Extrusion and compression moulding are two basic manufacturing processes that play a major function within the plastics trade. Every process has its distinctive traits, strategies, and purposes, making them appropriate for various manufacturing situations. This report offers an summary of each processes, highlighting their variations and particular makes use of.
Extrusion Moulding
Extrusion moulding is a high-volume manufacturing process that creates objects with a hard and fast cross-sectional profile. It entails heating a fabric till it turns into malleable after which forcing it by means of a die to form it right into a steady profile. This process is especially environment friendly for producing objects with uniform cross-sections, reminiscent of pipes, hoses, and rods.
The important thing parts of the extrusion process embrace the heating of the uncooked materials, the design of the die that shapes the product, the pushing mechanism that forces the fabric by means of the die, and the cooling process that solidifies the ultimate form. Extrusion moulding is understood for its effectivity, versatility, and cost-effectiveness, making it a preferred selection for producing a variety of styles and sizes at a low operational value.
Regardless of its benefits, extrusion moulding additionally has some disadvantages, such because the potential for varied defects and limitations within the varieties of shapes that may be produced.
Compression moulding, alternatively, is a process that makes use of compressive pressure to form a fabric inside a mold. It’s significantly appropriate for molding complicated, high-strength parts. The process begins with inserting preheated materials right into a mold cavity, then closing the mold and making use of strain to type the fabric into the specified form.
This methodology is sensible for merchandise which are typically flat or have strong, flat surfaces, reminiscent of kitchenware, automotive parts like fenders and casings for engine parts, and electrical insulation parts. Compression moulding is understood for its skill to supply massive, intricate parts and is cost-effective for high-volume manufacturing.
Nevertheless, compression moulding can generally lead to poor product consistency and problem in controlling flashing, that are drawbacks to think about.
Variations Between Extrusion and Compression Moulding
The first distinction between extrusion and compression moulding lies of their strategies and purposes. Extrusion moulding is a steady process appropriate for creating lengthy sections of merchandise, whereas compression moulding is a batch-based process excellent for big, intricate parts.
Extrusion moulding usually makes use of thermoplastics and metals reminiscent of aluminum and copper, whereas compression moulding is extra generally related to thermosetting plastics and fiber-reinforced plastics. By way of purposes, extrusion is commonly used for automobile parts within the automotive and aerospace industries, whereas compression moulding is most well-liked for inside parts like dashboards and door panels, in addition to for creating sandwich buildings that incorporate a core materials.
Overview of Extrusion Moulding
Key Parts of the Process
The extrusion process entails a number of key parts that work collectively to remodel uncooked supplies into completed merchandise:
- Hopper: That is the place the uncooked materials, usually within the type of pellets, granules, flakes, or powders, is saved earlier than being fed into the extruder.
- Feed Throat: It connects the hopper to the barrel and channels the fabric into the extrusion process.
- Barrel: The barrel homes the screw and is supplied with heaters to soften the plastic materials.
- Screw: Situated throughout the barrel, the screw is liable for pushing the molten materials in the direction of the die.
- Breaker Plate: This part maintains strain and serves as a filter, stopping overseas supplies from getting into the barrel.
- Die: The die offers the molten plastic its desired profile. It’s normally custom-made from metallic.
- Cooling System: After the plastic is formed by the die, it’s cooled and solidified into its last form.

Functions and Examples
Extrusion moulding is used to supply a variety of merchandise as a result of its versatility. Widespread purposes embrace:
- Tubing and pipes for varied makes use of, from medical purposes to large-scale plumbing.
- Profiles for home windows and doorways, which require exact and constant cross-sections.
- Blinds, wire insulation, and weatherstripping, which profit from the continual profile that extrusion offers.
- Windshield wipers and vinyl sidings, that are examples of the varied merchandise that may be created utilizing extrusion moulding.
- Plastic movies and sheeting, achieved by flattening the extruded plastic by means of cooling rolls.
