In modern manufacturing, sheet metal fabrication is widely evaluated in the manufacturing process and plays a vital role in connecting prototype manufacturing and series production. However, as the application fields continue to expand, the cost of sheet metal fabrication has also become one of the hot spots for product projects. Each of these has associated costs, from design to prototyping to precision machining processes, and advancement requires financial support.
In this context, what kind of sheet metal fabrication method is the most economical? This article will conduct in-depth research on various factors that affect sheet metal fabrication costs, the cost characteristics of common sheet metal fabrication methods, and how to choose the most economical sheet metal fabrication solution. It will help you choose the most economical sheet metal fabrication method so that you can complete your project. Save costs as much as possible and improve economic benefits.
What Is Sheet Metal Fabrication?
Sheet metal fabrication usually refers to a series of machining operations of the metal sheet (usually below 6mm) designed to plastic and deform the metal sheet to form the desired shape and size.

How To Fabricate Sheet Metal Parts?
The sheet metal fabrication process is a step-by-step approach that starts with determining the design requirements. It includes considering dimensional constraints, after which you choose the material for fabrication design. Subsequently, you create fabrication design blueprints that present sketches of the structure and geometry of sheet metal parts on paper. The creation of computer-aided design (CAD) comes next, where you have the model drawn to scale. Additional steps include considering the design for manufacturability (DFM), which involves evaluating manufacturing constraints, simplifying part geometries, and optimizing the number of manufacturing operations.
What Are the Common Types of Sheet Metal Fabrication Techniques?
Stamping
Stamping uses dies and stamp presses to shape metal coils and sheets. It uses both cutting and forming operations at room temperature to achieve maximum results. Stamping encompasses various techniques including piercing, blanking, drawing, coining, and embossing.
Piercing and blanking are simpler and are usually carried out as the first step in sheet metal fabrication. Drawing, embossing, and coining are more complex and can create intricate shapes and designs that do not require further processing.
Shearing
Shearing is the most common and basic process in sheet metal processing. It refers to the deformation form in which the cross section between the two forces is affected by the same transverse force, the opposite direction and the action line of the component is very close. Equipment such as plate shears are usually used to cut the plate into the desired shape and size through mechanical shear.
Laser Cutting
Laser cutting is the use of laser beam to illuminate the surface of sheet metal material, through the high energy density laser beam local heating and rapid cooling, so that the material melting, vaporization, ablation or reach the ignition point, at the same time with high speed air flow will melt or ablated material blown away, so as to achieve the purpose of cutting or drilling.
Bending
Bending is the processing method of plastic deformation of the sheet metal parts. According to the dimension of the bending diagram, the bending machine is used to bend the workpiece.
Welding
The welding process joins two or more metal parts together using heat, pressure, or a combination of both. Usually, a filler material is added to give a strong weldment as it cools and solidifies.
The most common welding techniques used for metal parts fabrication include Metal inert gas welding, tungsten inert gas welding, and metal active gas welding. They are carried out in different ways and have unique advantages and applications.

Advantages Of Sheet Metal Manufacturing
Sheet metal fabrication includes a variety of techniques that offer many benefits. The final parts have uniform wall thickness with remarkable mechanical properties. The following are some of the major advantages of sheet metal fabrication
Accuracy and Efficiency
The accuracy and efficiency of sheet metal fabrication are top-notch. It is suitable for producing both prototypes and end-use parts.
Furthermore, it is critical to understand that most sheet metal techniques are automated. The use of CAD software and CNC machining eliminates human errors. As a result, the final products usually have few or no deformations.
Versatility
The sheet metal fabrication process uses an array of techniques and tools. This makes it easy to choose the most suitable method for your project.
Furthermore, metal parts fabrication does not limit the materials one can use. There are a thousand and more compatible metals. However, the application of the final part will influence the material you use.
High Capacity Production at Low Cost
With sheet metal fabrication, one can achieve a production capacity that is equal to the market demands. Though the initial cost may be high and the time of setting up may be long, it gets better when production begins. The more the parts produced, the more money one saves.
