Aluminum fabrication is an indispensable technology in the modern manufacturing industry, and its wide application range and excellent performance make it the preferred material in various industrial fields. Aluminum has become a popular material for its lightweight weight, high strength, easy processing and corrosion resistance in aerospace, automotive manufacturing, construction and electronics.
In this guide, you will have a deeper understanding of what aluminum fabrication is, the aluminum fabrication process, the material characteristics, the main processing methods, the performance advantages of aluminum parts, etc. We will take you into the fascinating world of aluminum fabrication with advanced topics in an easy-to-understand way.
What Is Aluminum Fabrication?
In the simplest terms, aluminum fabrication is the process of processing aluminum into a finished or finished product. From complex aviation parts to everyday necessities, aluminum fabrication can do this.
The first strategies of aluminum fabrication embody extrusion, drawing, forming, casting, and forging. Extrusion entails forcing aluminum by or round a die to evolve to its form and dimension. Drawing pulls aluminum by a tapered die to stretch it. Forming presses all or part of the aluminum into the specified closing product. Casting entails pouring liquid aluminum right into a mold or die, whereas forging shapes aluminum by hammering or compressing it.
Concerning the varieties of aluminum, there are primarily three:
- Wrought Aluminum and Aluminum Alloys: These are fashioned by processes corresponding to extrusion, rolling, or forging. These processes are employed to type billets, rods, and ingots wanted for different manufacturing processes like machining. Wrought aluminum and its alloys are broadly utilized in numerous industries, together with automotive, aerospace, medical, and shopper product industries.
- Anodized Aluminum: That is aluminum or an aluminum alloy whose floor has been hardened and made extra sturdy by electrochemical reactions. Anodizing aluminum enhances its resistance to put on and corrosion, making it appropriate for a wide range of purposes.
- Aluminum Sheet Metal: That is generally utilized in fabrication processes. Sheet metallic may be minimize, bent, or stretched into almost any form after which joined to create a product. Aluminum sheet metallic fabrication is among the extra widespread strategies in manufacturing, utilized in making vehicles, cans, computer systems, home equipment, airplanes, and numerous instruments.

Benefits Of Fabricating With Aluminum
- Aluminum forming is relatively simple: compared to other kinds of materials. Due to its unique structure and properties, aluminum is widely used in industries such as automobiles, construction and electronics. This way makes aluminum easier to be processed into the desired form. In some applications, such as the automotive industry, aviation and aerospace technology, aluminum is considered one of the best options. In addition, aluminum is considered to be an economically efficient and recyclable material.
- On the grade of aluminum alloy: the different alloy grades have their own unique material properties, which provides a very wise reference for manufacturers in determining the grade of aluminum.
- Highly durable strength to weight ratio: Aluminum has become one of the core functions of the aerospace industry because of its highly durable ratio of strength to weight. This performance allows aluminum to be used to make parts such as aircraft wings, engines and rockets. Aluminum maintains the required tensile strength and toughness in both freezing and high temperatures. This gives it a good creep resistance and corrosion resistance. This material is seen as ideal in the aerospace industry because it is able to keep its core structure intact for long periods of time in extreme environments.
- Corrosion resistance: When aluminum is exposed to oxygen, its naturally generated oxide layer builds a protective barrier to avoid rust and corrosion.
- Safety and non-toxicity: The unique ingredients contained in aluminum ensure its safety and non-toxicity, making it ideal for all industries focused on safety and environmental issues, such as children’s appliances or kitchen tools.
Aluminum Fabrication Process Flow
The aluminum fabrication process mainly includes the following steps:
Raw Material Preparation
Aluminum material usually exists in the form of aluminum ore or aluminum recycled material. Raw materials need to be melted and refined to get pure aluminum ingots. Aluminum ingots are often square or cylindrical, and can be cut according to the production needs.
Melting And Casting
Aluminum alloy raw materials are put into high temperature melting furnace to melt and form liquid alloy. The liquid alloy is then poured into the mold and cooled and solidified to form a preliminary aluminum alloy casting.
Extrusion
The aluminum alloy casting is shaped through an extruder to obtain the desired shape and size. The extrusion process is performed at high temperature to deform the casting through pressure action.
Heat Treatment
The internal structure of the aluminum alloy material is changed by heat treatment to eliminate the internal stress and improve the strength and hardness. Heat treatment link is very important for the performance of aluminum alloy material.
