. In order to improve the efficiency of the equipment, the equipment can be maintained and maintained regularly to ensure that it is in the best condition. At the same time, the operators should be trained to improve their operation skills and equipment use efficiency. Advanced equipment management system is introduced to monitor the running status of equipment and optimize it.
What if the labor cost is too expensive in the manufacturing process?
Optimize personnel allocation to ensure that each position has the right personnel. Improve employee skills and efficiency, achieved through training and job incentives. Introduce automation and robotics to reduce manual operations.
Resource
A hybrid approach for estimating the drawbead restraining force in sheet metal forming