Manufacturing of Lightweight Components
Sheet metal fabrication produces lightweight yet durable parts. The excellent light-weight-to-strength ratio makes them useful in automotive and aerospace part manufacturing. Ultimately, it reduces manufacturing costs and improves fuel efficiency.
Custom-Built Designs
Sheet metal fabrication can be used to come up with innovative designs to build customized and unique parts. It is flexible and easily transforms metal sheets into personalized and aesthetically pleasing parts. The metal sheet fabricator can come up with innovative ideas and produce functional customized products.

Surface Finishes for Sheet Metal Fabrication
Most times, sheet metal fabricated parts require further polishing and post-processing to achieve the desired surface finish. There are many options available that serve both decorative and functional purposes. Here are the common surface finishes for sheet metal fabrication:
Electroplating
Electroplating involves depositing a metal layer onto the surface of the metal sheet using an external current. This process ensures surface uniformity and minimizes friction. Additionally, electroplated parts are corrosion and wear-resistant.
Bead Blasting
Bead blasting uses a spherical medium or other abrasive jet to dimple the surface of a metal sheet. By spraying at a high speed, the material creates an impact that leaves a matte texture and a more uniform finish. Note that the blasting medium one uses will determine what the surface will look like.
Polishing
Polishing is an aggressive process that uses a cloth wheel to “buff” or rub the metal surface to make it appear shiny. It removes rust, prevents corrosion, and further oxidation.
Powder Coating
This is directly spraying a charged metal component with dry powdered paint. Then, cure under UV light or in an oven to melt and adhere the powder to the metal. This process leaves a glossy or semi-glossy texture that is resistant to wear.
Anodizing
Anodizing is an electrolytic passivation process that converts the surface of the fabricated part into a thin but durable anodic oxide. This extra thickening makes the part nonreactive and corrosion-resistant. It also has aesthetic functions as it leaves a smooth and matte finish.
Factors affecting the cost of sheet metal Fabrication
Several factors are particularly important in the estimation of sheet metal fabrication costs that will directly affect the economy and final cost of the project.
material cost | The cost of materials used in sheet metal processing accounts for a large part of the total cost. The cost of different materials varies greatly, such as stainless steel, aluminum alloy, carbon steel and other materials at different prices. |
Processing process | Different sheet metal fabrication processes will affect the cost, such as the complexity and time-consuming of stamping, welding, cutting and other processes will affect the cost. |
Equipment cost | The investment cost of the equipment, machinery and tools required for sheet metal processing is also an important factor affecting the cost. Advanced equipment and tools may increase productivity, but they will also increase costs. |
Labor costs | Labor cost is an important part of the sheet metal processing cost, including the wages, training and welfare of operators, technicians and managers. |
design requirements | The design requirements of products will directly affect the difficulty and cost of processing. Complex design requires more processing technology and precision, thus increasing the cost. |
Purchase quantity | Mass production can usually reduce costs, because the cost of materials, labor and equipment can be saved through effects of scale. |
quality requirements | High-quality products usually require stricter process requirements and inspection standards, which may increase costs. |
Tips To Reduce Sheet Metal Fabrication Costs
If you want to reduce the cost of sheet metal manufacturing, you do need to use some clever techniques. Give us a deeper understanding of the various ways to ensure that the project is more cost-competitive:
Select Raw Materials
We prefer cost-effective materials such as aluminum or steel to more expensive materials such as stainless steel or titanium. In addition to making the design simpler, using economical and efficient materials can also significantly reduce the production cost of sheet metal. Although stainless steel or titanium may have its particular advantages, alternative materials such as aluminum or steel tend to exhibit similar excellent properties at a relatively low cost. When determining the most cost-effective material selection, specific functional requirements should be carefully considered and manufacturers consulted. Alternatively, note that the use of lower-cost materials may require subtle adjustments to their design to achieve optimal performance. By finding the correct balance between the function and the cost, we can effectively reduce the total cost of sheet metal production.