Mechanical Treatment
Including cutting, forming, processing and other steps. Cutting can cut the aluminum into the corresponding length and width as needed. Forming such as stamping, bending, stretching, etc. the aluminum processing into the desired shape. Processing is to fine process the formed aluminum to meet the requirements of accuracy and surface quality.
Surface Treatment
Including anodic oxidation, spraying coating, electrophoretic coating and other methods, aiming to improve the corrosion resistance, wear resistance and decoration of aluminum.Anoodic oxidation can form an oxide film on the aluminum surface to improve corrosion resistance and surface hardness.
Spray coating and electrophoretic coating can give aluminum material different colors and texture.
Quality Inspection
Conduct quality inspection of aluminum alloy materials and finished products to ensure meeting the quality requirements. Quality inspection is an important means to ensure the quality of aluminum processing.
Packaging And Warehousing
Aluminum products after quality testing are packaged and stored for further use.

Characteristics Of Aluminum Materials
Characteristics | Elaborate |
Low density | Aluminum alloy has a low density, usually between 2.63~2.85g/cm³, giving it the advantage of lightweight. |
High strength | the strength of aluminum alloy is higher, can be close to or higher than high quality steel, at the same time, its specific strength is close to high alloy steel, specific stiffness more than steel. |
Strong plasticity | aluminum alloy has good plastic processing performance, can be processed into various shapes and sizes of parts. |
Good conductivity and thermal conductivity | aluminum alloy has good conductivity and thermal conductivity, better than copper, iron and other metal materials. |
Good corrosion resistance | the aluminum alloy surface is easy to form a layer of dense alumina film, with good corrosion resistance. |
Easy to process | aluminum alloy cutting processing is good, processing process is not easy to stick knife, tool service life is long. |
Aluminum Fabrication Main Process Method
The aluminum fabrication process covers all of the steps from uncooked aluminum to the ultimate elements. The generally used aluminum fabrication strategies embody casting, forging, extrusion, rolling, stamping, welding, and so forth. The next desk outlines the traits, benefits, disadvantages, and utility ranges of those processes:
Fabrication Process | Traits | Advantages | Disadvantages | Software Vary |
---|---|---|---|---|
Casting | Merchandise are made by pouring liquid aluminum right into a mold | Can manufacture advanced parts, low price | Decrease precision, might have inside porosity or inclusions | Advanced parts corresponding to engine elements |
Forging | Aluminum is formed by strain | Excessive power, wear-resistant | Excessive price, form limitations | Excessive power parts, corresponding to aerospace elements |
Extrusion | Aluminum is extruded by a mold to create numerous shapes | Can manufacture numerous shapes, excessive precision | Excessive tools price | Numerous shapes of parts, corresponding to window frames, pipes |
Rolling | Aluminum is pressed into sheets or rods by strain | Can manufacture sheets or rods, excessive precision | Form limitations, excessive tools price | Sheets or rods, corresponding to aluminum foil, automotive sheet metallic |
Stamping | Aluminum is stamped into numerous shapes utilizing a mold | Excessive manufacturing effectivity, excessive precision | Excessive mold price, solely relevant to skinny plates | Skinny plate elements, corresponding to automotive parts, digital parts |
Welding | Aluminum parts are joined collectively utilizing warmth or strain | Can join parts of varied shapes | Requires specialised tools and expertise | Structural parts, corresponding to bridges, vessels |

Which Aluminum Fabrication Process Should You Choose?
The best forming process will be the one that offers the best characteristics according to your project.
- If you want fast production and multiple design options as well as excellent surface finish, aluminum extrusion may be your best choice.
- If you want a simple, cost-effective process to get complex shapes, then aluminum die casting may be your best choice.
- If you obtain an aluminum plate, aluminum sheet, or aluminum foil for further processing that can meet your needs, aluminum rolling may be a better molding option.
- If your product premise needs to have impact and fatigue resistance, then forging may be appropriate.

Aluminum Fabrication Performance Advantage
aluminum fabrication the performance advantages are mainly reflected in the following aspects:
Workability
Aluminum products have excellent cutting properties and can be processed by common metal processing processes such as die casting, extrusion, rolling, casting and so on. The easy processing of aluminum products reduces the processing cost, and the waste produced in the processing process is less, which meets the requirements of environmental protection.