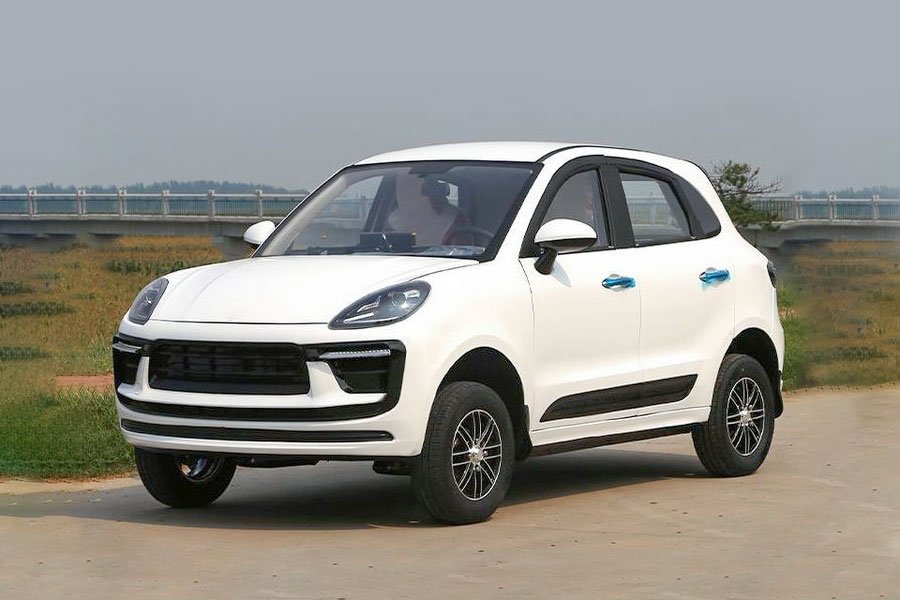
Advantages of Extrusion Moulding
Extrusion moulding presents a number of benefits that make it a most well-liked methodology for a lot of producers:
- Price-Effectiveness: It’s identified for its effectivity and low value per half produced, particularly appropriate for large manufacturing batches.
- Versatility: The process permits for the usage of a variety of supplies, together with thermoplastics, thermosets, and metals, and may produce quite a lot of styles and sizes.
- Constant High quality: Merchandise made by means of extrusion usually present uniformity all through their size, which is very prized for quite a few initiatives.
- Recyclability and Sustainability: The power to recycle extra plastic makes extrusion moulding an environmentally pleasant choice.
- Ease of Alterations: Publish-extrusion manipulation is comparatively straightforward, permitting for adjustments in form earlier than the product cools.
Regardless of its many benefits, extrusion moulding does have some limitations, reminiscent of design restrictions, materials limitations, and the necessity for a major upfront funding.
Overview of Compression Moulding
Process Traits
The compression moulding process is characterised by a number of distinct steps:
- Materials Preparation: The uncooked supplies, which might be thermoset or thermoplastic resins, are ready within the type of pre-measured and preheated prices.
- Mould Preheating: The mold is cleaned, coated with a launch agent, and preheated to facilitate the movement of the fabric.
- Cost Loading: The cost is positioned into the mold cavity, which has been machined from supplies like metal or aluminum.
- Compression: The mold is closed, and strain is utilized to form the fabric into the specified type.
- Curing: Warmth and strain facilitate the curing or hardening of the fabric into the ultimate product.
- Cooling and Ejection: After curing, the half is cooled after which ejected from the mold, typically requiring de-flashing to take away extra materials.
The efficiency of the supplies utilized in compression moulding is influenced by their composition, the ratio of fiber to resin, and the process parameters reminiscent of preheating temperature, molding strain, and cooling price.
Use Instances and Materials
Compression moulding is used to supply a wide selection of merchandise throughout completely different sectors:
- Automotive Business: Giant parts like automotive panels, engine parts, and inside automotive parts are generally made utilizing this process.
- Expertise: Gadgets reminiscent of online game controllers, keyboards, and mouse covers.
- Family: Kitchen instruments, utensils, home equipment, and dinnerware like bowls, cups, and plates.
- Electrical Parts: Elements like electrical sockets, switches, faceplates, and metering gadgets.
- Medical: Merchandise reminiscent of syringe stoppers, respirator masks, and rubber clothes.
The supplies utilized in compression moulding embrace thermoset resins like SMC, BMC, and epoxy, in addition to thermoplastic resins reminiscent of polypropylene, nylon, and PEEK. Numerous fiber varieties, together with fiberglass and carbon fiber, are additionally included to boost mechanical efficiency.
Advantages of Compression Moulding
Compression moulding presents a number of benefits:
- Price-Effectiveness: It’s identified for low tooling prices, lowered labor, and minimal materials scrap, which contribute to general value financial savings.