Surface Preparation
Consider the cost-effective surface treatments such as powder coating rather than chrome plating and anodic oxidation, etc.In addition to the manufacturing process, the surface finish selection also has a certain impact on the cost.When selecting materials, we tend to choose cost-effective options, such as a powder coating instead of the more costly chrome plating or anodized treatment. We recommend that you consult the manufacturer and evaluate different options for functional and aesthetic requirements to find cost-effective and effective solutions to meet project requirements.
Tolerance Control
One key factor to be considered when reducing the cost of sheet metal manufacturing is the tolerance requirement. While strict tolerances may be required for specific items, choosing looser tolerances can provide significant cost savings if they do not affect functionality or aesthetics. Before determining the tolerance level, the manufacturer must be consulted and all functional and aesthetic requirements carefully evaluated. Overall, realizing this can successfully reduce the cost of sheet metal manufacturing.

Simplify Manufacturing Steps
In collaboration with sheet metal processing manufacturers. Establishing close cooperation with trusted sheet metal processing manufacturers also saves costs in the manufacturing process. Simplify the process and eliminate unnecessary steps can save time and money. Please make further contact with your manufacturer to identify potential areas of improvement and work together to find ways to increase efficiency and reduce costs.
Quantity Ordered
Make the most of economies of scale by ordering more quantities at once. Another cost-saving strategy in sheet metal manufacturing is to take advantage of economies of scale by ordering more quantities at once. This can reduce manufacturing and transportation costs, thus saving on overall costs. Project requirements and storage capacity must be carefully assessed before placing bulk orders, but doing so can have a significant impact on reducing the cost of sheet metal manufacturing.
Invest In Technological Innovation And Sustainability
The introduction of technological innovation and sustainability practices is a long-term cost reduction strategy. The introduction of automation equipment can reduce labor costs and improve production efficiency. At the same time, the use of environmentally friendly materials and processes not only conforms to market trends, but also avoids additional costs due to environmental regulations. By constantly promoting technological innovation, enterprises can better adapt to market demand and improve competitiveness.
The cost characteristics of stamping
cost of material
Material cost is a large cost part of the stamping sheet metal process, which depends on the type, specifications and purchase price of the selected materials. Because sheet metal stamping processing can minimize waste by stamping on the same metal plate, it has a good material utilization rate.
Mold cost
Mold is a key tool in the process of sheet metal stamping, and its quality and design rationality directly affect the forming effect and production efficiency of products. The manufacturing and maintenance cost of molds is a non-negligible part of stamping sheet metal fabrication.
High efficiency and high precision
Sheet metal stamping processing has the characteristics of high efficiency and high precision, which can produce a large number of high-consistency parts and products in a short time. This helps to reduce the production cost of the unit product and improve the production efficiency.
Labour cost
Stamping sheet metal process requires skilled operators to operate and control, and labor costs include workers’ wages and benefits, etc. However, since sheet metal stamping can be processed with automated production lines, this helps to reduce labor costs and improve production efficiency.

The cost characteristics of shearing
Material cost
the shear sheet metal fabrication method mainly uses the metal sheet as the raw material. The cost of the material depends on the material, thickness, size, and market price of the selected plate. Since shear is generally used in the initial feeding process, the utilization rate of the material is relatively high, so it has certain advantages in the material cost.
Equipment cost
shear sheet metal fabrication requires the use of a shear machine or similar equipment. Equipment costs include equipment purchase costs, installation costs, commissioning costs, and subsequent maintenance costs. The cost of shear equipment usually varies depending on performance, degree of automation, and brand.
Labor cost
Although shear sheet metal fabrication is partially automated, it still requires operators to operate, monitor and perform simple maintenance of the equipment. Labor costs include workers’ wages, social insurance costs, and possible training costs.
Processing accuracy and efficiency
shear sheet metal fabrication belongs to the rough processing process, its processing accuracy is relatively low, but the processing speed is fast, and the efficiency is high. Due to the low precision requirements, the technical requirements for equipment and operators can be reduced, thus reducing the cost to a certain extent.