High-precision
Aluminum products have excellent mechanical properties, not easy to deformation, low thermal expansion coefficient, which makes it is widely used in the manufacture of precision parts. The surface smoothness of aluminum products is high, and the mirror effect can be obtained after polishing, which further improves its high precision.
Light
The density of aluminum is about 2.7g / cm³, which is only 1 / 3 that of that of iron or copper, making aluminum products have the advantage of lightweight. In aerospace, automotive manufacturing and other fields, lightweight materials can significantly reduce structural weight and improve energy efficiency.
Corrosion preventive
Aluminum is a very strong negative electric metal, in natural conditions or anodic oxidation under the surface will produce a protective oxide film, with much better corrosion resistance than steel. This characteristic makes aluminum products have wide application prospects in ship construction, chemical equipment and other fields.

Reinability
The strength of pure aluminum is not high, but it can be improved by anodized processes. This forzability makes aluminum products more competitive in applications that need to withstand larger loads.
Surface Processing Is easy to do
Aluminum anodized oxidation process is quite mature, stable in operation, and has been widely used in the processing process of aluminum products. Surface treatment can further improve or change the surface properties of aluminum to meet the needs of different applications.
Good electrical conductivity
Aluminum has good electrical conductivity, which makes it widely used in the fields of electronic equipment and communication equipment.
Easy to recycle
Aluminum products are easy to recycle and reuse, contributing to resource conservation and environmental protection.
Application field of aluminum fabrication
Aviation field
The aviation industry has very high requirements for the strength and lightweight of materials. Aluminum is one of the commonly used materials for aviation parts. Processing aluminum parts are widely used in aircraft fuselage, landing gear, engine shell and other components, which can greatly reduce the weight of aircraft, improve flight speed and fuel efficiency.
Automotive filed
Automobile manufacturing industry is one of the main application areas of aluminum parts processing. The automobile mainly uses aluminum profiles, aluminum plates and cast aluminum parts to meet the requirements of the strength and toughness of the material. Aluminum parts processing can reduce the weight of the car, improve the fuel consumption and control performance of the vehicle, widely used in the lightweight car engine, body and chassis and other key components.
Construction industry
Aluminum parts are widely used in the field of construction, including aluminum alloy doors and Windows, curtain walls, ceiling and partitions. Aluminum is easy to process, has strong durability, strong corrosion resistance, and has a superior weight and strength ratio, which is the core value material of high-rise buildings and skyscrapers.
Consumer electronics products
Aluminum is favored by many electronic manufacturers for its strong, beautiful, lightweight and good heat absorption and heat dissipation ability.Smartphones, tablets, laptops, flat-screen TVs, computer monitors and other electronic products are increasingly using aluminum in production.
Traffic
In addition to the automobile manufacturing industry, aluminum parts also have important applications in the rail and rail vehicle manufacturing industry, such as the production of high-speed bullet trains and urban rail transit vehicles.
Machine building industry
Precision aluminum profiles is widely used in the field of machinery manufacturing in the manufacture of structures and parts of various equipment and machinery.
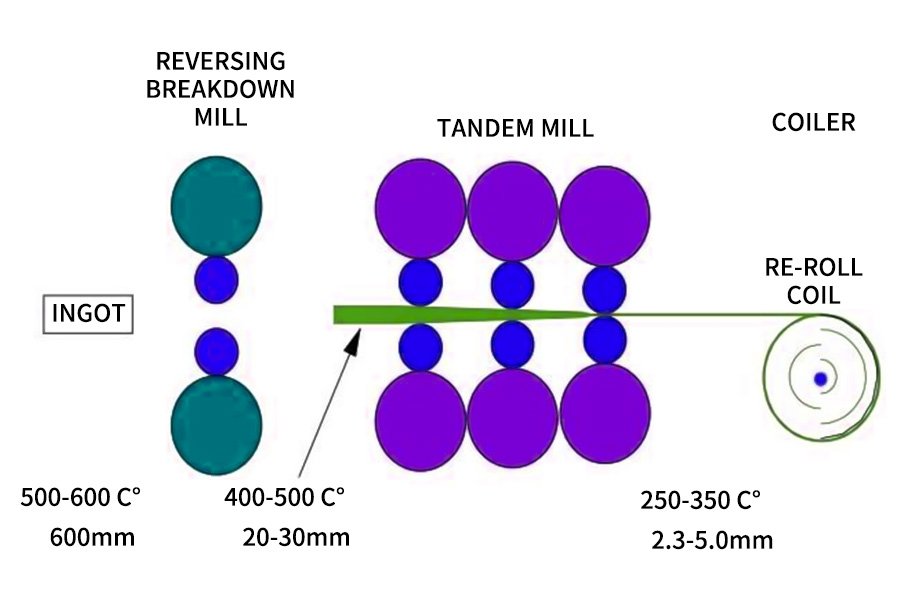
The Differences Between Aluminum vs. Steel Fabrication
Weight
Steel is significantly more dense than aluminum, and it weighs far more than it. Auto makers and the aerospace industry are turning to parts made from aluminum to reduce energy consumption. Lightweight vehicles and aircraft have more efficient fuel use. Because of its relatively light capacity, this leads to more cost-effective aluminum transportation costs.