- Energy and Sturdiness: The process produces parts with wonderful power and mechanical properties, typically akin to metallic parts.
- Design Flexibility: It permits for versatile design, excessive product uniformity, and good dimensional accuracy.
- Minimized Wastage: The process minimizes wastage and may embrace further options like boss attachments and inserts.
- Batch Manufacturing: A number of parts might be molded concurrently inside a single cycle, enhancing effectivity.
Compression moulding can be adaptable to automation, which may additional scale back prices and enhance consistency. The process is appropriate for quite a lot of supplies, together with each thermoset and thermoplastic compounds, permitting it to fulfill various software want.
Key Variations Between Extrusion and Compression Moulding
Extrusion Moulding | Compression Moulding | |
---|---|---|
Process Strategies | A steady process the place uncooked plastic materials is melted and fashioned right into a steady profile by being pressured by means of a die. | A batch process the place a preheated quantity of fabric is positioned right into a heated mold cavity after which compressed into the specified form. |
Materials Used | Sometimes makes use of thermoplastics and elastomers, and can even form metals reminiscent of aluminum and copper. Widespread supplies embrace polypropylene, nylon, acrylic, polyethylene, polystyrene, polycarbonate, and ABS. | Suitable with each thermoplastics and thermosets, together with supplies like DAP, epoxy, HDPE, melamine, PAIs, PEEK, PU, PPS, PF, PTFE, silicone, UF, and urethane. |
Business Functions | Used for quite a lot of purposes reminiscent of tubing, seals, gaskets, and profiles throughout the automotive, medical, and development industries. It is usually used for merchandise like consuming straws, pipes, hoses, rods, sheets, solid movies, extrusion coating and lamination, wire and cable coating, and pipe and tubing. | Generally used for producing massive parts and panels for autos, pc and gaming gadgets, kitchenware, electrical parts, and medical and dental system parts. |
NEED HELP?
While the information above provides basic guidelines, the experts at LongSheng can assist you in determining the most efficient and cost-effective process for your plastic part supply needs.
Case Research and Developments in Extrusion and Compression Moulding Materials
The manufacturing trade is witnessing a surge in technological developments, significantly within the fields of extrusion and compression moulding. These developments are usually not solely enhancing the effectivity and high quality of the manufacturing processes however are additionally introducing new supplies which are extra sustainable and higher suited to fulfill the calls for of varied industries.
Compression Moulding Developments
Tendencies and Improvements
The compression moulding sector is evolving with the combination of automation and Business 4.0 applied sciences, resulting in extra environment friendly and sooner manufacturing processes. There’s a vital shift in the direction of eco-friendly supplies and processes, with a give attention to lowering waste and bettering general effectivity. Using biodegradable supplies is on the rise, aligning with the demand for sustainable merchandise. Recycling initiatives have gotten extra prevalent, with firms more and more utilizing recycled supplies to reduce their environmental footprint.
Materials Developments
Improvements in compression moulding supplies embrace the usage of pure fibers for reinforcement, which presents improved mechanical properties and environmental advantages. The event of recent supplies can be a key pattern, with the intention of enhancing sturdiness and efficiency.
Business 4.0 Integration
The adoption of Business 4.0 applied sciences reminiscent of IoT, AI, and Massive Knowledge is revolutionizing the compression moulding process, resulting in enhancements in high quality, effectivity, and waste discount. Automated compression moulding techniques, additive manufacturing (3D printing), and simulation software program are a number of the improvements optimizing the process.
Market Progress and Future Outlook
The compression moulding presses market is predicted to develop considerably, pushed by the growing demand for compression moulded merchandise throughout varied industries. The pattern in the direction of light-weight and eco-friendly supplies is additional fueling this progress. Technological developments in compression moulding presses are contributing to market enlargement.
Extrusion Moulding Developments
Self-Bolstered Polymer Composites (SRP)
The ESPRIT undertaking centered on growing SRPs which are lighter, stiffer, extra impact-resistant, and recyclable in comparison with conventional composites. The undertaking aimed to create flowing supplies for complicated 3D shapes and novel selective heating strategies. The ensuing supplies demonstrated a power or stiffness a minimum of thrice greater than the mother or father polymer.