The cost characteristics of Laser Cutting
Equipment cost
Laser cutting equipment is a key part of the cost composition, and the initial investment cost is relatively high. Different models and performance of laser cutting equipment prices vary greatly, but it is generally more expensive. Equipment investment usually accounts for a large proportion of the total cost, especially for some high-end, high-precision laser cutting equipment.
Processing efficiency and speed
Laser cutting has the characteristics of high speed and high precision, which can significantly improve processing efficiency and reduce processing time. This means that more processing tasks can be completed in the same time, reducing the production cost per unit of product.
Stock utilization
Laser cutting can achieve high precision, low loss of cutting, improve the material utilization rate. Compared with traditional processing methods, laser cutting can reduce material waste and reduce material cost.
Maintenance and maintenance
Laser cutting equipment needs regular maintenance and maintenance to ensure the normal operation and extend the life of the equipment. Maintenance and maintenance cost is also one of the factors to be considered, but compared with other processing methods, the maintenance cost of laser cutting equipment is relatively low.
Human cost
Laser cutting equipment is simple to operate and requires relatively low skills for operators. This means that the demand for highly skilled workers can be reduced, thus reducing labor costs.
Processing quality and precision
Laser cutting can achieve high precision, high quality cutting effect, to meet the needs of precision machining. This means that the laser cutting sheet metal fabrication method can produce better quality, more accurate products, thus improving the added value of products and market competitiveness.
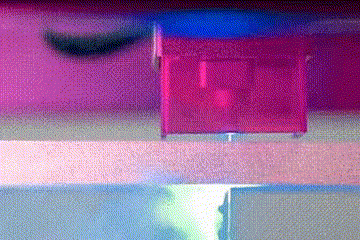
The cost characteristics of bending
Depreciation and cost of the equipment
Bending sheet metal usually requires the use of special equipment such as bending machines, which cost more to purchase. The depreciation cost of the equipment is spread over each bent workpiece, thus affecting the overall cost.
Labour cost
Bend operation requires skilled operators. Labor costs include workers’ wages, social security and other benefits.
Working efficiency
The efficiency of bending operation is affected by various factors, such as equipment performance, worker skills, workpiece complexity, etc. Efficient bending operations can reduce costs per unit of time. Turning a bend usually varies from 10 seconds to 100 seconds, which means that equipment depreciation and labor costs vary depending on the actual bend time.
Process complexity
The bending process complexity of different workpieces is different, and the complex bending process may require more equipment and labor input, thus increasing the cost. Complex bending processes may also involve multiple bends, angle adjustment and other operations, which will increase the processing time and cost.
Stock utilization
In the bending process, we need to ensure the full use of materials to avoid waste. Higher material utilization rate can reduce material costs. Optimizing design, improving operational skills and using appropriate equipment can all improve material utilization.
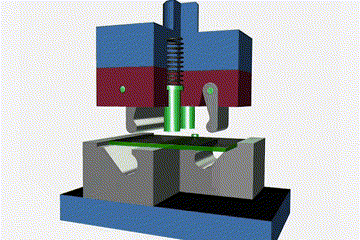
The cost characteristics of Welding
- Welding equipment: The cost of welding equipment varies according to the welding type and precision requirements.
- Labor cost: the connection process has high technical requirements for the operators, and the labor cost is relatively high.
- Welding quality: Welding quality directly affects the service life and performance of products, requiring a certain cost to ensure the welding quality.
- Post processing: After welding, grinding and cleaning may be required to increase the cost.

How to choose the most economical sheet metal manufacturing solution?
Define the needs and objectives
- Product requirements: First, specify the product size, shape, accuracy and performance requirements, as well as the expected production volume and delivery time.
- Cost target: Set a clear cost budget and cost control target.
Evaluate the raw material costs
- Material selection: select the most suitable sheet metal materials, such as aluminum plate, stainless steel, and consider the cost, performance and availability of the materials.
- Material utilization rate: By optimizing product design, improve material utilization rate, reduce waste generation, and reduce material cost.