Physical strength
Although both aluminum and steel can be used as tough metals, steel is more harder. The device has a stronger carrying capacity, but also shows a better tensile resistance, especially when stretched, it is not easy to break. However, the ratio of aluminum strength to quality is even higher. Lighter aluminum offers greater structural stability than the same weight of steel.
Conductivity
Compared with steel, aluminum has significantly superior thermal conductivity and conductive characteristics. In the application of heat dissipation technology, the heat dissipation performance of aluminum far exceeds that of steel. However, steel material can more effectively cope with higher temperatures and does not easily soften.
Machinability
The main production difference between aluminum and steel lies in its extenability, especially in the complexity of cutting, bending or folding of metal. Due to the density, thermal stability, and mechanical strength of steel, cutting or processing operations may encounter some challenges. Aluminum is easier to cut, bend or shape, although it becomes soft under heating conditions, a change that may pose some challenges in its manufacturing process.
What to Consider While choosing an Aluminum Fabricator?
- Experience: The amount of experience of professionals largely reflects their level of knowledge. Their past experience reflects their track record of fabrication high-quality products and completing projects on time.
- Costing accounting: discuss the product cost and budget in detail. The cost shall be specified in the terms and conditions so as not to affect the completion process.
- Quality: hire professionals to ensure that they use high-quality products and meet industry standards.
- Knowledge and skills: Ensure that aluminum manufacturers have the knowledge and skills of equipment, materials and technology to carefully process processes and complete projects in a timely manner.
- Multiple quotes: Get multiple quotes from different manufacturers so that you can compare market prices and choose the best offer for your project.
- Clear communication: Professional aluminum fabricator must communicate clearly with customers about the budget, schedule, availability, and products used. This helps to prevent misunderstandings in the process.
- Location: Ensure your selected fabricator is close to the site so that no additional shipping or shipping costs are incurred.
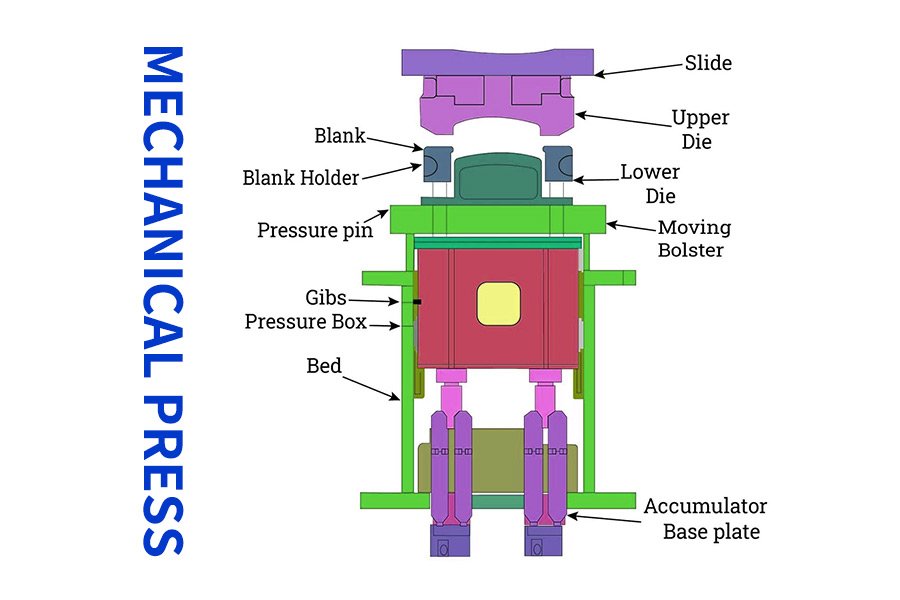
Future Developments In Aluminum Fabrication
With the development of expertise and modifications in social calls for, aluminum fabrication can also be welcoming some new improvement tendencies:
- Growth of New Aluminum Alloy Materials: With the event of latest materials science, extra new varieties of aluminum alloys might be developed sooner or later. These new aluminum alloys can have superior efficiency, corresponding to greater power, higher corrosion resistance, decrease density, and so forth., to satisfy the wants of varied high-end purposes.