Close to-Web-Form Molding Expertise
Piper Plastics launched a high-pressure molding know-how that produces near-net-shape polymers with isotropic mechanical properties. This know-how yields parts which are stronger than these produced by conventional extrusion or compression moulding strategies. It’s significantly helpful for big parts with complicated geometries.
Case Research and Functions
Case research have proven that totally moulded seals produced on superior compression vacuum presses can supply superior efficiency in comparison with extruded and spliced seals. The ESPRIT undertaking demonstrated the capabilities of the brand new applied sciences by means of a spread of parts, together with automotive parts and sportswear.
Market Insights
The compression moulding presses market is very aggressive, with key gamers specializing in growing modern machines with improved functionalities. The market is categorized into vertical and horizontal presses, every catering to completely different manufacturing wants. The presses are used throughout varied industries, together with aerospace, automotive, and electrical home equipment.
Conclusion
The developments in extrusion and compression moulding supplies are shaping the way forward for manufacturing. With the combination of recent supplies, automation, and Business 4.0 applied sciences, the trade is shifting in the direction of extra sustainable and environment friendly manufacturing strategies. These improvements are usually not solely helpful for the setting but in addition supply aggressive benefits to producers when it comes to value financial savings, materials properties, and product customization. The continued progress and improvement on this sector are anticipated to profoundly influence varied industries, from automotive to aerospace and past.
FAQs
Which is healthier, extrusion or compression?
The selection between extrusion and compression moulding depends upon the particular necessities of the mission. Each processes have distinct benefits and are appropriate for various functions.
Extrusion Moulding is good for creating steady linear, two-dimensional shapes, comparable to pipes, tubing, and varied profiles. It’s a steady operation and is especially environment friendly for large-scale manufacturing. Extrusion can also be recognized for its excessive manufacturing charges and shorter manufacturing cycles, leading to decrease per unit price. Nonetheless, it might be extra advanced and costly as a result of mold prices and materials concerns. The process is well-suited for merchandise like hoses, pipes, plastic bottles, movies, and sheets.
Compression Moulding, then again, is appropriate for manufacturing giant, pretty intricate parts. It’s cost-effective, produces little waste, and is good for big parts. Compression moulding is often used for thermosetting plastics and may deal with 2D shapes with out intricacies. This process is especially sensible for merchandise which can be flat or have strong, flat surfaces, comparable to automotive parts, kitchenware, electrical parts, and medical machine parts.
In abstract, the selection between extrusion and compression moulding depends upon components comparable to the form required, software of the product, manufacturing quantity, complexity, and price range. Each strategies have their distinctive benefits and are invaluable instruments within the manufacturing of plastic merchandise.
How to decide on the appropriate molding process?
When selecting the best molding process, a number of components should be thought-about to make sure one of the best match for the particular mission.
Materials Properties: Contemplate the properties of various supplies, comparable to warmth resistance, power, and supposed use of the product. Select a fabric that aligns with the necessities of the mission.
Design Complexity: Consider the complexity of the design and the options that should be precisely replicated. Sure processes could also be higher suited to intricate shapes and detailed, advanced options.
Manufacturing Quantity: Contemplate the anticipated manufacturing quantity. Excessive-volume tasks might profit from processes like injection molding for cost-effective mass manufacturing, whereas lower-volume tasks might discover compression molding extra appropriate.
Sustainability: With the growing concentrate on sustainability, contemplate the environmental affect of the chosen molding process and the supplies used. There’s a rising pattern in the direction of utilizing eco-friendly and biodegradable supplies.
Automation and Trade 4.0: The mixing of automation and Trade 4.0 applied sciences is revolutionizing the molding processes, resulting in enhancements in high quality, effectivity, and waste discount. Contemplate the potential advantages of adopting these applied sciences.
Price and Precision: Velocity, price, and precision within the remaining product design are key standards when choosing a fabrication methodology. Contemplate the trade-offs between price, manufacturing velocity, and the precision required for the mission.
In abstract, the selection of the appropriate molding process depends upon a mix of fabric properties, design complexity, manufacturing quantity, sustainability concerns, and the potential advantages of automation and Trade 4.0 applied sciences. Every mission might have distinctive necessities that can affect the collection of probably the most appropriate molding process.
Resource
Compression molding,From Wikipedia
Your blog is a testament to the power of positivity and the strength.