Consider processing costs
- Processing method: according to the product requirements to choose the appropriate processing method, such as bending, curling, stamping, punching and cutting, etc. Consider processing efficiency, depreciation of equipment, and labor costs.
- Mold cost: for the required mold processing methods, such as stamping, to evaluate the cost and life of the mold, as well as the cost of mold replacement and maintenance.
- Process optimization: reduce the processing cost by reducing the use of processing steps and reducing auxiliary materials.
Evaluate production costs
- Equipment cost: consider the cost of purchase, depreciation and maintenance of the required equipment.
- Labor costs: to assess the labor needs in the production process, including the direct and indirect labor costs.
- Production efficiency: improve production efficiency, reduce production time and cost. Consider the application of automation and intelligent production technologies.
Through the above methods, we can choose out of the most economical sheet metal manufacturing scheme, and ensure that the cost control and benefit maximization in the production process.
Longsheng: Your Trusted Sheet Metal Fabrication Design Company
At Longsheng, we are not only proficient in the various skills mentioned above, but we have a professional technical team that can provide leading sheet metal fabrication services to manufacture high quality parts for you at very competitive prices. As an ISO 9001:2015 certified company, we focus on the construction of quality management system to provide customers with reliable service.
Our team of experts has the experience to perform DfM (Design for Manufacturability) analysis to improve your design. We are not only a manufacturer, but also a partner, committed to providing full support and professional advice to our customers to ensure that the design can reduce manufacturing costs while still meeting high quality standards.
If you have a design model that needs to be manufactured, please upload it to us immediately and we will provide you with an immediate quote. Choose Longsheng, choose a quality, high technical level, cost-effective sheet metal fabrication partner, let us work together to create outstanding parts for your project to achieve greater success.
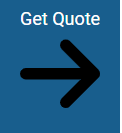
Conclusion
The economy of sheet metal processing depends on many factors, such as production scale, product requirements and processing technology. In choosing the most economical sheet metal processing mode, enterprises should comprehensively consider the equipment investment, production efficiency, processing quality and labor cost and other factors, according to their own actual situation to make a reasonable choice. With the continuous progress of technology and the gradual decline of the cost, it is believed that the future of sheet metal processing will be more economic, efficient and intelligent.
FAQs
What benefits does laser cutting offer for sheet metal components?
Laser cutting ensures precision and versatility in shaping sheet metal components. The process allows intricate designs, and minimal material waste, making it a preferred method for achieving high-quality results.
How to make sheet metal parts cheaper?
In order to make sheet metal parts cheaper, it is necessary to start from materials, processing, standard parts, labor, supply chain, technology and environmental protection and other aspects, comprehensive measures to reduce costs. At the same time, we also need to pay attention to market dynamics and customer needs, constantly optimize product design and production process, and improve product competitiveness.
How Does Sheet Metal Fabrication Work?
In the sheet metal fabrication process, thin sheet metal stock is initially positioned on a flat bed. Here, a laser cutter ① follows pre-programmed patterns to cut out the desired parts. Depending on the specific part’s geometry, a sheet metal punch ② may also be employed to create additional features. After the parts are deburred to remove any sharp edges or imperfections, they proceed to the press brake ③where they are shaped into their final geometries. Frequently, additional secondary operations are employed to complete the finishing touches on the sheet metal parts.
Which sheet metal Fabrication method is the cheapest?
There is no fixed answer to which sheet metal manufacturing method is the cheapest. This depends on the specific product requirements, production batch, equipment investment, labor cost and other factors. In practical application, enterprises need to choose the most suitable sheet metal manufacturing method according to their own situation, in order to reduce costs and improve production efficiency.In general, bending and stamping may be more economical for large volumes and simple shapes, laser cutting may be more appropriate if products have complex shapes and small batches, and manual operation may be more flexible and economical if products require special customization or very small batches. In addition, enterprises can also further reduce the cost of sheet metal manufacturing by optimizing product design, improving material utilization rate, reducing labor costs and other ways.
Resource
Comparison of technology of forming the sheet metal by numerical simulations