- Software of Clever Aluminum Fabrication Know-how: With the event of Trade 4.0 and 5.0, clever fabrication applied sciences might be extra broadly utilized in aluminum fabrication. For instance, by the Web of Issues, huge knowledge, synthetic intelligence, and so forth, the automation and intelligence of the aluminum fabrication process may be achieved, bettering manufacturing effectivity, decreasing manufacturing prices, and in addition bettering product high quality.
- Promotion of Inexperienced and Environmental Aluminum Manufacturing Ideas: With the society’s elevated consciousness of environmental safety, the idea of inexperienced and environmental aluminum manufacturing might be extra broadly promoted. For instance, by adopting extra environmentally pleasant fabrication processes, utilizing recyclable aluminum, decreasing waste emissions within the manufacturing process, and so forth., the greening and environmental safety of aluminum manufacturing may be achieved.
Why Select LongSheng?
As for why one may select LongSheng manufacturing facility, it is as a result of they focus on customized aluminum parts and excel in creating cupboards, enclosures, brackets, and complicated assemblies. Their providers embody design, mass manufacturing, floor remedy, and meeting. With over 20,000 initiatives accomplished for greater than 3,500 international patrons, they’ve demonstrated their capabilities and reliability.

Conclusion
Aluminum fabrication entails shaping aluminum or its alloys into particular types or merchandise utilizing strategies corresponding to extrusion, drawing, forming, casting, and machining. The three widespread types of aluminum utilized in manufacturing are aluminum sheet/plate, aluminum extrusions/profiles, and aluminum rods/billets. These types are broadly utilized in numerous industries on account of their light-weight, corrosion resistance, and flexibility. Selecting LongSheng manufacturing facility for aluminum fabrication may be advantageous as they focus on customized aluminum parts, providing providers corresponding to design, mass manufacturing, floor remedy, and meeting. With a observe report of over 20,000 initiatives accomplished for greater than 3,500 international patrons, LongSheng has demonstrated its capabilities and reliability within the area of aluminum fabrication.
FAQs
What is the difference between Fabrication and Manufacturing?
The main difference between fabrication and manufacturing lies in their scope and focus. Manufacturing is a broader concept that includes the entire process of producing final products, which may include fabrication as one of its stages. Fabrication, specifically, focuses on constructing and assembling components, often requiring customised work and a detailed understanding of materials and processes.
What’s The Commonest Aluminum?
In every day life and industrial fabrication, the commonest varieties of aluminum are pure aluminum and aluminum alloys. Pure aluminum is principally used within the energy trade, corresponding to for wires, cables, and so forth. Aluminum alloys, on account of their excessive power, mild weight, and corrosion resistance, are broadly utilized in industries corresponding to aviation, automotive, and development.
How to do anything if oxidation, stains and scratches appear in the process of aluminum fabrication?
Use professional cleaning agents and tools to clean the aluminum material and ensure that the surface is completely clean. Apply chemical oxidation, electrochemical oxidation or anodic oxidation methods to improve the quality of aluminum surface oxidation layer, enhance its corrosion resistance and decoration. Polishing finish, use a polishing machine or manual grinding tools to improve the finish and flatness of the aluminum surface.
What should I do if the aluminum material breaks, warps, or deforms during aluminum fabrication?
Choose appropriate aluminum, select models and specifications according to processing technology and requirements. Conduct preprocessing treatment, such as heat treatment or cooling treatment, to improve the processing performance of aluminum materials. Optimize the processing process, fine operation, rationalization of materials, reduce operation errors.After processing, such as annealing, elimination of internal stress, surface polishing and other methods, to improve the aluminum stability and surface quality.